Deploying AI to the real world: How Siemens Erlangen factory is leading the AI charge
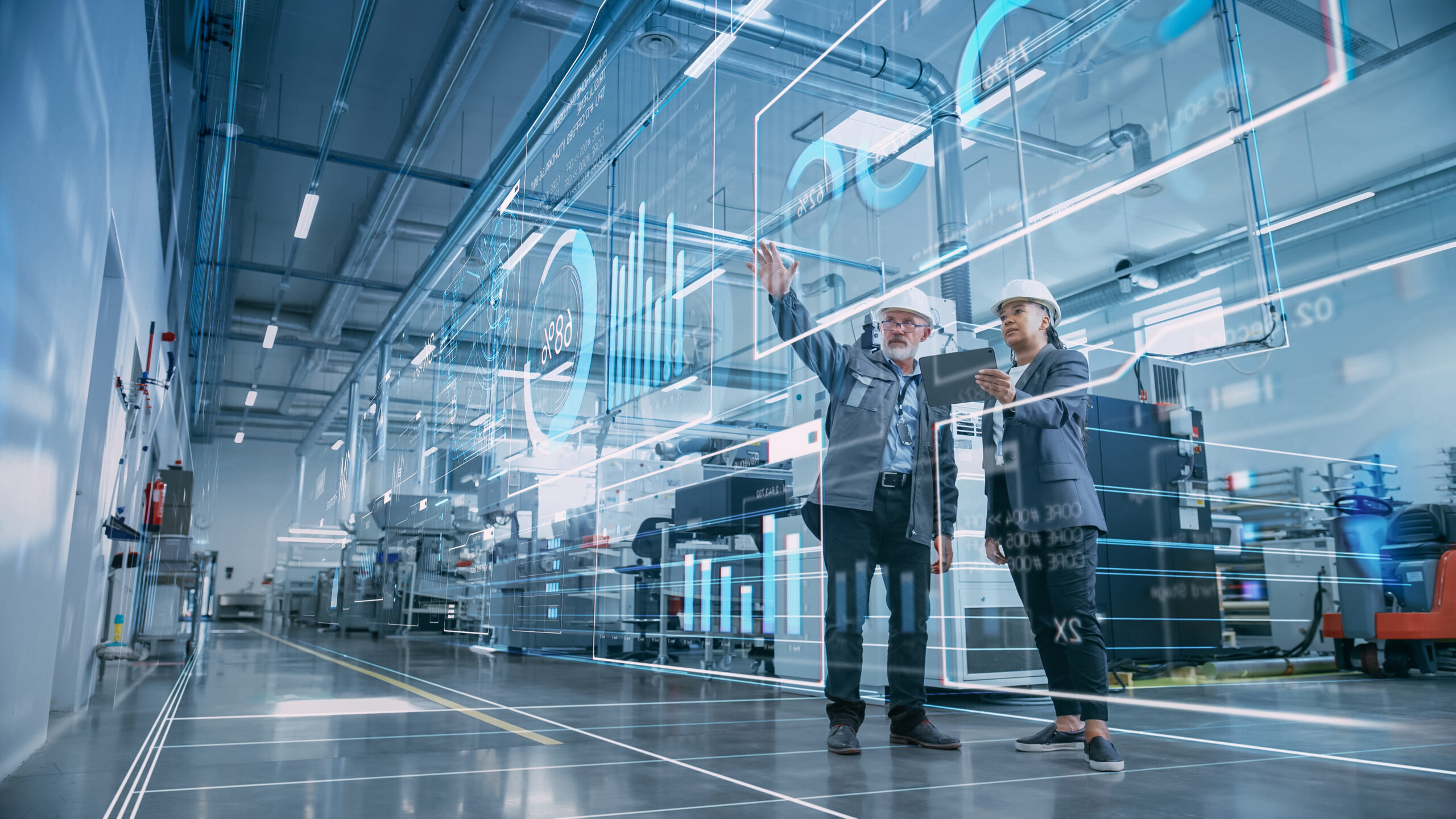
Artificial intelligence is at the forefront of the industrial world, with nearly every company either interested in or actively deploying AI. Companies are increasingly adopting AI to optimize processes, improve quality, and address pressing challenges such as the global shortage of skilled labor. But it is not a simple task to translate the desire to create AI solutions into an industrial grade AI solution.
