Replacement parts, fast, with additive
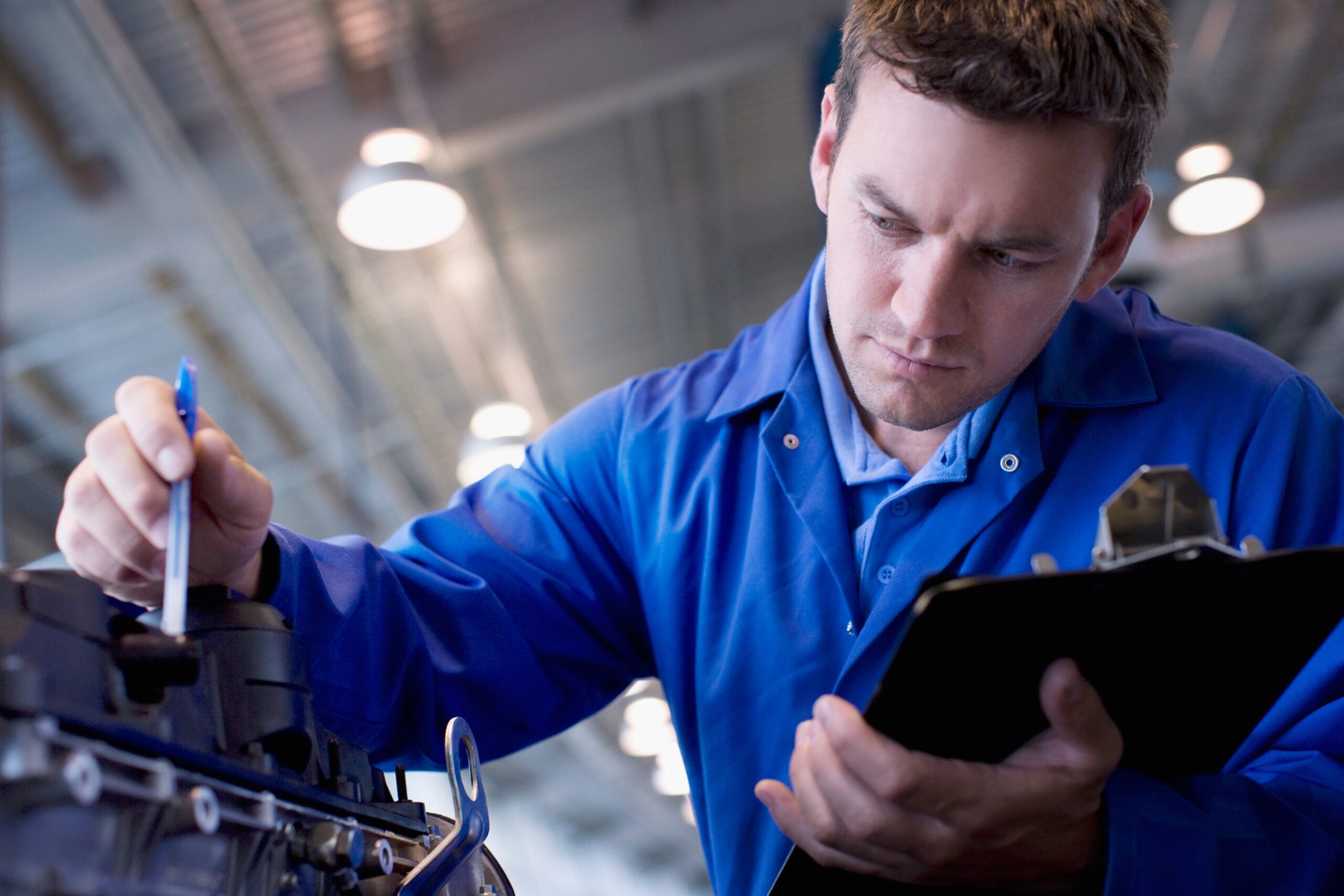
Reading a great article from 3D Printing Industry, I started really thinking about the application of additive manufacturing (AM) for replacement parts. The author explained the role of worn part repair as Siemens Energy has been working on as well as some full part replacement services from Daimler AG and Sauber Engineering, but how far could an AM application extend for prolonging the lives of our favorite machines? Will replacement parts be more accessible? Will once inefficient designs be upgraded? What will be the impact on decommissioning when something finally goes caput?
The first path in extending the product life is already a part of some industries. Keeping stock of replacement parts is an expensive proposition for many aerospace and high-end automobile manufacturers. The cost of holding onto, often custom-made, parts for non-wearing systems is too great compared to the loss of floor space or warehousing costs. Instead, some manufacturers are holding onto the CAD files and printing a new part when needed. This also eliminates the need to hold onto the tooling for parts or worse purchasing a new set after getting rid of the originals. But this application may not have to remain in these cutting-edge industries, as printing becomes more automated and the financial barrier to entry lowers the technology could make its way into small repair businesses. Rather than trying to order out-of-stock parts for home appliances, the repair tech could make a copy of the part in-house and get everything running in no time.
Aside from one-to-one replacements, there is also an opportunity to improve the performance of our machines with a proliferation of AM technology. It could be a machine that has been in operation for years or an early prototype of something new, but if there is an avenue for performance gains someone will likely want to exploit it to make their machine better. For a refrigerator it might mean replacing the compressor and adapting the existing coolant lines to the new system. For a vehicle is might mean replacing a generic fluid line with something optimized for better flow characteristics and efficiency. It is unlikely this would become viable in the home applications beyond the highly dedicated, but for automotive it could be here soon. Tuning shops have existed almost since the first car and AM would just be the next variable to tweak for better performance. More performant replacements could also make headway in electric vehicle conversions as petroleum use fades away – as aerodynamic improvements, weight reductions, or for custom mounting hardware for new componentry.
The last possibility I see for bespoke AM components extending the life of our machines is in the decommissioning and reuse of functioning components. Whether as a means of cost savings or to reduce waste accumulation, reusing functioning components from dead systems will be critical in the shift towards a circular economy. If only a handful of identical components are available it would be foolhardy to create the traditional tooling to reuse the component in a new system, but AM removes the upfront investment meant for high-volume production. Adapting older components to newer ones is already a common process for vintage cars where owners put new engines and transmissions into their beloved vehicles to get more time with it, more power from it, or completely change the drivetrain with electric swaps. The next step will be incentivizing the use of old components rather than those directly from the factory. This could become easier in the automotive market during the switch the electric as components are becoming commoditized and would be ripe for a competitive used market. AM could become the translation layer between new and old in any system.
I am not an oracle for the future of AM, but I wanted to share my thoughts on the possibilities that can be imagined with such a groundbreaking technology. These ideas may never come to pass in large volumes, if at all, but to create the next economy we all need to think about change. How can we reduce the wastes of current economic structures and incentives? How can we make our products friendlier to the environment? Additive manufacturing is one of the tools to creating that new world, but it has to be done intentionally to make the results as great as possible.
Siemens Digital Industries Software is driving transformation to enable a digital enterprise where engineering, manufacturing and electronics design meet tomorrow. Xcelerator, the comprehensive and integrated portfolio of software and services from Siemens Digital Industries Software, helps companies of all sizes create and leverage a comprehensive digital twin that provides organizations with new insights, opportunities and levels of automation to drive innovation.
For more information on Siemens Digital Industries Software products and services, visit siemens.com/software or follow us on LinkedIn, Twitter, Facebook and Instagram.
Siemens Digital Industries Software – Where today meets tomorrow