Overcoming roadblocks to achieve digital transformation of manufacturing in the A&D industry
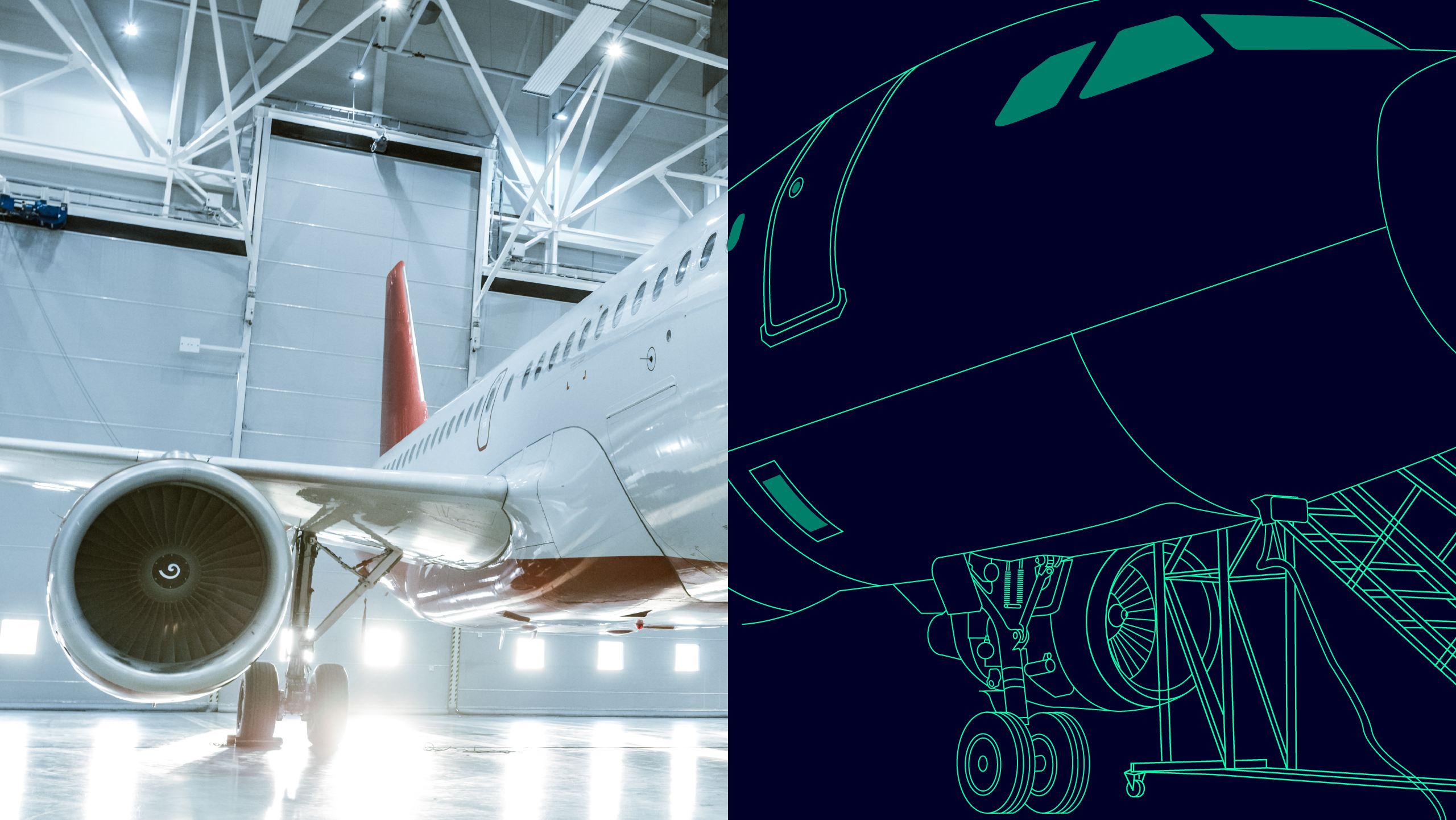
How can you achieve smart manufacturing faster?
Introduction
Digital transformation in the A&D industry has become critical to achieve smart manufacturing faster and maintain a competitive edge in a rapidly evolving landscape.
According to a report from Lifecycle Insights in 2022,
40 percent of A&D companies find that their physical parts do not conform to digital design.
Lifecyle Insights 2022
Because of this, many manufacturing organizations are still operating as they have for decades, waiting until the product definition is finalized before developing their manufacturing plan. Before developing a process plan or implementing digital solutions on the shop floor, it is crucial to identify the current industry challenges that impact manufacturing decisions.
Current roadblocks to achieving digital transformation
Many hurdles are preventing companies from achieving efficiency, cost-effectiveness and sustainability in the industry. Siemens Digital Industries Software offers digital manufacturing solutions to enable aerospace and defense (A&D) manufacturers to overcome obstacles and achieve new levels of manufacturing productivity and excellence. This article addresses the current hurdles A&D companies are facing and discusses why traditional approaches are no longer successful.
Program cost and schedule
As pressure mounts to deliver complex products faster, A&D customers are constantly looking for ways to speed their processes and reduce costs to streamline operations. Companies must navigate the delicate balance between delivering high-quality products within stringent timelines and optimizing expenditures. Between these program cost and schedule issues among other factors, many companies are struggling to find the balance. Achieving this balance is crucial to remain competitive in the market and satisfy customer expectations.
