Flow-based design for additive manufacturing
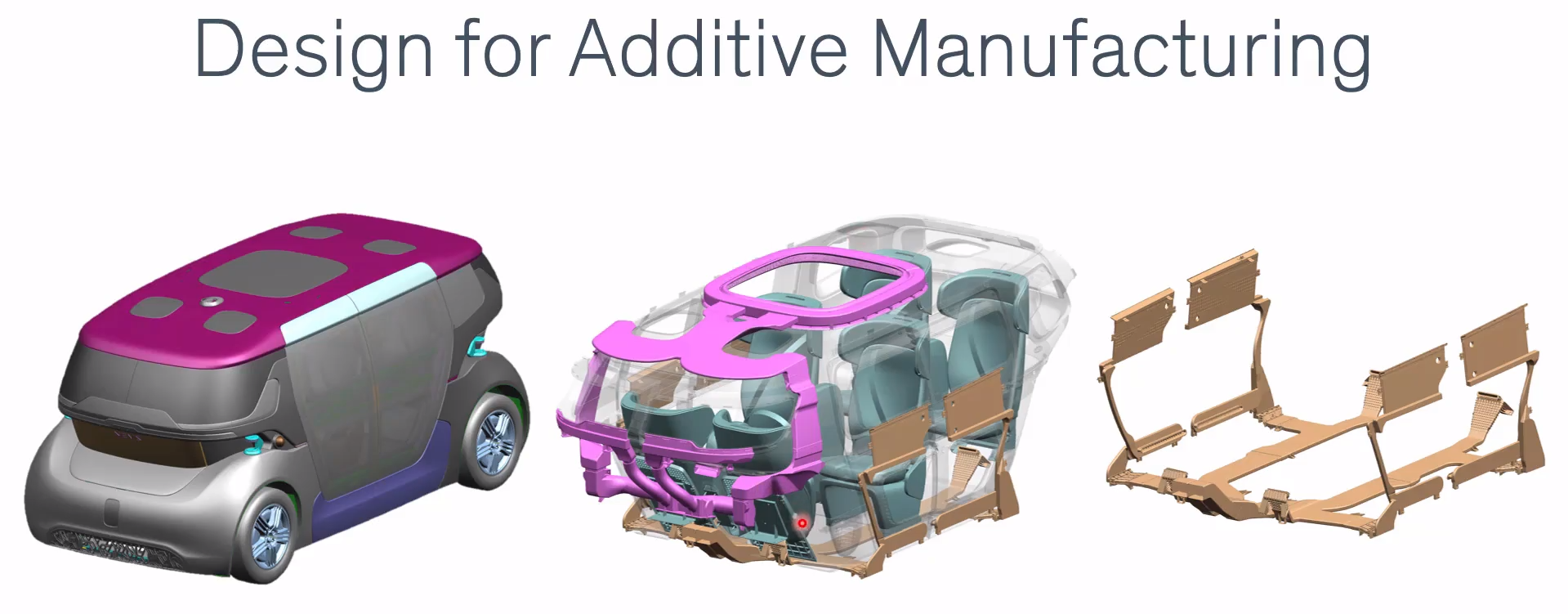
Realize Live has always been a way for our customers to speak with each other about how they are solving problems, both with software and expert guidance, and this year is no different even with it be virtual. One great presentation this year came out of a collaboration between the Swedish electric car manufacturer NEVS and Siemens experts in fluid flow and additive manufacturing. For the full story make sure to register for the Realize Live on-demand sessions before they’re gone at the end of June. But if you can’t make it for the session, here is a taste of what the teams discussed.
For a quick background, the NEVS team grew out of the rich heritage of another Swedish car company – SAAB – and a majority of their current engineering work is devoted to autonomous vehicle technology and their flagship vehicle, Sango. With an autonomous transport vehicle, NEVS was able to toss aside many of the common design choices for passenger vehicles to better accommodate a new transportation experience. These improvements to system architecture were not without hurdles, as the team found the limited design space of the mostly glass doors to hamper airflow for the heating system. To keep the air ducts from being visible, the team enlisted help from Siemens to optimize the airflow through the floor vents and doors vents with topology optimization and additive manufacturing (AM) to complete the system.
