The digital transformation of battery manufacturing – The Battery Podcast S01E05 – Transcript
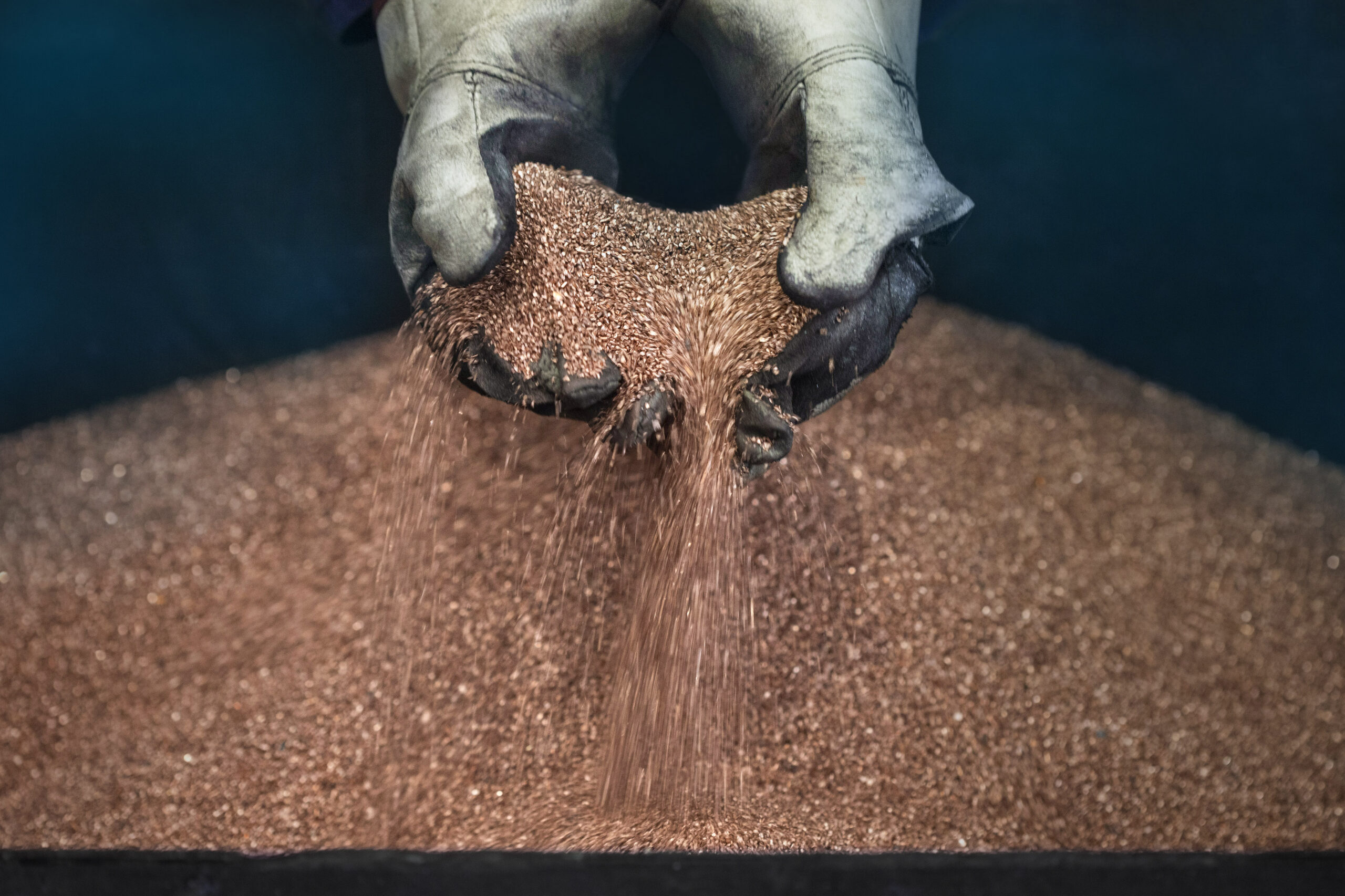
If you missed episode five of The Battery Podcast the first time, here is the complete transcript from Puneet Sinha’s conversation with Magnus Edholm on bringing digitalization to the realm of battery manufacturing. Read along at your own pace or hit play and absorb this electrifying conversation.
Nick Finberg:
Welcome to the Battery Podcast from Siemens Digital Industries. In this episode Puneet and I are finishing our conversation with Magnus Edholm, who drives digital enterprise for Siemens Digital Industries. We last left off talking about the value of the IT-OT convergence and the battery industry and how it drives more in-depth understanding and decisions with data, which is important for sustainability as well.
The high-level goal of batteries and electrification is about decarbonizing. A crucial part of achieving that goal is continuing to improve the battery performance in several areas, whether it’s energy density, longevity, reliability or cost really all of them at once if you can. How can companies pursue these improvements and do so quickly enough to meet the demand?