Sustainability
In an era of growing environmental awareness, A&D companies are striving to reduce their carbon footprint and embrace sustainable practices. A 2022 Lifecycle Insights report shows that 80 percent of global manufacturers are aiming to incorporate sustainability in their manufacturing processes by 2024. While this commitment to sustainability is commendable, it also adds complexity to product development processes. Balancing the imperative of eco-consciousness with efficient manufacturing processes presents an added layer of unique challenges.
Lack of visibility across the entire manufacturing process
Traditionally, your mechanical, electrical, software and factory automation teams tend to operate and optimize independently. Applying constantly changing mandates and regulations to new products can be detrimental when you continue adjusting manufacturing processes after a product definition is finalized. This is especially so when managing various product configurations across a global landscape. With this traditional approach, you can’t discover that anything is out of sync until you physically commission the line for the first time. Losing design intent on the shop floor compromises the ability to prove compliance and deliver your products.
Traditional manufacturing approaches
With traditional, linear processes, you can’t discover that anything is out of sync until you physically commission the line for the first time. Having to fix unforeseen problems at this stage means that your commissioning process takes longer than necessary and puts your delivery target at risk. Even after you’ve resolved the commissioning issues, maintaining the line presents another set of challenges because you can’t predict performance or the need for maintenance. And of course, you can’t build every line from the ground up (greenfield), so you must be able to leverage legacy equipment as much as you can.
Reluctance to adopt new solutions or processes
Companies are reluctant to shift to dramatic innovations because there is fear that there is no way to “backstep” in case the new approach fails. Many manufacturers use a model-based approach, but it may not be software driven. The big question for manufacturers is – if you can’t predict processes how can you prevent problems downstream? With so much on the line and so much pressure to deliver quality, complex products faster, what is holding aerospace and defense manufacturers back from implementing digital transformation at their organizations?
Workforce challenges
The industry is always facing workforce challenges including the continuous turnover of skilled engineers. In addition to these factors, other things can play into these workforce challenges such as industry shifts, constant competition for engineering talent from competing industries and businesses, working environment, remote versus in-person working and much more.
Culture change/change management
Another major issue facing the workforce is change management. Changing the culture within a company is hard and changing behavior is even more difficult. Change management in the A&D industry refers to the idea of structured process of planning, implementing and monitoring changes within organizations. This can involve managing transitions in processes, technologies, organizational structures, policies, data or other aspects that may impact the way the company operates on a daily basis. In the A&D industry, change management is not only about managing internal organizational changes but also about adapting to shifts in global factors, market demands and ever-changing smart technology. Effective change management can lead to improved efficiency, reduced risk, increased innovation and more efficient overall performance within the industry.
A 2023 study from PricewaterhouseCoopers titled ‘Evolving workforce and aerospace and defense firm needs’, mentions how A&D companies can start addressing these workforce issues and risks of turnover, the need for specialized skills, clearance delays and rapid retirement rates by reimagining company incentives, creative workforce planning and offering advanced technology training – all while striking the right working balance that can fuel growth and efficiency for long-term success.
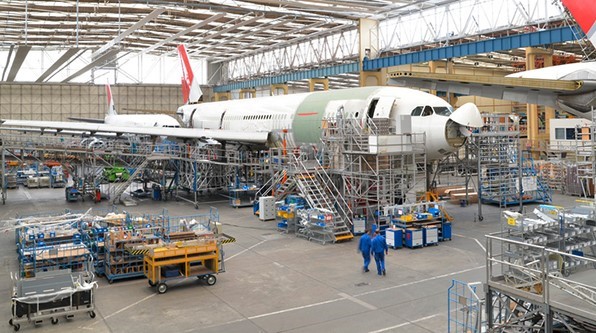
A path forward for smart manufacturing
To embark on a successful digital transformation journey, A&D companies need a clear plan and vision. This path forward involves learning how to achieve right first-time production and efficiency and how to develop a model-based manufacturing plan. Another aspect of this involves uniting the virtual and real worlds to validate your plan and reduce production costs and speed delivery time. These concepts will help companies ultimately optimize products and processes for the flexible, connected factory of the future.
To embrace and adopt digital transformation in the manufacturing process, it’s key to understand the hurdles that many companies are facing and the flexible and scalable options for our industry to overcome them. Embracing digital transformation in manufacturing is no longer an option but a necessity for A&D companies aiming to secure a competitive advantage.
Learn more about managing change in the A&D industry and about approaches for digital transformation in manufacturing in a three-part ebook series, soon to come. Discover how to leverage these concepts to achieve digital transformation in your manufacturing process to achieve long-term success.
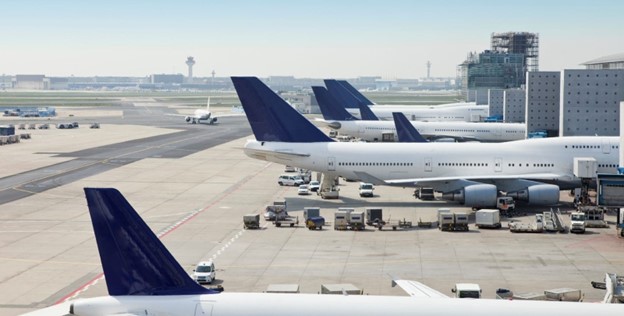
For more information on achieving digital transformation in aerospace and defense, please visit our website.