Accelerating flexible and sustainable food production
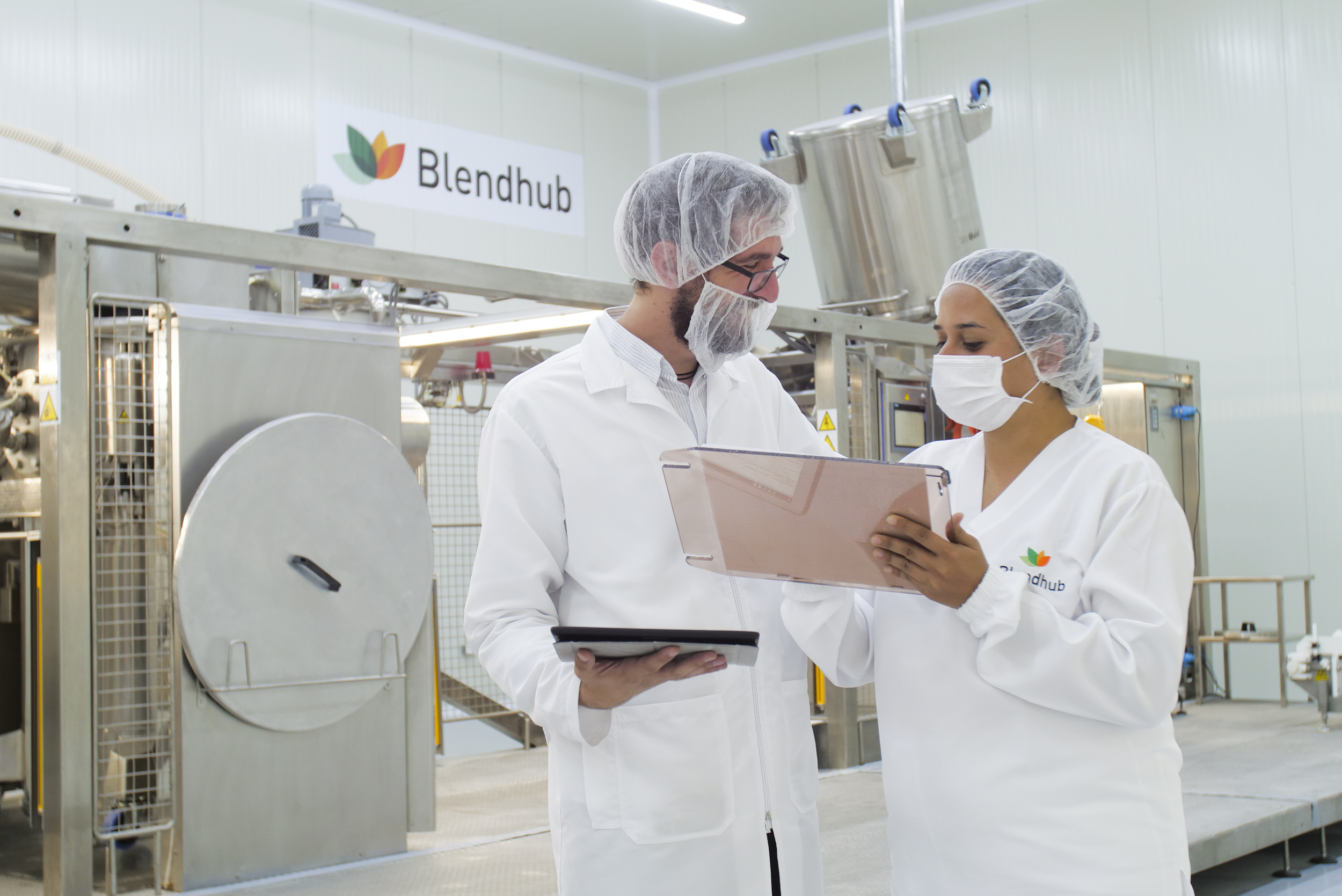
Food insecurity is one of our oldest problems as humans. And even with the vast technological advances over our time on earth, 820 million people suffer some form of hunger each day. There is a huge disconnect between supply and demand when so many are hungry and a third of food produced globally is wasted or lost. Part of this disconnect comes from the immense distance foods travel from where they grew to people they nourish. The global food market brought access to nutritious foods to many and helped grow our modern economies, but it has left many behind.
On a mission to help correct the inequities of food insecurity, our customer Blendhub is making food security a sustainable mission. Their goal is to transform food production and facilitate access to healthy, affordable, and local products. They are using digital twin technology and software-defined automation to bring the idea to life. Two key aspects of BlendHub’s approach to food availability are modularity and agility.
By working from a modularized design contained within a 40-foot shipping container, they can reduce their cost overhead and complexity to deliver food reliably to those in need. Their micro-factories can be deployed quickly as well, relying on existing infrastructure for transportation via marine freight. Modularization also helps get production facilities up and running faster with local help. Without unique equipment in every deployment, it is easier for locals to learn how to operate on their own.
BlendHub’s focus on agility is important beyond getting food to those in need as fast as possible. It also enables the tuning of what’s produced to the local needs. Certain areas might have higher rates of one nutrient deficiency over others and tweaking recipes to the need provides much better outcomes. It is also important to understand dietary requirements of the regions in need or the availability of local produce to further tweak what is being made for the community.
The modularity and agility BlendHub can achieve is possible because they start to define and optimize the systems they need in the virtual world. This reduces both the need for material and cost intensive prototypes. Their work in the digital world has also brought down the deployment time for their micro-factories. A factory can be on-site in six months, compared to the years it can take for others. And once their hubs are deployed, they can be easily monitored and controlled by operators in real time to ensure the customized recipes are being completed as correctly.
For more information about BlendHub, you can visit our website.
Siemens Digital Industries (DI) is a leading innovator in automation and digitalization. In close cooperation with its partners and customers, DI is the driving force for the digital transformation in the process and manufacturing industries. With its Digital Enterprise portfolio, Siemens provides companies of all sizes with all the necessary products, along with consistent solutions and services for the integration and digitalization of the entire value chain. Optimized for the specific requirements of individual industries, this unique portfolio enables customers to enhance their productivity and flexibility. DI continuously extends its portfolio to include innovations and the integration of future-oriented technologies. Siemens Digital Industries, with its headquarters in Nuremberg, has a workforce of around 72,000 people worldwide.
For more information on Siemens Digital Industries products and services, follow us on LinkedIn, Facebook, Twitter, and YouTube.