Holistic Manufacturing Management for Industry 4.0
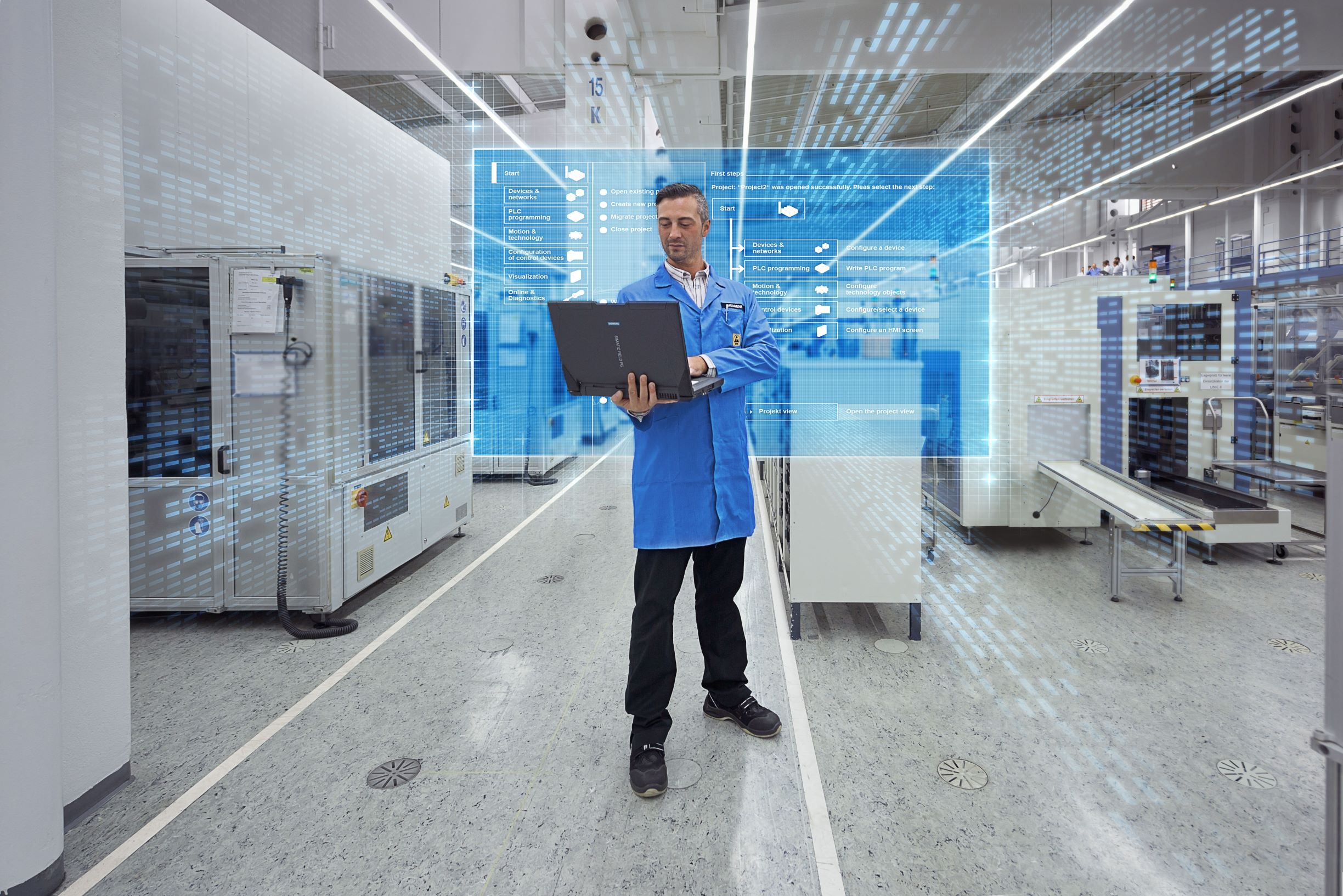
As a part of Siemens Digital Industries Software, Valor engineers are creating integrated solutions for industrial applications and deployment platforms (e.g., SDKs, OML, digital product models and libraries, and preconfigured apps) that enable customers to develop applications specifically for their production needs and processes. These tools are updatable to ensure continuous functionality in an evolving or changing environment, flexible enough to support a large ecosystem of current and future devices and machines, and enable authentication and provide security measures. They support a wide range of connectivity options, such as ubiquitous communication connectivity.
