MBSE applies everywhere, even Formula 1
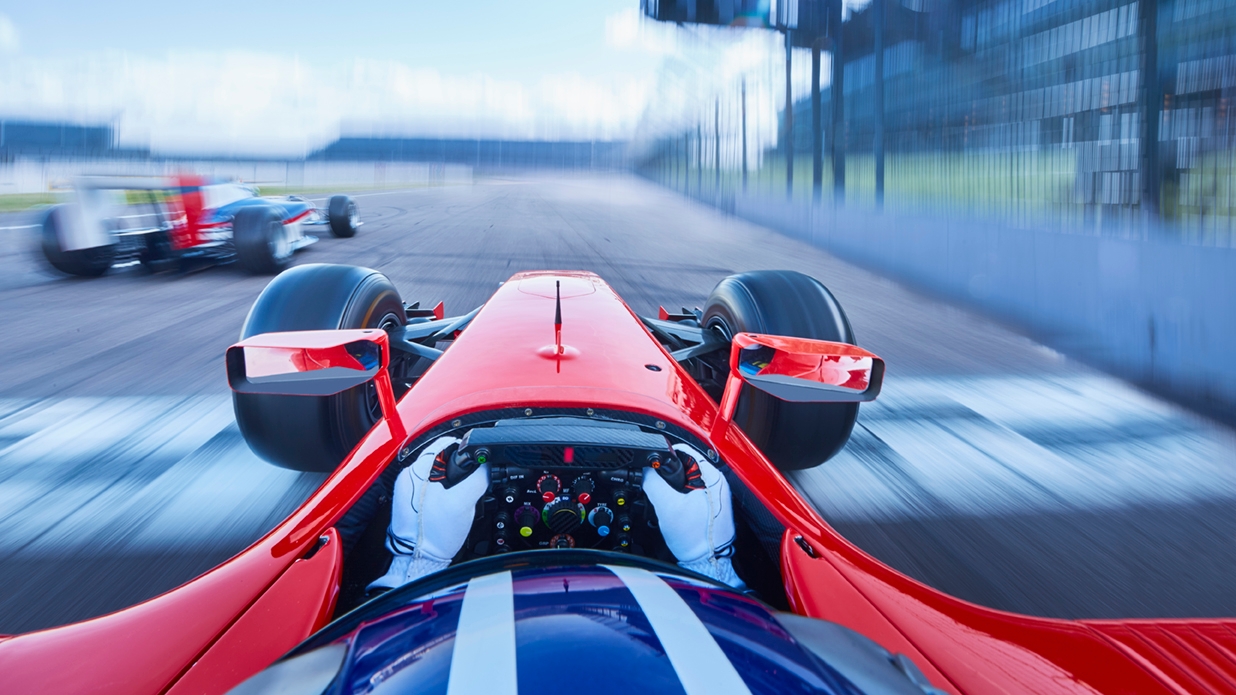
For most companies the entire value proposition around model-based systems engineering (MBSE) rests on designing more-complex systems, doing it faster than before, and enabling rapid changes from a variety of stakeholders. That fits a variety of industries and products – consumer products, aircraft, and even industrial equipment. Each of these is seeing complexity from rapid introduction of electronics and software as well as a growing need to meet sustainability targets. But one business type that might usually be overlooked when it comes to MBSE methodologies is Formula 1 racing, it is a sport steeped in tradition and full of engineers already working as agile teams.
Formula 1 is not unencumbered by complexity however, there are highly optimized designs in the engine and powertrain, the aerodynamics of the cars, control systems, and much more. There are also pressures to change what has been central to much of F1 pedigree for decades – the engine. Whether the organizing body adopts hybrid fuels, hybrid drivetrains, or full-electric systems, there is set to be lots of change to the engine bay. That may require a completely new set of skills to work together on these powerful machines. This complexity and other’s inherent to the sport have not been overlooked by those with an eye on success. Red Bull Racing is one of those competitors, employing a suite of connected software solutions.
Harnessing constant iteration
To many, Formula 1 is seen as the peak of automotive innovation, and it is hard to argue with that descriptor. The sport is often the first to employ technologies in design, production, and more. The entire sport is built on eking a few more percentage points out of every system through better airfoils, better energy transfer, and better braking performance. But it is not just a sport of year-over-year improvements, it requires a new design with high frequency. And it might even be a complete overhaul, as was seen with the technical requirements published before the 2022 season. The teams need to be able to iterate as quickly as possible to get a car ready for each season and even tweak the cars between events to account for track conditions, weather, and even driver preference. MBSE coordinates the many different engineering groups to prevent backups and redesigns from poor communication of design requirements.
Low volumes are still complex
It might not be the most accurate description to say that an F1 car is a product, its not as if they are sold in any volume. They might even be considered continuously evolved prototypes, but that does not remove the complexity of manufacturing and logistics. In some cases the low volume makes the lifecycle of an F1 car more complex. One of a kind designs need to be manufactured, and many manufacturing processes are eared towards high volume production. This makes production extremely expensive, with no efficiencies of scale. It also pushes teams towards the innovative technologies like additive manufacturing, whose eccentricities need to be understood be designers and manufacturers to get the right component at the end – remanufacturing takes time, which comes at a high cost. There is also the problem of logistics. How do the parts get from manufacturing to the track? Are the right revisions being installed to meet the most current race requirements? Is a complete set of parts being set to the right region of a race series? Tracking all of the information is made exceedingly easier with digital and connected tools.
The reasons for MBSE are many
Model-based systems engineering provides so many different advantages to the development cycles of F1 teams, that it could be a whole book. But they are not the only business that can take advantage of the business accelerating tools within an MBSE methodology and digital transformation. To learn more about how Red Bull Racing is deploying these techniques, Engineering.com has a great article on the subject. But if you brought in on the lure of F1 and work in a very different industry, you might want to check out the topic page on MBSE from Siemens Digital Industries Software. I had to completely skip their innovative use of simulation that was pre-empted by the regulatory changes for the 2022 season.
Siemens Digital Industries Software is driving transformation to enable a digital enterprise where engineering, manufacturing and electronics design meet tomorrow. Xcelerator, the comprehensive and integrated portfolio of software and services from Siemens Digital Industries Software, helps companies of all sizes create and leverage a comprehensive digital twin that provides organizations with new insights, opportunities and levels of automation to drive innovation.
For more information on Siemens Digital Industries Software products and services, visit siemens.com/software or follow us on LinkedIn, Twitter, Facebook and Instagram. Siemens Digital Industries Software – Where today meets tomorrow