AMSIG Tech Session – May 15,2024 Optimizing Support Generation in Additive Manufacturing: Breakthrough Techniques for Aerospace, Defense, and Motorsports
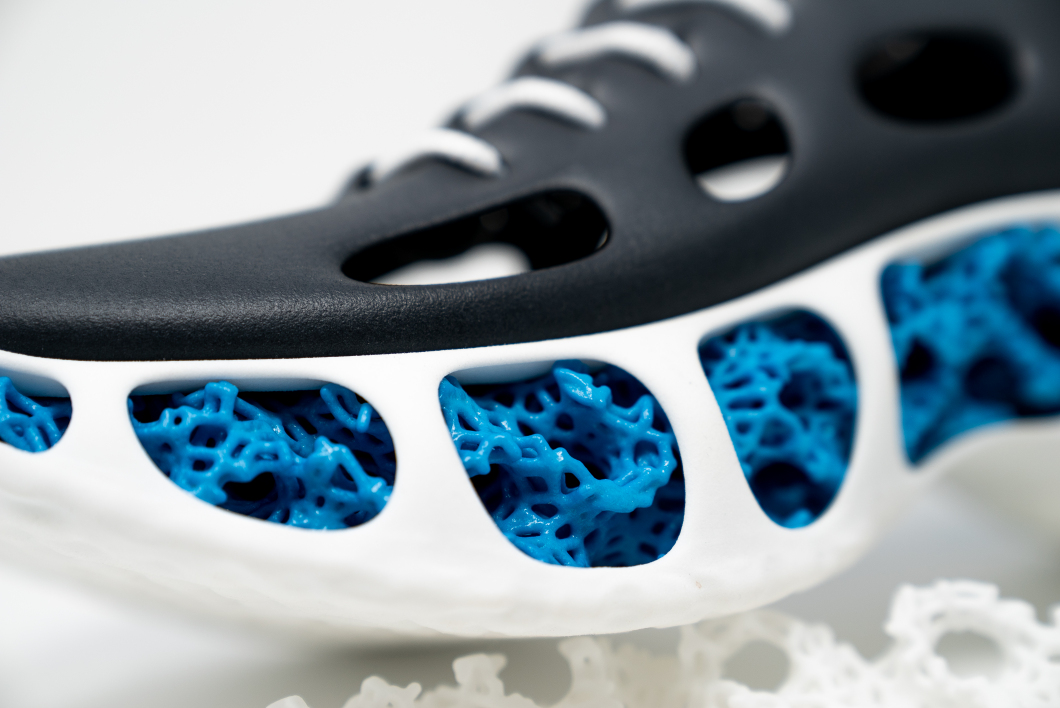
Additive manufacturing, particularly in high-stakes industries like aerospace, defense, and motorsports, demands intricate support structures for complex parts. Mike Vasi, a specialist in additive manufacturing software at Siemens, discusses innovative approaches to support generation that cater to these high-end requirements.
Support generation is a critical, yet time-consuming, step in the additive manufacturing process. It involves creating thousands of design features to support complex parts, a task that can take up to a week for a single part. Effective support design must consider various factors, including part geometry, material properties, layer thickness, and the specific printer model used.
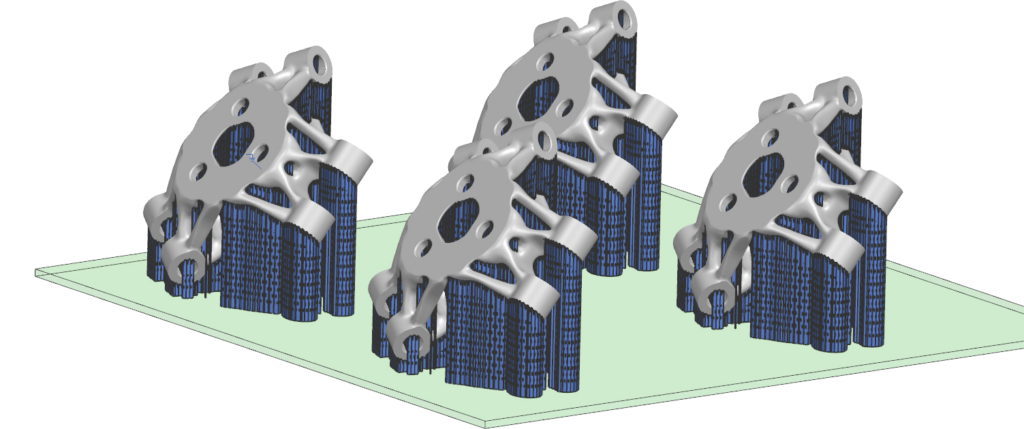
Key Strategies for Optimized Support Structures
1. Conformal and Associative Supports
For aerospace and defense applications, support structures must be conformal—fitting precisely to the part geometry—and associative, meaning they automatically adjust to any changes in part positioning or design. This tailored approach ensures that supports provide the necessary stability without compromising on material efficiency.
