Additive Manufacturing at Realize Live 2022
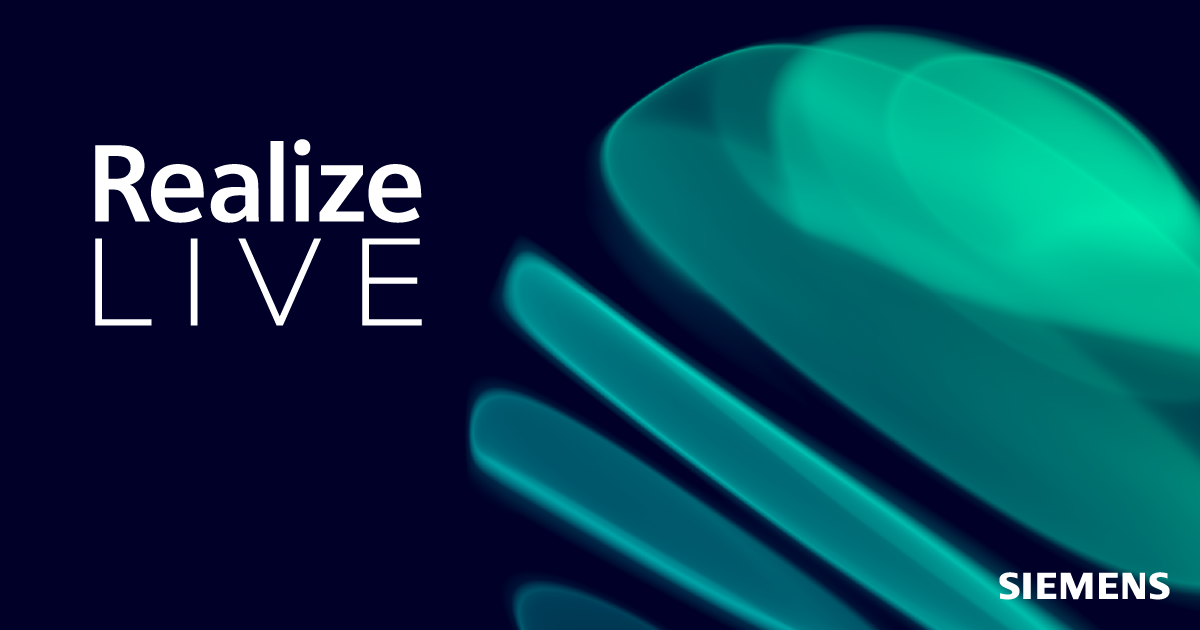
May 9th through the 12th is Realize Live Americas, where Siemens brings together internal experts and customers from a wide range of businesses to learn how to better solve the challenges of the day. That includes solutions for additive manufacturing (AM), and there are some great sessions planned. If you are not attending in-person there will still be on-demand presentations available free of charge – be sure and register – but here is a taste of what will be discussed this year at Realize Live 2022.
Kicking off the week, Jeffrey Blandford of Morf3D will be presenting on additive build simulation. Specifically, he will discuss how to compensate for the distortion of metals due to extreme temperatures and timescale gradients in the materials. These errors would typically require post-process machining to remove defects and return the component to the nominal shape. By implementing the right finite element analysis (FEA) process, however, the deformation can be simulated and compensated for before printing. Learn how to pre-distort your components by integrating FEA with advanced modeling technologies, robust workflows, and a handful of best practices to make AM a viable solution for your business. If you can’t make the session, check back here in the following weeks as I review this valuable information.
Another exciting session is being held by Taylor Anderson of Siemens NX, on algorithmic modeling in NX with our partner ELISE. Algorithmic modeling is a game changer for additive manufacturing design, because while AM machines can print highly complex geometries someone still needs to develop those shapes. Traditionally complex lattice structures or surface formations relied on hard-coded geometries and manual modeling, but now it can be done with a set of rules which the modeling software follows. If you are going to be here at Realize Live for additive design, this session should not be missed.
If you are working in design and manufacturing of AM parts on a daily basis, you probably know the importance of support structures to enable greater freedom of geometry. But you may also understand the tedium of some of the operations. To address these challenges to wider adoption, Cameron Tighe and Charles Garret of Siemens will be showing users how to create support structures more efficiently in NX. They will cover both automatic and manual supports, but possibly more important the best practices for modifying these structures. And to get this information in as many hands as possible, this session will be available on both Monday and Wednesday.
If you are not completely sold on the value of AM in your manufacturing process, Tod Parrella of Siemens will be presenting on how additive manufacturing is changing the way products are designed. It is driving an explosion of innovation for a variety of components for higher performance, greater efficiency, and more customization. Fortunately, as the innovations with AM have progressed so too have the most comprehensive development software solutions. Learn about structure modeling, improved simulation, and even design for manufacturing capabilities within Siemens NX for your next product.
We will also be joined by Sam Anand of the University of Cincinnati (UoC) to learn about design and pre-processing tools for additive manufacturing. Professor Anand works with the Department of Mechanical and Materials Engineering at the university in conjunction with Siemens to develop geometry-based pre-processing and simulation tools. Learn how the team has developed support structure generation, accessibility evaluations for support structures, orientation optimizations, and much more through integrations with NX. Many of the tools seamlessly integrate using C++, the NXOpen API, and Ufunc routines, and are being demonstrated for assignments and case studies at UoC for undergraduate and graduate courses. This session will provide insight on how these tools operate and why they are so important to AM.
The last important session for those interested in AM s not specifically about 3D printing, but much like the real-world AM will only be one tool available of many. Hosted by Roland Zaugg of GF Manufacturing Solutions and Bernhard Maurer of Janus Engineering, you will learn how to manufacture a Formula 1 double-walled turbocharger housing with AM and CNC processes. The high-performance designs of F1 cars require the complexity afforded by AM and the precision of CNC operations. This session will walk through the design, planning, and manufacturing process to create one-of-a-kind components for a groundbreaking sport. Learn how to implement a multi-step manufacturing process using state-of-the-art manufacturing technologies more effectively than before, even with integration of the factory environment.
If you can’t make it to Realize Live this year, we will miss you, but to make up for it I will be covering sessions like these as well as many others on sustainability and model-based systems engineering during the event and for the weeks to come. This information is important for the collaborative growth of the industries it benefits. And the following week, we will be at Rapid 3D to talk specifically about additive manufacturing and at Hannover Messa later this year to cover more of the manufacturing side of AM rather than focusing on design.