Sustainable batteries from production to recycling – The Battery Podcast S01E06 – Transcript
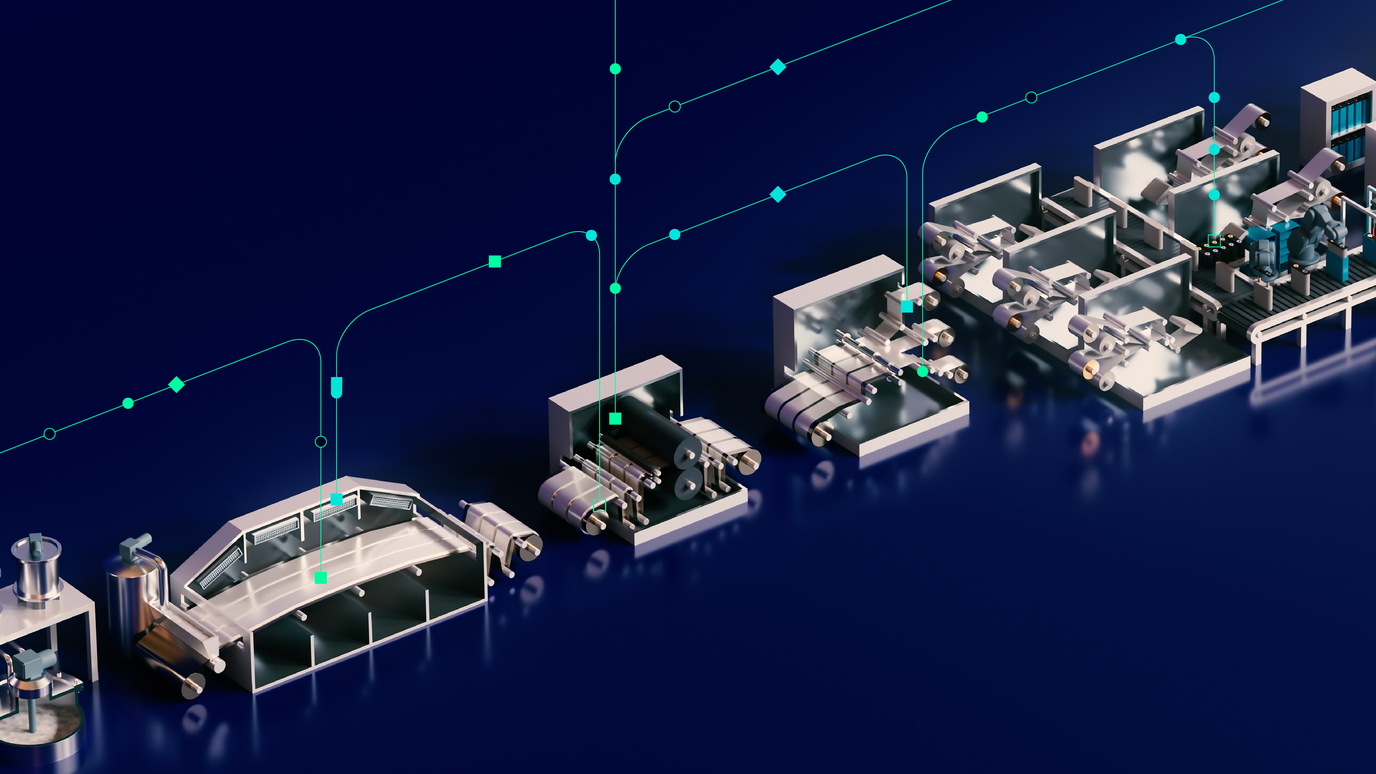
To talk about the sustainability of batteries from raw materials to recycling, Puneet Sinha sat down with Magnus Edholm for episode six of The Battery Podcast. Tune in to the conversation below or read at your own pace:
Nick Finberg:
Welcome back to the Battery Podcast from Siemens Digital Industries where we talk about all things battery with industry leaders, key partners, and Siemens experts. I’m Nick Finberg and I’ll be your moderator for the podcast. Today’s episode we’ll focus on digital transformation of industry, specifically battery as they’re forced to accelerate to keep up the pace of changing demands.
