A decade of Battery Innovation – Why does a chocolate expert make battery slurry?
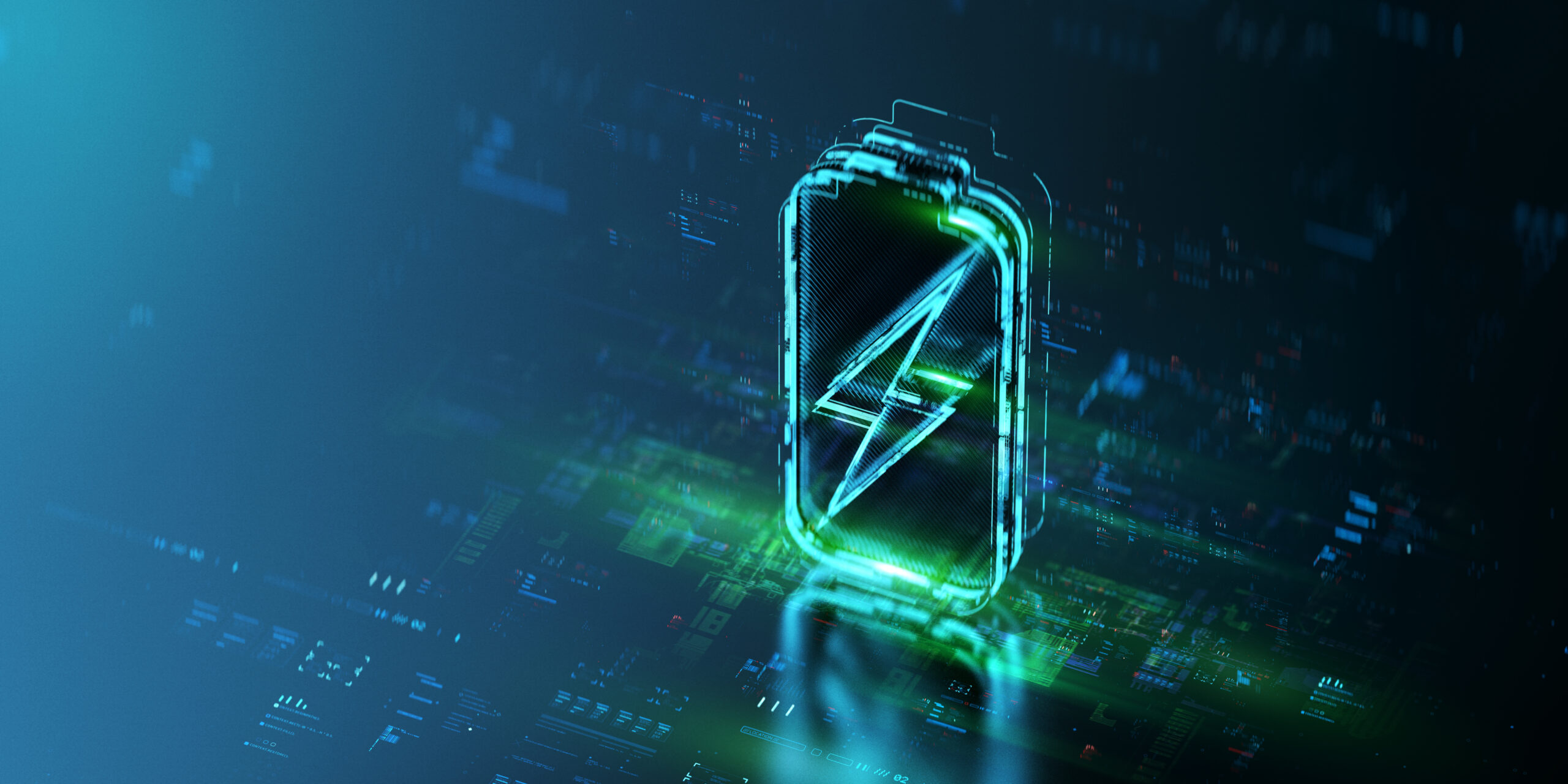
What do chocolate and batteries have in common? A lot more than you might expect, though the taste award definitely goes to chocolate. For the seventh episode of The Battery Podcast from Siemens Digital Industries, our host and battery manufacturing expert Marc Deyda sat down with Adrian Spillmann, the Market Segment Director of Battery at Bühler. If you know much about the food and beverage industry, that company name may sound familiar. They are a process solution provider for food manufacturing, as well as many other advanced materials processes. And the name is not the only similarity between batteries and chocolate – continuous mixing and extrusion are vital to successful production in both.
Though the entire conversation is not about the similarities between chocolate and batteries, this short session with experts on battery production is a great primer for understanding the manufacturing side of the battery industry. You can listen to the full episode below and keep reading for some of the most important topics from the discussion.
Bühler’s pioneering work in continuous mixing the battery electrode solution has many benefits for lithium-ion battery production. Continuous mixing allows the combining of all the unit operations in a single, continuously operated machine. Doing so reduces the number of needed mixing lines, increases their productivity, produces a higher consistent quality, and reduces the operational costs compared to the traditional batch mixing technology. These types of optimizations are important to understand and implement in reaching a business’s key performance indicators, more often including sustainability targets.
Part of making the continuous process continually better is collecting data and optimizing critical process and product parameters. Producing the highest quality and consistency in the electrode slurry provides financial benefits through partner relationships and optimized material use. Moreover, better material utilization reduces the environmental impact of battery production by producing less waste, thereby reducing the burden of raw material extraction and per unit emissions during battery production. There is one more advantage as well, one that will be extremely important to the future of batteries – improved traceability. Continuous quality testing of the slurry enables businesses to identify when a problem occurred, and because the timing is consistent for every process step, the question of where can also be extrapolated.
The battery industry is poised for rapid transformation as countries around the world push for more electrification, especially in the transportation sector. Fortunately, many amazing people are working on how to make that a reality and do so without inflicting further harm on ourselves and the environment to move away from fossil fuels. But because the challenge is so complex, people and businesses like Adrian and Bühler are using digitalization to their advantage. By bringing innovative production processes to market faster and optimizing supply chains into and out of a production environment, we are accelerating the transition toward a more sustainable world.
To learn more about the battery industry, be sure to check out our other episodes of The Battery Podcast. If you are all caught up, make sure to subscribe to the podcast on your favorite platform. And if you can’t wait to learn more about the world of batteries, our siemens.com/battery is a great place to continue your transformation journey.
Siemens Digital Industries (DI) is a leading innovator in automation and digitalization. In close cooperation with its partners and customers, DI is the driving force for the digital transformation in the process and manufacturing industries. With its Digital Enterprise portfolio, Siemens provides companies of all sizes with all the necessary products, along with consistent solutions and services for the integration and digitalization of the entire value chain. Optimized for the specific requirements of individual industries, this unique portfolio enables customers to enhance their productivity and flexibility. DI continuously extends its portfolio to include innovations and the integration of future-oriented technologies. Siemens Digital Industries, with its headquarters in Nuremberg, has a workforce of around 72,000 people worldwide.
For more information on Siemens Digital Industries products and services, follow us on LinkedIn, Facebook, Twitter, and YouTube.