Maximilian Metzner, Global Lead for Autonomous Manufacturing Systems at Siemens Digital Industries, spoke about some of the benefits of pursing AI automation within factories, especially with how it can offer a cost-effective path to replicate human-like capabilities. Beyond the hypothetical benefits, he also how these principles are being employed in Siemens’ own Erlangen PCB factory to great effect when combined with the comprehensive digital twin.
Redefining automation with human-like robotics
To truly bring about a new age of industrial automation, autonomous systems must be able to more closely match human dexterity and perception. By integrating industrial grade AI with robotic systems, it’s possible to enable autonomous systems to perform tasks that were previously thought to be exclusive to human workers. This includes tasks such as those requiring high manual dexterity, visual recognition, or adaptive learning.
For example, at Siemens’ Erlangen factory, by deploying AI in conjunction with advanced robotics, they create an autonomous system that can not only replace human workers for a highly repetitive task but do so without the need for significant pre-preparation of parts. These AI systems can autonomously pick unsorted parts from a box, identify them accurately, and place them in specific orientations for assembly, a task that would have once required a slew of human abilities can now be completed fully autonomously.
Accelerating AI training with the digital twin
A key enabler for developing industrial grade AI is the digital twin, which allows for the training and validation of proposed AI systems in the virtual world without any of the risks typically associated with the process. This virtual testing ground dramatically reduces training time and costs associated with AI implementation.
Instead of relying on vast amounts of real-world data, which can be time-consuming and expensive to collect, AI models can be trained on synthetic data generated within the digital twin. At the same time, the digital twin also offers a safe training environment that perfectly recreates the characteristics of the real system the AI will eventually control. This not only accelerates the development cycle of AI-enabled systems, but also ensures a higher degree of accuracy and reliability compared to often limited real-world testing.
Going beyond theory at Erlangen
At the Erlangen PCB factory, robust industrial grade AI-controlled solutions, developed in conjunction with the comprehensive digital twin, are going beyond theory or proof of concept and being deployed to great effect today. One such example is the use of automated quality inspection. This technique leverages AI algorithms trained to identify even the smallest defects in products, significantly improving the accuracy and efficiency of quality control processes.
Another area that is benefiting from AI is tactile fitting of electronic components, which, through a combination of AI, force/torque sensors, and sophisticated control algorithms, allows robots to perform delicate tasks like inserting Through Hole Technology (THT) components into PCBs with a level of precision and finesse previously unmatched by traditional automation solutions.
In both these cases, AI helps to take on the burden of repetitive and error-prone tasks that would otherwise require human works to accomplish.
AI reshapes manufacturing
Siemens’ Erlangen factory represents a proof point and an important first step on the road to an AI-driven and autonomous future for manufacturing. Boring, repetitive tasks that required human-like dexterity, intelligence, comprehension, or a mixture of all these traits that traditional automation systems lacked can now be passed of to industrial grade AI controlling advanced robotics.
Leveraging the comprehensive digital twin, AI expertise, and their own factories, Siemens represents an ideal customer 0, Maximilion explains, to truly showcase what a next-generation AI-driven factory can be. At the same time, deploying AI to a full production environment also proves that the technology has gone beyond a mere curiosity or lab experiment and is ready for deployment in the real world where companies ready to take the next step forward will be able to reap all the benefits AI has to offer.
Siemens Digital Industries Software helps organizations of all sizes digitally transform using software, hardware and services from the Siemens Xcelerator business platform. Siemens’ software and the comprehensive digital twin enable companies to optimize their design, engineering and manufacturing processes to turn today’s ideas into the sustainable products of the future. From chips to entire systems, from product to process, across all industries. Siemens Digital Industries Software – Accelerating transformation.