Generative design helps design teams innovate faster
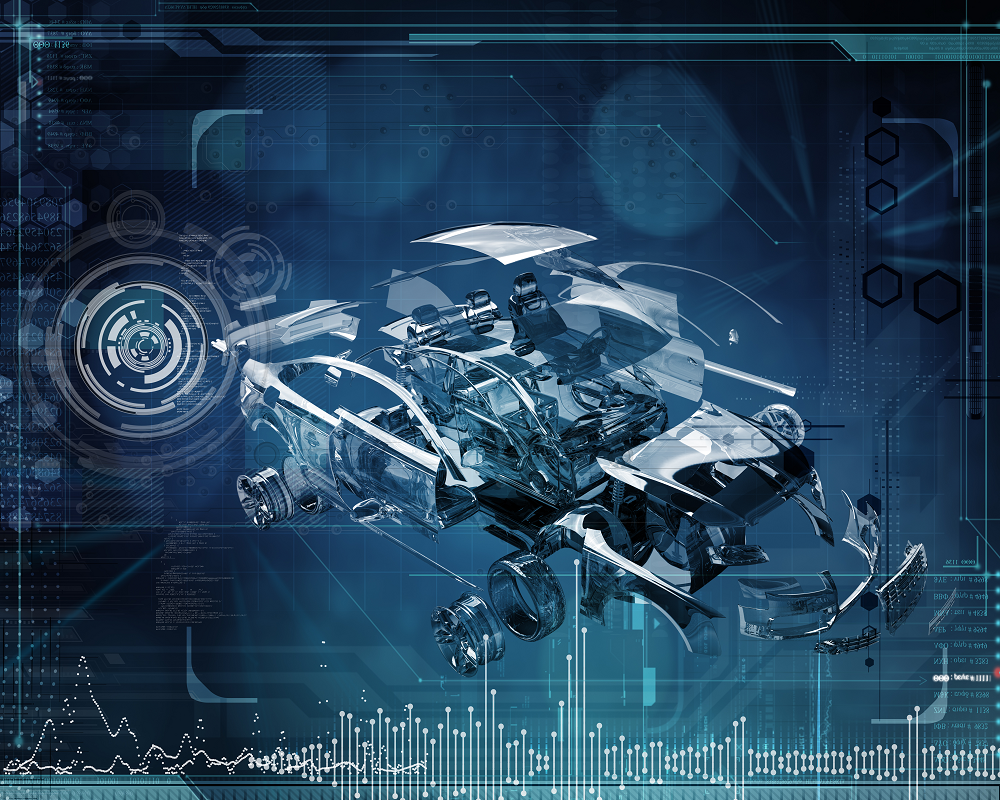
We all know what happened when high-performance computers armed with artificial intelligence competed in chess, Jeopardy and Go. They beat humans who were the reigning grand champions.
Fewer are familiar with the results of open chess tournaments that test all-comers—human, computer, or teams of humans and computers.
The surprise outcome of one of those competitions? The winner was neither a super computer, nor a grandmaster using a state-of-the-art PC, but a pair of amateur American chess players using three computers at the same time. Former Chess Grandmaster Garry Kasparov explained:
“Their skill at manipulating and ‘coaching’ their computers to look very deeply into positions effectively counteracted the superior chess understanding of their grandmaster opponents and the greater computational power of other participants. Weak human + machine + better process was superior to a strong computer alone and, more remarkably, superior to a strong human + machine + inferior process.”
Similar human-computer collaboration is coming to industry in the form of generative design and Convergent Modeling. Both are new capabilities that—when combined with a wave of disruptive trends including high-performance computing, integrated design workflows and artificial intelligence—are revolutionizing product design processes and development.
The tools are particularly critical for companies in highly competitive industries that must frequently and quickly deliver new and innovative designs of complex products, such as automotive, aerospace, energy, industrial machinery and heavy equipment, biomedical and electronics.
Manufacturers that can master integration of digital workflows and knowledge between humans and computers and across the product lifecycle will set new performance levels for their industries, gaining big top- and bottom-line benefits.
Generative design quickly finds optimum solution
Generative design and Convergent Modeling are complementary capabilities within the latest product design software applications. Generative design leverages algorithms drawn from existing design knowledge to autonomously design all possible permutations of geometric alternatives, given a set number of constraints. In doing so, it delivers more options than would be possible with traditional tools and likely many options that engineers hadn’t considered.
