Digital threads forecast for major investment in A&D
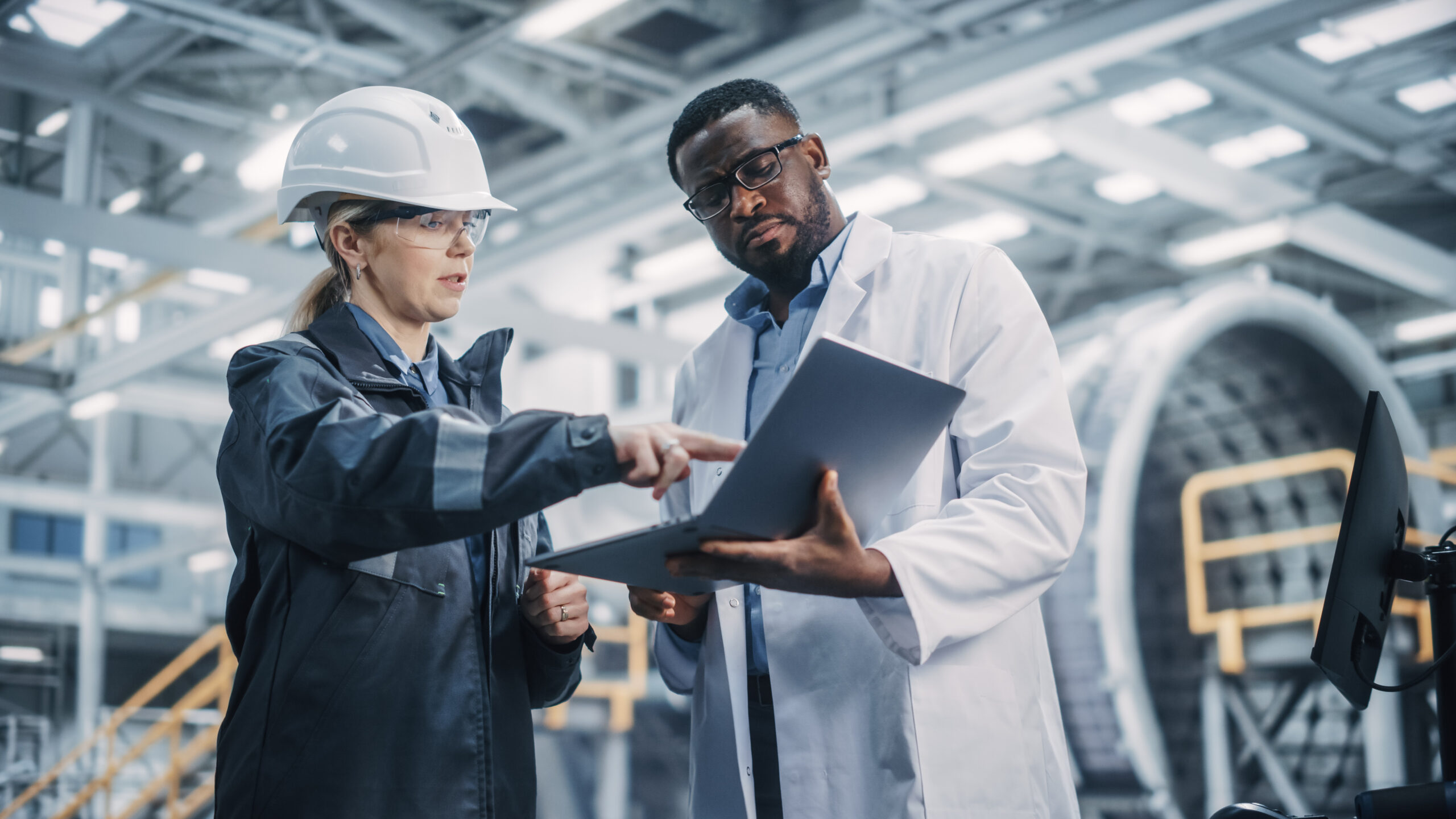
Some time ago, CIMdata conducted research on behalf of the Aerospace and Defense PLM Action Group (AD PAG) member companies, including Siemens, to gain insight into investment in digital threads. The respondents were from various industries, though those from aerospace and defense (A&D) made up the majority. The results, which are fully described in this eBook, indicate that digital thread investment is poised to grow rapidly in the coming years. Such investment bodes well for the A&D industry, as digital threads can connect data across the entire product lifecycle, which can help address many of the challenges hurting the industry today, such as siloed engineering domains.
