How batteries are taking off in aerospace
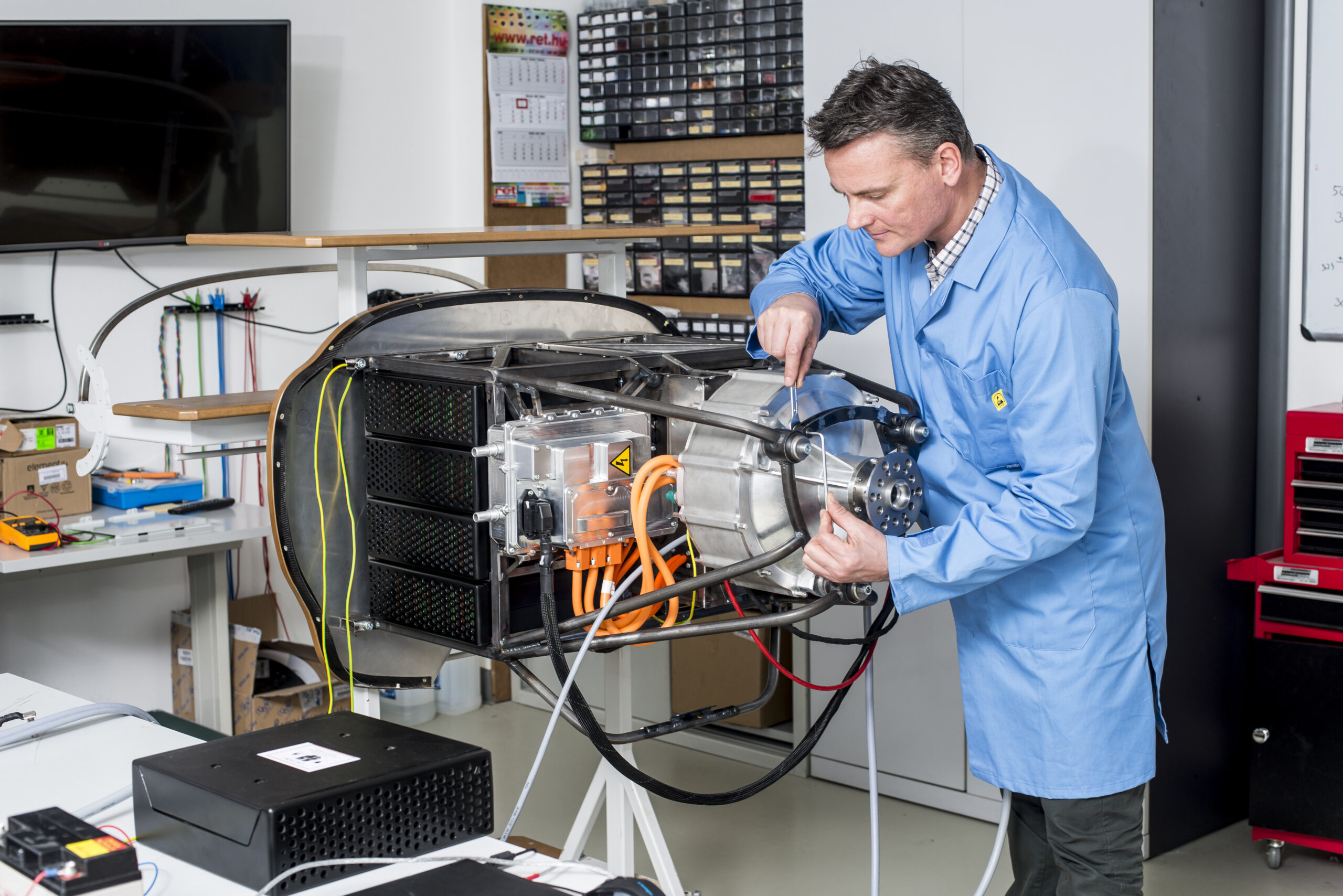
The battery industry does not have a rigid description as others might. It connects to disparate businesses such as personal electronics, transportation, and grid storage while also covering the breadth of the manufacturing process from raw material to finished product. This amorphousness necessitates talking about the industry through specific lenses, whether it is the application in a vehicle or the manufacture of cells. But in past episodes of The Battery Podcast, one application has gone undiscussed – the aerospace industry.