Puneet Sinha:
A great question, Nick. Let me take this. As you said, batteries are definitely a great enabler for world’s goal of decarbonization. However, battery production is very energy intensive. There are analysis that it takes today approximately 30 to 40 units of energy consumption to produce one unit of battery energy. Again, today, 30 to 40 units of battery energy consumption to create one unit of battery energy. You can think depending on the energy mix that is used in a giga factory, battery production can have a significant carbon emission. And because of these reasons, there are many reports where analysts talk about that although use of batteries in a vehicle significantly reduces tailpipe emission, production of those batteries can increase carbon footprint. That’s why it is critical when we talk about sustainability, we look at the carbon footprint of gigafactories. And what are the steps that can be taken to reduce the overall energy consumption in the manufacturing.
There are many smaller steps that can be taken that can have a far-reaching impact. One example is what Magnus already mentioned, such as in a battery pack assembly companies use a robot. Those robot gripper heads can be really heavy. We have seen that by leveraging additive manufacturing and light-weighting designs of those gripper heads, companies have achieved almost five to 10kgs weight reduction of each robot. If you start adding the number of robot arms in a factory, these small reductions add up in making the overall battery production less energy intensive, more sustainable. In the same way, sustainability is not something that should be thought of as a standalone topic bolted on at the end. At Siemens, we think that sustainability is an inherent process that needs to be accounted for in the whole lifecycle of a battery. From the development to how this manufacture to how battery is used in a field application. How optimal design is for a cell, for a pack, has an impact on overall weight of the battery.
How companies can optimize the chemistry and the various materials that are in there has an impact on the overall carbon footprint and for a battery lifecycle. Similarly, how companies can maximize the energy they can extract from battery to wheels in case of electric vehicle is very critical and has an, again, impact on overall energy efficiency and sustainability in the same way the overall energy management of a giga factory is very, very critical. All of these aspects add to lowering carbon emissions. In addition to that, there are things like worker efficiency, energy management, as I said, at a factory level that come into play. Magnus, I wonder if you want to add something on that.
Magnus Edholm:
Absolutely, I think you covered a lot of things and I think what you said there that sustainability should be something more than just a bolt on. It’s something that you need to, how can I say commit to, you need to drive it. I guess it’s important that you do something instead of doing nothing. I probably can’t do everything at one go.
Starting and building the sustainability thinking through the processes and in the company, and I’m fairly sure that by doing that can drive what we could call a profitable sustainability because it’s got to be up there as a business target, not just something you do because we have to. We do have to do something about it, I’m sure there’s business also in all of this.
Also looking at the CO2 footprint with inside your company, that’s one thing, but very often companies be it in the battery manufacturing industry, be it in car industry, computers, food and beverage, what have you are dependent on those essential ecosystems which are built up by suppliers, customers, et cetera.
It’s also important to measure the CO2 footprint in the supply chains because they also add to the whole of your product. For that, we have something called SiGREEN, which is available as a software as a service. It is built on a platform called Estainium on which companies can register their materials being used in the development of products.
The transportation methods, the manufacturing methods, and that that’s a very quick and dirty explanation, but that enables you as the manufacturer to step in and say this is what I’ve been producing now I’m going to use those suppliers, can you give me a feeling for where my CO2 footprint going to land?
You might have set the requirement when you did your product and the SiGREEN will enable you to get that type of information. I mean, to take this one step further sustainability, the first thing that you may think of is that recycling and reuse of batteries. Today, Nick and Puneet, I am told that only 5% and I say 5%, 5% of all batteries are being recycled, that is to me catastrophic.
We are throwing away so much value, so many valuable minerals, so much material that we could perhaps reuse. Now, it’s clear that recycling batteries is potentially harmful. You’re working with rest voltage, you’re working with chemistry and we need to get smarter in all of this perhaps. I mean, if we look at a product and the products environmental impact to 80% is based on decisions made in the design process.
Perhaps we already in the design process need to think about the recycling of batteries for example, enabling us to take advantage and reuse those minerals, those metals that are being put in a battery. Also, this to come back to the gripper that both Puneet and I spoke previously.
Perhaps robots can be used in this, perhaps artificial intelligence can be used to scan a battery and then figure out a way to actually disassemble this battery in an automated type of way. We need to remember that the car battery today, it is glued, it has bolts, it’s got foam.
Those things are compact because the need to endure pretty tough treatment when positioned in the car, but it’s got to be a way around this. We are actually working with a technical institute here in Germany in Karlsruhe and they are utilizing cameras and artificial intelligence to analyze the batteries. What material do we have in this particular battery.
Today, there’s a huge vari of batteries, different types, different sizes. This is something we are definitely attacking. Another thing, and I’m sure Puneet going to step in here soon, if we look at the battery passport that some of you may have heard of, a battery passport is essentially the same thing as the passport that you and I have when we’re traveling.
