Using digital manufacturing to machine high-quality components for aerospace and defense
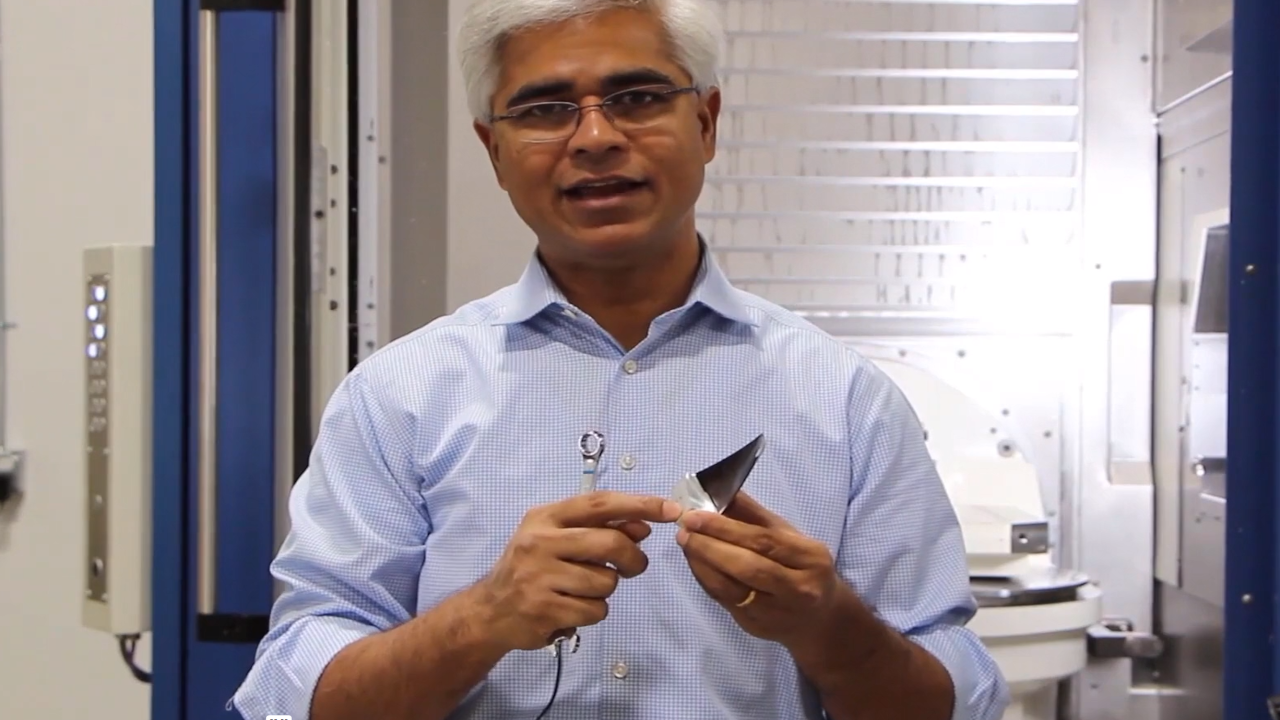
Aerospace and defense products are some of the most complex products in the industry. Plus, these products and their many parts are held to stringent quality and safety standards. The powerful integration of NX CAD, NX CAM and SINUMERIK CNC solutions is enabling aerospace and defense manufacturers to produce increasingly complex parts without sacrificing accuracy or efficiency. By implementing Siemens’ powerful digital manufacturing technologies, you can maximize machine tool performance, achieve leaner production, become more resilient in times of crisis and accelerate your business.