In traditional product design processes, a designer uses software to design a product or component to meet specific requirements. With generative design, the designer sets the specific requirements and parameters—material, design space and target weight, for example—and the software automatically configures the optimum geometric solution.
Generative design can deliver more options than traditional tools, including options engineers hadn’t considered.
Capturing the benefits of generative design
Generative design provides many transformative benefits to companies that can easily incorporate into their product design processes. These include:
• Taming complexity: Generative design helps companies more effectively meet customer demand for more complex and customized products, which increasingly require the latest disruptive, technology-embedded electronics, Internet of Things connectivity/communication and augmented reality. It automates the analysis that determines things like weight-to-strength ratios, efficient material use and performance optimization, while taking into account how all the product systems will work together.
• Faster decision-making: Because generative design works autonomously, design engineers can make more complicated decisions more quickly. With a given set of specifications, engineers can conduct more experiments in much less time than is possible with traditional design methods. They can also run multiple variations simultaneously.
• Reducing material use: Generative design creates models that require only the amount of material needed to meet product requirements, and no more, which reduces material waste and cost.
• Lowering shipping costs: Because products created with generative design use the least amount of material, they tend to be lighter than their traditionally designed counterparts. This translates to lower shipping costs, which, if you’re shipping millions of parts each year, could generate billions of dollars in savings.
• Transforming production: When paired with additive manufacturing, generative design delivers a number of benefits, including the following:
o Gives manufacturers the capability to produce complex shapes that are impossible to build using traditional methods.
o Speeds production of prototypes and finished parts.
o Reduces costs by eliminating the need for expensive equipment and tooling, as well as by using less material.
• Preparing for the future: As customers demand that the latest technologies be incorporated into products and expect them to be delivered faster, generative design gives companies an advantage, preparing them with a fast, efficient way to meet new opportunities.
Convergent Modeling supports b-rep modeling for generative design
Generative design delivers still more and bigger benefits when combined with Convergent Modeling, which helps integrate generative designs with traditional ones. Generative design creates faceted or mesh models that must be converted into b-rep models for use in traditional manufacturing.
Siemens’ Convergent Modeling solution supports b-rep modeling operations on facet bodies without conversion, allowing designers to build analytical features into the generative body, complete with dimensions and Product Manufacturing Information. It allows designers to combine facets, surfaces and solids in one model without converting data, which includes the capability to import scanned 3D data as facets.
BMW tackles complexity
The biggest benefits of generative design and Convergent Modeling are gained when the technologies are embedded in a broader digitalization effort – that is, when they are part of an end-to-end PLM strategy linking design, engineering, manufacturing and maintenance data and knowledge within a unified solution.
BMW is among the first to adopt generative design as part of its digitalization strategy. The company must increase the pace of innovation as the industry transforms with the introduction of driverless and electric cars and in-car wireless connectivity. BMW is focusing on five key areas: Big Data and analytics; cloud; security; computer performance; and in-car mobile device use.
BMW’s Vision 100 concept car, presented in 2016, demonstrates the company’s aim in which the car adapts to the driver, as when switching between autonomous to traditional driving. Creating a product with such complex integrated electronics and technology would be time-consuming and cumbersome with traditional design tools and disconnected processes—if it could be done at all.
Human + machine + better process = competitive advantage
Companies that are first to bring together humans, high-performance computing and artificial intelligence in an end-to-end generative design thread across the design cycle will not only deliver complex designs more quickly: they’ll upend industries as they perfect and accelerate speed-to-market for differentiating innovation.
This concludes part one of our series on multi-disciplinary design. In part two, we discuss how generative design can make the most of additive manufacturing processes.
About the author
Tod Parrella is the product manager responsible for NX Design. He has worked in the NX Product Management organization for more than 11 years and is responsible for the development of a number of NX CAD innovations including Synchronous Modeling, NX Realize Shape Subdivision Modeling and most recently Convergent Modeling. Tod is also the Design lead for the NX Generative Design initiative which includes investments in Bionic & Lightweight Structures Design and Design for Additive Manufacturing. In addition to his role as Product Manager for NX Design, Tod also manages a small industry product management team responsible for driving industry requirements into the NX Design planning process.