The mobility transformation and the rise of electrification
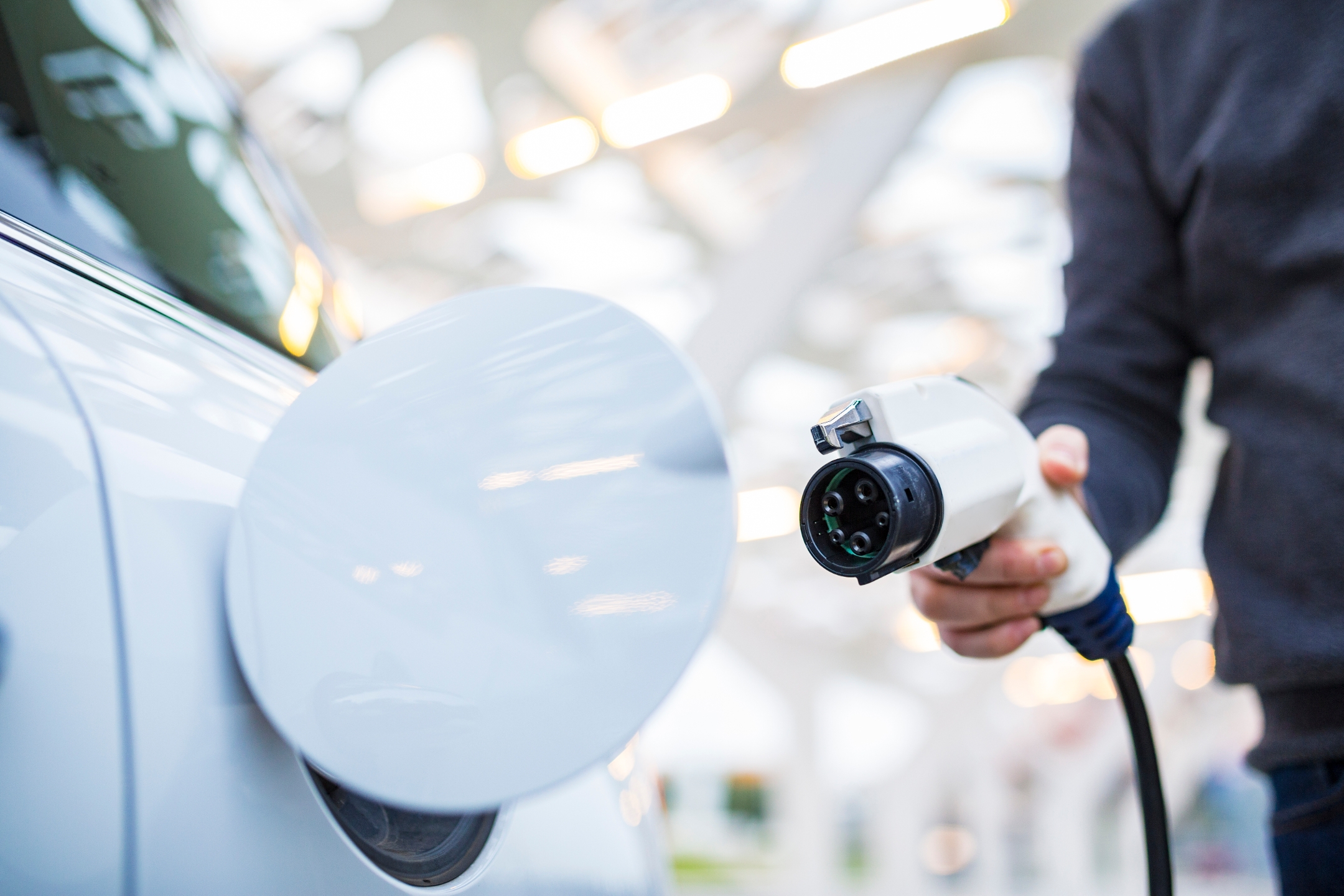
Vehicle electrification is one of the driving forces in the transformation taking place in the automotive and transportation industries. Modern EVs are stylish, spacious, comfortable, and very capable, making them a compelling and legitimate alternative to more traditional internal combustion vehicles. As EVs have gotten better, consumers have responded. According to the International Energy Agency’s Global EV Outlook 2021, global EV stock increased 43% from 2019 to 2020, with each of the three major three automotive markets – Europe, China, and the USA – seeing growth. In Europe, EV registrations increased by nearly double (IEA, 2021). And in the US and China, the sales share of EVs increased compared to overall vehicle sales (IEA, 2021). With nearly every major automotive manufacturer either already selling an EV or bringing one to market very soon, we can expect more and more consumers to go electric soon.
