CAD software: your comprehensive guide
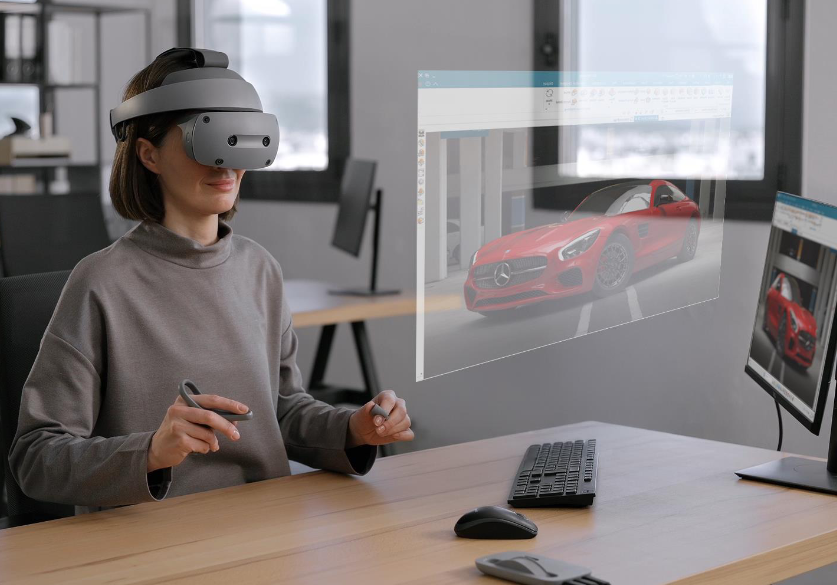
Introduction to CAD software
Computer-Aided Design (CAD) software has significantly transformed the world of engineering, architecture and product design over the past several decades. These powerful digital tools have reshaped the way professionals visualize, create and bring their ideas to life. From the initial concept to the final product, CAD software has become an indispensable part of the design and engineering workflow.
At its core, CAD software provides designers and engineers with a digital canvas to create 2D drawings, 3D models and complex simulations. By leveraging advanced computer graphics and computational algorithms, these applications enable users to design with unparalleled precision, efficiency and creativity. Whether you’re an architect designing a skyscraper, a mechanical engineer developing a new automotive component or a product designer crafting the next consumer electronics masterpiece, CAD software is an essential part of the modern design process.
Key features and capabilities of CAD software
CAD software offers a wide range of features and capabilities that empower designers and engineers to easily tackle complex projects. Here are some of the key functionalities that make these tools so powerful:
2D and 3D modeling: CAD software allows users to create detailed 2D drawings and 3D models of their designs. This includes generating precise technical drawings, schematic diagrams and photorealistic 3D renderings.
Parametric modeling, direct modeling and synchronous modeling: Many CAD applications incorporate parametric modeling, which enables users to define relationships between different design elements. Parametric modeling defines relationships in the model, allowing for easy modifications and updates to the design, as changing one parameter can automatically update the entire model. Direct modeling allows model geography to be modified independently, allowing for quick and intuitive adjustments. Synchronous modeling combines the speed and simplicity of direct modeling with the flexibility and control of parametric design. Additionally, some CAD software – such as Siemens NX and Solid Edge, part of the Designcenter suite, offer parametric, direct and synchronous modeling capabilities, allowing users to seamlessly move between the three approaches and leverage the strengths of each for optimal design flexibility.
Part and assembly modeling: CAD software supports the creation of complex assemblies, where individual components are combined to form a complete product or system. This feature is particularly useful for mechanical and electrical engineering projects, where the interaction between various parts is crucial.
Simulation and analysis: Advanced CAD tools work with Computer Aided Engineering (CAE) tools, which often include simulation and analysis capabilities, allowing users to test their designs virtually before physical prototyping. This includes structural analysis, fluid dynamics, thermal simulations and more, which help to identify and address potential issues early in the design process.
Collaboration and data management: CAD software empowers design teams to work together in real-time, allowing multiple users to contribute to the same project simultaneously. Additionally, these tools often include comprehensive data management systems that ensure seamless collaboration by tracking design revisions and maintaining version control.
Automation and customization: CAD software frequently provides opportunities for users to streamline repetitive tasks, improve workflow efficiency and tailor the software to their specific needs using automation and customization, such as the ability to create custom macros, scripts and plugins.
Interoperability: Modern CAD applications are designed to work seamlessly with a wide range of other engineering and manufacturing tools, facilitating a truly integrated design-to-production workflow. This includes the ability to import and export various file formats, ensuring smooth data exchange across different software platforms.
