Additive manufacturing failures (Part 2) – challenges to first-time-right printing
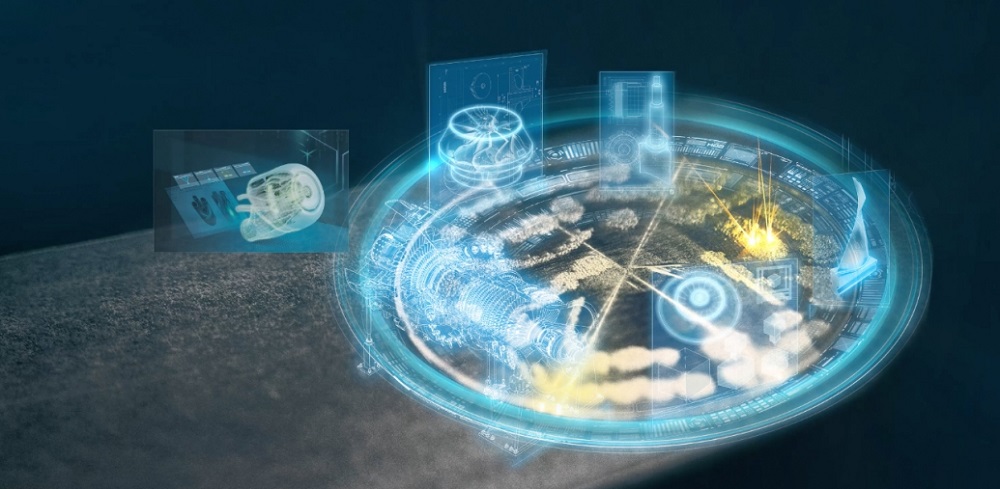
Achieving first-time-right printing is the holy grail of additive manufacturing (AM) or 3D printing. AM is a complex process involving many variables that can affect the viability of the produced part. To avoid wasting time and materials, companies need solutions to the myriad of issues that impact their ability to adopt additive manufacturing in an industrial fashion.
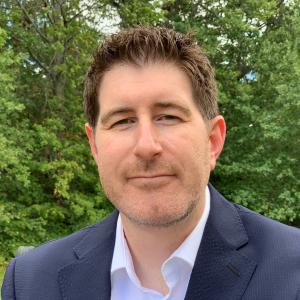
In our first blog on this topic, we discussed the problems AM users often encounter resulting in printing failures. In this blog, we will present how companies are achieving quality prints at an industrial scale by adopting expert-guided software for aiding in first-time-right printing. This significantly decreases the need for test prints and printing iterations to produce quality results.
Solutions via specialization
However, before we discuss software, it is worth noting one of the ways companiesare addressing the quality problem with AM via specialization. In this case, a company will limit their hardware to a single or limited number of vendors and their materials as well. This has the effect of removing variables from the process. However, this also has the result of limiting their opportunities because they may not be in the position to take advantage of innovative new technologies or materials.
Therefore, specialization is one method being used to reduce the number of failures with additive, but it has its own costs.
