AVs demand closed-loop engineering – IESF Auto recap part 2
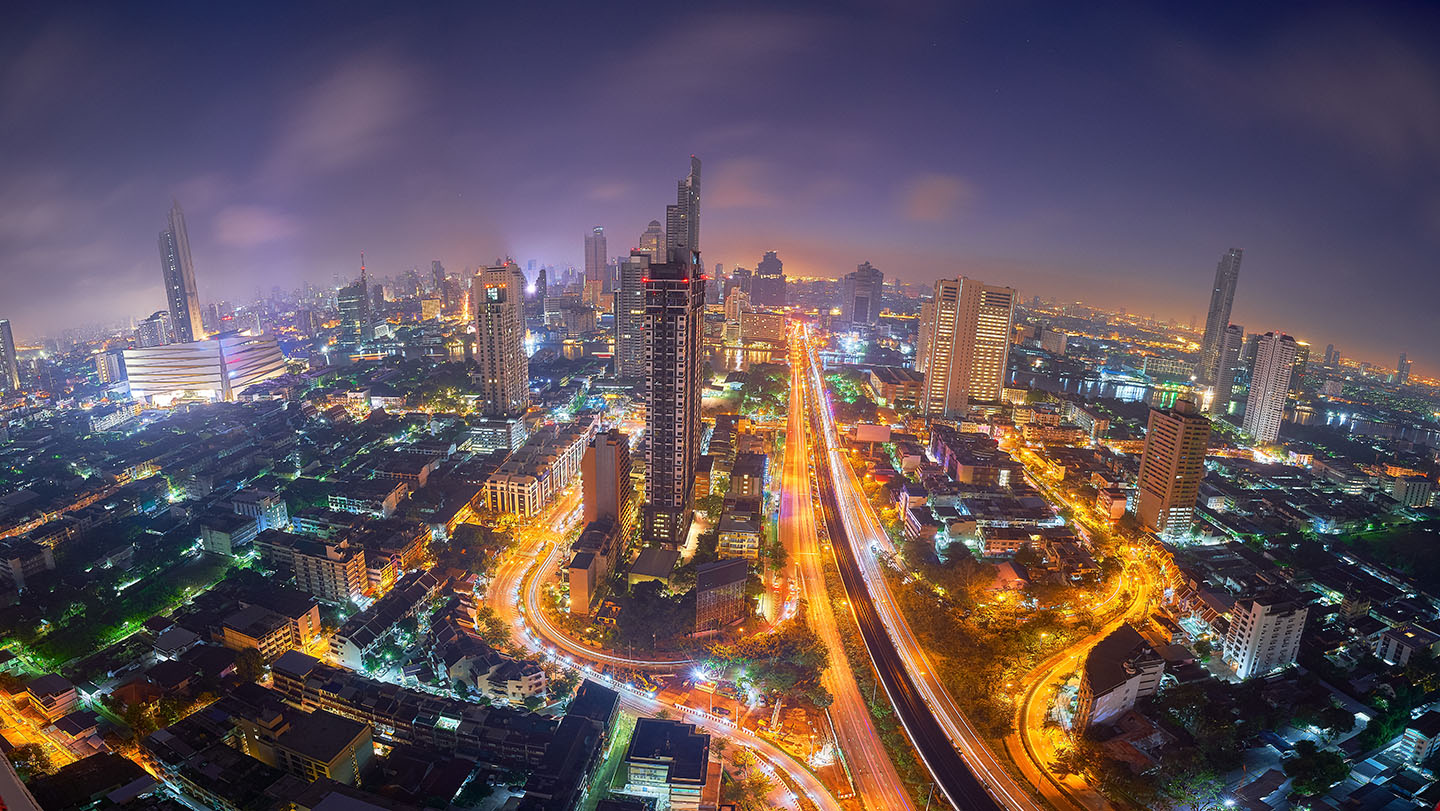
In the next part of our recap of IESF Auto 2020, I’ll take a look at a fascinating session lead by Matthieu Worm, Director Autonomous Vehicles Simulation and Test Solutions at Siemens Digital Industries Software, on how closed-loop solutions will be critical to the future of AV development.
Worm began the session by outlining a critical challenge in today’s automotive industry. Modern urban landscapes are practically overflowing with vehicles. Continued urban population growth has contributed to high levels of congestion in city centers. This is an unsustainable trend. Increasing congestion prevents steady traffic flow and contributes to greater emission of pollutants in city centers. Worm contends that we need urban environments that are less congested, more sustainable and more efficient as more people choose to live in or near large cities.
