The future of smart machines and smart industries – ep. 2
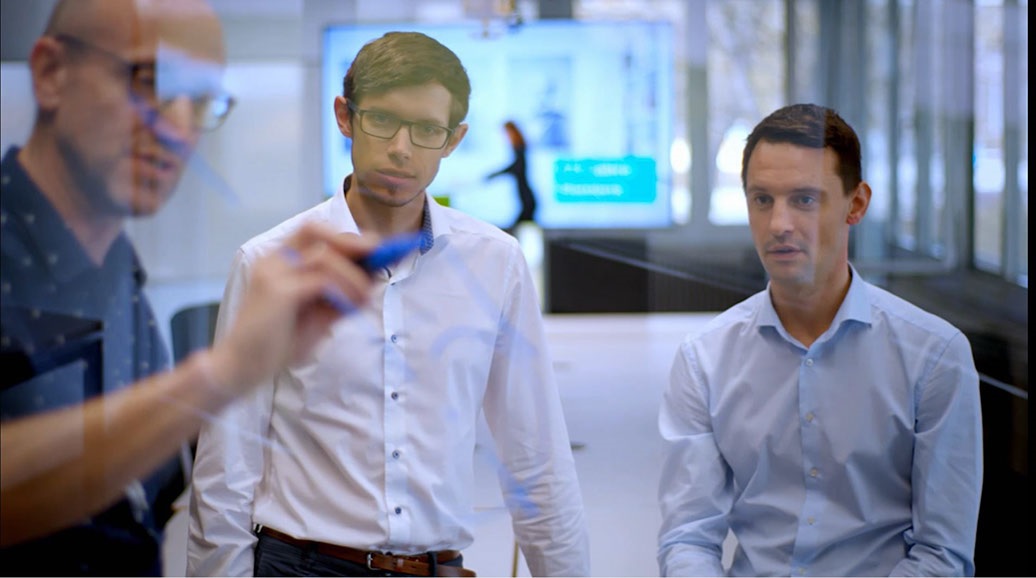
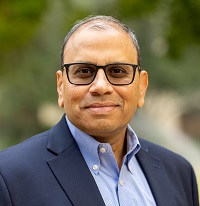
In part two of our smart machines/smart industries podcast series, we are joined again by our engineering experts, Dale Tutt, VP of Industry Strategy; Rahul Garg, VP of Industrial Machinery; and Michael Thomas, SVP of Digital Industries Factory Automation and Head of Production Machines at Siemens Digital Industries Software. This podcast is a vibrant discussion between these industry experts, discussing the challenges facing the current manufacturing ecosystem, addressing technological advances on the horizon, and how digitalization is enabling the future of smart manufacturing.
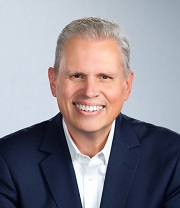
Complexity is affecting manufacturing companies at every level. Manufacturing end customers are moving from automated production facilities to adaptive, flexible production. This process has a massive influence on machine deployment and machine building.
Essential pillars provide flexibility and intelligence to machine builders
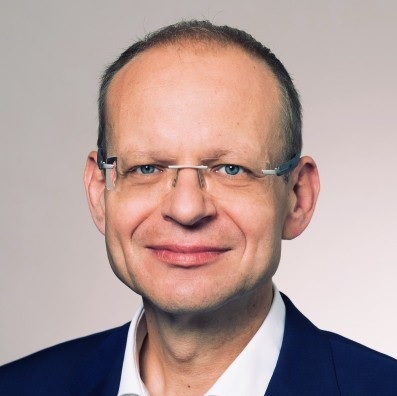
To deliver on customer expectations for smart or adaptive manufacturing, machine builders must transform how they design, engineer, and support the machines across the lifecycle. The three essential pillars that enable machine builders to provide this greater flexibility and intelligence are:
- electrification
- automation
- digitalization
Electrification, automation, and digitalization help machine manufacturers lower risk and improve predictability, providing the path to repeatable processes in machine design and operational processes.
It is vital to continually evaluate the electrical and behavior model of machines within the context of the factory to discover the impact of any proposed changes across the more extensive operation. Fortunately, Siemens provides many plug-in tools and simulation applications to assist companies in evaluating the multi-physics models of smart machines in the context of the broader factory environment. The simulation capabilities for industrial systems encompass the component, machine, and plant levels, providing many tools to the customer to evaluate the entire performance of a production plant, from production planning to actual operations.
Initially, simulation enables the creation of a digital twin of the machine during the design process, which is used to explore a broader range of design possibilities and virtually prototype them. Then, this digital experience generated in the design process is maintained over the machine operation’s lifecycle, merging the physical and digital versions of the machine and process. During machine operation, real-world data is fed back into the machine’s digital twin to optimize the twin’s fidelity. It is possible to explore ‘what if’ scenarios for improving machine quality or line modifications before committing to actual changes. Equally important, it provides a way to optimize continuously for sustainability over the lifecycle of the machinery.
Create a complete mechatronic digital twin of the manufacturing line
Having already evaluated and well-tested libraries for various manufacturing capabilities, such as drives and motors, is invaluable.
Based on our industry-leading role in factory automation, we enable machine builders to create a complete mechatronic digital twin of the manufacturing line. Our capabilities can use the machine’s digital twin to assess energy flows or simulate a possible line conversion, including the rollers, winders, clampers, and sub-applications. Machine builders can easily combine all these in a Lego block manner and take the digital twin of the line to complete 3D physics.
This combination simplifies the process for a machine builder to manage the machine life cycle while delivering a range of machine variants to different customers. The digital twin contains:
- All the mechanical design elements.
- The electrical design elements.
- Any changes to the machine design over the years.
And it leverages that information throughout the entire design life cycle in manufacturing and facility maintenance.
Integrate a digital twin using IT and OT
One of the concepts discussed in the podcasts is how to bring together information technology and operational technology. Integrating a digital thread from the machine and factory design into actual operations reaps significant customer benefits. Taking the data generated on the shop floor and using IT technology to analyze that data provides transparency into operations to:
- Generate more significant performance insights for optimizing machine availability and performance
- Improve productivity in real-time across the machine, line, and plant level
- Enable the use of AI for superb analysis and understanding
These innovative technologies are working in concert to bring change in the industrial machinery industry for smarter operations.
Siemens Digital Industries Software helps organizations of all sizes digitally transform using software, hardware and services from the Siemens Xcelerator business platform. Siemens’ software and the comprehensive digital twin enable companies to optimize their design, engineering and manufacturing processes to turn today’s ideas into the sustainable products of the future. From chips to entire systems, from product to process, across all industries. Siemens Digital Industries Software – Accelerating transformation.