Unlocking the Potential of the BMS – The Battery Podcast S01E04 – Transcript
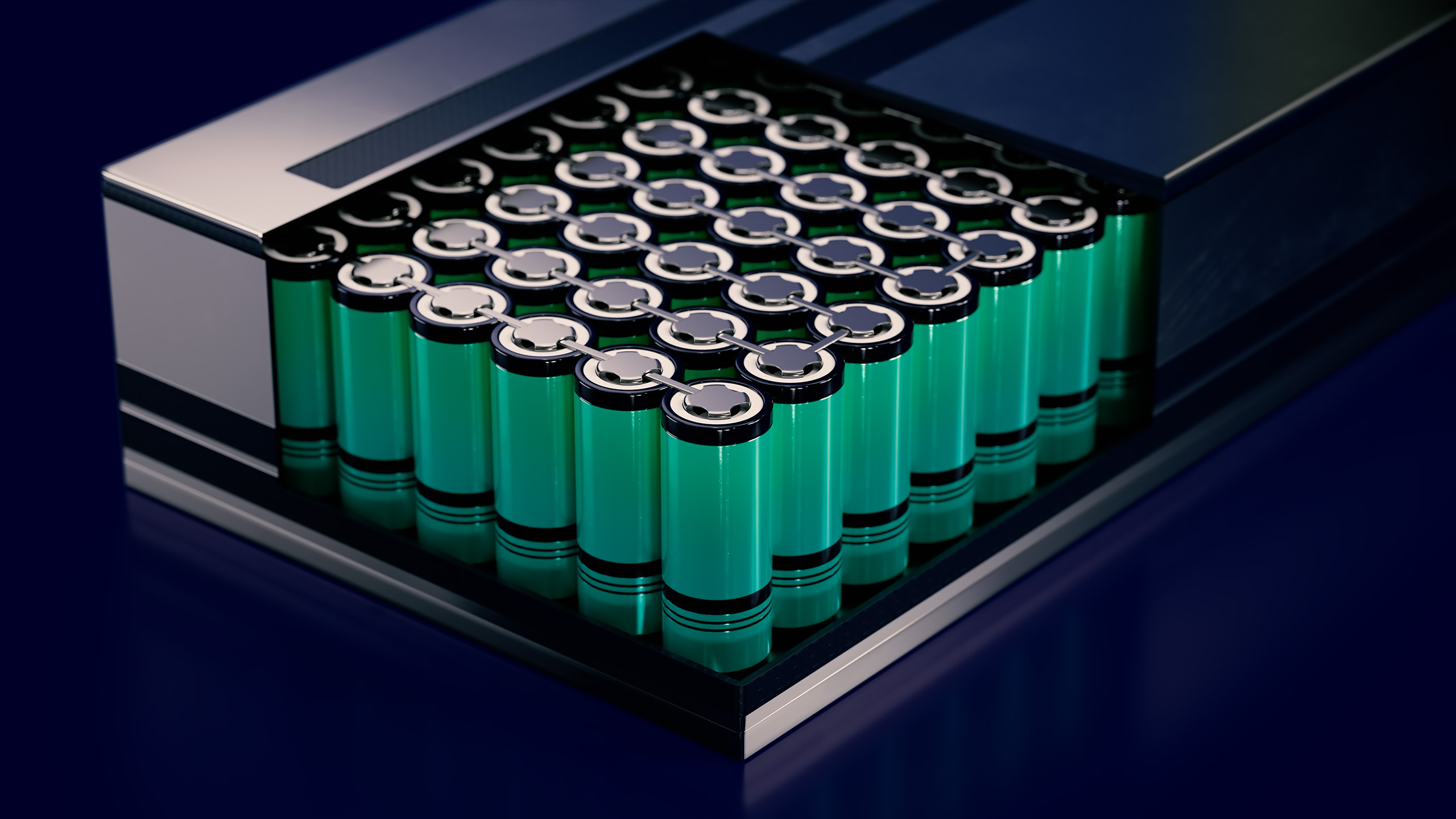
Here is the full transcript of S01E04 of the Battery Podcast, with Dr. Cecile Pera and our host Puneet Sinha. In this second half of our discussion we cover some of the technologies driving innovation in the automotive world and electric vehicles. Hit play to listen along if you’d like, but lets dive into the discussion.
