Driving Innovation in Cell Manufacturing: Siemens and Accenture’s Impact on Gigafactories
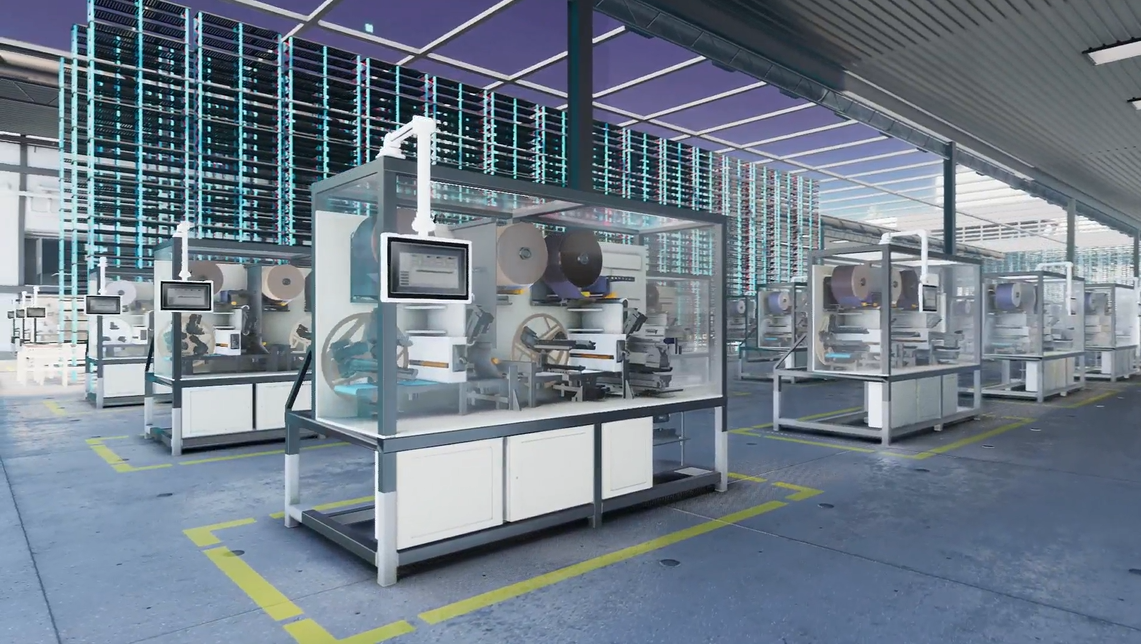
Stemming from demand and regulatory pressures on the battery industry, production is moving beyond the traditional hubs for manufacture. And one of these new regions for battery production is continental Europe. There are regulatory pressures to adopt electric vehicles en masse and to do so using locally produced components for many different reasons. But that is not the story for today, however the pressure is being applied, the businesses setting up manufacturing capacity in the region have a need to accelerate their business. To talk about this exact situation, Marc Deyda sat down with Dr. Philipp Wunderlich from Accenture for on Episode 12 of The Battery Podcast.
You can listen to the full conversation here but keep on reading to get a quick summary of what these two experts had to say on accelerating battery manufacturing in Europe.
Scale is perhaps the most apparent challenge in the world of battery. While a revolutionary cell technology is a great technological leap for the industry, taking that to market scale is a large portion of the work that will go into the battery development. Manufacturing a battery means assembling a very complex and sophisticated electromechanical device. Doing that successfully requires high-quality, repeatable, and efficient production. An additional challenge for the European market is that it is being set up without the wealth of experienced workers and business relationships present in the Asian manufacturing hubs. This is why strong partnerships are so important for businesses trying to grow up in the region.
Starting a cell manufacturing project can be a costly capital expense, and a risky one if a business does not have as much information and support as possible. Accenture for instance offers business planning and strategy consultations to help businesses understand the feasibility of a possible project. And from the Siemens side, we can help these businesses learn as much as possible by testing the production design and processes in the digital world. By working in the digital world early on, businesses can reduce the risks and financial burdens of physical assets and even kick-start their production to reach a viable product in less time.
Though batteries are often seen with a sustainability filter, because they offer a path to electrifying many industries, the production of the cells themselves is very energy and resource intensive. Simulating production early on helps bypass some of the most common sources of failure in production before making a single cell, but once a factory is running it needs to continuously improve. Using real time data from the machine, production, and even the product, manufacturers can optimize production to use less energy, fewer resources, and do so over shorter timespans.
In addition to data helping the manufacturing process, accurate data collection is necessary to comply with regulation. That might be emissions tracking to conform to local policy, but it is also for battery passport regulations. Part of making the battery sector more sustainable is providing transparency across the entire value chain from raw material to recycling. Fortunately, this requirement also offers an opportunity to manufacturers and OEMs using the batteries. They can learn how the product is being used and how it fares in the real world across a much wider sample set compared to testing that could be done in-house.
But his is only a fraction of the great conversation in this episode of the Battery Podcast. I would recommend listening in to learn more and subscribe to the series so you don’t miss new episodes as we explore the world of battery.
Siemens Digital Industries (DI) is a leading innovator in automation and digitalization. In close cooperation with its partners and customers, DI is the driving force for the digital transformation in the process and manufacturing industries. With its Digital Enterprise portfolio, Siemens provides companies of all sizes with all the necessary products, along with consistent solutions and services for the integration and digitalization of the entire value chain. Optimized for the specific requirements of individual industries, this unique portfolio enables customers to enhance their productivity and flexibility. DI continuously extends its portfolio to include innovations and the integration of future-oriented technologies. Siemens Digital Industries, with its headquarters in Nuremberg, has a workforce of around 72,000 people worldwide.
For more information on Siemens Digital Industries products and services, follow us on LinkedIn, Facebook, Twitter, and YouTube.