Accelerating battery manufacturing with Capgemini – Battery Podcast S01E09 – Transcript
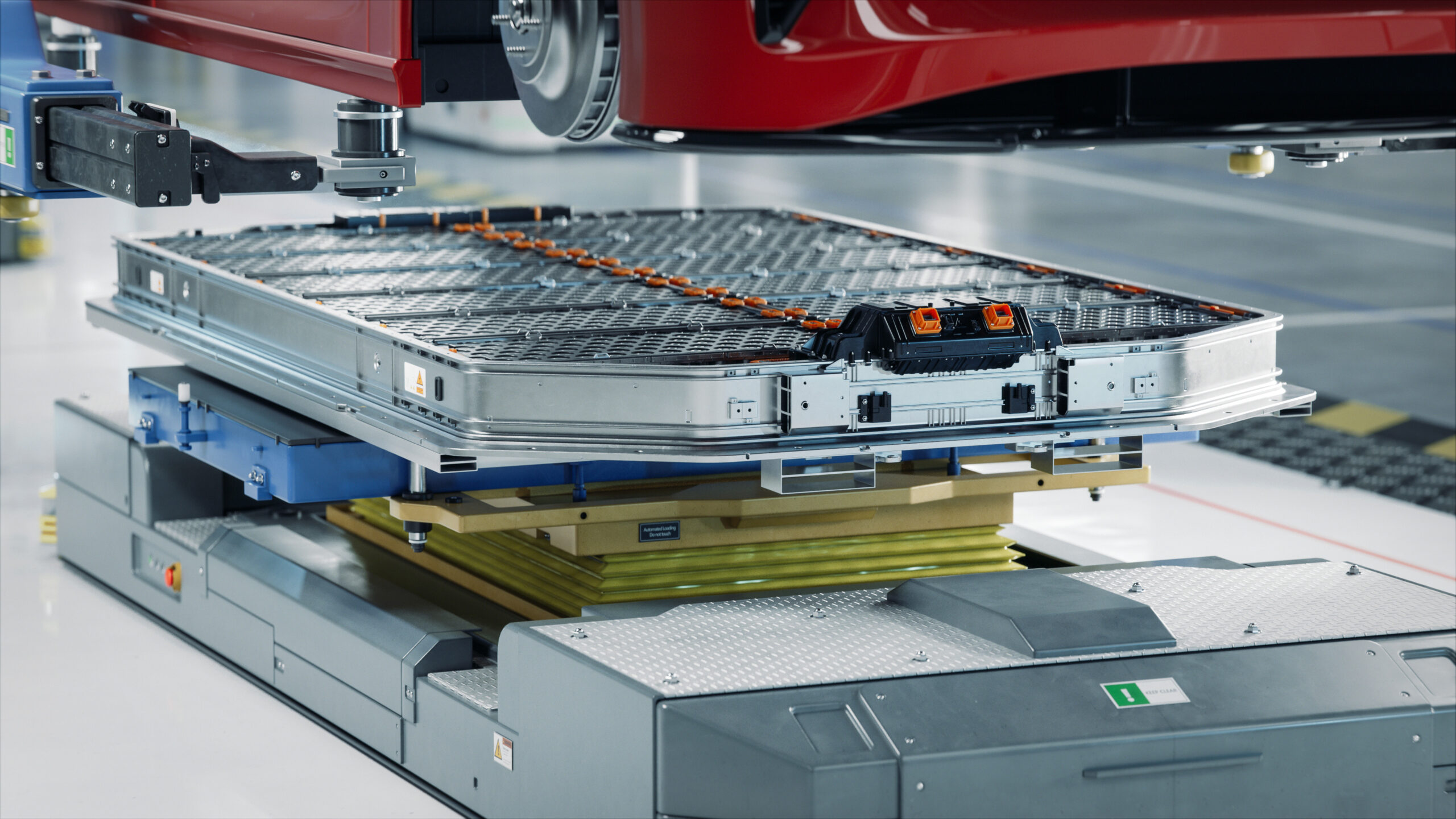
Here is S01E09 of the Battery Podcast, with our host Puneet Sinha talking about the acceleration potential of battery manufacturing with guest Pierre Bagnon of Capgemini. Let’s dive into the discussion!