And yet, despite much cause for optimism, automotive OEMs and startups continue to face challenges in the production and sale of EVs on a mass-scale. What are some of these challenges, and how can manufacturers improve their abilities to overcome them?
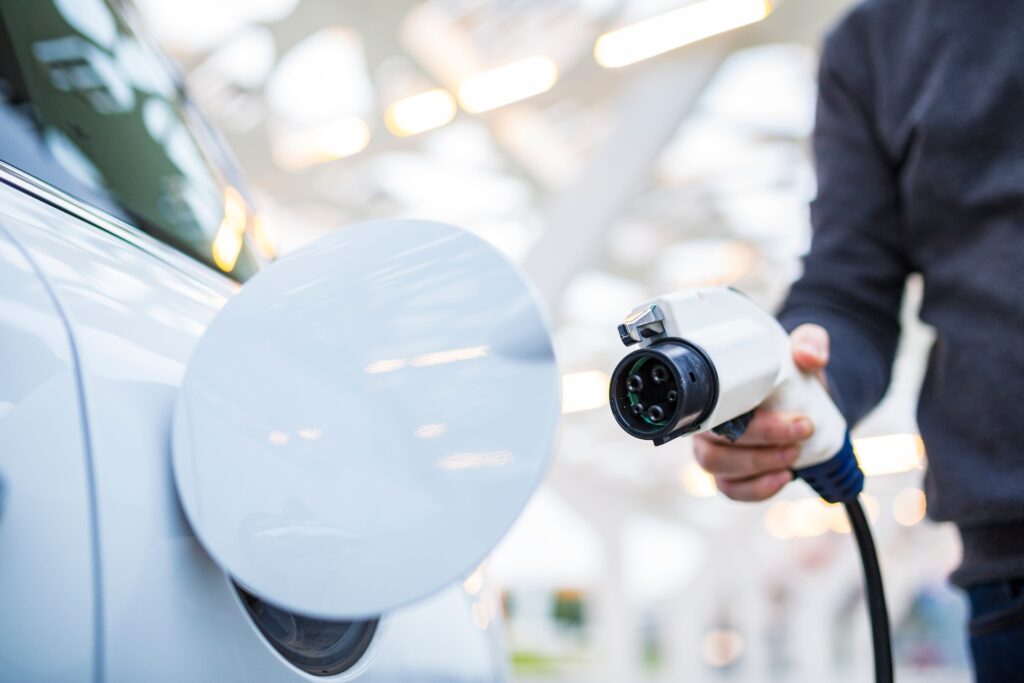
First, though battery technology and recharging times are improving quickly, many consumers continue to have concerns over drive range and the time required to recharge once the batteries are empty. Today, with many EVs able to achieve 300 or more miles on a single charge, this anxiety is primarily driven by the sparsity of charging infrastructure, at least when compared to the vast network of gas stations on which drivers of combustion vehicles can depend. To convince people to make the switch, EV manufacturers will need to contribute to the development of charging infrastructure by working with various levels of government, utilities companies, charging station manufacturers and more.
The next set of challenges comes into play during the manufacturing and service of EVs. Due to the high voltages required in an electric powertrain, the production and service of an EV entails unique safety considerations. Production and service technicians working on EVs need special training and equipment, such as insulating rubber gloves, to perform their duties safely. Furthermore, areas of a facility in which the service or manufacturing of high voltage components is being performed must be well-marked to ensure all employees are aware of the potential risk. Manufacturing and service procedures must adapt to these safety considerations or be replaced by new methods. EV manufacturers also need to determine the best strategies for the recycling, reuse, or disposal of EV batteries. New materials have helped to improve battery performance and reduce the cost of battery production, but they can also be dangerous or toxic if improperly handled. The industry must continue to develop appropriate methods for processing these materials at scale.
Addressing these challenges will help EV manufacturers as they strive to entice consumers with new EV offerings. As modern EVs continue to push styling, performance, comfort, and high-tech features forward, consumer opinion is already beginning to shift. Automakers that can capitalize on this shift early stand to reap the greatest benefits. We believe a new approach to vehicle development is necessary. Automotive manufacturers must embrace digitalization and break down the boundaries that often exist between engineering domains and the stages of product development and manufacturing. Key to this approach is a comprehensive Digital Twin that captures every aspect of the vehicle design and production. Using such a Digital Twin, automotive manufacturers can connect engineering teams from across the electrical, electronic, software and mechanical domains. This means manufacturers will be able to design, verify and validate entire vehicle platforms, ensuring the highest standards of safety, reliability, and passenger comfort.