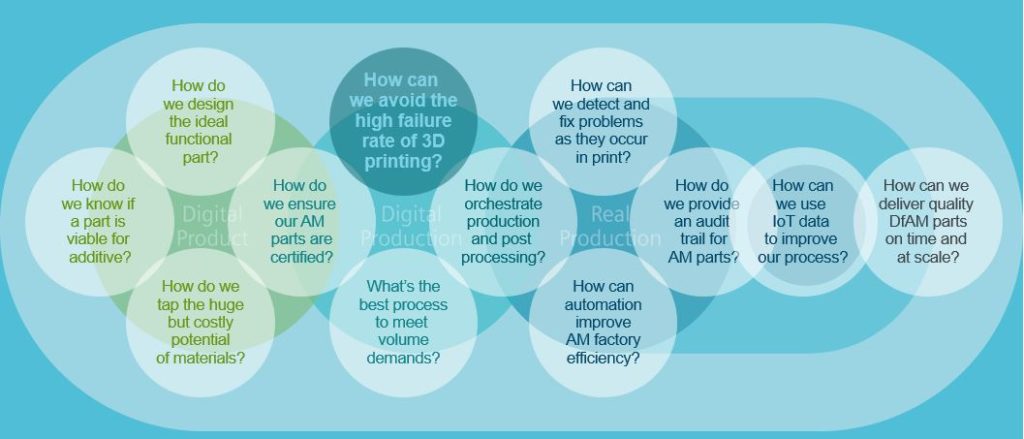
Reducing failures via software solutions
The overarching hurdle to meeting volume demands is achieving first-time-right printing – a difficult task. Printing a part correctly at scale requires careful research and expertise, often at a large expense, so companies are looking for creative ways to short-circuit this knowledge acquisition process. One way to do this is through software.
Additive manufacturing simulation software helps companies optimize their AM process without the lengthy knowledge acquisition learning curve. Additive manufacturing optimization software provides answers to difficult production problems by simulating the AM production process at various levels.
First, we will look at how users of AM can use software tools to alter their printing process. In November of 2019, Siemens acquired Atlas 3D and their AM simulation tool, Sunata. Sunata works with direct metal laser sintering (DMLS) printers to automatically provide design engineers with the optimal print orientation and requisite support structures for additive parts in real-time.
Atlas 3D’s Sunata™ software contributes to print quality by using
thermal distortion analysis to provide simple automation for optimizing part
build orientation and generating support structures. This method allows the
designer—rather than the analyst—to complete these simulations, reducing the
downstream analysis via software for achieving and meeting design requirements.
“Our solutions industrialize additive manufacturing for large enterprises, 3D printing service bureaus, design firms and CAD designers,” says Zvi Feuer, Senior Vice President, Manufacturing Engineering Software of Siemens Digital Industries Software. “The cloud-based Sunata software makes it easy for designers to determine the optimal way to 3D print parts for high quality and repeatability. The combination of Sunata with the robust CAE additive manufacturing tools in Simcenter enables a ‘right- first-time’ approach for industrial 3D printing.”
Siemens also has other tools for improving first article print quality. These include Simcenter 3D AM and the forthcoming Path Optimizer. These tools work at different levels to simulate the printing process in detail, attempting to identify and correct areas of distortion, shrinkage, etc. Simcenter 3D AM and the Path Optimizer both look at the deposition process in a very granular fashion, using different techniques to also help customers print first-time-right parts.
The future – First time right printing by default
As the processes for additive manufacturing continue to be refined, we expect first-time-right printing to eventually become the norm. However, this will take some time, and in the interim, simulation of the printing process is the best way to reduce the iteration cycle required to achieve high quality prints. Tools like Sunata, Simcenter 3D AM and Path Optimizer assist in this process, bringing the vision of a first-time-right printing closer to reality.
There is no overstating the benefit of addressing the challenges of high failure rates. Achieving a higher ROI is becoming a necessity to compete in the additive manufacturing space. Therefore, tools like these are becoming a requirement for advancing a company efficiently towards first-time-right printing.
This concludes the second blog in this series on the challenges of industrializing additive manufacturing, discussing first-time-right printing, providing technology for where today meets tomorrow. Our third blog will continue discussing this topic at a case study level, addressing build materials, durability, machine algorithms and fatigue properties for print build orientations.
Related Links:
– Additive manufacturing failures (Part 1)
– Press Release – Siemens expands additive manufacturing portfolio through the acquisition of Atlas 3D
– Additive manufacturing overview
– Webinar: Industrializing Additive Manufacturing 3D Printing through an Integrated, End-to-end Process
About the author:
Ashley Eckhoff has a background in engineering and has been with Siemens for over 20 years in various capacities. He has spent the past few years deep-diving into additive manufacturing in both product design and marketing roles.