Podcast transcript: Intelligent performance engineering (Part 4) – closed-loop validation
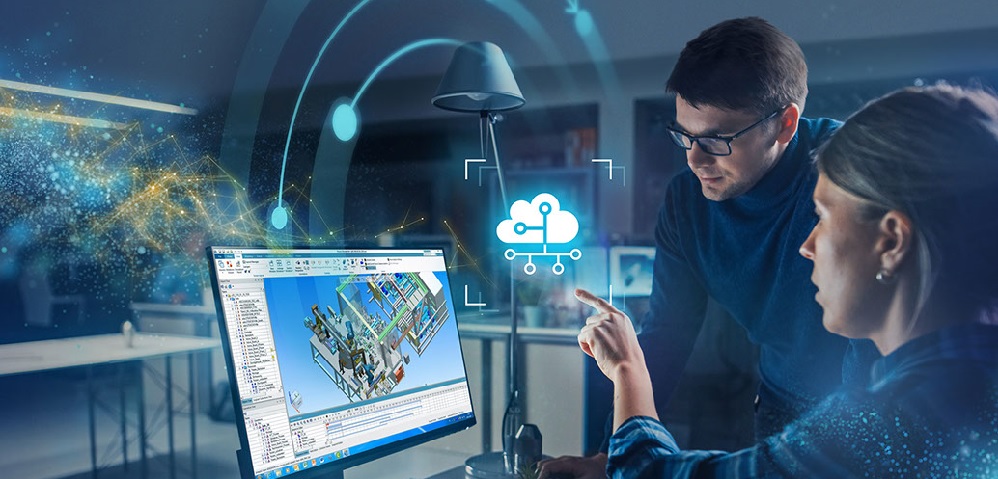
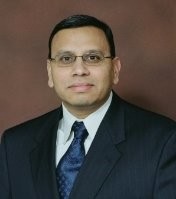
The machinery industry requires equipment manufacturers to address the dynamic challenges in response to an increasing demand for customization in manufacturing to produce personalized and differentiated customer products. This last podcast in the series discusses closed-loop validation which allows machine builders to validate their simulation by capturing and testing the relationship between their requirements virtually.
Read the transcript listed below or listen to the audio.
Read the transcript
Below is a transcript of the final Intelligent Performance Engineering podcast series, describing innovative solutions for modern, complex machines with experts Rahul Garg and Giulio Camauli.
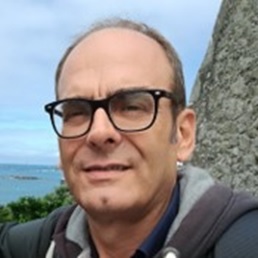
Bill Butcher: Welcome to Siemens Digital Industries Software podcast series on Intelligent Performance Engineering, brought to you by the Siemens Thought Leadership team. As we’ve learned throughout this podcast series, industrial machinery manufacturers are seeing an increase in complexity associated with the flexibility needed to respond quickly to consumer demands. During this podcast series, we’ve been discussing how machine builders can leverage the Intelligent Performance Engineering solution as one way to address this complexity and increase flexibility.
In this fourth and final podcast of the series, we’re discussing another differentiating theme of the Intelligent Performance Engineering solution: Closed-loop validation. Closed-loop validation allows the machine builders to validate their simulation by capturing and testing the relationship between their requirements virtually. Throughout this series, we’ve been fortunate to have Rahul Garg and Giulio Camauli with us. They are also joining us in our today. And as you may recall, Rahul is the Industry Leader for the Industrial Machinery Industry, and Giulio Camauli is the Industrial Machinery Industry Leader for the Simulation and Test Solutions within Siemens Digital Industries. Gentlemen, thank you, and welcome again!
