Additive Manufacturing in the Aerospace Industry – ep. 2 Transcript
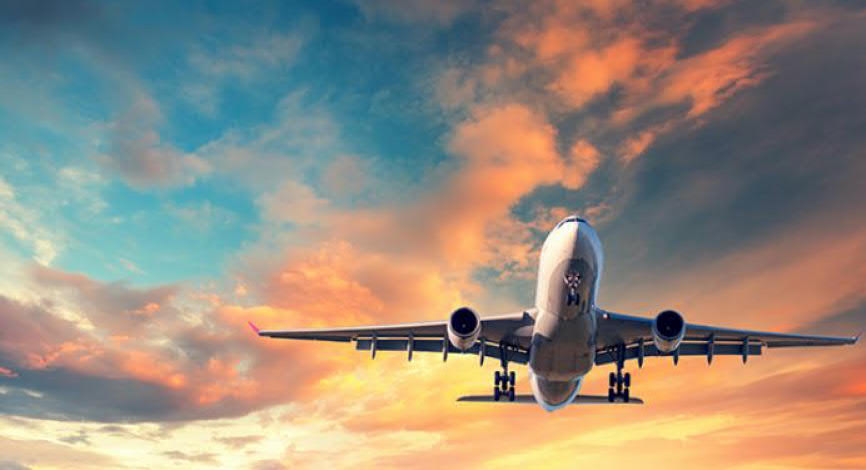
Thanks for joining us in the second podcast episode of the additive manufacturing and aerospace series, learning from the experiences of early adopters of additive technology, and the role software plays in the process. Also, find out about the hurdles to industry-wide adoption and the future of aerospace technology.
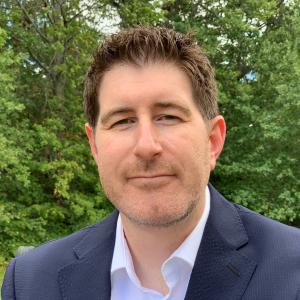
We are joined again by Ashley Eckhoff, Marketing Manager for Siemens Manufacturing Engineering group, and Dale Tutt, Vice President of Aerospace and Defense Industry at Siemens Digital Industries Software. As a crucial element of our industry strategy development around aerospace software, Dale provides valuable insight into the needs and perspective of customers to assist our product teams in developing innovative solutions that improve the overall experience. Listen to the podcast or read the transcript below.
Read the transcript:
Ashley Eckhoff: Hi everyone, and welcome back to season two of the Siemens Additive manufacturing podcast. I’m Ashley Eckhoff and I work for the additive manufacturing product team at Siemens Software. This is episode two of our second season and today we are continuing our conversation with Dale Tutt. Dale is the Vice President of the Aerospace and Defense Industry at Siemens Industry Software, so Dale leads the industry strategy around aerospace software.
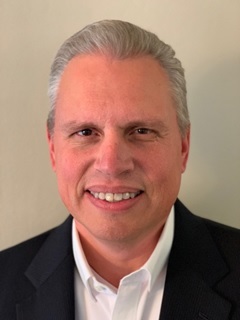
If you missed our last episode, Dale and I talked about how additive manufacturing is affecting the aerospace and defense industry, the types of aerospace parts being printed, and we touched on standards and certifications.
Welcome back Dale. I think I’d like to start off today talking about using suppliers vs. printing in-house.
It seems like a good portion of the larger aircraft manufacturers that I know of are utilizing suppliers for a lot of their part production, which I guess is similar to what I hear of in the automotive industry; what percentage of printing would you say is being done in-house versus at suppliers’ these days, and does that differ between commercial, defense, and space applications?
