Structural performance simulation for 3D parts
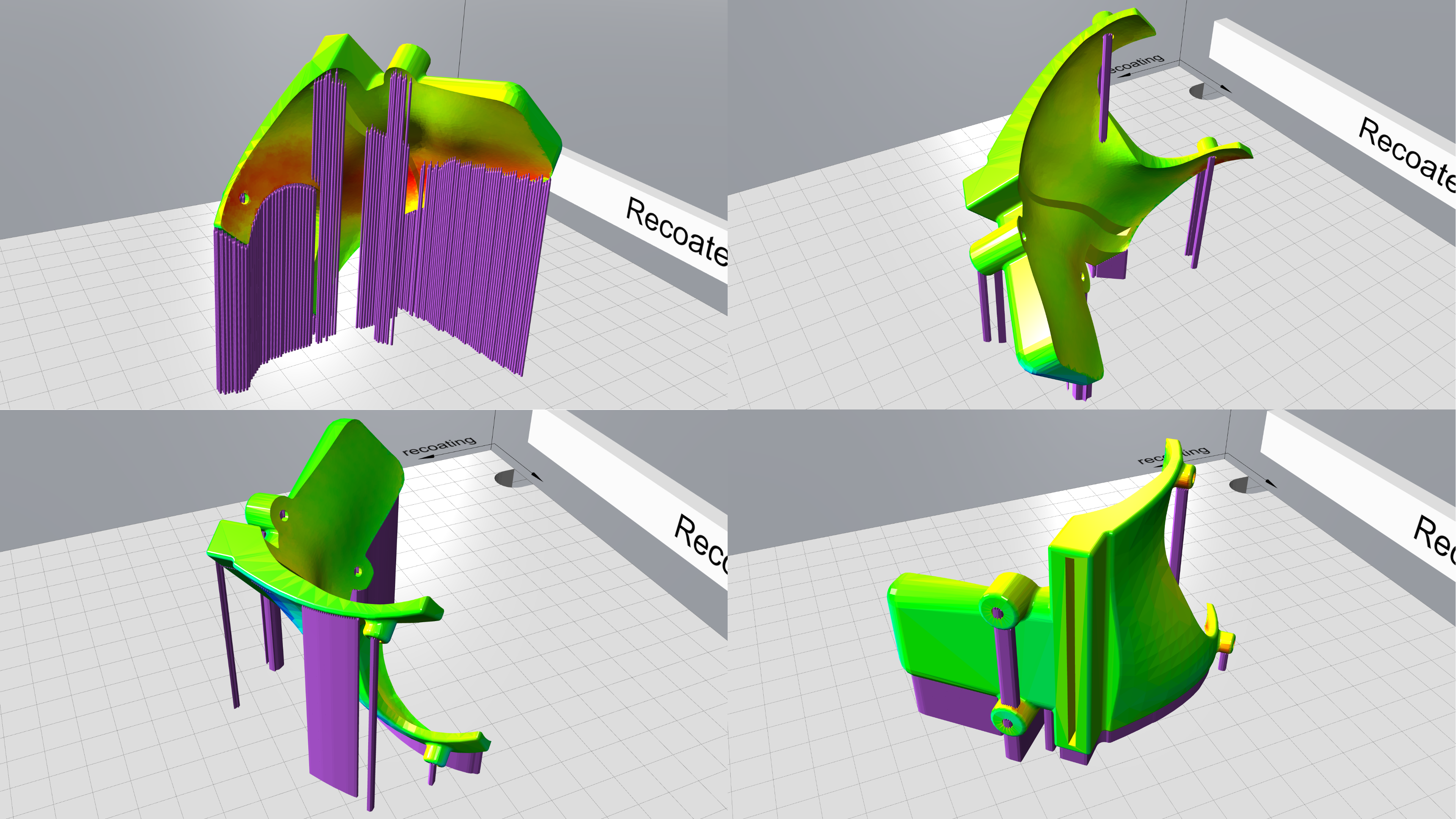
Additive manufacturing and 3D printing are seeing rapid adoption across almost every industry. That increased breadth of use is a fantastic sign for the possible applications of the technology, but in the short term it has revealed some of the problems that were not as relevant to the first wave of adopters – the tinkerers, the prototypers and engineers enabling the complex structures we have today at the press of a button. Many of the early applications were experiments in themselves, testing the limits of what the printers could produce and how make the software deliver the result from easy to use tools. But when a part is going into an airplane or the human body, it is critical to know how that part is going to perform and preferably without destructive testing on what can be very expensive components, that is where simulation comes into the story.
Simulation is another rapidly evolving tool in the engineering toolbox, fortunately it is much more mature and will be invaluable in printing the right components the first time. It shores-up many areas of the additive manufacturing process, from creating the optimal geometry for fluid flow or understanding how much mass can be shed from a part while retaining strength requirements to understanding how the printing process will progress along the toolpath. The latter, however, is more important to our discussion today as it contains many more of the unknowns in what produces the perfect part.
Multi-scale methodology
The need for multi-scale methods in 3D printing is two-fold, AM technology is not as intuitively understood compared to more mature manufacturing methods like casting and to compete on value with the more established techniques AM needs to offer something unavailable in other processes. To the first driver, simulation of process is tantamount to a successful print. Without the decades, and even centuries, of iteration traditional manufacturing methods leverage AM needs simulation to bridge the divide a produce parts that are reliable from the micro-scale to the macro-scale. Simulating too broadly at one scale may miss deformations that could result in unexpected stress concentrations or reduced durability. But simulating the entire component at a fine scale would likely provide too much data to effectively use the information being collected.
Multi-scale examinations are also valuable for the simulation of product, as complex additive parts are likely to include structures far more varied size than other manufacturing methods. The added complexity to improve performance often emerges as internal lattices in lightweight parts or in specialized fluid flow channels for cooling. Regardless of the application, there is a wide range in geometric scale and simulating fine structures with a course analysis misses data and fine analysis on course structures provides too much just as with the simulation of process. Only testing one situation would be analogous to only testing a Formula One car on straightaways and assuming it will perform fine in the corners.
Informed selection
There is no single solution for how to implement these solutions, just as with more traditional manufacturing methods. Granted there are rules of thumb that can produce good enough solutions to most problems, but finding the perfect solution often requires intricate understanding of the process, even an intuition which is why some forms of metallurgy are considered an art. But implementing multi-scale simulation into the workflow for additive manufacturing can act as training wheels for development. As more experienced is gained, there can be less reliance on the software solutions. But that analogy only stretches so far with AM, as multi-scale simulation will always be a part of the development process in the form of geometry optimization for part performance or in adjusting to changes in the printing process. Robust multi-scale simulation tools enable informed design, planning and production of additive manufactured components.
For a more broad understanding of the role of simulation in 3D part production for structural reliability, there is a great article by Tom Kevan from multiple experts in material science and additive manufacturing.
Siemens Digital Industries Software is driving transformation to enable a digital enterprise where engineering, manufacturing and electronics design meet tomorrow.
Xcelerator, the comprehensive and integrated portfolio of software and services from Siemens Digital Industries Software, helps companies of all sizes create and leverage a comprehensive digital twin that provides organizations with new insights, opportunities and levels of automation to drive innovation.
For more information on Siemens Digital Industries Software products and services, visit siemens.com/software or follow us on LinkedIn, Twitter, Facebook and Instagram.
Siemens Digital Industries Software – Where today meets tomorrow