Digitalization in marine engineering and the future fleet
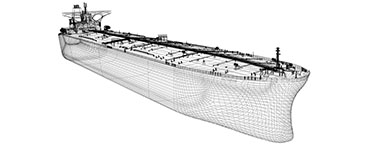
The Dream Chaser® faces a tough mission. Once completed, the world’s fastest “Space Utility Vehicle” will be taxiing passengers and goods to and from the International Space Station at speeds of over 17,000 mph (27,358 kph) while enduring temperatures well over 3,000 degrees Fahrenheit (1,648 degrees Celsius) in an environment where failure is not an option.
To complete this mission, every component of this spacecraft must be in perfect order. Both materials and structural engineering calculations need to be absolutely spot-on, and every piece and part, from the largest thruster to the smallest seal, must be up to spec and working in complete harmony.
Even more challenging, this perfect state of order must be maintained no matter how the cargo changes or how the missions evolve.
This is a challenge that no old-fashioned blueprint can possibly take on. It requires high-tech tools that allow engineers, builders and crew to monitor, verify, simulate and test every piece, part and operation to achieve the level of absolute perfection they need for success.
And that makes sense: Space-age challenges like this require space-age solutions.
But back on Earth, this same kind of challenge exists for a very different breed of ships.
Military ships today are arguably every bit as technologically advanced as a space taxi, and they face performance challenges that demand the same component-level perfection as well.
But they face a major challenge that the Dream Chaser most likely will not: a service life that stretches decades and covers missions, environments and retrofit requirements we can’t even imagine today.
This means these ships need to be every bit as rugged as their predecessors, every bit as honed and refined as space ships, and yet be flexible and adaptable enough to ensure they are able to complete whatever mission comes next.
And this shipbuilding technology challenge only has one solution: digitalization.
Ships need to be rugged, honed and refined as their predecessors, but they must also be flexible and adaptable enough to ensure they can complete whatever mission comes next.
Sub mission: PLM & the digital twin
In the U.S., two companies are permitted to build nuclear submarines, both of which pull in the combined intelligence and efforts of hundreds of global suppliers and dozens of assembly locations to complete their builds.
Despite all of the many hands involved in this construction process, every ship and each minute component of them must be exactly the same. They must have the same designs, the same advanced features, and the same upgrades and conversions that develop through the build. No matter where it comes from or who builds which part, the Navy requires consistency and perfection.
To do this, shipbuilders have turned to 3D modeling and advanced PLM software designed to keep everything aligned and up-to-date across the supply chain — the same system that will drive the production of the Dream Chaser.
This software allows marine engineers to examine spaces and components, even down to piping and wiring requirements, to verify where equipment will be placed and determine the best installation plan. They can experiment with different features and functions for ship operation and different ergonomic considerations for the future crew; they can optimize operations, production, and maintenance practices and routines before the ship even exists.
And, most importantly, this shipbuilding technology can sync all designs and changes to every supplier and builder involved in the project, so no time is lost and no inconsistencies find their way on board.
This also means a huge advantage during production. Shipbuilders can create digital models to simulate the entire fabrication process step-by-careful-step until they reach an optimal process. The 3D modeling capabilities allow production teams to virtually inspect every component and every system on the ship to optimize material flow through shipyard, assembly and out to sea.
In a very practical sense, these tools boost efficiency through all phases of the ship’s lifecycle. This shipbuilding technology allows builders to validate designs earlier and test the control configurations faster and easier. It lets them set routines and checks earlier in the engineering process, which greatly reduces the risk of failures and errors in the critical phases of the lifecycle. Having these 3D model capabilities ensures production teams that chance to virtually inspect each component and system on the ship for better material flow through the shipyard, assembly and at sea.
Marine engineering sails into the future
When all of this data exists on an integrated data platform, it creates the capability for later modifications to be tested and verified in exactly the same way as all of this pre-launch work.
Once a completed ship is out on the water and begins its long, 50+ year lifecycle, these 3D models provide a key to future upgrades. As the ships are retrofitted and re-equipped with emerging technologies and for new missions over the years, designers and production crews can work with the existing models to help create the best performing fleet possible with as little disruption as possible.
Using the “digital twin” created in this end-to-end PLM system, designers can lay out, test and simulate every step of the updates, from installation to performance, to guarantee that the ship will perform as the mission demands and without unnecessary delay.
This, in a sense, helps “future proof” these billion-dollar investments, keeping them afloat and up-to-date no matter how the world or the technology changes.
It provides a level of quality and adaptability never before seen in this industry, and brings space-age technology back down to the original frontier.
This concludes the second part of our digital shipyard series. In part three, we look at how digital shipbuilding is crucial to a strategy that promotes innovation and rapid incorporation of prototypes and upgrades.
About the author
Tim Nichols is the Director of Marketing Communications for the Global Aerospace, Defense and Marine industries at Siemens PLM Software, a business unit of Siemens’ Digital Factory division. He has more than 30 years of experience in aerospace and defense, which spans product management, marketing, new business development and business management. Tim spent nine years of active duty with the United States Navy. He is a graduate of the U.S. Naval Academy and holds two graduate engineering degrees from the Massachusetts Institute of Technology in Cambridge, Massachusetts.