Nick Finberg:
Hello and welcome to The Battery Podcast from Siemens Digital Industries. This is a continuation of our discussion from last time with Cecile Pera talking about battery developments and the automotive market. I’m your moderator, Nick Finberg, and I’m joined by Puneet Sinha, Senior Director and Head of Battery Industry at Siemens Digital Industries Software. For anyone that missed part one with Cecile, she has a background in traditional automotive power trains, but switched gears when she saw the rise of electrification and has kept up to date with the industry since. We’ll start off today’s discussion. What are your thoughts on maybe the shift towards commodification of specific components within the industry? So if you’re standardizing to certain form factors or voltages or even standard pack sizes, do you see a shift in maybe how the automotive industry might function when there are fewer people creating these items or it’s a smaller market?
Cecile Pera:
So it’s a very, very common question I receive very often and what if all the industry could sit together and decide that some standardization because in terms of recycling, in terms of refurbishing and so on, it would really help, I’m going to say humanity, to get everything simple and maybe agree on something, everyone would get some standard about this. But I don’t believe this can happen for the reason that OEM need to differentiate themselves. Because internal combustion engine adds a specificity that you add some character, some specificity. So here again, you really need to get your specificity as an OEM, and this is one of the key points in terms of it’s still difficult for many people to see emotion and still difficult to see how they sell their image, but you can see some OEM trying to do that and some better than others. Like Tesla get a certain personality and for sure Tesla is not going to adapt, for example, the standard of someone else.
Or for example, Porsche. They have the unicity to get, it’s not very common as you know to get two gear for an electric vehicle and they keep that also in the sense that it makes them, or at least the Taycan slightly different from other pack maker or there is the Maserati Gran Turismo that gets a battery pack with definitively not a flat floor battery because they need this for their personality and their work to drive.
So in terms of strategy, if the OEM would agree altogether on some standard like say everyone using prismatic or everyone using cylindrical or whatever, then it’ll remove a certain competition and plus the fact that there is so many things happening all the time because just the cells there are new sales format, cell factor or slightly a little bit more increase here and this increasement in power density may be enhanced because you have this sort of cooling here. So I don’t believe OEM get an interest to sit all together to agree first. Secondly, I also do not believe in terms of the best of the technology, it would cut the possibility to develop further in my opinion. But I do agree that if we could get something like some kind of standard then in terms of future problem like recycling, dismantling and so on, of course it would help, but I don’t believe it’s going to happen. I don’t believe so.
Puneet Sinha:
Let me add some color to it as well. I agree that industry right now is far away from a centralization for many, many reasons. Those reasons include but are not limited to the shape and size of the cells they’re using in their pack. The size of the pack and the technology elements and those technology elements can be not just about the cell hardware but also even about battery management system. A lot of the companies are using wired battery management systems. Some companies are looking to move to a wireless battery management system architecture as well.
But then there are additional issues also start coming. As you know right now most of the companies are working on delivering battery packs that can be charged quickly and when I say quickly means less than 30 minutes. So that’s where some companies are delivering solutions. A lot more companies are looking to build those battery packs and integrate in their vehicles to achieve that. But in the pursuit of reducing charging time, some of the companies are also reinvigorating the concept that has been tried let’s say 10, 15 years back that is battery swapping and now that the electrification has become a mainstream element of transportation industry, I think there are certain benefits of re-looking at it.
NIO in China for example, is one such company that is strongly looking into and also rolling out some of their battery swapping stations. So when you look at all of these elements of not just technology but the customer experience companies are looking to deliver, standardization is not possible. Having said that, for a given company which is looking to build electric vehicles for different purposes for passenger vehicle to pickup trucks, even to semis or mass transportation, there is significant benefit if they can within a company can standardize on a battery pack platform which is modular, they can add to that but keep the structure or the layout same.