In the first three podcasts, we talked about the evolution of technology within the machinery industry and the key trends that continue to shape the industry today. We also introduced the Intelligent Performance Engineering solution at a high level where you guys both discussed the three key differentiators: Multiphysics simulation, integrated design and simulation and closed-loop validation. In our last two sessions, we took a deep dive into multiphysics simulation and integrated design and simulation. In this session, I’d like to close out our discussion on the differentiators for the Intelligent Performance Engineering solution, as we take a deeper dive into closed-loop validation and why this is important. Let’s have that be our first question, Rahul. What exactly is closed-loop validation and why should it be important for machine builders and their suppliers?
Rahul Garg: Thanks, Bill. This is probably one of the most exciting aspects of what we are trying to help our customers with – this whole concept of closed-loop validation. So, when you look at how simulation is done, one of the things that happens during that whole process is there is a simplification of reality to ensure that you can at least get the simulation context done. And, as part of that whole simplification process that happens is you miss out on the true criteria and the true environments under which the machine could be working. So, to make sure you do not miss out on any of those assumptions, you can’t oversimplify your design and offering requirements. It’s critical that you’re able to test and validate your machines in the real environment. And that’s where the closed-loop validation process comes in. With intense scrutiny of how the machine is performing, you can get a real sense of how it is meeting the customer’s needs. From production rates, from scrap, from noise, from vibration, you can get real-time feedback and then you can correlate that to your simulation environment. What this allows you to do is to make sure that your simulation models are accurate and you’re able to address even potential issues before they come out on the field, and you will be able to evaluate how your machine is performing on an ongoing basis. And this really helps you evolve your machines to the next generation in a very rapid manner.
Bill Butcher: You mentioned the excitement that you have around this topic, which I think is fantastic. And I think for machine builders or machine manufacturers it might be a little daunting, right? I mean, they’re hearing about connectivity; how do I do that? What does that mean for me and my processes? So, what current challenges are machine builders facing around the topics of data connectivity and test-based validation today?
Rahul Garg: So, when we think about the issues around data connectivity and test-based validation – getting your machines harnessed and wired out with the appropriate sensors through your design and simulation processes is one aspect of it. You can obtain the necessary information from the real operation of the machine with the right connectivity using 4G and 5G connections. The bigger issue that comes about is from a business perspective – the end-customer who’s using the machine may not be too keen to share the data that is coming out of the usage of the machine. So, those are some complexities from a business perspective. As part of that process, your ability to work, obviously, with your end-customer so that they can also realize the benefit of sharing that data with you, obviously becomes critical. There are many more ways to do that test-based validation. Giulio, perhaps you want to comment on that?
Giulio Camauli: Yes. It is very important that you can measure it from the field. So, the real usage information is fundamental for many different reasons. Knowing how the machine is used can help the designer to improve the product, but it also gives an important help to the end-user because knowing the real usage of the machine allow you to anticipate maintenance before going into a critical downtime issue. The digital twin is also very important and can bring value at this level. Just combining test and simulation, you can acquire several channels through physical testing and physical points – it measures acceleration forces, temperature, noise, whatever – but sometimes it’s not so easy to instrument your machine. So, you can integrate and complement the physical measurement with virtual measurement that comes from virtual sensors. Therefore, having the digital twin of the machine, you can virtually acquire data from your model in sync with your real measurement. That’s a big advantage of sharing the information between test environment and simulation model. Having that ability to import your simulation model into the test environment makes it very easy to have a huge set of information synchronized, and verify the real condition combining measurement with animation, videos and sound – and all will be reliant.
Bill Butcher: So Giulio, taking that a little bit further, how can Intelligent Performance Engineering solve some of the challenges that machine builders are facing, specifically in the context of validating machine simulations and the relationships between these machine requirements?