Surface modeling: CAD software often includes advanced surface modeling capabilities, allowing users to create complex, freeform shapes and surfaces. This is particularly useful for industrial design, automotive and aerospace applications.
Visualization: CAD tools provide advanced visualization capabilities, enabling users to create highly realistic and photorealistic renderings of their 3D models. This includes the ability to simulate lighting, materials and textures, as well as generate animations and virtual walkthroughs. Furthermore, many CAD platforms now integrate with virtual reality (VR) and augmented reality (AR) technologies, allowing designers and engineers to experience their designs in an immersive, three-dimensional environment.
CAD software advantages
The adoption of CAD software has brought numerous advantages for designers, engineers and organizations across various industries. Some of the key benefits of using CAD tools include:
Improved efficiency and productivity: CAD software enables users to create designs and models faster, with greater accuracy and attention to detail. Automated features, such as parametric modeling and simulation capabilities, help streamline the design process and reduce the time required to bring a product to market.
Enhanced visualization and communication: CAD tools provide powerful visualization capabilities, allowing users to create photorealistic renderings, animations and virtual walkthroughs of their designs. This improved visual representation facilitates better communication with clients, stakeholders and cross-functional teams, leading to a shared understanding of the project.
Reduced errors and rework: By leveraging CAD software’s precision and computational power, designers and engineers can minimize the risk of design flaws and errors. Simulating and analyzing designs virtually helps identify and address potential issues before physical prototyping, reducing costly rework and delays.
Increased collaboration and data sharing: Many CAD platforms offer robust collaboration features, allowing multiple users to work on the same project simultaneously, share files and track design revisions. This enhanced collaboration improves productivity and ensures that all stakeholders – from designers and engineers to suppliers and partners – have access to the most up-to-date information, regardless of their location. By facilitating seamless data exchange and synchronization across the entire organization and extended supply chain, these collaborative CAD solutions empower companies to make faster, more informed decisions, accelerate product development and maintain a competitive edge in the global marketplace.
Streamlined manufacturing and production: CAD models can be directly integrated with Computer-Aided Manufacturing (CAM) and Computer Numerical Control (CNC) systems, enabling a seamless transition from digital design to physical production. This integration helps to reduce lead times, improve manufacturing accuracy and minimize waste.
Competitive advantage: The use of advanced CAD software can provide organizations with a competitive edge, as it allows them to design and develop products more efficiently, effectively and with greater innovation. This can lead to faster time-to-market, improved product quality and the ability to stay ahead of the competition.
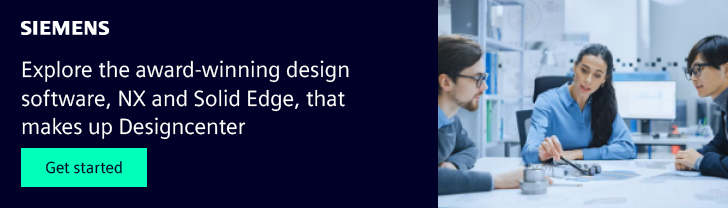
Advancements in CAD technology
The field of CAD software has witnessed remarkable advancements in recent years, driven by the rapid progress in computer hardware, software algorithms and emerging technologies. These advancements have significantly enhanced the capabilities and user experience of CAD tools, empowering designers and engineers to tackle increasingly complex projects with greater efficiency and precision.
Artificial intelligence and machine learning: One of the most notable advancements in CAD technology is the integration of Artificial Intelligence (AI) and Machine Learning (ML) algorithms. These technologies are being leveraged to automate various design tasks, such as generative design, shape optimization and predictive maintenance. AI-powered CAD tools can analyze design data, identify patterns and suggest optimized solutions, helping to streamline the design process and unlock new levels of innovation.
CAD in the cloud platforms: Another significant development in the CAD landscape is the rise of cloud-based and hybrid cloud solutions. CAD in the cloud platforms, including those within the Siemens Designcenter suite, offer users the flexibility to access their designs, collaborate with team members and leverage powerful computational resources from anywhere, at any time. This shift towards cloud-based and hybrid cloud CAD has enabled remote work, improved data security, reduced IT costs and facilitated seamless cross-device collaboration.
CAM and CAD integration: The convergence of CAD and Computer-Aided Manufacturing (CAM) technologies has considerably impacted the design and manufacturing landscape. As CAD software has evolved, it has become increasingly integrated with advanced CAM tools, enabling a seamless transition from digital design to physical production. This integration allows designers and engineers to optimize their products for manufacturability, reduce lead times and ensure the highest quality standards throughout the entire product lifecycle.