To discuss this, we have a resident host, Puneet Sinha and our guest today, Magnus Edholm, head of marketing for Siemens Digital Enterprise. Welcome to the Battery Podcast, Magnus. Would you please introduce yourself for those that may not recognize you?
Magnus Edholm:
Absolutely, thank you very much. First of all for having me, Nick, it’s a pleasure to talk to you and of course also to Puneet. A few words about me, myself, I’ve been in the field of digitalization for I guess the better part of 25 years. Of those 25 years I’ve probably spent 12 to 15 driving the digital enterprise within Siemens.
I started off as an application engineer. I’ve been working as a consultant on various different companies around the globe, mainly in the field of manufacturing to be honest. Simulation, manufacturing, planning and so on and so forth. Then I’m moving into marketing probably 15 years ago using what I learned over the years.
Nick Finberg:
Awesome. Well, thanks for joining us. And for the audience that may not recognize Puneet, he is our global head of Battery Industry in Siemens Software – with over 15 years in the battery field in research at GM and in business development helping a startup democratize battery development and engineering.
Every year we use a technology or industry to showcase our solutions across design, manufacturing and logistics at our large show events. Magnus this year you presented on battery. Why did you want to talk about batteries this year?
Magnus Edholm:
Exactly, that’s how we do. At our big trade shows and events we always start to focus on things that are interesting for the world. If we look at the sustainability that drives the industry forward, probably the most important part of what we do today to drive sustainability in everything we do.
Obviously, this is reflected also in the field of manufacturing. With sustainability being so important, this also obviously affects, for example, transportation. I mean, you have battery applications for cars, you have it for industry, you’ve got it for storage and even handheld tools.
What we did was we drilled down all the use of batteries in electrical cars this year. I think it’s important to know that from 2018 to 2030, the demand for batteries will increase with a factor of 14, 14, that is a huge increase. This means that we as manufacturing companies out there need to be able to develop batteries quick with high quality and of course also sustainably.
Therefore, I think it’s extremely important and those batteries needs to be developed or produced in machines. Machine building, I mean everything comes together and we’ve found it being extremely important and interesting to dig down in the field of batteries and show how we, as Siemens can support the industry with the software required to design and develop the best batteries, sustainable high-quality batteries.
Also, the machines being able to meet the demand of this factor of 14. It’s huge, just keep that in mind. That’s what we did and we also took the whole scope, took a holistic approach. We’ve gone upstream looking what material we’re using, we’re looking at the sustainability.
I’m sure we’re going to talk about that in the next few minutes, but that was our approach showing how we as Siemens with our software and hardware and services know-how can support the industry delivering this increased amount of batteries.
Nick Finberg:
Given some of the challenges ahead, what do battery manufacturers need to be successful? Is digitalization an important step for these customers?
Magnus Edholm:
I would say it is crucial for the manufacturers. If we look at the traditional way of creating or developing batteries, it’s usually been done on physical batteries if you like, working with the assets and the metals. It’s been a time consuming and resource intense development methodology with the digitalization solutions.
I’m thinking mainly about the software simulation tools that we have. You are actually able to develop the battery, simulate the chemistry, develop the battery in parallel with the battery management system because you need the battery management system in there. Everything you do at digital will save you time.
I believe that digitalization solutions, the software simulation stuff that we have enables you to increase the amount of iterations. You do a test, you simulate it, you see the result, you learn from that. If you didn’t hit the spot then you do it again. I think that it’s extremely important and this is not something new.
I mean, battery is an industry that’s important, but the same approach we can also take be it in the electronics industry, be it in pharmaceutical, be it in aerospace using digitalization solutions are key for this. Perhaps you, Puneet, want to step in here and add some thoughts to it also?
Puneet Sinha:
Absolutely Magnus. First of all, I had a pleasure to be with Magnus at the event he was referring to earlier this year. Everything that Magnus mentioned of the need of battery demand that is growing with various applications, with transport, energy storage is real. When we were at this event together, we saw tremendous demand for digital transformation and digitalization of battery industry. To add to what Magnus said, if you can take a step back and look at battery and the underlying physics, underlying process to engineer or manufacture battery, it’s fundamentally different from the kind of process industry is used to while developing IC engines or IC vehicles.