2. Multi-Angle Overhang Support
Different overhang angles on a part require distinct support strategies. For example, shallow angles may need minimal supports, while steep angles require robust, dense structures to prevent deformation. By segmenting the part into various overhang intervals and applying appropriate supports, material use is optimized, and the likelihood of print failures is reduced.
3. Optimized Build Plate Connections
Ensuring strong adhesion of parts to the build plate is crucial for print stability. Using optimized fillets—rounded connections at the base of the part—reduces stress concentrations and the risk of cracking during cooling. This method enhances the overall structural integrity of the part.
4. Specialized Supports for Titanium Parts
Titanium’s high melting point and thermal conductivity pose unique challenges in additive manufacturing. Segmented supports that accommodate thermal contraction are essential to prevent warping and cracking. These supports absorb stress during cooling, maintaining the integrity of the printed part.
5. Lightweight Lattice Structures
Lattice structures, which are less dense than solid supports, offer significant benefits in terms of material efficiency and ease of removal during post-processing. These structures can be customized to match the specific requirements of the part, improving the overall quality and efficiency of the printing process.
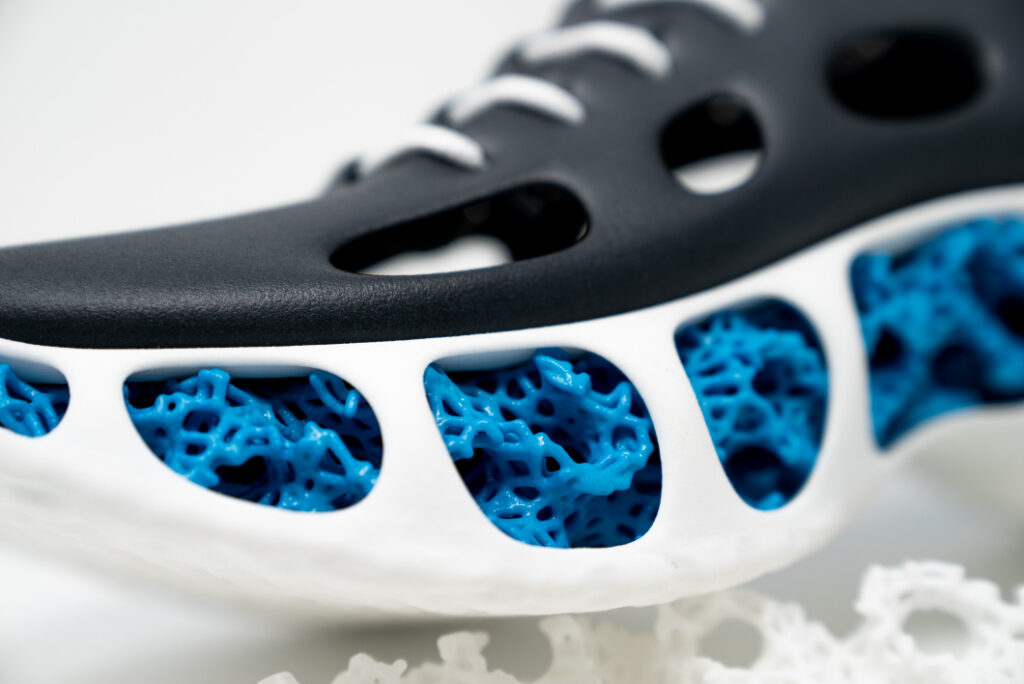
Case Studies and Practical Applications
Vasi highlighted several case studies demonstrating these advanced support strategies:
- Multi-Angle Overhang Support: By creating support regions based on overhang intervals, materials are used more efficiently, and the printing process is streamlined.
- Optimized Build Plate Connections: Using a 4mm radius fillet optimized through the “root 2” formula significantly reduces the risk of part failure due to cracking.
- Titanium Part Supports: Segmented, flexible supports manage thermal stress, preventing deformation during the cooling phase.
- Lightweight Lattice Structures: Custom lattice designs enhance material efficiency and simplify post-processing, making support removal more straightforward.
Conclusion
The development of advanced support structures in additive manufacturing is crucial for high-end applications where precision, material efficiency, and structural integrity are paramount. Siemens’ innovative approaches, including conformal and associative supports, optimized fillets, and custom lattice structures, address the complex requirements of industries like aerospace, defense, and motorsports, setting a new standard in the field.
As additive manufacturing technology continues to evolve, these sophisticated support generation techniques will play a pivotal role in advancing the capabilities and applications of 3D printing in critical industries.
If you would like to join the AMSIG to get the full benefits, membership is free, just click the button below to e-mail us with your request to join.