CNC Digitalization Partnership for Vocational Education
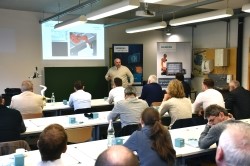
Skilled machine operators for the challenges of digitalized manufacturing
By Peter Kemptner • March 13, 2020
To prepare for the challenges of tomorrow, manufacturers will need to establish a robust digital thread, extending from design and engineering to the machine in operation. This changes the requirements employees in production need to meet. Siemens Digital Industries Software is offering vocational and engineering schools a cooperation turning them into manufacturing education centers where today meets tomorrow. This enables them to provide the industry with skilled graduates familiar with a fully digitalized approach to end-to-end product creation.
Digital transformation needs education. And it needs it in the right places so it reaches the right people. Colleges and universities are full of digital natives preparing for office careers. What the manufacturing industry is most desperately in need of, however, are skilled workers to operate the milling, turning, grinding and measurement machines on the factory floor.
Digitalization changes needs new competences
The ongoing automation has been replacing repetitive, cumbersome, simple tasks usually performed by unskilled workers. Digitalization, on the other hand, is a means to get things right the first time. Technologies enabling multi-discipline simulation and optimization through iteration allow companies to remove barriers between disciplines and domains, supporting an open and inclusive engineering environment.
These technologies are used to ensure that automation can happen across the various disciplines within the product creation process, spanning a digital thread from product ideation to computerized numeric control (CNC) program generation to machining and assembly operations.
Traditional metal cutting know-how like the right choice of cutting rates for different materials or CNC programming and operation will not cease to be crucial competences in tomorrow’s work environments. Machining operations will, however, increasingly be aided by information technology (IT) processes.
Digital transformation needs education.
To reduce standstills and improve productivity, more and more companies create NC programs using computer-aided manufacturing (CAM) software. They are turning to computer simulations in the virtual world, using the digital twins of their products, the production machines and the machining tools to test manufacturing processes before actually executing the CNC programs in the machine tools.
As an important prerequisite for digitalization in manufacturing, people on the shop floor will therefore require additional competences; competences needed to provide them with the ability to handle these novel methods. As the number of machine-bound tasks decreases, their skills need to extend at least far enough to span all machine-related processes starting at program creation. This is how digital transformation of businesses and processes changes the requirements their education has to meet.
Including upstream CAD/CAM processes
Some manufacturing careers start after combined theoretical and practical education in Universities of applied sciences or in technical colleges and schools. In Central Europe, however, most of them are trained during apprenticeships. Their practical training on the job in employing companies is supplemented by theoretical and practical courses in vocational schools.
Skilled machine operators can supplement their competences in additional courses like the CAD/CAM planner course at the ebiz technical training center in Pocking, Germany. During this 12-month course the non-profit organization introduced in 2018, they learn to create and modify 3D designs and use the models to generate and virtually test CNC code for metal cutting as well as additive production strategies in the machine tools.
To counter the lack of skilled labor in manufacturing and at the same time help companies bridge the digitalization gap on the factory floor, numerous vocational schools have started extending their CNC machining courses to include the upstream CAD/CAM work preparation processes.
Providing end-to-end product creation training
“Spanning the entire workflow chain from part design to machining typically requires the installation of various software products, including interfaces between them and to the machines,” says Marius Sikora, technical instructor at Karl Peter Obermeier (KPO) vocational school and technical school for electrical and mechanical engineering in Passau, Germany. “Although our government provides the educational system with digitalization funding, the training requirements imposed by a heterogeneous system landscape are impeding attempts at realigning vocational education to provide for the requirements of digitalization.”
KPO is among the first schools in Germany to offer production-oriented training courses using machine tools that include the digital upstream process chain. The school profits from an educational alliance offered by Siemens to cover everything from CAD/CAM work preparation to machining education using the SINUMERIK CNC automation system. This also includes education work on the digital twins of both the machines and the CNC controllers using SINUTRAIN and the Virtual Numeric Control kernel (VNCK) for simulation and verification. This makes it easier to provide a stable environment with end-to-end software compatibility and data consistency.
Unparalleled CNC digitalization training partnership
The Siemens digitalization for technical education alliance provides schools with inexpensive hardware and software products and support as well as a wealth of training material. “Where today meets tomorrow, our end-to-end product creation training courses provide a digital thread across the entire process chain from CAD/CAM to the CNC controller,” confirms Sikora. “It provides apprentices with the practical skills required to make the digital transformation of their future employers a success.”
To achieve this, the students can use NX installations from home. And teachers are kept up to date with the latest developments in manufacturing and control technologies as well as digitalization. The Siemens digitalization for technical education alliance also includes regular trainings for the teachers involved. And it comes with options from Siemens Finance & Leasing making the use of CNC machine tools and related equipment affordable for school operators.
“The Siemens co-operation for end-to-end digitalization in technical education provides us with access to a training program beyond anything we could get from other sources,” says Eduard Weidenbeck, headmaster of the Karl Peter Obermeier school. “It enables us to support companies through digital transformation, providing them with skilled graduates who have already gone some way along that path.”
Quote 1:
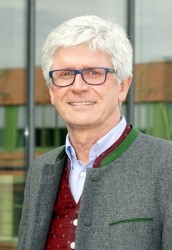
The Siemens co-operation for end-to-end digitalization not only provides us with access to a training program beyond anything we could get from other sources. It enables us to support companies through digital transformation, providing them with skilled graduates who have already gone some way along that path.
Eduard Weidenbeck, headmaster of the Karl Peter Obermeier vocational school and technical school for electrical and mechanical engineering in Passau, Germany
Quote 2:
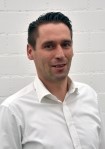
Within the Siemens cooperation, we can provide mechanical and electrical engineering students with a NX license for a year so they can use the installation on the school’s server from home.
Marius Sikora, technical instructor at Karl Peter Obermeier vocational school and technical school for electrical and mechanical engineering in Passau, Germany
Captions:
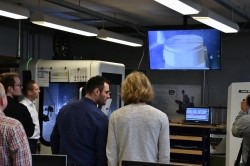
Karl Peter Obermeier vocational school and technical school for electrical and mechanical engineering in Passau, Germany, offers production-oriented training courses that include the digital upstream process chain including CAD/CAM work preparation using Siemens NX software.
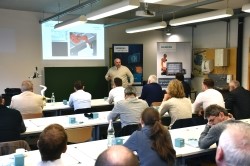
The Siemens digitalization for technical education alliance provides schools with inexpensive hardware and software products and support as well as a wealth of training material, and teachers are kept up to date with the latest developments in manufacturing and control technologies as well as digitalization.
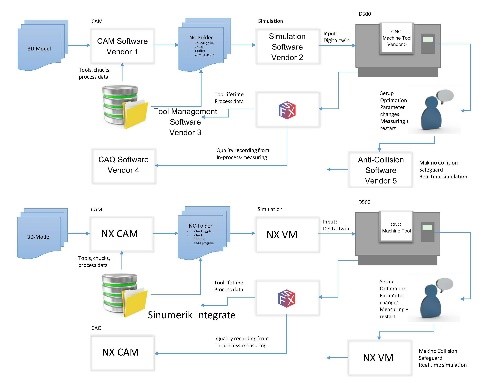
By contrast to a heterogeneous system landscape (above), the Siemens educational alliance provides a stable training environment for everything from CAD/CAM work preparation to machining education and including the digital twins of both the machines and the CNC controllers with end-to-end software compatibility and data consistency.