Defining digital threads
Before going further, it’s important to define what, exactly, a digital thread is. The term gets thrown around a lot in A&D and other industries, but since digital thread adoption is still immature, there is no commonly accepted definition. However, according to responses gathered by CIMdata, there are several widely accepted criteria that different companies use to define a digital thread’s purpose. Over 70% of respondents reported a digital thread’s purpose is to establish traceability of product information, and over 50% report how it acts across domains in the product lifecycle, such as mechanical, E/E, software, and firmware. This matches with how most respondents go on to define a digital thread as the “linkage and traceability between data elements at the meta data level,” as well as the “interoperability between data elements for interpretation of one by the other.”
As mentioned above, the confusion around what a digital thread is can be attributed to its immature adoption throughout industries. Some companies have already implemented such threads in their product lifecycles, but they are not applied across the entire lifecycle. According to data from the eBook, most current adoptions of digital threads are implemented at the earlier stages of the lifecycle, with over 40% of respondents adopting them for the concept stage and over 30% adopting them for the development stage. While digital threads are being used, they are not yet being used to their full potential.
Where digital threads are needed
This immaturity is also reflected in companies’ current lack of digital thread applications in use cases they deem critical. For example, the use case deemed most essential in the eBook was lifecycle bill of materials (BOM) management, with around 85% of respondents claiming it was essential or important. Yet less than 30% currently implement a digital thread for that area. Similarly, more than 80% of respondents claimed a digital thread would be essential or important for cross-discipline traceability, but less than 20% implement one for that use case. There are many areas companies want to apply digital threads to, but most of them still need to make the full commitment.
Cross-discipline traceability is especially important for the A&D industry, which currently struggles with a number of data-related issues like siloed engineering domains. As discussed in a previous blog, aerospace engineers in different domains often use different software tools to create and test designs. To ensure their systems work safely together in the final product, they have to transfer data between each other, which is currently done through inefficient exchanges of paper or electronic documents. As a result, engineers spend most of their time hunting down data rather than actually doing any engineering, increasing program delays and costs. Digital threads could help bridge those gaps and get engineers back on track by improving cross-discipline traceability and data exchanges.
A future with digital threads
Fortunately, according to the eBook, investment in digital threads is predicted to drastically increase in the near future. Most respondents stated their intentions to significantly raise digital thread investments in the near-term (less than three years) and long-term (more than three years), especially for data types in later stages of the product lifecycle currently lacking digital threads. As more stages across the product lifecycle are enhanced by digital threads, product lifecycles and engineering methodologies are very likely to increase in efficiency with A&D being one of the biggest beneficiaries.
Not only does the data gathered by CIMdata forecast on optimistic future for digital threads, but it also bodes well for digital transformation at large. Companies seeking to adopt them into new lifecycle stages will soon experience the benefits of connected product lifecycles, but connection is only the beginning. Continued investment in digital transformation can perhaps one day go beyond connection, not only improving engineers’ performance, but also making the data itself work for them. In any case, digital threads give A&D companies the chance to raise their product lifecycles to new, unseen heights.
Read the entire CIMdata eBook for the full research results.
Siemens Digital Industries Software helps organizations of all sizes digitally transform using software, hardware and services from the Siemens Xcelerator business platform. Siemens’ software and the comprehensive digital twin enable companies to optimize their design, engineering and manufacturing processes to turn today’s ideas into the sustainable products of the future. From chips to entire systems, from product to process, across all industries. Siemens Digital Industries Software – Accelerating transformation.