Dale Tutt: It’s a little bit hard to say, I’d say right now that as companies are adopting the technology for the first time, it’s probably not that unusual that most of the parts will be printed at a supplier. And the reason for that is they may not see that they have enough throughput to make the parts, to keep the equipment busy at their own facility, so they can partner with a supplier and have those parts made at the supplier. But then I think, as they ramp up the production processes, you’ll start to see then there’ll be more balance, maybe it’s 50-50. Maybe be basing that a little bit on what we’ve seen even with composite part manufacturing, with sheet metal part manufacturing that it’s not that unusual for 50% to 60% of the parts to be made at local suppliers. So, I think that you might still see the same thing with additive manufacturing. Now, the one difference that may play a little bit role into this, it would depend on the kind of part; if you are making an engine part that’s supercritical engine part, or maybe you’re making a landing gear trunnion, at some point in the future, that you want to highly control that process and you want to really know how it goes – so, those very critical parts, you might want to make them on your own machine so that you can really keep track of the process and really have knowledge about the entire process as it goes through that. But a lot of times that would really be more of a business decision than necessarily a technical decision because the equipment is the same, the supplier’s capabilities are often the same. I think it really just comes down to a business decision. I don’t know, right now it probably feels about 50-50, I’m not sure, as different companies are approaching it a little bit differently, especially if you look at defense versus commercial.
Ashley Eckhoff: I think what we see a lot with just an industry in general, not necessarily specifically aerospace, but the companies start out relying on suppliers because there’s a knowledge gap. Additive is one of those processes that just has a million different variables and wrangling those down to the ground. and understanding them thoroughly takes a lot of time and a lot of investment. So, there are special suppliers who’ve done all of that groundwork and we find that in other industries, a lot of companies rely on them, especially initially when they’re first getting into Additive. And then maybe bring some of that in-house as they learn more about the process. I assume that aerospace is similar in that regard.
Dale Tutt: Yes, I would expect it to be the same way. One of the things that you would see some of the companies do is when you’re just in the prototyping phase, you’re printing parts, you might get those from a supplier, but then as you transition into production that you might buy the machines yourself. It really depends on how busy you think you can keep the machines. Ideally, you have a printing machine, you really want to keep it running most of the time to get the most return on your investment. So, I think that’s what goes into the trade-offs of when to adopt it as well as those cost trade-offs.
Ashley Eckhoff: I think we see that in other places as well.
Dale Tutt: Absolutely. I think it’s the same.
Ashley Eckhoff: How about software? We work for the software side of Siemens. Where does software play in the adoption of Additive Manufacturing for aerospace?
Dale Tutt: To me, it’s the key. If you’re really going to get the benefit out of, say, light weighing, out of these structures, the topology optimization and how you design and analyze the tools, and as well as building the ladderstructures into some of these areas; you’ve got to have good capable software that you can trust the results that you’re going to get. I think software plays a big part of it. I’ll give an example, this has, probably, been more than 20 years ago, and we evaluated some of this optimization software. And the parts it was producing, it didn’t represent what you could actually machine. So, it didn’t have the right constraints built into it that would accommodate how you would actually machine the part in five-axis machining. So, even though you could optimize for extremely lightweight parts, they weren’t buildable. So, the engineers and the manufacturing team really didn’t have a lot of confidence in the software, and we didn’t buy it. That was in the mid-’90s when we’re doing that. But now the software is much more capable and you can trust the software, and having proven software to design and analyze the parts is pretty critical. So, the design software, the simulation software, the analysis software, the ability to really have confidence and trust in it is pretty key to being adopted more quickly because people can trust the results that they’re getting from the software.
Ashley Eckhoff: How about certifiability of the process? Being able to trace apart from its initial design through the various stages of simulation manufacturing shop floor. I assume, in a highly regulated industry like aerospace, similar to what we see in medical that that would be important as well?
Dale Tutt: Absolutely, you have to be able to trace the parts all the way back to the material itself. So, having that traceability and being able to document it, understand how the part was built: what was the source of the materials? Did they comply to the material spec? It’s all very critical to the process. Especially, when you’re first going through that type certification process, you have to be able to show that what you said you are going to build in your design data is what you actually built. So, going through that process of that certification and knowing what the first article looks like fully complied, then even unless you move into production itself, you still have to have that paper trail throughout because you have to be able to validate that the parts are coming in, that are representative of what you certified in the original design. So, throughout the entire process, you have to have that traceability and it’s very, very critical for our customers to be able to show that. And that’s one of the nice things about Additive is that you can have a bit of that digital thread all the way throughout your process, and to be able to keep track of how the materials were made, and you have the process controls – it’s all right there – it’s heavily automated.
Ashley Eckhoff: I think you mentioned material science and quality, I assume those are things that are a part of that as well – being able to do your test coupons to make sure the material conforms and all those sorts of things as well.