And we are seeing many companies are looking to move in that direction. For example, GM has come up with their Ultium battery architecture. So of course as they look to electrify their complete vehicle line, they’re not going to use the same battery pack, but they’re looking to leverage the same architecture and the same goes for many other companies. So a lot of companies are looking to do that to bring more efficiency in their design, engineering, manufacturing service of their electric vehicles. And that is a welcome move because that definitely makes it a lot more easy for one company’s vehicle to be serviced better, to be manufactured a lot more easily. That brings down the cost and also then the issues of reuse and recycling becomes relatively easy for a set of vehicles that are coming from one company. So that is great and I believe more and more companies are looking and moving in the direction of standardizing their electric vehicle battery architecture, which may differ from other companies’ architecture.
Cecile Pera:
I would like to add something here. It’s true what you say, it’s completely true and modularity is really one of the key trend we see in battery pack design, but it still depends on the strategy of the OEM. Like for example, Volkswagen gets this MEB platform, which you’ve got your battery pack, which can be I think seven, nine or twelve module. So it’s relatively easy because the module easy to integrate and they’re the same. So you can plug and play in the sense depending on the size of your pack. So it’s relatively modular and with one architecture they can fit a lot of different cars inside the Volkswagen group. But that works because most of their car are not that much different. If you take a group like Stellantis for example, this is slightly different because if you take an OEM like Maserati, they cannot, if they would use the same platform as, I don’t know, just a Opel or whatever, this would not allow them to differentiate themselves inside the brand.
So in the case of Stellantis, the Maserati would get a very different battery pack if you’re talking about the Gran Turismo or if you’re talking the the Grecale, which is the SUV because you still need to get this identity and this differentiation because otherwise you have no purpose. So its true modularity is key and it’s reduced cost obviously, but at the same time it also reduces the personality you can add inside your own group or within different worldwide OEM. So it’s a difficult game between what you try to standardize in terms of simplification and cost reduction and where you try to be able to be more flexible or get more high performance technology or very on purpose development. Again for certain purpose of application like slightly motor spa I would say. But still it’s a difficult choice to do for an OEM to know where they want to get something very, very modular or more specific.
Puneet Sinha:
So Cecile, I have a question. I would love to understand your perspective. As both you and I know, battery pack is more than assembly of cells. There is battery management system, which is actually the brain of battery and there is a lot of activities happening in the industry to build a robust battery management system that can help avoid a lot of recall issues. I’ll be very interested to understand your perspective on what is happening in the industry for battery management system development and some of the challenges that come with it.
Cecile Pera:
So again, BMS is a full part of the technology on itself with BMS getting different sub technologies that are trying to be developed in parallel by many people. So there are many, many different things I can talk about. BMS, you mentioned wireless BMS is one of them. I think another very key trend is also to use coupling the BMS with the cloud. So you also store a part of the energy then enter here a lot of different strategies. So some people want to put a part of the computation directly on the chip, on the BMS and then just exchange a part with the cloud. Some people want to exchange more in the cloud, they are here. Also, the topic about digital twin, because in order to save a little bit of data, there are a lot of strategy to construct highly complex digital twin, which it’s one of the key trend.
There are also a lot of things about aging of the cell. We have not talked about that, but warranty and life of the battery is very key. So for now the standard is eight years but we have people pushing for ten years and some lobby pushing for twelve. I have even heard fifteen years possible in the future. So balancing of the cell being able to target the aging is very key. Also, another point is when we have developed internal combustion engine, we have been through discovering problems that happen. Like for example, a very famous example in internal combustion engine is what we call the anti-mini cycle. So it mean like I’m an old woman, I’m not old, but let’s imagine I’m old on this example and I just want to take my car to buy some bread daily. I take my car, make a cold start each morning, drive my car one kilometer, come back.
We have discovered with aging of automotive that this sort of behavior is very bad for internal combustion engine because you are running cold start constantly. What I want to say is that I am sure I’m one hundred percent sure that in the future we will discover that some behavior may not be that good for aging of the battery. I don’t know what it is for now and I guess people would like to know, but I don’t know, maybe if you leave close to the sea and get a lot of corrosion or I don’t know, maybe if you park your car and you are on the mountain and do not regenerate correctly when you start, I don’t know. We probably are going to discover that there are some behavior better than others and then the BMS here start to be key because it’s not only monitoring the cell, I mean like the brain you have discovered, you have described before, but it also monitoring and gathering information to give this access to OEM.