Giulio Camauli: You know, starting from requirements, that’s interesting because sometimes you have in mind a competitive solution as a market target. But how can you verify the performance of that machine when you don’t have the design and you don’t have the simulation model? The only thing you can do is to measure performance. Imagine that you want to reach a noise level that you prefer in your competitor’s product. You can measure those values and use those measurements in your simulation model to verify which solution needs to apply to your design to reach that objective. That’s the first use of test to help simulation. Another easy mechanism where test can help simulation is when you want to verify the realism of your simulation model. So, simulation is fine, and is saving a lot of time and cost. But, of course, an error in simulation can bring much damage. Therefore, sometimes you need to do some measurement. You don’t need the complete prototype – but maybe you can use a measurement that you already have from a predecessor or measure just a part or a mechanism to verify if the simulation model is representing the reality. Then, consider again a combination of test and simulation. If you need to certify your product against a standard – acoustic or vibrational – it is very important. Of course, in this condition, you can’t avoid the prototype. The certification needs to be performed on a physical object. But, if you have a digital twin of your product, you can simulate and pre-assess, and de-risk your final acceptance test working on the numerical model. Then you can pass the certification immediately, the first time that you go there. It is a damage if you will not pass the certification and you have to restart from design to apply modification, to correct the problem. So, it’s much better to de-risk that upfront on the simulation model and go to the certification phase in a smoother way.
Bill Butcher: I want to quickly go back to something that you mentioned earlier, in capturing real-time data from the field to help validate the virtual simulation. You mentioned service opportunities. Can you expand that a bit further for our listeners? And how does this happen exactly? Why is it so important for machine builders?
Giulio Camauli: The connection between the simulation model and the machine in the real-life condition has two important effects. Firstly, is that measuring the behavior of the machine when it is used by the the end-user – it brings a lot of value to the design and manufacturing process. So, having the ability to collect data in a centralized and safe environment brings much information to use as an input for the digital twin that predicts various conditions under those real loads and real missions. So, you can verify how the mission is evolving and how the machine is behaving in order to plan your maintenance, thus avoiding the critical condition of an unexpected problem or a downtime situation. But I started from the end. It is also important if we consider that having this digital twin is also very important when you deliver the machine on-site to your customer, and need to commission it. The objective is to get acceptance as quickly as possible, without any problem. You achieve this by anticipating the verification and the optimization process of your PLC code for the automation of the machine. By working with real PLC, the physical controllers apply on the digital twin of the machine. This is nice because you can then improve your code having in mind the objective – for example, energy efficiency, while you increase the throughput rate. And when you go inside, the commissioning supported by the virtual commissioning will be much easier.
Rahul Garg: The whole concept of bringing in the simulation and test environment takes it to the next level in thinking how to make your machines more adaptable, right? So, as you’re getting the real feed from your machine performance, by applying that against the different simulation environments, you determine if any changes are necessary to the actual performing and usage of the machine. So that’s where the adaptable nature of this whole concept comes in – by running this one motor at 100 RPM, you’re getting some throughput issues; perhaps you could use that information to adapt it. You can say, “You know what? If we were to run it at 70 RPM, we will still get the same throughput, and it will not have an impact on the overall performance of the machine and will not run into any heat issues at least at the moment.” So that’s where the adaptability of being able to obviously address any issues in real-time come in. Therefore, it’s not merely issue resolution but improving things as they go. I think that’s the other very interesting part of closed-loop validation.
Giulio Camauli: Another point, is when you try to improve the throughput speed that is the typical requirement from the customers, and they expect you to maintain or exceed the accuracy. When you increase the speed, the typical problem is that the machine will start vibrating. Speed generates vibration, vibration means less accuracy. So, the capability to predict all those behaviors in the simulation model while having proof of the reality with physical information from the field is very helpful.
Bill Butcher: Rahul and Giulio, I can’t thank you enough for spending the time with us discussing the unique value delivered through the Intelligent Performance Engineering solution. Throughout this series, we covered a lot of topics and you guys delivered incredible insights into the challenges and trends that are driving the machinery industry today. And before we end the podcast series, Rahul, I have have just a couple more questions for you. From your perspective, could you quickly summarize what are the main advantages for the machinery industry to embrace this digitalization topic?