Nick Finberg
Welcome to another episode of the Battery Podcast by Siemens Digital Industries. In this episode, we delve into the race to develop gigafactories, where Siemens and Capgemini are at the forefront, accelerating the battery manufacturing market. As the demand for electric vehicles rises, efficient scaling of production is becoming critical to success. Together, Siemens and Capgemini are leveraging their expertise in digitalization and industrial automation to advance battery production capabilities. In today’s discussion we’ll uncover the innovative solutions they’re pioneering and their implications for the future of sustainable energy. Joining us to discuss this are Puneet Sinha, Senior Director of the Battery Industry at Siemens, and Pierre Bagnon, Executive Vice President at Capgemini. Puneet, over to you!
Puneet Sinha
Welcome, ladies and gentlemen. I’m excited to have you here for this presentation. I’m Puneet Sinha, Senior Director and in charge of battery industries for Siemens Digital Industries Software. And with me today is Pierre Bagnon.
Pierre Bagnon
Hello, Puneet. Hello, everyone. Pleased to be with you today. I’m Pierre Bagnon, the head of the Intelligent Industry Accelerator within Capgemini.
Puneet Sinha
Battery Gigafactory, it’s a race. Races are exciting, but they are also a challenge. To win, one needs the right preparation and the right team. Today, we want to show you that how Siemens and Capgemini can be the right team for you to win in this fast evolving battery production landscape.
Pierre Bagnon
Thank you, Puneet. Well, indeed, Gigafactory have been a race. And to understand this, there is a booming adoption of the EV and hybrid vehicle on the market also amplified by the adoption of electrified public transportation, energy storage. So, all together, that’s a complete new ecosystem, new value chain that is being created, taking into consideration new mine for cobalt, lithium, manganese, equipment providers, and also production capacity. Actually, we estimate $300 billion being the investment by 2030 that will be injected to create this new industry. And the production capacity will have to be multiplied by 14, 1-4, which means over 90 production, so gigafactories, are being planned and built across the world. So that’s a different scale, and this comes with few challenges. Puneet, will you tell us a bit what type of challenges you see?
Puneet Sinha
Absolutely. When it comes to gigafactories, there are many challenges. I want to focus on a few, starting with the time it takes to build gigafactories and ramp up production. Recent examples have shown us that many companies are taking five to seven years to reach stable large-scale production from the time they announce gigafactories. That’s too long a time in this rapidly changing market. Second, very high scrap rate. Based on our conversation with battery industry, we have seen 40% or higher scrap rate at the start of production, and even for fully functioning factories, scrap rates have hovered close to 30%. That is too high a scrap rate to have cost-effective large-scale production. Even few percentage reduction in scrap rate means hundreds of millions of dollars of cost saving. Other challenges are improving quality and improving factory throughput. Pierre, tell us what are the other challenges you are seeing.