Cecile Pera:
So they can also analyze in the future. And again, I think the OEMs that are the most advanced, like Tesla, they benefit from the fact that they have data and collections of data for many many years so they know better than others some of these behaviors probably better than others. Which in my opinion also participate to the fact Tesla batteries seem to age better than some others. And again here Siemens would have a lot of things to do because data management as a software company, you have many things to play here
Puneet Sinha:
That’s great Cecile. This is very insightful. Some of the things that we are also seeing in our engagement with the industry.
All the issue that you mentioned, are coming to the floor. Recently, my team was talking with an OEM and they were talking about the usage driven in general. It’s pretty much taking similar example that you said, Hey, there is a person who is charging their vehicle every time they find a charger versus a person who is more adventurous, they’re only going to charge their vehicle when the battery is pretty much at zero. What are the implications of that on battery aging? How the battery management system can help guide certain controller strategies and learn from the usage of vehicle depending on driver persona. So they are definitely some of the areas companies are looking into and again, we are more and more in our daily lives getting used to getting a customized experience, be it with our cell phones, be it the e-retail shopping experiences and those technologies, AI and the machine learning and the behavior mapping. I believe they are very rapidly going to make their way in the world of battery because at the end today’s generation is that of experience.
Nick Finberg:
So a lot of that parallels what’s happening in the automotive industry, whether it’s ICE or electric vehicles in figuring out what is the usage of these cars by the customers and even to a large extent with electrification, not just in the battery or the propulsion systems, but in the accessory or entertainment systems. You can update them automatically or once they leave the lot. Is there any way currently or pathway in the future to begin to update BMS systems after they leave the shop floor to either prioritize the charging schedules for someone who goes all the way to zero every time or if they’re topping up to create more of a padding at the end or the top of the battery to help with the longevity? Are there any things happening in that space?
Cecile Pera:
Over the air? So what we call OTA over the air is again one of the key trends for electric vehicle in general because OTA can be used in two way or at least two way I know. The first one is to make update of the software. So maybe there is one things you want to update about the software, whatever. The second one is to, as I say, push the data from the OEM. So you at battery show for example, you could see some people explaining you how OEM could maybe in the future get fleet management or at least statistics of data where they received information from the BMS with this auto. Then I would say also to complete the BMS discussion in this order, they are also BMS that are able to adapt the behavior of the driver by some artificial intelligence.
So there is a company called Eatron Technologies, at least I know this one in UK where they have A BMS where their BMS will take into account aging, which can be slightly different depending on the way you are using your electric vehicle. As you say, if you are charging it daily or if you are driving super sporty or like an old woman or whatever. So depending on this, the way the BMS will control the aging of the cell will start to adapt individually. If I would say that thanks to some kind of artificial intelligence and discussion to the cloud and modeling store in the cloud and so on, they will start to get a better BMS and better idea on people of this exchange. So again, OTA is one key.
Nick Finberg:
Oh, that is super cool
Cecile Pera:
Over the air and all this is really, really key. There are also people who want to use this over the air application also potentially to store what is the state of health of your battery. Also, if you would like for example to do, if you want to sell your electric vehicle secondhand, we also can imagine the future that with this knowledge, I’m going to say coming from exchange with the BMS and OTA and so on with the QR code on the battery pack, you could have an estimation of what is the state of health of your battery pack. So it would for example, help people purchasing a secondhand car to know if the battery’s at risk or not, for example.
Nick Finberg:
Thank you Cecile for joining us for this discussion and bringing your insight on the automotive market for battery. And thank you to the audience. We hope to have you back again soon. If you haven’t listened to part one of our discussion with Cecile, it covers some of the design and manufacturing challenges OEMs and manufacturers are facing in the battery industry as well as how a system view is critical to understand these hurdles or listen to Marc Deyda’s interview from the Battery Show Europe and you can check out the episode description for where to find us and more information on the battery industry.