Rahul Garg: There are a few key important things that come out. The first one, for Intelligent Performance Engineering, is you’re making your engineering a lot more efficient, easier and faster to get your products out the door. That is number one. Number two, you’re reducing your risks by being able to test and evaluate and determine all scenarios. The more you can do, the more you can test them, and the smaller the risks that you may encounter in the field. Thirdly, is you have a managed environment, which helps speed up the process to serve the demanding customer needs of multiple configurations, multiple changes, and responding quickly to those needs. To me, those are the three big advantages that one can see by embracing Intelligent Performance Engineering.
Bill Butcher: One last question before I let you go. If I’m a machine manufacturer today, why do you feel it’s critical that I evaluate the solution we’ve been discussing? You know, why should the Intelligent Performance Engineering solution be considered?
Rahul Garg: The whole idea behind Intelligent Performance Engineering is summarized in three key areas. Firstly, multiphysics simulations. In the real world there are many different issues that are faced by the equipment. Being able to evaluate and test all those various situations simultaneously under one umbrella becomes very critical – from thermal analysis to fluid analysis, to vibration analysis and electromagnetic interferences. All these will keep rising, right? So, being able to do that simultaneously makes it much easier. So that’s the multiphysics simulation. Secondly, is the Integrated Design and Simulation where you have one environment to bring your designers, simulation experts and suppliers together into the whole process. Therefore, there’s the ability to quickly respond to customer changes, needs and to varying configuration needs by allowing testing, designing and evaluating iterations faster. Thirdly, is the closed-loop validation. You are able to bring real-life situations into your design engineering environment. This is where the industry is going to turn the corner in a big way where you can bring in that real-life information and use that to help address customer issues when they’re using the machine and to improve the overall performance, design and capabilities of the next-generation machine. So those are the three key areas I think are very important for customers to consider to help improve their engineering processes and take them to the next level.
Bill Butcher: And I think it’s becoming clear that manufacturers are looking for help to address the problems we talked about. You listed three great examples of how to do that. Gentlemen, thank you again. It’s been a pleasure to speak with both of you throughout this series on Intelligent Performance Engineering. You know, we highlighted the positive effects of the solution for the machinery industry but we also gained some really valuable insights from your experiences. So, I’d like to say thank you again very much for taking the time. We look forward to hearing your contributions in an additional podcast series coming very soon. Thank you, everyone!
Siemens Digital Industries Software drives the transformation to enable a digital enterprise where engineering, manufacturing and electronics design meet tomorrow.
Xcelerator, the comprehensive and integrated portfolio of software and services from Siemens Digital Industries Software, helps companies of all sizes create and leverage a comprehensive digital twin that provides organizations with new insights, opportunities and automation levels to drive innovation.
Listen to podcast01, podcast02 and podcast03 from this series.
Also, for more information on Siemens Digital Industries Software products and services, visit siemens.com/software or follow us on LinkedIn, Twitter, Facebook and Instagram.
Siemens Digital Industries Software – where today meets tomorrow.
About our experts:
Giulio Camauli – Simcenter Industry Solutions Manager at Siemens Digital Industries Software. Giulio has been with Siemens almost 30 years, covering many roles from application engineer for test solutions, to customer services manager responsible for strategic initiatives dealing with several key-customers in the Italian market. In his current role he contributes to the Industry campaigns and strongly collaborates with the different Simcenter sub-segments, marketing and regions to define broad and balanced Simcenter messaging and promotion.
Rahul Garg is the Vice President for Industrial Machinery & SMB Program, responsible for defining and delivering key strategic initiatives and solutions and global business development. He and his team are responsible for identifying key initiatives and developing solutions for the industry while working closely with industry leading customers and providing thought leadership on new and emerging issues faced by the machinery industry. Rahul’s experience and insight are derived from 25 year career delivering software-based solutions for product engineering and manufacturing innovation for the global manufacturing industry, spanning a career in R&D to program management, sales and P&L management and having focused exclusively on the industrial machinery and heavy equipment industry since 2007.