As many new technologies are being introduced into manufacturing operations, the decades-old manufacturing execution system (MES) is a crucial piece of the foundation for digital transformation. Technologies—such as augmented reality, AI, cloud and edge computing, and mobile and auto ID—are being integrated into MES solutions. Likewise, smart machines, sensors, and IIoT platforms are expanding capabilities to integrate to enterprise-level MES.
This is because important functions and features provided by an MES cannot be replaced by new IIoT platforms, even with analytics and apps. IIoT devices and platforms do not provide operational context for data or trigger actions in response to data and are not designed to orchestrate processes across the factory and value chain. Many production processes need people in the loop, and the MES provides that connecting platform.
For Industry 4.0, the MES needs to integrate into a company’s digital platform and “system-of-systems,” including engineering design, validation/verification, test, quality assurance, business, and factory management, production, assembly, and fabrication systems. Again, IoT-connected operations are integral to smart manufacturing, connecting machines to gather data and enable monitoring the production process throughout a plant. And in this connected world, the requirements for an MES have changed.
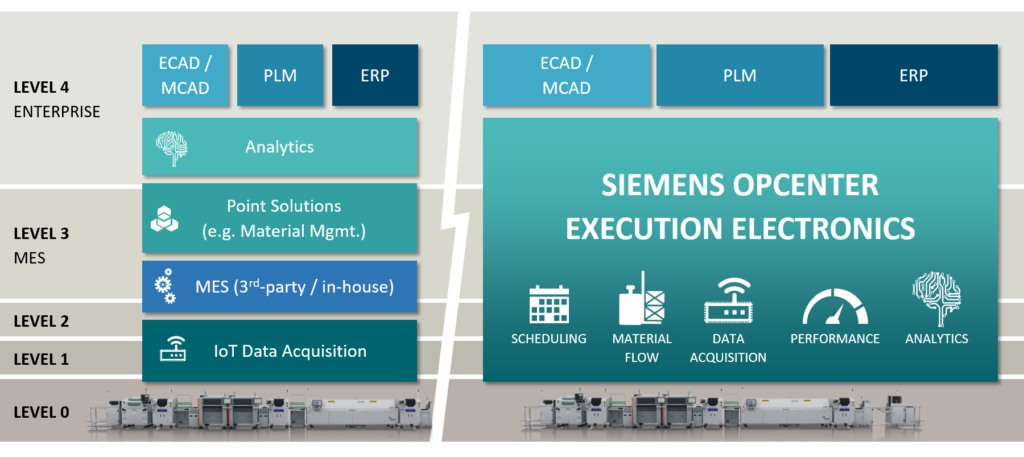
Closed-loop Feedback to and from PLM
In PCB manufacturing, closed-loop feedback—generated thanks to the integration of MES with PLM—provides great benefits. This flow of information is from MES to PLM.
Even more important is the flow of information from PLM to MES, especially information regarding the engineering of manufacturing processes. It is key that this process-related information is efficiently transferred from PLM to MES, as the resulting speed-up makes new product introduction (NPI) more reliable.
An MES for Industry 4.0 must integrate into other enterprise systems, such as PLM, enterprise resource planning (ERP), other manufacturing operations management (MOM), and scheduling programs. Integration with a scheduling engine, for example, is especially important in smart manufacturing. In an advanced scheduling solution, the MES sends data to a scheduling engine, which manipulates it to create an optimized schedule and returns it to the MES. The MES then uses the optimized schedule to generate the queue for order dispatching and operation view. The benefits of advanced scheduling include lower inventory levels, reduced costs, and faster response to shorter lead times.
To learn more and see these solutions in action, join us at our booth, February 4 – 6, at IPC APEX, Hall D Booth #3223 for a live demo.