Dale Tutt: Absolutely. It’s understanding and making sure that you’re producing the part, that you don’t have any voids in it, that you are getting the right mix of the materials. I think to be able to track, and know that you built the part and got the right part is pretty critical for all of these customers as they go through the certification process as well as the production process. So, understanding the materials, and understanding how your machine is operating, and did it produce the part accurately? Is part of that inspection process?
Ashley Eckhoff: We’ve talked a lot about the various ways that Additive was maybe being adopted, what are some hurdles that you see, some things we still have to get past here to aid Additive and its adoption across the aerospace?
Dale Tutt: The one that we talked about the most is obviously regulatory. As I said earlier, I think, as we’ve talked about it that you have a process that you need to go through, what most companies are seeing right now is that the part that they’re certifying is qualified to be produced on a certain machine, using under certain conditions, so it is very tightly controlled right now. And then if you want to build the part on another machine, you have to build a show that equivalency to what he originally certified. So, there certainly are regulatory hurdles but I would argue that they’re becoming pretty well understood. Obviously, the material science piece of it, and how they react within the 3D printing process, and the temperatures, and making sure that you’re getting the right mix of the material. But understanding one step back as things like fracture mechanics of a billet of aluminum, or a piece of sheet metal that you understand the material characteristics, as that part is in service.
So, understanding what kind of properties you’re getting with the part and over the life of an aircraft that maybe last 50 years that how is that part going to operate while it’s in service. So, understanding the materials science behind it, the strength, the durability, the fracture toughness of the material, all of that, that goes into it. And then we talked a little bit about the confidence and just having confidence in the tools that are used to design and analyze the parts but also just confidence in the parts as they come off that you have a mechanism to know that you got the part that you intended to get. So, when you do your inspections, when you do your review of the materials of the process to make sure that are operated within the control limits, all of that, I think, plays a part of the adoption of that. Some of this that we talked about, it’s not unlike what we’ve been through before within the aerospace and defense industry with the adoption of the composite materials because you had a lot of the same challenges that you needed to make sure that you follow the process, that you cured the parts at the right temperature and the right humidity levels, and that you had mechanisms to inspect those parts afterwards. And I think if you have all that in place, you can have a lot of confidence in the part.
Ashley Eckhoff: It seem like things to me that gets solved over time. So, it seems like it’s just time and work that we have here between us and full-scale adoption here. I’m sure you’re familiar with the Gartner Hype Cycle curve, where would you say that aerospace AM is on that curve? Have we gotten past the heightened expectations and disillusionment, are we close to turning it into a viable production technology in aerospace, where do you think we’re at?
Dale Tutt: I do think that we are close to turning it into viable production technology in aerospace, and we’re seeing a lot of evidence of that already. And it is somewhat dependent on the application, you’ve seen a lot of application of Additive being used in space applications, you’re also starting to see it used on commercial aircraft and on military aircraft, and not just on secondary structures but being evaluated on some pretty heavy-duty primary structures that I’ve seen. So, I would argue that companies are moving into that, I guess, it’s the slope of enlightenment. Obviously, there are some parts or people who maybe would say that we’re still entering the trough of disillusionment; I don’t know that I would call it that, I wouldn’t call it the trough of disillusionment.
For some of the things like primary structures, it’s more in reality, it’s the plateau of practicality that companies know that there’s going to be some regulatory difficulties to certify for some applications. As certainly for primary structure and critical systems, we mentioned the landing gear trunnion earlier, that’s a pretty critical system, and most companies use a forging for that today. But over time, it may be hard to find the business case to adopt the new technology right now. So, you’re looking at what does it take to certify a new process for those kinds of parts. And I think over time, the business case will be there, and they’ll do it. So, disillusionment, no; practicality, absolutely. I think that’s where we stand on a lot of these processes today.
Ashley Eckhoff: As the certification gets easier, as the process gets more understood, the ROI goes upright. So, you hit this inflection point where things become more possible than they were in the past because the path is easier. So, just to close things out here, we’ve talked about a lot of different things, but I’d like to like to step outside of Additive Manufacturing for a moment. Other than Additive Manufacturing, what are some some future technologies do you see becoming more important to the aerospace industry in the years ahead? What should our listeners be looking for, maybe, technology-wise to be rising importance there?
