Part 2: Impact of ADAS on wire harness design
This is Part two in a three part series on ADAS design, to read Part 1: Introduction to ADAS please click here.
Among the most rewarding aspects of work at Mentor is the chance to collaborate with our experts around the world working on a range of disruptive automotive technologies that appear regularly in the news. One of these experts is Martin O’Brien who is based in Newbury, England and serves as general manager of the Integrated Electrical Services Division focusing on cabling and wiring design, and harness engineering. Another is Amin Kashi, Mentor’s director of ADAS based in the Silicon Valley (in our Fremont, Calif. office). The two recently collaborated on an article that will run this fall in Hanser Automotive, a leading German trade publication. Here is the English version of Part two in a three part series.
ADAS implications are keenly felt in the often overlooked realm of wire harness design, still a highly manual process, particularly in Germany and Japan. Indeed these two countries lead the world when it comes to rigorous methodologies and application of consistent rules and processes, on the car assembly line and in a host of other industrial contexts besides.
However, the growth of electrical/electronic content is such that even the best processes are reaching their breaking point. A modern vehicle can have many dozens of ECUs and 5 miles or more of wire, posing difficulties in wiring layout, vehicle weight, integration and development time.
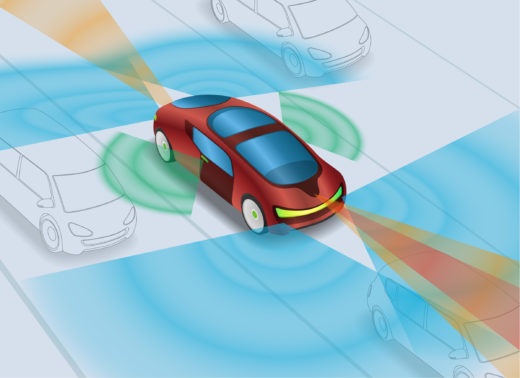
Anyone who has spent years and decades traveling to Detroit, Munich and Toyota City, will find it impossible to miss ascendance of senior managers with electrical engineering backgrounds. The unabated and accelerating increase of systems and components is almost certainly the central fact of automotive design today, where the lion’s share of innovation and novelty comes from electronics and software, not from the traditional mechanical or styling domains. Even as additional electrical design challenges come to the fore — multi-voltage systems, dual redundancy in critical circuits (for years standard practice in aerospace) and resultant new challenges in EMI —physical space for wiring remains constant. Combine that with the mounting expectation of customer choice associated with such systems and each car starts to have the feel of an individually designed product where the wiring systems are almost unique to each vehicle. Meeting that level of variety is an enormous design challenge for the industry.
Faced with these issues, leading automotive companies and suppliers are now adopting advanced engineering capabilities that support all aspects of creating a complex electrical harness: from product definition through electrical system design, harness manufacture and vehicle maintenance. These tools, such as Mentor Automotive Capital Products, deliver cycle-time reductions and support improved engineering processes by incorporating powerful design asset reuse and correct-by-construction technology that automatically generates optimized platform-level wiring. Using these powerful solutions, wire harness designers can efficiently deliver the new electronic features demanded by the automotive buyer, while minimizing the cost and weight of the wire harness.
Consider, too, the new challenges related to the security of these designs. Let’s ignore, for a moment, breathless media coverage of car hacking (A Feb. 22 article in Scientific American neatly sums up the current threat in its headline: “Why Car Hacking Is Nearly Impossible.”). Rather, we are talking about the need for ever greater security and confidence that designs are correct and defect-free, meeting both regulations and engineering intent. Lack of automation and the sheer number of transcriptions involved in the electrical design flow can make it hard to offer any sort of certification.
Comments
Leave a Reply
You must be logged in to post a comment.
The unabated and accelerating increase of systems and components is almost certainly the central fact of automotive design today, where the lion’s share of innovation and novelty comes from electronics and software.