Immersive technologies: The integration of Virtual Reality (VR) and Augmented Reality (AR) technologies has also transformed the way designers and engineers interact with their CAD models. These immersive technologies allow users to visualize and manipulate 3D designs in a lifelike, three-dimensional environment, enhancing the design review process and enabling more intuitive design exploration.
Additive manufacturing: The increasing adoption of additive manufacturing (3D printing) has driven advancements in CAD software, as designers now have the ability to create complex, customized parts and products that were previously impossible or impractical to manufacture using traditional methods. CAD tools have evolved to support the unique requirements of additive manufacturing, including the creation of optimized lattice structures, support generation and file preparation for 3D printing.
Software as a Service: The rise of Software as a Service (SaaS) in the CAD industry has enabled more accessible and scalable solutions. Cloud-based CAD platforms delivered through a SaaS model offer users the flexibility to access the latest software features and updates without the need for on-premise infrastructure, simplifying deployment and reducing the burden of IT management.
Sustainability: Siemens Designcenter is at the forefront of sustainability, providing users with the tools and capabilities to design and engineer products that are not only technologically advanced, but also environmentally responsible and sustainable. One such tool, the NX CAD Sustainability Impact Analysis module, enables users to calculate, view and evaluate the impact of their design decisions based on a diverse and comprehensive set of 30+ environmental impacts. By leveraging the power of Designcenter’s comprehensive suite of solutions, designers and engineers can optimize their workflows, reduce material waste and incorporate sustainable design principles to create a more eco-friendly future.
As technological innovation continues to accelerate, the future of CAD software promises even more exciting developments. Advancements in real-time rendering, generative design and the integration of Internet of Things (IoT) data are poised to further alter the design and engineering landscape, empowering professionals to create more innovative, efficient and sustainable products.
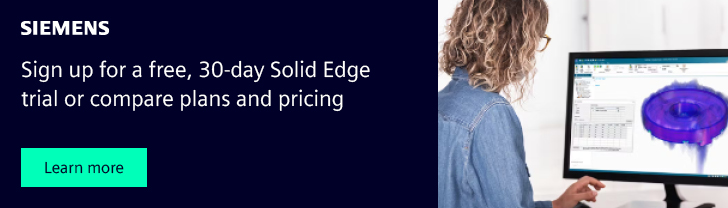
Siemens CAD software: Designcenter suite
Siemens, a global leader in industrial technology, has long been at the forefront of the CAD software landscape, offering two premier solutions: NX and Solid Edge.
Now Siemens is introducing Designcenter. A complete software suite for product design and engineering, Desgincenter is uniquely scalable, as it can seamlessly move data with 100% fidelity from browser to desktop – a capability that competitors’ solutions cannot match. As the most comprehensive design and engineering software suite, Designcenter, which includes NX and Solid Edge, provides unrivaled capabilities in cutting-edge technologies like AI, immersive experiences and cloud computing. This unmatched flexibility enables users to mix, match and customize Designcenter’s solutions to best fit their specific design and engineering processes, accelerating product development by combining the physical world with an AI-enhanced digital twin.
NX, Siemens’ flagship CAD/CAM software, is a core component of this integrated platform. NX empowers designers, engineers and manufacturers to tackle the most complex design challenges with its powerful 3D modeling capabilities, advanced simulation tools and seamless integration with other Siemens DISW solutions. NX has become a go-to choice for organizations across a wide range of industries, including aerospace, automotive, machinery and consumer products, thanks to the comprehensive capabilities of the Siemens Designcenter suite.
One of the key strengths of NX is its ability to support the entire product development lifecycle, from concept design to final production. The software’s parametric modeling capabilities, coupled with its robust assembly management and simulation tools, enable users to create, validate and optimize their designs with unparalleled efficiency. Additionally, NX’s advanced automation and customization features allow designers and engineers to streamline their workflows and tailor the software to their specific needs.
Solid Edge is a versatile and user-friendly solution that caters to a wide range of design and engineering professionals, from small businesses to large enterprises. Solid Edge combines powerful 3D modeling, 2D drafting and comprehensive simulation capabilities, making it an attractive choice for organizations seeking a cost-effective yet feature-rich CAD platform.
One of the standout features of Solid Edge is its intuitive, easy-to-use interface, which helps to reduce the learning curve for new users. The software’s integrated design, simulation and manufacturing tools enable seamless collaboration and data exchange, allowing teams to work together more effectively. Solid Edge also offers a range of industry-specific capabilities, such as sheet metal design, electrical routing and generative design, making it a versatile solution for diverse design challenges.