Dale Tutt: I think there are so many possibilities. When you look at the amount of innovation that’s out there right now, with air taxis, hundreds of companies work in air taxis; you see startup companies working supersonic aircraft; you see a lot of startup companies working in space. So, it’s going to drive innovation and technology. I do think that we’re going to see, especially with high speed and hypersonic applications, high-speed aircraft or hypersonic, you’re going to see more advanced materials technology. I wonder at what point in time, we’re going to see the elimination of flight control surfaces – return to the Wright brothers with wing warping, and I know that there are studies out there right now. But that’s interesting to me because it’s going to drive new materials, and it’s also going to drive new software and new electronics. So, it’s kind of a fun one to think about if you’re maybe thinking out there 20 or 30 years.
Ashley Eckhoff: That’ll drive the analysis guys crazyI’d imagine.
Dale Tutt: But the aerodynamic guys are going to love it because there are no gaps. We’re certainly going to see a lot more even in things like battery technology and zero emissions – it’s going to drive a lot of changes in our propulsion systems, and the electrical and software systems. So, there are a lot of fun stuff, a lot of really cool stuff going on in aerospace right now and I’m looking forward to it.
Ashley Eckhoff: You actually mentioned something there, I’d like to follow up on since you mentioned it. The environmental impact of air travel, and especially it is something that a lot of people are really looking at these days, and we didn’t really talk about the environmental aspects of aerospace, but maybe that’s another place where Additive can come into play. What do you think?
Dale Tutt: Probably in a couple of scenarios that when you think about machining parts on a large scale, it’s not uncommon to take 100-pound billet of material and you turn it into seven pounds of part. So, that means you have like 93 pounds of metal that has to be recycled. Along with that, you get cutting fluids and some other things that have to be dealt with. And companies are dealing with it quite successfully today, but I think when you when you start looking at Additive that you’re only using the material that you need, you reduce that overage of material quite significantly, I think, that’d be one of the areas where we can see some benefits from Additive. And certainly as airplanes just getting lighter, as airplanes get lighter, even if they’re still burning gas, if they’re still burning jet fuel; if it’s a little lighter aircraft, then you don’t need as much fuel to push it through the air. So, that’s a couple of different areas where I can see Additive having an immediate impact on the industry in that respect and how we’re making airplanes, and how much carbon we need to fly them.
Ashley Eckhoff: I would say even if we get to a future with electric aviation being mainstream that light weighing saves you the amount of battery you need, and those have heavy metals, they have weight over their own. Seems like it would be something worthwhile.
Dale Tutt: One other thing is that when you start looking at batteries and the packaging, the amount of batteries that you need; if you can start to optimize those packaging to mimic the shape of the vehicle that you’re putting them into, then you may have a more efficient battery design as well. So, there are definitely a lot of possibilities there.
Ashley Eckhoff: Well, thank you, Dale. I really appreciate you talking with us today. It’s been awesome.
Dale Tutt: You bet. I’m really pleased to be here today, and I enjoyed the conversation.
Ashley Eckhoff: So, that’s a wrap. I’d like to thank the Siemens Thought Leadership team for sponsoring our podcast, and I’d like to encourage all of you to subscribe to our podcast, to send us comments, and to look me up on LinkedIn if you have any questions about anything you’ve heard here today.
In our next episode we will be finishing up our discussions of additive manufacturing in the aerospace industry as we talk with our friends at Sintavia.
As always, we appreciate you joining us. You’ve been listening to the Siemens Industry Software additive manufacturing podcast, my name is Ashley Eckhoff, and we look forward to seeing you next time.
Siemens Digital Industries Software is driving transformation to enable a digital enterprise where engineering, manufacturing and electronics design meet tomorrow.
Xcelerator, the comprehensive and integrated portfolio of software and services from Siemens Digital Industries Software, helps companies of all sizes create and leverage a comprehensive digital twin that provides organizations with new insights, opportunities and levels of automation to drive innovation.
For more information on Siemens Digital Industries Software products and services, visit siemens.com/software or follow us on LinkedIn, Twitter, Facebook and Instagram.
Siemens Digital Industries Software – Where today meets tomorrow
Related links:
AM podcast01
AM Podcast02