Pierre Bagnon
Yeah, right, Puneet. So we mentioned about speed, and fundamentally that’s a race. We mentioned about quality, ramp up. On top of this, and this is a bit more specific to this industry, we can name talent wars, sustainability, and traceability. Let me take some examples here. There is truly a fierce competition of talent currently, considering electrochemists, system engineers, technology players understanding the battery space. Gigafactories have to anticipate the workforce they will need. Take the example of a 30-gigawatt factory. It takes 3,000 to 4,000 employees, which means engineers, technicians, maintenance players that will have to be trained. Sustainability, of course, is a key element. Sustainability will fall under two aspects, energy consuming. In the energy consumption part, it takes about 50 to 60 kilowatt hour to produce one kilowatt hour battery. So that’s quite energy, and here the industry again will have to improve. Still on the traceability, we have to quite understand what will happen upstream with the raw material and that stream. So upstream, it’s about traceability to ensure the origin, quality of the raw material. Of course, through the manufacturing process, a full traceability of the product and the process and what happens during its lifecycle, understanding the process, trace it, and the dismantling part. So that’s part of the new challenge actually that this industry has to face. And for this, the digital is a key lever. Now, to deep dive a bit, and we understood that speed, race is a key element. Puneet, could you tell us a bit what are the levers and the technology that notably Siemens is putting forward on how to build fast and accelerate the production ramp up of those Giga factories?
Puneet Sinha
Absolutely, Pierre. One of the foundational pillars to build a fast and accelerate ramp up is simulation first approach. Siemens brings digital twin of cell as a product, manufacturing processes, and digital twin of factories. With our digital twin of product, companies can evaluate virtually impact of chemistries on cell performance, cell safety, cell aging. They can also optimize their cell designs to maximize energy density and fast charging. And more importantly, they can validate those designs to meet pack and system requirements. We have seen adoption of these digital twin frameworks bringing 2 to 3X improvement in the overall product engineering. Similarly, digital twin of manufacturing allows companies to virtually design lines, plans, and optimize production process before implementing them on the factory floor. This avoids costly tweaks that companies may have to do later on. We also bring a PLM backbone that connects all these digital twins of product, process, and factories, and it allows companies to account for interconnectedness, effect of change in the whole life cycle. Other key important point is it’s not enough to just have digital representation of your product, your process, and factory. These digital representation needs to be connected with the physical work that is the real factory. We bring that digital to physical connection and thus accelerate physical commissioning, rapid integration of innovation and change. Let me move to another question. Pierre, help us understand how Siemens and Capgemini coming together can reduce scrap rate while improving quality and throughput.
Pierre Bagnon
Thanks, Puneet. Scrap and quality after speed is probably the number one issue that Giga factories actually face. Take the example of running Giga factories. They usually run at the 30% scrap rate, which is out of standard in the automotive industries. Taking the example of greenfield, it’s above 40% scrap rate that they will have to face. So there is truly here a big challenge, a challenge that is explained by the complexity of the production processes. It’s 600 manufacturing steps, partially automatized with data but very scattered. So there is no holistic view yet on how to treat the quality challenge. And the challenge is big and the state important because taking the example of the 30-gigawatt Giga factories, by improving by 10% the quality level, it’s basically 200 to 300 million of gains that a Giga factories will do. So it pays off all the investment on data. And data here is quite important because when talking to Giga factories or battery producers, it’s 30 to 50 use cases that they usually unveil on how to improve the quality. So I mentioned it and part of the foundation and the backbone is on how to capture data. How to capture data not only on the equipment but the full process and product part to understand at any point of time how the process is deviating and anticipating this quality. So IoT here is key. It’s key in order to get the data, of course, combined with edge because there is a big amount of data, a lot of integration to be made, and this is where AI is necessary. So what are the different use cases that we typically see? Well, it’s about in-line quality systems, visual computing in order to measure the slow-reviscosity, for example, or model that help basically to predict the electrical behavior during the edging process. So that’s part of the example that you see. Now, in order to make those use cases happen, you need a solid data platform and a standardized data model. This is absolutely key in order to ensure the interoperability and whatever the data sources be, the possibility to put those data together. Now, Puneet, on the execution part, what do Siemens do?
