Expanded automation for additive manufacturing
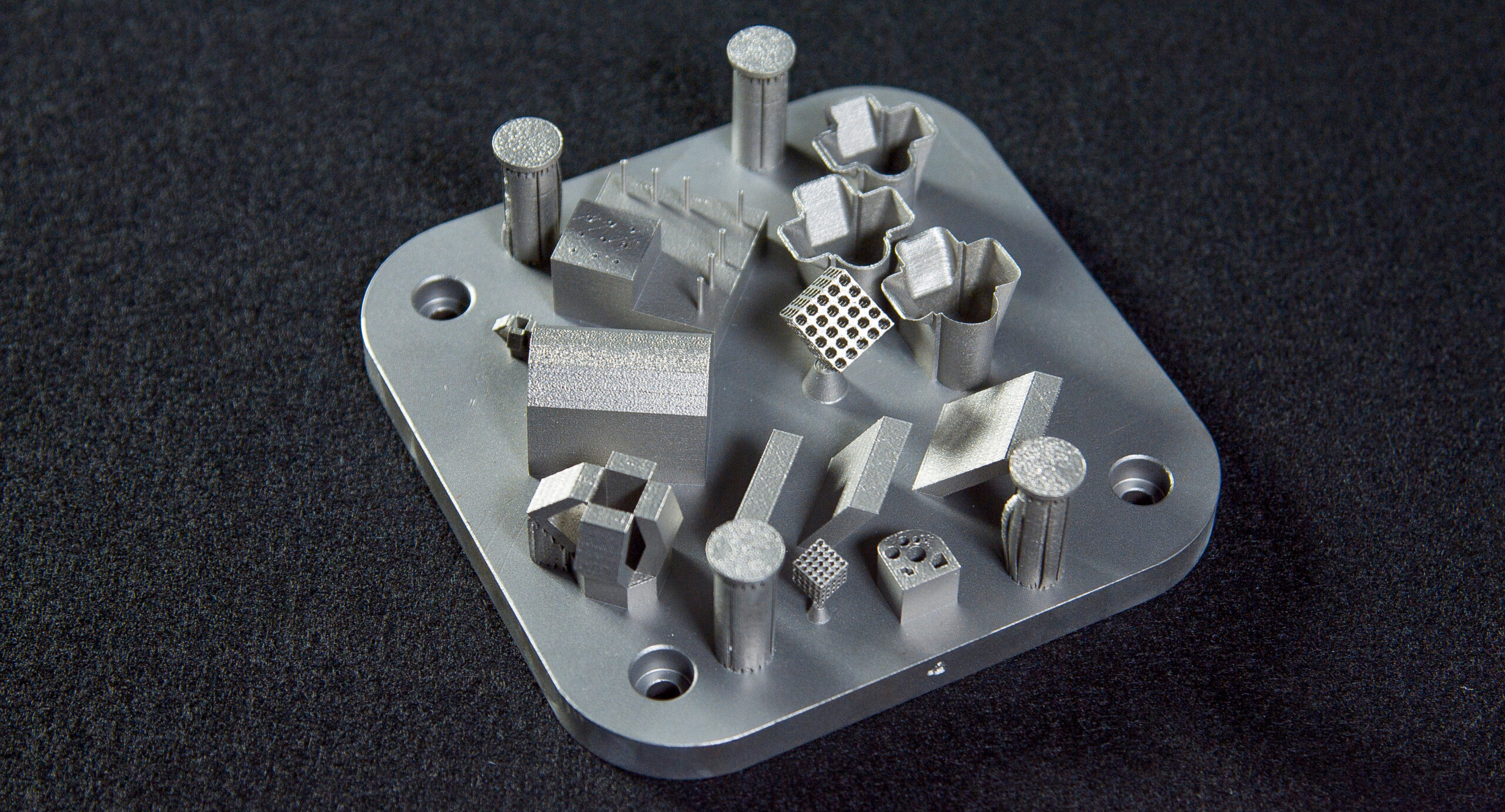
Realize Live and the User to User conference are online again this year, but there is still so much to discover about industry innovations around additive manufacturing (AM). To kick off the sessions around AM, Aaron Frankel the VP of Siemens’ additive manufacturing software program covers the advancements that have been made in cooperation with users over the past year. The most notable of these advancements is the expansion of automation across every phase of development – neatly separated into design, planning and production automation. For the fullest experience make sure to register for Realize Live, but as a taste here are some of the major topics from Aaron’s presentation.
Designing parts for AM has come a long way, many of the geometric capabilities once only accessible with complex coding and manual modeling are integrated features in the top software packages and simulation capabilities have accelerated the adoption of generative engineering solutions. But for many of these advancements to catch hold in the industrial manufacturing sector with high volume implementation, more design autonomation is needed. For custom printed products, teams need to be able to flow data gathered in the order management system into the design processes with limited intervention. Some companies are implementing generative engineering to deliver custom parts optimized to their requirements whether those are biotic geometries for prosthetics or climate control ducts for vehicles.
And from the design phases, it is essential to automate manufacturing planning removing points of error from the process whether that means compensating for printer capabilities or simulating printing to ensure the right print comes out of manufacturing. But one of the greatest time savers for teams working with AM processes, is the automation of build preparation. This can be a tedious job encompassing not just optimal orientation of a single printed part but finding the optimal orientation for entire lots fit into the build tray. Making sure that work is not wasted, build simulation ensures the printing task will finish without error or damage. It is also rare that a part’s only step is printing, but making the decisions on how it is depowered, surfaced or implemented in a greater system is a lot of manual work when producing large quantities of custom parts. Automating all of this saves engineering time and overall manufacturing time because the entire workflow can be optimized.
With a great part design and manufacturing plan, it is time for production. Usually this means transferring the final files to a slicing tool to convert the 3D geometry into a usable set of instruction for the printers. But by integrating printer information directly into the design and planning environments this can be automated. Connecting the manufacturing processes to the rest of development also enables high-level optimization based on the factory monitoring data of many new production machines. Production capacity can be balanced across machines to improve printing times. Print quality data and analytics can be utilized to optimize printers as well or alert maintenance staff that a machine is in need of service because it is falling behind other machines. By extending partnerships with machine manufacturers, prints will no longer be qualified for individual printers but any machine of the same make, with the possibility of entire product lines in the future.
The possibilities in digitalizing automating the additive manufacturing workflow are growing every year with investment from software companies like Siemens, but also from the everyday users and researchers working with the technologies on their passion projects. For the full story of what is available today, Aaron Frankel covers it all in his keynote you can find in the agenda. For specific solutions to your problems today or just in the interest in innovation, there are plenty of additive specific sessions this year. All presentations will be available through June 25th.
Siemens Digital Industries Software is driving transformation to enable a digital enterprise where engineering, manufacturing and electronics design meet tomorrow.
Xcelerator, the comprehensive and integrated portfolio of software and services from Siemens Digital Industries Software, helps companies of all sizes create and leverage a comprehensive digital twin that provides organizations with new insights, opportunities and levels of automation to drive innovation.
For more information on Siemens Digital Industries Software products and services, visit siemens.com/software or follow us on LinkedIn, Twitter, Facebook and Instagram.
Siemens Digital Industries Software – Where today meets tomorrow