To put it more specifically for batteries, there is a strong interaction between different domains like chemistry, mechanical, thermal software, electrical and electronics. This cross domain interaction while developing battery or manufacturing a battery was not present or at best, very weak for IC engines or other technologies. When we look at the battery, fundamentally it is very critical that companies change the way they are going about engineering and manufacturing them. Hence, the need for the digital transformation is there so that companies can evaluate different aspects, trade-offs across different domains and how they’re going to develop these batteries more effectively.
If you look at the manufacturing, there are some fundamental aspects and the things that Magnus is highlighting. If I can add a little bit to what he said, if you think of battery manufacturing, actually it is very interesting. The analogy between battery manufacturing and a cake baking, as I said, battery manufacturing and cake baking. The process of how you bake a cake from mixing a goo or ink, spreading it on a flat surface and then going through the process and at the end you’re taking a cake and putting it in an oven to bake. The processes for cell manufacturing are exactly the same.
Interestingly as you can imagine, if you give the same recipe of cake baking to an experienced cake baker, an amateur like me, you can be very sure that the quality of a cake that will come from an experienced baker versus me is going to be significantly different although the recipe is the same. It is the same thing we are seeing in the battery industry too, that although many companies may have the same recipe or manufacturing processes, experience today continues to be a big success factor, ensuring the quality of battery manufacturing and that is something that needs to change for battery industry to grow at a speed it needs to grow to meet this ambition.
This is where data-driven development is critically essential so that battery development does not always remain pivoted on experience so that companies leveraging the data coming out from the machines and factories can improve their manufacturing processes. What we are seeing in the interaction with the battery industry across the world, is that there are a couple of key challenges that are getting highlighted more and more often. One of them is very high scrap rate. We are seeing that a lot of companies, when they’re starting, there is large scale production. Their scrap rate is 40% or a little bit higher, and even then they get to a more stable, running factories. They’re still dealing with scrap rate of around 15%, which is too high to get to a cost-effective large scale manufacturing.
These kinds of challenges need to be addressed in a very fast way, given the rapid demand increase for batteries, for the data-driven process, how digitalization can help in understanding these key limitations is very critical.
Nick Finberg:
You mentioned high scrap rate is one of the challenges, but I’m sure there’s a lot more to really scaling manufacturing capacity the 14 times that you need to the expected demand, what is that going to look like?
Magnus Edholm:
Well, first of all Nick, if I can take this one, if we start looking at those gigafactories, I’m sure you’ve seen them. I mean, those things are huge, really massive. For our European audience, if you take a couple of them Eiffel Towers and just put them on the side, you can probably fit like seven, eight of those Eiffel Towers in a gigafactory for American audience, the Pentagon in Washington D.C.
Also, there you can probably squeeze in some five Pentagons in the gigafactory that gives you feeling. For those into sports, I mean also here you’re going to stop soon, but I mean there’s got to be quite a few football fields in a gigafactory, so it’s big.
If you look at it, how many machines can be in there, what many machines do you need in there that is posing a challenge definitely. One more number by the way, I forgot this one. One giga hour capacity takes about 10,000 square meters. Now Nick, you do that into square feet please, if you can. What do we have?
Nick Finberg:
That’s what? A little over 100,000 square feet?iemens
Magnus Edholm:
In other words it can take years to get those facilities up the line because Puneet talk about data. In a gigafactory, we have machines that are talking to each other, they are exchanging information and we as let’s say leading or driving a gigafactory or those driving a gigafactory, they need to collect that data that’s been generated.
They need to analyze and understand that data and then use that data and feed it back into the system to continuously optimize everything that is being done. It’s a big thing but there are opportunities in here, one being to work with our digitalization solution and perhaps virtually commissioning commission machines and lines.
We are essentially simulating the way the machines are working. When we have the simulation we can use APLC code, the programmable logical controller data that controls the machine. We use a virtual controller and basically well, start that machine off in a digital environment to make sure it works the way we planned it.