To rectify the hole in the wide battery market, resident host Puneet Sinha and moderator Nick Finberg brought in Todd Tuthill, the VP of Aerospace, Defense, and Marine Industries at Siemens Digital Industries Software, to help more people understand what is happening with battery electrification in aerospace. You can listen to the first half of this great discussion below. Or, to get a few of the important points keep scrolling to get a summary of the discussion.
Electric aircraft are not innovative on their own, electrification has taken off in many small applications most notably in drones, the change and why we wanted to talk with Todd is the rapid innovation happening to bring electrification to more flight applications. Electric vertical take-off and landing (EVTOL) craft are the next major step after companies like Zipline Aero brough commercial viability to the space with point-to-point delivery. More electrification in the space not only increases the logged flight time of these systems and the associated reliability, it is also helping to reduce the cost of implementation as in-roads are built between battery and aerospace companies.
Unfortunately, technical expertise and access to the base technologies are not enough to bring a successful EVTOL to market or any other passenger aircraft to market with reasonable range. Making a viable product requires constant coordination between the aircraft design and the battery technologies. Some challenges stem from the innate differences in energy storage, others from current limitations of battery storage density. The weight of the batteries is a constant load during flight whereas fuel is burned, making the craft lighter for landings and progressively more efficient over the route. But the biggest facet of this challenge is during landing, requiring a large share of the total battery capacity to bring these aircraft to a safe stop, with enough buffer to do so should anything unexpected happen in the flight. Understanding these dynamic situations requires rigorous simulation and testing to ensure these craft are ready for passengered flights.
There are other challenges to battery powered aircraft beyond the in-flight operations. Making these products profitable requires near constant use to get a return in a reasonable period. The problem many aerospace companies are uncovering is that the landing procedure has an additional impact on the EVTOL systems. The high power draw of landing heats up the batteries. That is not a problem on it’s own and it is often understood going into the initial designs, but it also has a negative impact on charging and getting aircraft back in the air. Charging a hot battery greatly reduces the lifetime of the cells, by breaking down the anode and cathode interface materials. This challenge is why so many aerospace companies are moving to designing battery infrastructure internally so that they can better integrate solutions to the problem. Some are making swappable battery packs as seen in some automotive and mobility applications. Others are making the battery packs easily replaceable and designing shorter battery lifetimes into the product.
The paths aerospace companies are taking to profitable electric aircraft may be incredibly diverse, but the solutions to their challenges are often very similar. Digitalization is a major driver for these businesses. It helps create an early plan of what a product should be able to achieve. It guides development teams through the highly integrated systems by linking the requirements in a digital environment. And it helps test ideas before ever committing resources to a physical prototype. These benefits are all extremely critical for a burgeoning aerospace sector where CEOs and managers often have to provide projections of not only capability, but pricing, timelines, and component sourcing.
The first half of our discussion with Todd Tuthill on The Battery Podcast is great for understanding the trajectory of electrified aircraft. And there is much more not covered here in this brief summary. But we hope that you decide to listen in if you have the time or come back for part two where we get into the specific design challenges of electric aircraft and the possible future of the space.
Siemens Digital Industries (DI) is a leading innovator in automation and digitalization. In close cooperation with its partners and customers, DI is the driving force for the digital transformation in the process and manufacturing industries. With its Digital Enterprise portfolio, Siemens provides companies of all sizes with all the necessary products, along with consistent solutions and services for the integration and digitalization of the entire value chain. Optimized for the specific requirements of individual industries, this unique portfolio enables customers to enhance their productivity and flexibility. DI continuously extends its portfolio to include innovations and the integration of future-oriented technologies. Siemens Digital Industries, with its headquarters in Nuremberg, has a workforce of around 72,000 people worldwide.
For more information on Siemens Digital Industries products and services, follow us on LinkedIn, Facebook, Twitter, and YouTube.