Deploy smart manufacturing to conquer complexity
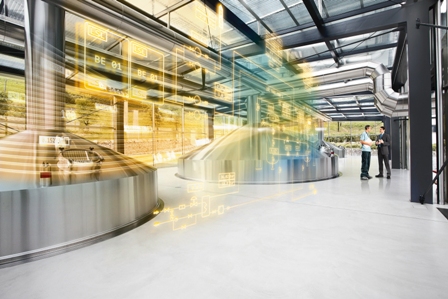
As the world becomes more interconnected, manufacturers demand sleeker, more personalized machines to stay ahead of the competition. Likewise, original equipment manufacturers (OEMs) are eager to meet their customer needs while adhering to strict deadlines and tight cost margins while satisfying new environmental and compliance requirements. Due to pressure from both customers and governments, machine builders have felt the need to digitize.
Digitalization can be a complex process, but it boasts many rewards. Digitally transforming processes can help OEMs answer customer needs, meet regulatory standards, and get closer to achieving zero defect manufacturing, all while keeping costs down and productivity up. Implementing smart manufacturing solutions enables machine builders to:
- Unify data
- Manage complexity
- Reduce errors
Unifying data
Today, many businesses operate a diverse pool of machinery. And many machines utilize separate interfaces all while generating different types of data in disparate file formats and creating disconnected processes. Without homogenous processes, it is difficult to manufacture machines that meet current electrification, digitalization, and sustainability standards.
Smart manufacturing solutions guarantee seamless data exchange between design, engineering, and manufacturing. Promoting access to data between these teams helps companies develop efficient manufacturing processes from the start as well as identify issues and opportunities for optimization on the shop floor earlier. As a result, machine builders can manage more complex requests from customers while realizing massive time and cost savings.
Managing complexity
On top of encouraging collaboration, the smart manufacturing approach aids companies in boosting throughput, reducing downtimes, and overall improving manufacturing key performance indicators. Inter-team connectivity empowers business to align planning, execution, and quality, which in turn simplifies managing complexity across any facility around the globe.
Smart manufacturing solutions can also simplify systems. Integrating manufacturing operation management (MOM) and manufacturing execution system software with product lifecycle management (PLM) and enterprise resource planning (ERP) systems ensures that all sources of information are easily accessible. With increased data transparency, companies can bolster productivity, sustainability, and consistency.
Overall, uniting data and merging systems allows manufacturers to deploy closed-loop manufacturing. Closed-loop manufacturing execution can lead to long-term benefits such as improved manufacturing speed and process optimization and can even streamline interactions with suppliers and customers.
Reducing errors
Data consolidation and system integration offered by smart manufacturing solutions creates a single source of truth that helps companies get closer to achieving zero-defect manufacturing. If design, engineering, and manufacturing are sharing common information, the number of reworks will decrease, reducing both time to market and waste.
Meanwhile, on the shop floor, assimilating MOM, PLM, and ERP systems improve defect detection and reduce production risks by giving workers the knowledge and tools to make informed decisions. This combined with the increased collaboration of the design, engineering, and manufacturing teams can make zero-defect manufacturing feasible.
Welcoming future innovation
To address today’s challenges and stay competitive, OEMs have begun to increasingly digitize their process. Despite being an intimidating task in the short-term, the smart manufacturing approach boasts both immediate and long-term benefits that will foster resilience and efficiency.
Smart manufacturing solutions allows companies to connect their operational data, enabling seamless data exchange between design, engineering, and manufacturing which in turn helps machines meet electrification, digitalization, and sustainability requirements all while keeping costs low. Utilizing the smart manufacturing approach, companies can simplify managing their factories around the globe.
Another benefit of smart manufacturing is system integration. Integrating systems increases the possibilities, facilitating closed-loop manufacturing. And when combined with data consolidation, it can reduce reworks while improving fault detection and correction. Eventually, zero-defect manufacturing becomes attainable.
Ultimately, deploying the smart manufacturing approach optimizes processes, streamlines operations, and inspires companies to be future ready. Here at Siemens, we have an extensive library of digital tools that can help your organization defy today’s expectations and anticipate tomorrow’s needs.
Siemens Digital Industries Software helps organizations of all sizes digitally transform using software, hardware and services from the Siemens Xcelerator business platform. Siemens’ software and the comprehensive digital twin enable companies to optimize their design, engineering and manufacturing processes to turn today’s ideas into the sustainable products of the future. From chips to entire systems, from product to process, across all industries. Siemens Digital Industries Software – Accelerating transformation.