That is also a way to test those what if scenarios. Again coming back to the iteration, meaning that when you are about to go live and to ramp up the factory, you can be sure that your machines, your lines and perhaps even your entire factory will work exactly as you have done in your digital environment.
I believe that you can reduce the real commissioning time with up to 95% if you’ve done a proper virtual commissioning of the machines and lines. There you can obviously save a lot of time to get it up there. Another thing coming back to data, I’m sure the convergence of IT and OT is something that you’ve been talking about.
Basically connecting the top floor with the shop floor if you like, making sure our data flows from let’s say the ordering down to the machines. You are on track of what’s happening on your machines. You can follow the batches, you can be sure that you’re producing quality product. Everything comes in to add to the value of a factory, a gigafactory, and get it up and running.
Also here, I believe that automation in combination with simulation tools is also an enabler. I mean, there’s no secret that one of the biggest challenges ahead is the lack of people working. I mean, demographic change at least in Europe is pretty obvious and hands-on. I believe working together with automation and people with the right skillset will be the enabler and perhaps also what drives the success in all of this. I assume this is the same more or less globally.
I think having the convergence of people and automation is also outmost importance to reach the success. Also here, I’m sure Puneet, you being a specialist on the topic, anything you’d like to add on the field of IT and OT?
Puneet Sinha:
Magnus, you have already touched on some very excellent points. When we look at the giga factories, some of the big challenge you talked about, time it takes to scale up factories, factory throughput, costs, scrap rate. And if you look at these challenges, one reason behind these challenges is how the traditional ways of manufacturing work wherein the different tool sets are kept separate. IT system and OT systems don’t necessarily interact with each other, whereas they need to if you’re looking to address the challenges, Magnus, you talked about. And yes IT, OT integration is becoming a big need for companies to address it, be it the new players or existing incumbent players who have been doing manufacturing for many years, they are looking to improve… Again, be it the new players or existing incumbent players who have been doing manufacturing for many years.
They are looking to improve the efficiency of the production. What does it mean to have IT, OT integration? I want to spend perhaps a couple of minutes on this with our audience. IT, OT integration allow companies to connect their shop floor with the rest of enterprise, and one concrete example of that is how companies can leverage the data coming out of a factory. As Magnus mentioned, in a giga factory there are many equipments, a lot of machines, and there’s a lot of data that is generated when these machines are operational. Many of our interactions have shown that perhaps 80% of the data coming from factory is not necessarily utilized. I repeat again, 80% of the data. And if companies are looking to solve the problems we just mentioned, they need to do so. And key enabler for that is IT, OT integration. As Magnus was mentioning, how some of the OT layers such as PLCs, drives and other hardwares in a factory need to connect more effectively with EMEA systems, cloud and apps. If you can connect that, it can enable companies to make smart decisions that can help them scaling up their production and reduce their scrap rate faster. Very importantly, IT, OT integration also allow companies to enforce the best manufacturing practices.
This includes, but not limited to, how operators can do more tasks, how material which is needed at certain machines can be provided to them in a timely manner and how predictive maintenance of various machines can be scheduled in a timely fashion. All of these issues come together in making sure that overall throughput of a production process is maximized. This makes sure that the production cost goes down and margin becomes better. In a sense, IT, OT integration is a big part of what is needed in the industry to scale up manufacturing in giga factories and meet their ambitions.
Nick Finberg:
IT/OT sounds like a very important topic for optimizing not just your shop floor, but your entire enterprise. But for battery manufacturing sounds like a really complex process. How are companies optimizing these processes to improve manufacturing efficiency? How are they dealing with an increased need for flexibility on top of the greater throughput?
Magnus Edholm:
I’m going to go back Nick to what I said before, the use of data, again, all machines are more or less connected with each other and a huge amount of data is being generated. I think it is important that you take this big data and you turn into smart data, you need to know what you’re going to look at.
For here, you have new technologies coming into play, probably artificial intelligence to recognize patterns, et cetera. Essentially, the important part is to, if you want to improve something, you need to measure it first. If you don’t know where you’re at, it’s going to be terribly difficult to improve your performance. Therefore, we need again collect the data.