It tells you where you’re from, birthdate and so on and so forth. That information will be, and correct me if I’m wrong here, Puneet I think 2026, it’ll be included on all batteries bigger than I think two kilowatt hours. Two kilowatt hours batteries is basically the size of the battery that you have in those e-scooters, the two wheelers that are more or less all over the place.
From that size and upwards, every battery will have a battery passport and that I believe will make it easier to recycle. You would immediately know what do we have in this battery perhaps just some information we can use when we are disassembling this, which I hope will happen. I say again, only 5% are being recycled. Puneet support on this one.
Puneet Sinha:
100%, Magnus. You’re absolutely right. When we look at the batteries, very little percentage, as you said, 5% of the batteries are recycled today. And that’s a big problem and it’s a big problem right now because if you think of it, the first wave of EVs with lithium-ion batteries came around 2010 timeframe. And the cars that went on the road in 2010, 2011 timeframe, those cars are about to come to their end of life now after 12 to 13 years. And all of a sudden, we are about to get a huge number of batteries coming out from the field application. And now companies have to deal with, and when I say companies, automakers as well as battery suppliers, they have to deal with how they’re going to recycle.
Actually the question is should they recycle or should they look to find a second use of those batteries? Especially for the batteries that were in electric vehicles, when they come to end of life, there still is a lot of energy left in them. Companies have to decide how they’re going to work to disassemble and recycle those material and put those material back in the manufacturing of new batteries or retarget, repurpose those batteries for second usage. As you said, Magnus, around 2026 timeframe, it’ll be mandated in EU that every battery more than two kilowatt-hour is adhering to battery passport regulation. And there are other growing regulations and legislations around this topic in other countries as well. All of this comes down to having a traceability of what materials went into a battery, who produced that material, how it has gone through its development lifecycle, its usage lifecycle before it comes out for recycling or repurposing.
Having that traceability is extremely critical for companies as they’re looking to improve recycling process or repurposing those batteries for some other usage. And again, data is key part of it. Right now what we’re talking about is data that cuts across a number of companies who are playing very different roles in the whole supply chain. Battery passport is very critical and expected to play a very big role in ensuring that battery recycling can improve, that repurposing can be sharpened, as well as allowing companies to have better ideas on how they’re going to improve their overall carbon footprint.
Nick Finberg:
What should a technology partner bring to the table for a battery manufacturer? What expertise and technologies are required to help them get going?
Puneet Sinha:
This is a question that I spend a lot of my time thinking about as part of my job. I’m going to take this question, break it in couple of parts. First of all, why do companies even need technology partner and then the second part being what are they looking from the technology partners? As I mentioned earlier, battery development, engineering and manufacturing is fundamentally different from the kind of engineering and manufacturing practices companies have been leveraging in the past. The biggest reason for that is the fundamental difference in what we’re dealing with here in batteries. There is a very strong interaction among chemistry, electrical, electronics, mechanical systems and manufacturing domains. What that means is if you make a small change in a material, it has significant implications not only on battery performance, but potentially on safety, its usage, as well as recycling and that makes battery engineering and manufacturing really challenging.
On top of it, if you look at the market dynamics as we talked multiple times today that the demand for batteries exploding because of the pull from electric vehicles and energy storage applications. In this scenario, companies need to deal with the new ways of engineering and manufacturing batteries while they don’t have much time to perfect these processes. They need to do so in a short time and also do it in a large scale and in cost-effective way. For all of these reasons, they’re looking for technology partners who can help them in their pursuit of meeting their scale up ambitions, and this is an area where Siemens comes into play. From Siemens perspective, our aim is to become the preferred technology partner for the whole battery ecosystem. And by battery ecosystem, I mean companies who are developing materials that goes in a battery, companies who are building self-impacts, also companies who are taking these batteries, integrating them in a system and the system can be a car, a device that goes in our pockets or something that goes in air or water, as well as the companies who are recycling these batteries.
When we go and engage these companies, meet them, many of them are new startups who are coming from a very different perspective, many of them being electronics players, as well as a lot of large incumbent enterprise companies. All of them are telling us that they need an end-to-end solution that can help them address these challenges. They need to bring digital transformation in their processes so that they cannot only innovate faster, but they can also put those innovations in production and in usage in an agile fashion. What that means is connecting the digital worlds where they can explore and optimize product and production process very quickly and then connect them with the physical world where they’re producing those batteries, and where these batteries are going in a real world application.