Both NX and Solid Edge are supported by Siemens’ extensive ecosystem of complementary software and services, including PLM (Product Lifecycle Management) solutions, manufacturing tools and cloud-based collaboration platforms. This integration ensures that Siemens CAD users can leverage a comprehensive, end-to-end solution for their design and engineering needs. Additionally, Siemens offers NX X and Solid Edge X, SaaS-enabled versions of their flagship CAD software, allowing users to access fully featured CAD capabilities in a secure, cloud-based environment.
As the design and engineering landscape continues to evolve, Siemens remains committed to driving innovation in the CAD software space. Through ongoing advancements in areas such as artificial intelligence, generative design and cloud-based collaboration, Siemens is poised to help its customers stay ahead of the curve, delivering more innovative, efficient, and sustainable products. Both NX and Solid Edge are available as student editions, which are free for any student to download. See more software available for free to students on our academic software page.
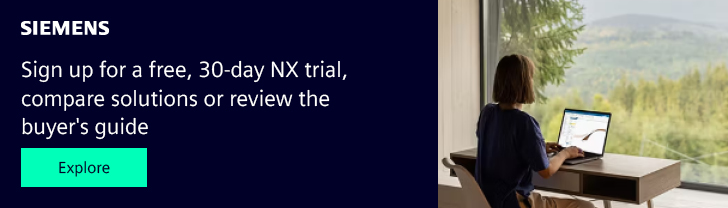
Integrating CAD with other engineering software
The true power of CAD software lies in its ability to seamlessly integrate with a wide range of other engineering tools and software platforms. This integration enables a holistic and streamlined design-to-production workflow, where data and information flow effortlessly between different applications, optimizing efficiency and collaboration.
One of the key integrations is the connection between CAD software and CAE tools. CAE applications, such as finite element analysis (FEA) and computational fluid dynamics (CFD) software, allow designers and engineers to virtually simulate and analyze the performance of their designs. By integrating CAD and CAE, users can easily transfer 3D models between the two platforms, conduct comprehensive simulations and make informed design decisions based on the results of the analysis.
Another important integration is the connection between CAD and Computer-Aided Manufacturing (CAM) software. CAM tools generate the necessary instructions and toolpaths for CNC machines, enabling the translation of digital designs into physical products. By seamlessly integrating CAD and CAM, manufacturers can streamline the production process, reduce errors and ensure a smooth transition from digital design to physical manufacturing.
Many organizations also need to integrate CAD with PLM systems. PLM platforms provide a centralized hub for managing the entire product development lifecycle, from initial concept to end-of-life. By integrating CAD with PLM, designers and engineers can maintain version control, track design changes and ensure that all stakeholders can access the most up-to-date information, fostering collaboration and efficient decision-making.
Furthermore, integrating CAD with Enterprise Resource Planning (ERP) systems enables the alignment of design, production and business operations. This integration helps organizations optimize their supply chain, inventory management and overall business processes, ensuring that product design and manufacturing align with the broader organizational goals and strategies.
As the design and engineering landscape continues to evolve, integrating CAD software with other tools and platforms will become increasingly important. By leveraging these interconnected systems, organizations can achieve greater efficiency, improved collaboration and enhanced decision-making capabilities, ultimately leading to the development of more innovative and competitive products.
CAD in the cloud is the future of design
The rise of CAD in the cloud software has ushered in a new era of design and engineering, transforming how professionals access, collaborate and innovate. CAD in the cloud platforms offer a range of benefits that are reshaping the future of the design industry.
One of the key advantages of CAD in the cloud is the increased accessibility and flexibility it provides. By hosting the software and design data on remote servers, users can access their projects from any device, anywhere in the world, as long as they have an internet connection. This enables designers and engineers to work collaboratively, share files and make real-time updates, regardless of physical location.
CAD in the cloud also offers enhanced scalability and computational power. Instead of relying on the hardware limitations of local machines, cloud-based platforms can leverage the vast computing resources of remote servers to handle complex simulations, rendering and data processing tasks. This allows users to tackle more ambitious projects without needing powerful local workstations, democratizing access to advanced design capabilities.
Another significant benefit of CAD in the cloud is improved data management and security. By storing design files and project data on secure cloud servers, such as AWS or Microsoft Azure, organizations can ensure that their intellectual property is protected and backed up, reducing the risk of data loss or unauthorized access. Additionally, cloud-based platforms often provide robust version control and collaboration features, making it easier to track design changes, manage revisions and maintain a single source of truth.
CAD industry applications and case studies
CAD software has become an indispensable tool across various industries, enabling professionals to design, simulate and bring their ideas to life. From architecture and engineering to manufacturing and product design, CAD has transformed how these industries approach their respective challenges.
