Drive every domain with Model Based Systems Engineering
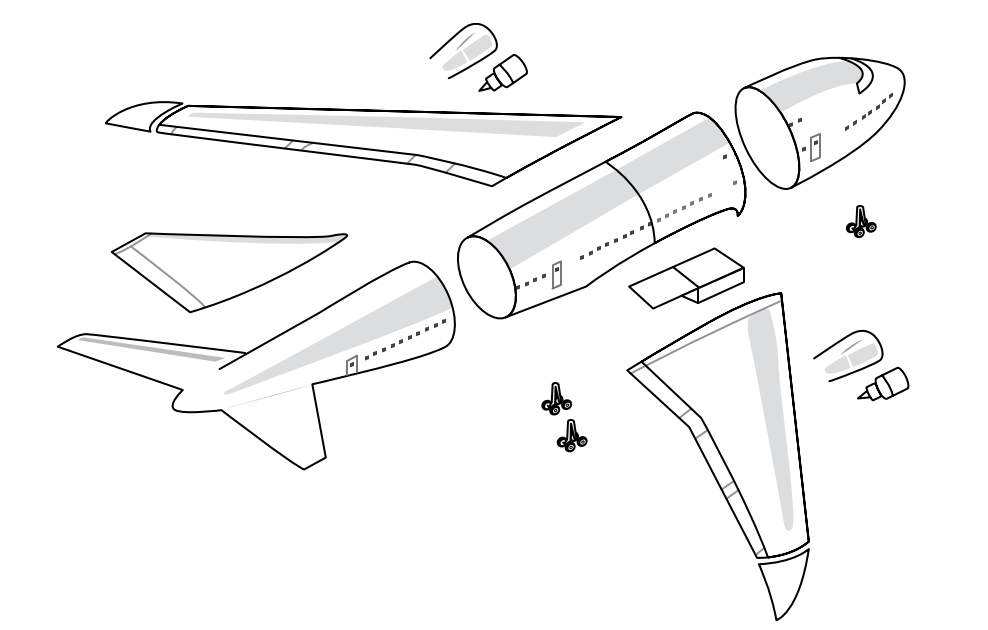
Manufacturing an aircraft successfully is a feat of organization and capability in and of itself, using math, science, and ingenuity to give humans flight. It is one of the greatest achievements of the modern world, but the ubiquity of flight has challenged what is acceptable in a design. It must be faster, safer, more comfortable, and more sustainable. Solving these requirements today is becoming much more involved, not only because there are more systems being integrated, but also because the growing number of requirements is making the balance point harder to find for a successful aircraft. For a while, the v-diagram of more traditional systems engineering was enough to drive every domain of an aircraft’s development, but the complexity of these new systems is grinding systems engineering methods to a halt. Model-based systems engineering (MBSE) on the other hand proliferates the knowledge on the system by managing requirements, modeling the system, verifying the results, managing integrations and much more.
MBSE makes successful programs more attainable, but for the full story check out the Siemens Special Edition of MBSE for dummies. To learn more about how the connections are being created between every domain, brush up on the Xcelerator portfolio.
Managing requirements
Any project begins with a determination of features and functions — if it’s a plane, you begin with the general vision of what functions the plane must achieve and under what circumstances. Imagine that you’re having dinner with the customer CEO and jotting it all down on a cocktail napkin. This plane can fly 2,000 miles, with a specific number of passengers, and a particular top speed over specific routes with their own set of conditions. All of these needs inform the architecture of the project, and the more complex the product the more requirements will be needed to define the system. Keeping this information in a single source of truth, rather than a number of different documents throughout the development process, ensures everyone in the program understands what needs to be done.
By explicitly managing all of this information more engineering work can be devoted to creating innovative solutions to the problems at hand. Rather than working on three complete systems, hundreds or thousands of options can be tested against the system requirements. Managed requirements enable flexible development practices, which is especially important for the transition to software and electronics in aircraft systems.
Modeling the system
Testing many design ideas is only possible because the requirements are linked to a single source and integrated with modeling capabilities. For example, a requirement might involve the flight characteristics for a wing, but it may not be fully defined. A robust modeling environment enables teams to test a variety of options before committing engineering of manufacturing resources. For a wing, that could be a litany of unique wing shapes or a previous design altered with a few key variables to find the perfect fit for the current aircraft’s needs. The model becomes ever more refined as information and ideas are passed between groups. Aerodynamicists may hand off a wing form to structural designers to create the internal support and receive an edited design back to remain within a requirement of the structural group. Whatever the series of events, this guided methodology surrounding the model lets everyone work together to create the best product.
Verifying the system
In a perfect world, after working together on an aircraft design it would be good to progress to the next phase of development. But our world is messy, mistakes can be made and assumptions of certain design choices can be wrong. MBSE provides a continuous framework to check whether the right decisions were made. Does the electronic control system reliable communicate accurate information about the state of controlled systems? Will an internal structure safely support the weight of an external component? Will a part survive the projected lifetime of an aircraft and can it be replaced efficiently? All of these questions are covered through verification of the entire development process from concept to service and even decommissioning.
Managing integrations
But what makes MBSE so valuable in complex systems, is integrating a disparate collection of work, often conducted around the globe for large aerospace projects. Parts from suppliers in one region need to interface with components designed in-house just as well as if everything where made by a single group. Managing the interconnections between suppliers and OEMs enables parallelization of design, shortening the overall development schedules of these massive projects. This management relies on the requirements first established in the concept phase and are iterated upon as problems are found and solutions applied. It is not solely the mechanical interfaces either, software needs to communicate with mechatronics components and understand the impact of hardware systems. A digital MBSE solution enables continuous integration across the entire development cycle.
While these are great reasons for adopting model-based systems engineering for your complex aircraft systems, they are only a handful of them. There are many more workflows and practices within an MBSE framework that enable complex development without the costly investment of time required by previous iterations of systems engineering. But for a more complete look at how MBSE accelerates aircraft development, our eBook on the topic is a great jumping off point. Chapter four walks through today’s discussion in greater detail, but if you are looking for a broader understanding, start from the beginning and work your way through.
And if you’re attending INCOSE this year, we will have presentations on MBSE for the aerospace, automotive and electronics industries. There will also be physical copies of MBSE for dummies available at the event. We hope to see you there in June!
Siemens Digital Industries Software is driving transformation to enable a digital enterprise where engineering, manufacturing and electronics design meet tomorrow. Xcelerator, the comprehensive and integrated portfolio of software and services from Siemens Digital Industries Software, helps companies of all sizes create and leverage a comprehensive digital twin that provides organizations with new insights, opportunities and levels of automation to drive innovation.
For more information on Siemens Digital Industries Software products and services, visit siemens.com/software or follow us on LinkedIn, Twitter, Facebook and Instagram. Siemens Digital Industries Software – Where today meets tomorrow