Fluid flow optimization
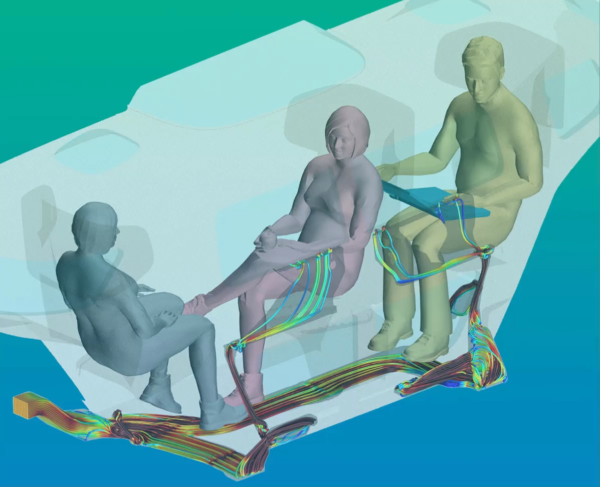
The first step in solving the problem was to understand the available design space within Sango, and fortunately this was already well known because the current heating system had been design to fill all available space in the hopes of increased flow performance. From here, Siemens’ simulation experts were able to model the flow path through the system and define the requirements for a successful heating duct. With that information it was time to optimize, through many iterations of the fluid simulation the topology optimization software can remove portions of the geometry that do not add to the final requirements of the system. That technique has two advantages for NEVS’ electric vehicle, firstly it improves the fluid flow of the heating system to reduce energy requirements to move the air, but it also reduces the overall weight of the system improving Sango’s range.
Preparation for additive manufacturing
The optimized ducting is not quite ready for manufacturing however, from the optimization there can be multiple artifacts that are left in the geometry. With enough compute time these would vanish, but it is far more time efficient to remove these with manual model techniques. Any simulation solution will reach a point of diminishing returns, and understanding when comes from experience with the tools. The cleaned geometry is now ready to start the manufacturing planning process, with the first step being how to segment what is essentially a vehicle sized duct system. Printing as one monolithic structure would be costly for a variety of reasons, using a printer capable of the print volume would be unsustainable due to costs of printer time and the assembly process for such a large component. Instead the most dramatically altered geometries are pulled from the model and sent along the printing process.
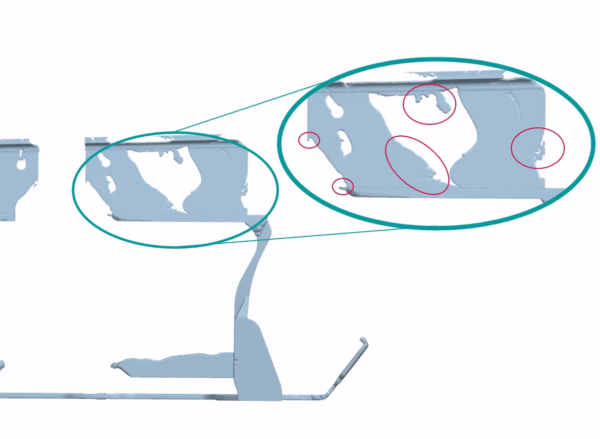
Removing the fluid-optimized geometries results in smaller component sizes for printing, but in NEVS’ case also leaves the untouched duct sections as candidates for the traditional manufacturing processes they were designed around. This can save money by using processes optimized for large lot sizes like injection molding for the more basic geometries and using AM only where it adds value to the project. After segmentation, the parts destined for AM are still not entirely ready for the printer, they still need to be converted to thin-walled bodies. The simplest action to accomplish the final geometry is to create an offset surface outside of the fluid-flow geometry and then remove the internal geometry. To successfully print the parts it is important to understand where the part might be too thin, and where it becomes susceptible to deformation during printing.
While the collaboration between NEVS and Siemens is not yet complete, their story is a great example of how fluid-based design is implemented today. It also captures many of the sub-processes required to successfully create components with additive manufacturing technologies. The presentation is full of details on how much of this process is conducted and is a highly recommended resource for engineers and companies looking into flow-based design for their projects, register for the additive manufacturing sessions at Realize Live to earn more.
Siemens Digital Industries Software is driving transformation to enable a digital enterprise where engineering, manufacturing and electronics design meet tomorrow.
Xcelerator, the comprehensive and integrated portfolio of software and services from Siemens Digital Industries Software, helps companies of all sizes create and leverage a comprehensive digital twin that provides organizations with new insights, opportunities and levels of automation to drive innovation.
For more information on Siemens Digital Industries Software products and services, visit siemens.com/software or follow us on LinkedIn, Twitter, Facebook and Instagram.
Siemens Digital Industries Software – Where today meets tomorrow