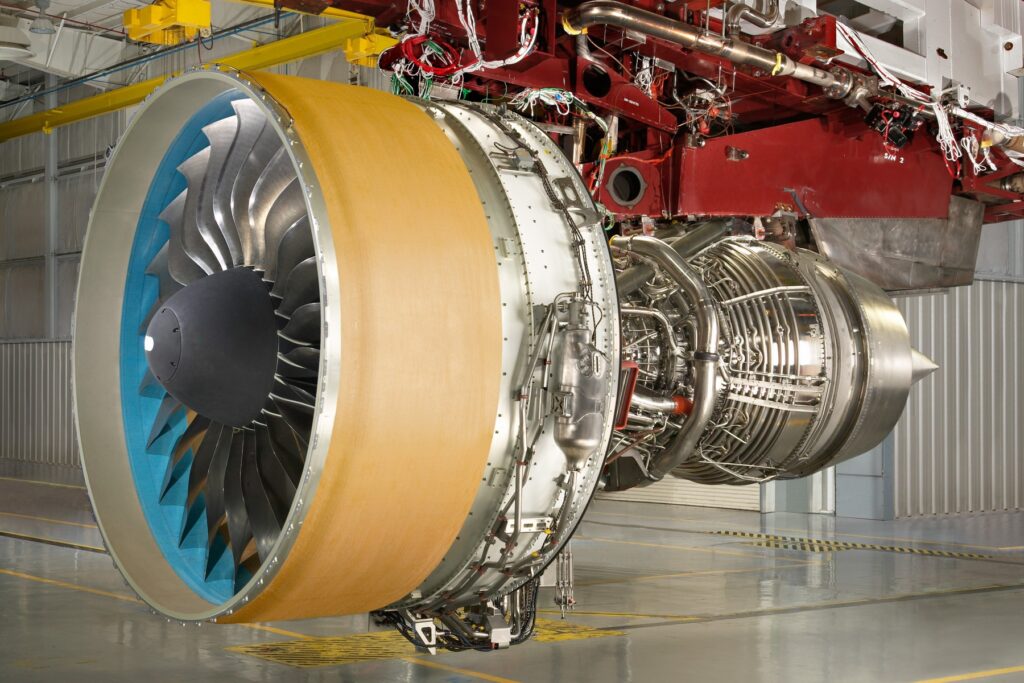
Solving complex machining problems
In this article, we are featuring SIXDIGMA, a Cincinnati, Ohio-based digital manufacturing company that helps manufacturers overcome challenges in five-axis machining. The company uses the Siemens CAD, CAM and CNC technologies to solve complex part manufacturing problems.
Edwin Gasparraj, founder of SIXDIGMA, shared with us how the company used those three key digital manufacturing technologies – CAD, CAM and CNC – to machine a complex airfoil.
Integrating CAD, CAM and CNC systems to machine an airfoil
The machining of an airfoil involves three machining challenges: using innovative toolpaths for excellent surface finish, advanced probing for exact part alignment and achieving high tolerances with a closed-loop adaptive machining process. Solutions for these challenges are outlined below.
Achieving the desired surface finish of parts for aerospace
Advanced CAM systems are needed to achieve the desired finish and dimensional accuracy on parts like an airfoil. Airfoils have complex features and tight tolerances that must be met. It’s difficult to program a toolpath that meets the necessary tolerance using traditional CAM systems. Advanced CAM systems can generate highly efficient toolpaths with less effort.
Advanced CNC machines today are capable of much better surface finishes, but discontinuities in 3D surface geometries can cause axis reversals that will tarnish the final surface finish. Siemens’ NX CAM has many tool axis and projection options, so you can generate any toolpath and tool axes to correct issues. Plus, NX CAM has integrated G-code-driven simulation technology enabling advanced and accurate digital machining validation that eliminates possible errors on the machine.
Accurate part alignment and adaptive toolpath technology
It’s incredibly important to have accurate positioning and a clear understanding of surface locations when machining an airfoil. Variations in surface geometry from part to part can impact accuracy. At times, it may be necessary to correct individual toolpaths within the part program as the variation may only be present in certain areas. Running adaptive toolpaths can help maintain high consistency and accuracy from part to part.
With Gasparraj’s method, the airfoil is clamped in the fixture and individually probed. These probing data are processed by the CNC, mathematically computed by using an advanced algorithm into new location data and calculated into the offset of the part and alignment of the toolpath. The part is probed a second time to fine-tune measurements and readjustments of workpiece offsets and toolpaths. At that point, actual part surface accuracy can be achieved within a few microns.
The powerful capabilities of the Sinumerik controller and NX CAM software enable the computation of this complex algorithm using massive amounts of data at an amazing speed. This makes it possible to utilize this process for serial production.