Additive manufacturing process: a modern factory in Sweden
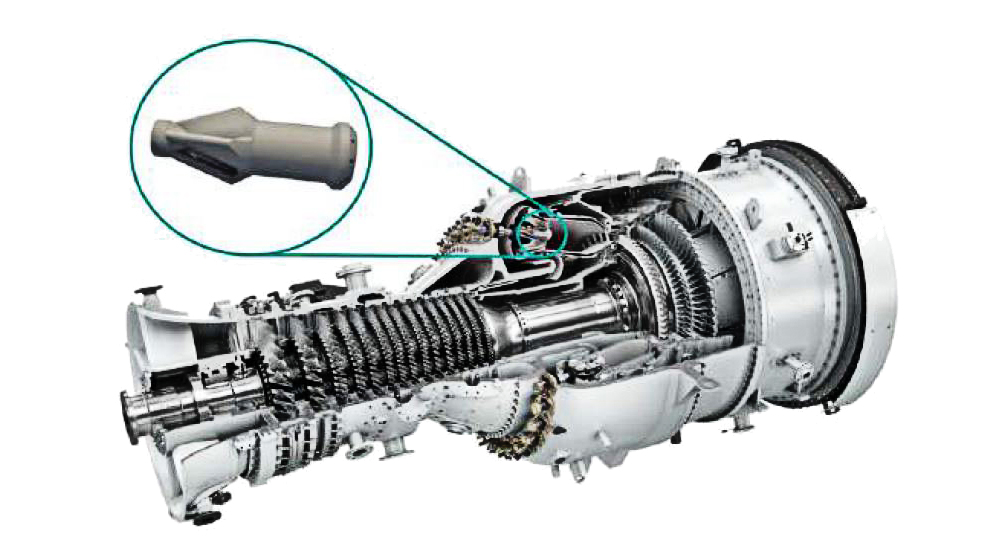
What can’t you print? A valid question in the world of 3D technology where 3D printing, also known as additive manufacturing, can output almost anything via digital simulation, including cars.
This innovation is currently being used to meet the need for out-of-production parts, repair of parts and improvement of manufacturing tools. The possibilities for improvement of these parts and tooling are unlimited, and often the improvements can save manufacturers valuable time and money while vastly improving efficiency.
Additive manufacturing uses multiple technologies to produce a part layer upon layer. One of its benefits is streamlining the overall manufacturing process by removing the need for costly castings and machined tooling. Use-cases like these are prime examples of the advancement this technology is making to the overall production process.
Traditionally, the production and repair of parts can require taking measurements, designing and producing molds, casting the raw part, finishing, assembling, and many times correcting miscalculations (by repeating this cycle).
However, this process is transformed via additive manufacturing where technology, innovation and efficiency come together via innovative design and simulation to produce parts that in the past required longer lead times due to trial and error.
The modern factory via the additive manufacturing process
Additive manufacturing simulation presents a tremendous opportunity to improve current products by making them more cost-effective to produce and therefore less expensive to the consumer. So, manufacturing finds itself on the cusp of change that is not slowing down.
A phenomenal example of this innovation resides in the rolling hills of Sweden in a centuries-old city called Finspång, where automation meets production. This 500-year-old factory, which once manufactured canons, entered gas turbine production in the mid-1950s. As recently as 2008, the factory began an entire chain of additive manufacturing via power specification, additive manufacturing process parameters, material properties development, design for additive manufacturing and manufacturing itself.
Burner tip repair
The Finspång factory uses additive manufacturing to perform burner tip repair via 3D printing technology. When a gas turbine burner went into a gas turbine and ran in the field, the burner tip would erode after a certain number of hours due to flame and combustion performance inside the engine. The cost of new burners was high, so customers wanted to repair and re-certify burners as a lower cost alternative.
Burner tip repair is a lengthy, expensive process requiring the part be sent to another facility for machining away the damaged area, welding on a new section and completing the refurbished burner assembly with several required manual steps. Though this method was more cost-effective than assembling and replacing the entire burner, it was still an extremely lengthy and costly process.
However, with additive manufacturing this process is most efficiently streamlined by machining away only a small portion of the damaged burner tip to provide a clean, known surface to additively manufacture directly onto the burner ‒ massively reducing scrap, work and repair time. This method of tip replacement has been hugely successful with significant turnover reduction, while the burners are still operating under daily cycles after 20,000 hours ‒ and inspected as good.
Better design and repair via the additive manufacturing process
The original turbine burner head design called for many individual pieces to be machined and welded together. This design created a complicated manual manufacturing process.
As the Siemens team in Finspång gained more knowledge about additive manufacturing, it envisioned other uses for the technology. Engineers thought about a complete redesign of the burner head that could combine many of the individual parts into one single unit and incorporate unique features that could be additively manufactured.
Having a low mass burner design weight was essential. The team found that the burner walls could be made slimmer for an improved temperature response, including lattices to make the burner stronger at this lower weight, resulting in less thermal inertia. The lattice structure also provides effective cooling of the fuel.
This design delivers a stronger, more agile product for the turbine’s heating and cooling cycle, allowing the burner to have a less hostile heating and cooling routine. This increases the burner’s longevity and lessens oxidation and crack formation that can typically damage the burners.
From this process, the team achieved a 22 percent weight reduction and is working on refining it to attain a 50 percent reduction.
Design collaboration and evolution
Collaboration is the key to developing the additive manufacturing process and the technology to repair gas turbine burners. By removing silos, collaborating via technology, and developing trusted partnerships, a path is paved for innovation. The Finspång accomplishments assist other industries to advance their additive manufacturing on an industrial scale.
Additive manufacturing knowledge is growing at the Finspång facility, along with the ability to take advantage of its amazing potential.
This concludes part one in a series of upcoming articles on additive manufacturing and what was accomplished by Siemens at the Finspång facility in Sweden. In part two we will continue our discussion of the beginnings of additive manufacturing at Finspång. In the meantime, you can still learn more about additive manufacturing.
About the author
Blake Snodgrass is a writer for the Thought Leadership team in Siemens Digital Industries Software. He speaks with experts in their field who provide insight into innovative technologies affecting industries and their future impact. Blake has a Bachelor of Arts degree in Mass Communications with over 25 years of experience working for IT companies.