Advancing Additive #12 – Powering a Multi-axis AM Operation
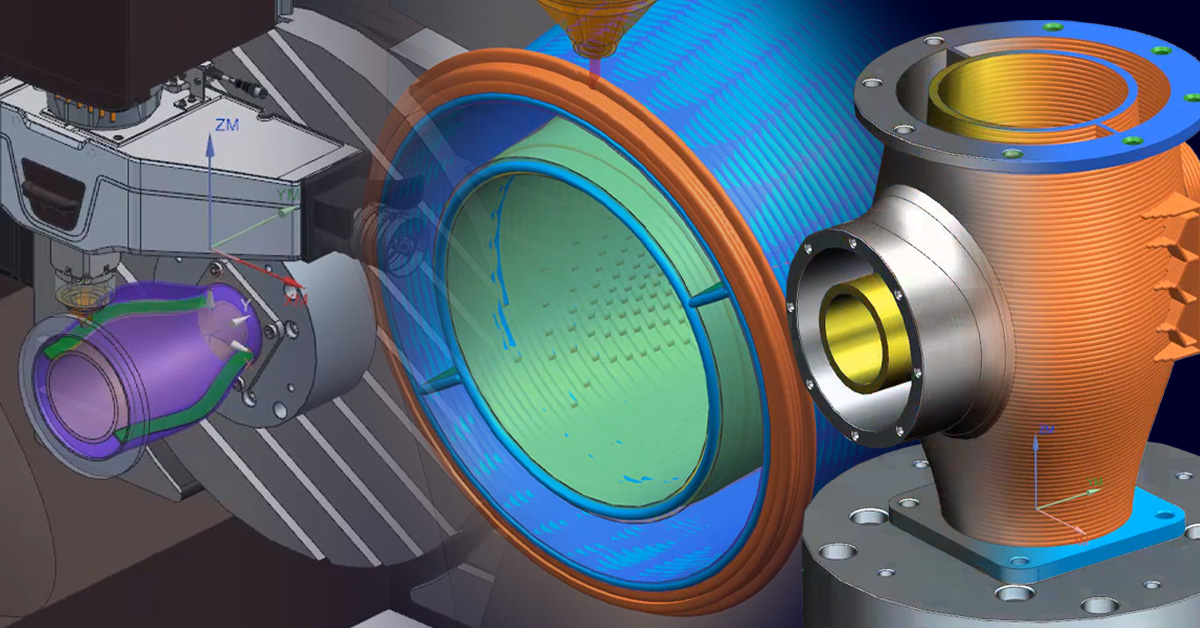
The overall CNC market is projected to grow over the next six years at a seven percent compound annual growth rate. This is largely due to the growing demand for more multi-axis machines. And one of the fastest growing segments of the multi-axis market is hybrid manufacturing. In fact, the market for additive/subtractive machines will grow twice as fast as the overall CNC market (15% CAGR). And, of course, the primary driver for the increased usage of hybrid manufacturing is the growth of metal additive manufacturing, which is actually growing at nearly twice the rate of the hybrid market (28% CAGR).
The problem with all this growing demand for multi-axis and hybrid manufacturing is that companies need software to drive their new multi-axis machines. Often, they try to get by with three-axis milling software and rotary tables to achieve the additional degrees of freedom, a so-called 3+2 programming strategy. But without full simultaneous five-axis machining software, companies compromise quality and efficiency. Five-axis machines maintain continuous contact between the tool and the workpiece, leading to better part finishing, less scrap, and less human interaction.
So…what sort of capabilities should you look for in multi-axis AM software? First and foremost, it has to have the functionality to do the job. That means enabling additive/subtractive toolpath programming, proper material coverage, consistent bead thickness, handling of overhangs, superior sidewall and surface finish, and more.
But beyond functionality, the multi-axis software for your machines should connect seamlessly within an industrialized AM workflow. That means that there should be a unified, associative digital environment from design and part validation, through part build preparation and simulation, to 3D printing, follow-on machining, process monitoring and quality control.
This is the sort of solution that Siemens NX CAM and AM software provides. Our solution spans the entire process of designing hybrid parts, validating their manufacturability, creating NC programs, simulating machining operations, and controlling the CNC machines.
Here’s a short video showing the workflow for hybrid manufacturing in the unified NX environment.
About the writer:
Aaron Frankel is Vice President of Siemens’ additive manufacturing software program. He has over 20 years of experience in the PLM software industry and has held various positions in engineering services, product management, and marketing – all focused on helping manufacturers take advantage of the latest digital design and manufacturing technology.