Understand data and use the data because that will give us the insights we need to improve the throughput. Again, what Puneet spoke about, the IT/OT having this transparency, which is crucial to know that what you’re doing is been done in the absolutely right way. This through the entire life cycle of the battery in this case. It obviously applies also to other products.
In the design phase, the realization, and the optimization phase. What you mentioned at the beginning at a trade show this year Hanover it was, we started off, we basically took a complete holistic approach to the battery production as I said. I also mentioned three different areas and we can start with the mixing process.
Being able to simulate how this slurry comes together without having the physical mixing device or working with the physical chemistry that you put in there, the different materials we’re able to simulate and optimize this mixing device. It’s almost like every morning, Nick, when you do your breakfast you make a smoothie I guess, bananas, some berries and what have you.
Same type of approach, but you measure the outcome, you can simulate exactly how this slurry going to work, when it’s being then put on this film or the foil that’s actually being used to create the batteries. Taking it from the mixing, we go into a slitting machine which essentially takes this foil on which we have the slurry.
We cut the foil in the exact width we need on a very cool machine called the slitting machine. It’s big, it’s heavy, and it’s exactly very, very exact in the way it cuts it. Then, we take that information and perhaps move it on to let’s say the assembly of the batteries. Also here, I mean, there’s a huge put optimization potential in all of this.
The mixing can be optimized, the splitting can be optimized and also the assembly. A great example is that we had this robot assembling the battery packs. The battery pack weighs somewhere around 38 to 42 kilos, which is pretty heavy, meaning you need to have a very sturdy gripper. That gripper was made in aluminum, aluminum as you say in the US.
We were able to work our magic on this part using generative design and topology optimization, creating something that’s very organic. The cool thing is we walked away from the use of aluminum, used a CO2 neutral polymer material and we reduced the weight with 80%. Enabling us to work with a smaller robot because the weight of the gripper had gone down so much that this gripper, even those light was capable of lifting those fairly heavy battery packs.
There’s so many areas that you can optimize and improve and get more effective and flexible in a battery pack. I could probably talk for hours on this. Puneet would fall asleep, but I’m going to hand over to Puneet because you were also an essential part of the battery showcase right, Puneet?
Puneet Sinha:
Absolutely. Magnus has already mentioned some of the key elements. If you think of it, approximately there are 40 to 50 different steps in manufacturing a battery. Some of them are discreet manufacturing steps and some of them are process manufacturing steps. Every step has its own challenges in terms of the time it takes to complete that step as well as the amount of energy that a specific step consumes. And the combination of these two determine overall throughput and cost of running a factory. I’m going to focus on something a little bit more specific. Among various steps involved in cell manufacturing, cell formation and aging steps are huge bottlenecks. If you go back to the analogy I was giving earlier about how battery manufacturing is pretty much same as cake baking.
The steps for cell formation and aging is pretty much exactly the same as when you put cake in an oven. And these two steps happen towards the end of the cell manufacturing and operators literally take these cells and put them in an oven to be baked and formed and those steps can take almost two weeks, if not more. Think about it. You are waiting for two weeks for every cell to go through those processes before finding out whether you have made a good or bad cell. Two weeks. That significantly lowers production throughput and definitely puts a lot of pressure on the capital as well. Improving these steps is critical for any company who is looking to improve its throughput and looking to improve its quality. How you go about that is, again, coming back to move away from experience-based manufacturing and pivot to data-driven manufacturing processes. We are leveraging simulations, leveraging AI-based data analytics on these steps. If you can collect and analyze time series data, these machines are generating to prognosticate cell quality and how various steps of manufacturing can be improved based on the data, this can help accelerate cell formation, aging steps, find root score, root cause of quality limiting elements and allow companies to take corrective actions on the fly.
And that’s the power of pivoting to data-driven manufacturing where data, real data coming out of machines allow companies to make data to make decisions in real time.
Nick Finberg:
Unfortunately, we can’t record this faster than real time. Because we are out of time for today’s discussion. But we will pick up the rest of our conversation on battery with you Magnus in our next episode. Thank you to both of you and to our audience. If you can’t wait for the next episode, you may want to check out one of the episodes you’ve missed, talking with other industry experts. Or you can read more on siemens.com/battery. Have a great day and we hope to see you again soon!