Architecture and construction: In the architecture and construction industry, CAD software plays a crucial role in designing and planning buildings, infrastructure and urban environments. Architects and engineers use CAD tools to create detailed 2D drawings, 3D models and Building Information Modeling (BIM) data, which help to visualize the project, identify potential issues and coordinate the work of various stakeholders. CAD software also enables the integration of design data with construction management systems, streamlining the entire construction process.
Automotive and aerospace: The automotive and aerospace industries were early adopters of CAD technology, leveraging its capabilities to design, engineer and simulate complex products. CAD software allows engineers to create detailed 3D models of vehicles, aircraft and their components, enabling them to analyze performance, optimize designs and ensure compliance with safety and regulatory standards. Integrating CAD with CAE tools, such as finite element analysis and computational fluid dynamics, has been particularly transformative in these industries.
Mechanical and industrial engineering: In mechanical and industrial engineering, CAD software has become an indispensable tool for designing and developing a wide range of products, from consumer goods to industrial machinery. Engineers use CAD to create precise 2D and 3D models, simulate the performance of their designs and generate manufacturing instructions for CNC machines and other production equipment. The ability to quickly iterate on designs and optimize for cost, efficiency and sustainability has been a significant advantage for engineering professionals.
Industrial and agricultural machinery: CAD software has become an indispensable tool for industrial and agricultural equipment manufacturers. From mass-produced modular designs to highly specialized, engineered-to-order products, CAD enables designers and engineers to create detailed 3D models that optimize manufacturability, performance and customization. The seamless integration of CAD and CAM workflows allows a streamlined transition from digital design to physical production, reducing lead times and ensuring the highest quality standards. Whether it’s designing the next generation of tractors, construction equipment or processing machinery, CAD empowers manufacturers to innovate, improve efficiency and deliver specialized products that meet the evolving needs of their customers across the industrial and agricultural sectors.
Consumer electronics and household goods: The consumer electronics and household goods industries have embraced CAD software to design and develop a wide range of products, from smartphones and laptops to kitchen appliances and home furnishings. CAD tools enable designers to explore innovative product concepts, create detailed 3D models and simulate the user experience, all while ensuring compliance with industry standards and regulatory requirements.
These are just a few examples of the diverse applications of CAD software across various industries. As technology continues to evolve, the role of CAD in driving innovation, efficiency and sustainability will only become more pronounced, transforming the way professionals approach design and engineering challenges.
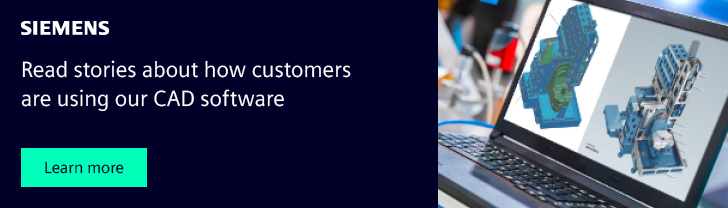
CAD software FAQs
Q: What is the difference between 2D and 3D CAD software?
A: 2D CAD software is primarily used for creating technical drawings, such as floor plans, schematics and engineering diagrams. These tools focus on creating precise 2D representations
Q: What are the key benefits of using CAD software?
A: The key benefits of using CAD software include:
- Improved efficiency and productivity in the design process
- Enhanced visualization and communication of design concepts
- Reduced errors and rework through virtual testing and simulation
- Increased collaboration and data management capabilities
- Streamlined integration with manufacturing and production systems
- Competitive advantage through innovative design and faster time-to-market
Q: How do CAD software and CAE tools work together?
A: CAD software and CAE tools are often integrated to create a seamless design-to-analysis workflow. CAD models can be easily transferred to CAE applications, such as finite element analysis (FEA) and computational fluid dynamics (CFD) software. This integration allows designers and engineers to virtually test and simulate the performance of their designs, identify potential issues and optimize the product before physical prototyping and manufacturing.
Q: What are the key considerations when choosing a CAD software solution?
A: When selecting a CAD software solution, some of the key considerations include:
- Features and capabilities (2D/3D modeling, simulation, collaboration, etc.)
- Industry-specific tools and workflows
- Ease of use and learning curve
- Integration with other engineering and manufacturing tools
- Scalability and computational power
- Data management and security
- Cost and licensing options
- Vendor support and ecosystem
Q: What’s the best way to learn CAD software?
A: Siemens Xcelerator Academy offers live and on-demand trainings for the Siemens software portfolio. students can gain free access to software training on Siemens Xcelerator Academy by following these steps.