Puneet Sinha
Thanks, Pierre. This is what we call end-to-end integration of the overall production process. With Siemens integrated hardware and software for MOM solution, we bring execution insight that is critical to enforce best practices for battery cell manufacturing. Also, with our industrial IoT technologies and automation technologies, Siemens bring a connected system, bringing IT and OT technologies together that improves the data harvesting coming from machines in the factory. This data-driven manufacturing operation is critical to introduce or improve closed-loop manufacturing process, bring predictive quality, improve process optimization. This is desperately needed in the industry, both by startups but also incumbent battery manufacturers so that they can reduce their scrap rate, improve quality, and the manufacturing throughput. So, Pierre, we talked about scrap rate. We talked about how to build fast. How about looking at the future? What do you think will ensure that the future gigafactories can be scaled fast, companies can repeat, replicate them easily, and are ready for what is coming in the future?
Pierre Bagnon
That’s a very important aspect, Puneet, because the race is not only about going fast in ramping up one gigafactory, but for our clients, it’s about scaling gigafactories across new production networks. And this is multi-geo. So, and it comes with few challenges here. For this, they need basically a blueprint that make sure that starting on the digital part, they build what we call, and here Siemens and Capgemini are paying particular attention, a digital IT/OT architecture that will be scalable, interoperable, modular, but also from a cybersecurity bulletproof. It’s quite key in order basically to assist through the industrial phases, so the R&D line, the pilot line, the first range of the gigafactories, and the following gigafactories, all the modulatory and the evolution. And here, it creates two question. The first one is how to bring an industrial and digital system that is robust enough to secure the SOP and industrial startup, and then that is evolutive enough actually to accommodate all the innovation and differentiation that our clients are pulling forward. So on top of digital, we have also to consider the physical part, the organizational process, and this is where Capgemini is helping gigafactories to put and design what we call a target blueprint, which will encompass the operating model, the standard process, the example of production, of quality, or maintenance, but also supporting them in the industrialization phase.
Puneet Sinha
Absolutely, Pierre. One central tenet of bringing this holistic approach for future replicability, future readiness, is to have comprehensive solution. We bring digital twin software, automation technologies, industrial network, and cybersecurity. This comprehensive solution allows a centralized interfaces, data, libraries that essentially allow for machines to be easy plug and play in any gigafactory. Together with Capgemini, we also ensure that these solutions can be implemented fast and efficiently. So Pierre, thank you for having this engaging conversation. I hope our audience has gotten some insight into how we bring end-to-end solution and services in our partnership. Siemens brings technology and solutions, as I mentioned, digital twin of battery product and production, automation and industrial IoT technologies, IT/OT architecture, standardization of machine integration, and the expertise of our personnel. I believe in this partnership, Capgemini is a perfect complement across all these aspects through their services and offering. Tell us more about Capgemini.
Pierre Bagnon
Indeed, we have very complementary offering capabilities. So here, Capgemini will bring a range of professional services, starting with management consulting or strategy consulting and helping your clients to design their industrial strategy, but also digital strategy, this IT/OT architecture, combined with capability to implement on the IT solution part and the OT also business process out serving. And what makes us quite unique, actually, is the capability to bring on top engineering services with battery expertise, engineering services on system integration, system validation, process design, and also all the supply chain. And this is all together combined with Siemens and Capgemini that we have a quite unique combination to help our clients to accelerate and create an industry that is not only efficient but sustainable.
Puneet Sinha
Absolutely. So in summary, Siemens and Capgemini partnership brings the needed solutions, services, and expertise that can help battery industry reduce its ramp-up rate for gigafactories 2x faster, help it reduce its cap rate three times faster than the traditional practices. With these business values, we believe our partnership can help win companies in this gigafactory race. If you want to find more about our solutions, please come and visit Siemens and Capgemini booths. We have our experts there to answer your questions. Thank you for joining this presentation, and we look forward to doing business with you in the near future. Bye-bye.
Pierre Bagnon
Thank you, Puneet. Thank you.
Nick Finberg
Thank you to the audience as well. We hope you find these discussions from the show floor an interesting augment to our other discussions around the battery industry. Be sure to subscribe so you don’t miss future episodes. And until next time visit us at Siemens.com/battery