The number one thing the battery ecosystem is looking for is how a technology partner such as Siemens can help them connect their digital exercise and pursuit with the physical world. These technology partners, therefore, need to offer them digital twin technologies, but also help them connect these digital twins with the automation technologies that these companies are putting in their factories, but also with the IOT and AI technologies they want to leverage for battery engineering and manufacturing and its usage. Doing all of this in a seamless connected fashion is the biggest requirement for a successful technology partner. Siemens has become the preferred technology partner for the battery ecosystem because of these reasons and the fact that we deliver on them. We are not just delivering tools to these companies and leaving the burden of using these tools on these companies, but we are bringing the right knowledge of business process that is very critical for the battery companies to not only have tools but, also understanding of how they can deploy these tools as part of their existing processes. Magnus, anything more to add from your perspective?
Magnus Edholm:
Well not a whole lot, I think you did a great job there, but what I’d like to say, I mean, now we’re talking batteries for sure. I mean this what you said, Puneet applies to all other industries also to find partners to find the network. If you go into Siemens Xcelerator or open digital business platform there we have those partners.
We have those networks of ecosystems available. It would be rather easy to find the correct partner to work with in any type of industry. You’ll also find the software solutions, the hardware solutions with IT/OT capabilities at the Xcelerator.
This powerful digitalization portfolio inside Siemens Xcelerator, it includes software, hardware, and also services that you can use to constantly optimize the work you’re doing. That’s the only thing I’d like to add, Puneet to what you just said.
Nick Finberg:
These sound like awesome solutions for really any company, but where can the industry go with digitalization in the next 5 to 10 years? What do battery companies need to get there today?
Puneet Sinha:
I’ll start and then it’ll be great if you can add your perspective, Magnus. If you look at what’s coming in next five to 10 years, there are a couple of things that jump out to me. Number one, we will see tremendous new innovation at the material level, at the new engineering concepts level to increase energy density of a battery. That means how much energy you can pack in a kg and liter of a cell and how fast you can charge that.
These innovations will be more driven from the new chemistries such as solid state battery or sodium ion batteries. And because of these new material level technologies, I also believe that increasingly next five to 10 years we will see that batteries will start becoming an important part, not only for vehicle electrification but also for electrification of other modes of transport, including but not limited to air transportation like EVtol. Second, as you talked about, Magnus already a couple of times, increasing the recycling rate from today’s 5% to a significantly higher number of what industry needs to reach either to achieve effective recycling or repurposing of those batteries for other usage. And third and perhaps extremely interesting is how companies are going to leverage technologies such as AI and industrial metaverse to bring new innovations and leverage data to find new solutions. I’m going to spend a couple of minutes on the topic of AI.
All of our lives have been changed since ChatGPT has come. I’m sure many of you, like me, are using ChatGPT very frequently when we are looking to plan our vacations or finding some more curiosity questions, answers, but companies are also looking to see how they can leverage AI, ChatGPT, other natural language models for battery engineering and battery production. Some of the work that we in Siemens are doing is also very exciting based on our internal solution development, but also the kind of partnerships we have with Microsoft to connect our PLM framework with ChatGPT, OpenAI system from Microsoft so that operators can register their issues a lot more efficiently. Right now, 70% of the issues in a factories go unreported because of the time and the effort they require for an operator to report them. By bringing these technologies, it’ll make it easy for operator to register their issues and then by connecting those additional twin technologies, the resolution of those issues can come faster. And these are just some examples. There is a lot more in the area of AI and how industrial metaverse can impact or disrupt battery ecosystem we shall see in the next five to 10 years. Magnus, what do you think?
Magnus Edholm:
I can only agree with you. I mean you mentioned the digital twin. We have the digital thread, which describes the user journey to tackle the challenges. I mean, all those things come together. Of course, also combine the real digital world. Those three I think is a prerequisite for enabling the industrial metaverse.
In all of that, we touched upon the connecting top floor to shop floor or IT/OT convergence. You spoke AI, definitely important. In all of this also, cybersecurity is playing an important role building those ecosystem. I mean, there’s so many things going to happen in there are so many new methodologies coming out.
So many new technologies and having AI work in parallel to support us in our decision making I think is definitely something that will keep them evolving over time. I think it is a very cool time to be alive, to experience all those changes, all the new cool things that are coming around. I have a good feeling that the future looks bright.
To tie back to sustainability, I believe technology is what will actually turn this around and make the world a better place. We can do it. We have technology. We just need to be open-minded and we need speed. We need to accelerate the digital transformation according to me.
Nick Finberg:
Well, thank you so much both of you for joining us for this episode. It’s been awesome listening to it.
Magnus Edholm:
Thank you, Nick. It was a pleasure being on board with your talk show. Also, thank you, Puneet. Great seeing you again.
Puneet Sinha:
Thank you, Nick and Magnus. I had fun talking to you guys about these exciting topics.
Nick Finberg:
And thank you to the audience. We hope to have you back again in the future and stay tuned for some more interviews from the show floor with Marc Deyda. Until then, check out our other episodes, reach out on LinkedIn, and continue reading at siemens.com/battery. See you next time!