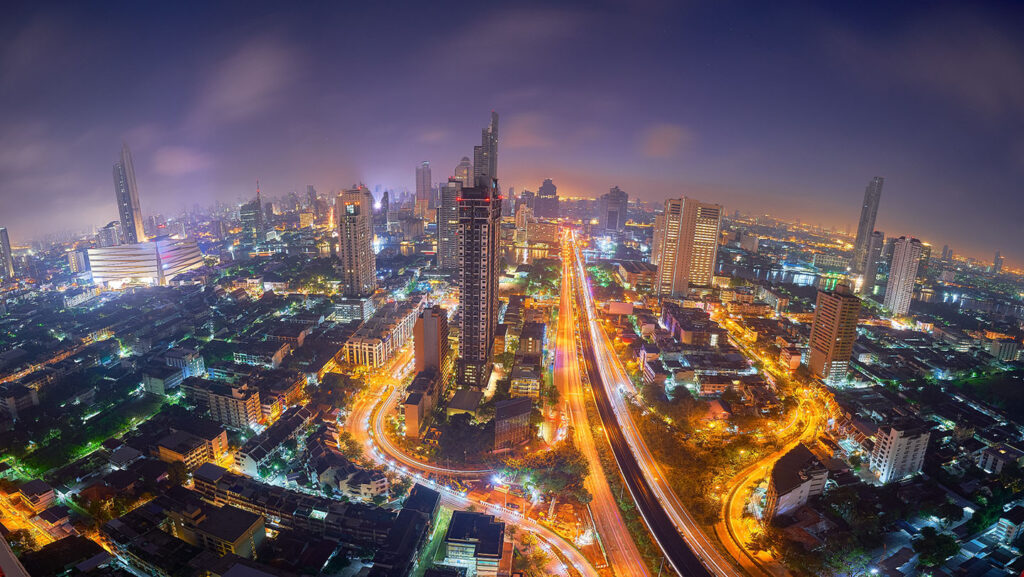
Fortunately, autonomous vehicle (AV) technologies offer a potential solution. Modern cars march closer to being ‘computers on wheels’ with each year. Electrical and electronic (E/E) content, network signals, and software lines of code (SLOC) have increased consistently over the last decade to support greater levels of vehicle automation. In addition, automotive OEMs have started investing in more high technologies including integrated circuits (ICs) and systems-on-chip (SoCs) devices to improve the on-board computational power of vehicles. For many, this investment has included new partnerships with high tech companies that specialize in certain aspects of AV development.
Such partnerships make sense because AVs are systems-of-systems. Each sub-system is highly complex and requires specific knowledge for proper implementation. AVs require cutting-edge silicon chips, sensors, electrical wiring, artificial intelligence and more. At the next level, the vehicle must be able to connect with a larger ecosystem of other vehicles and smart infrastructure systems. Each of these areas has specific challenges and requires specialized domain knowledge. AV manufacturers must then integrate these various sub-systems into a unified vehicle and verify and validate the overall system to ensure its safety and reliability. In fact, it is the verification and validation of these systems that is expected to prove the greatest challenge. Experts predict that AV systems will require the equivalent of billions of miles of testing to ensure their safety. As a result, it is clear that real-world testing alone will not suffice. AV manufacturers will need to adopt a combined simulation, emulation and real-world testing approach.
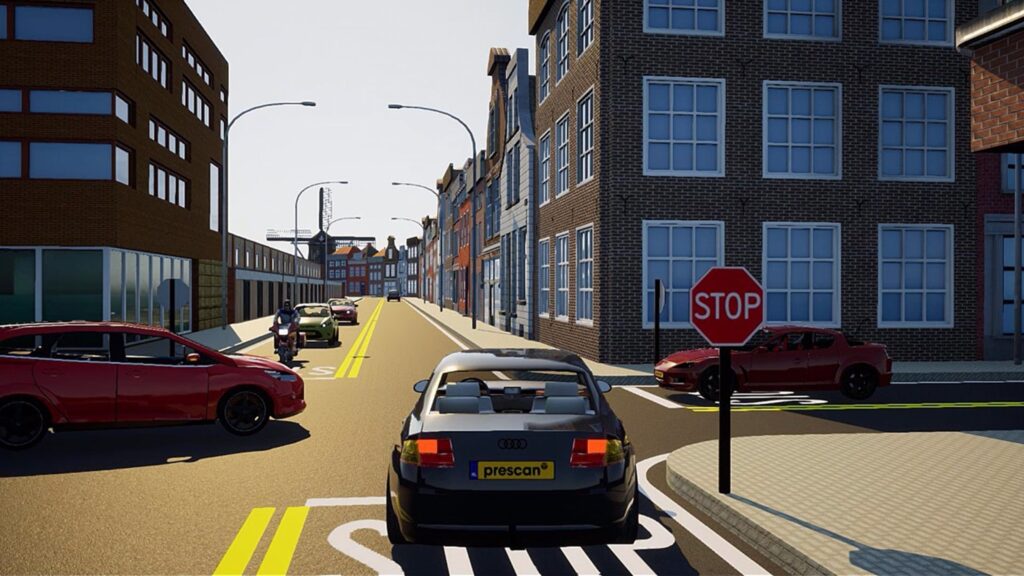
But, what would such a hybrid approach look like? AV manufacturers will need to integrate massive simulation of vehicle dynamics, traffic conditions, weather and more with real-world testing. Such integration must go beyond combining the results of simulated and real testing. It is critical to establish a closed-loop connecting vehicle development and testing in both virtual and real-world settings. Today, raw sensor data can be captured from test vehicles and combined with simulated data to train neural networks, identify corner cases and improve the fidelity of the simulations. Furthermore, it is important to understand the vehicle as part of a larger transportation system. As a result, AV simulations must capture realistic transportation systems and be able to evaluate the vehicle as part of that system.
Many engineering software companies are now able to support a few of these capabilities. Siemens Digital Industries Software, on the other hand, offers solutions through its Xcelerator portfolio that cover the entire AV lifecycle, from chip design and testing to the integration in city environments. These solutions offer AV manufacturers the ability to establish a closed-loop, multi-attribute functional twin of the vehicle and its environment. With such a digital twin, companies can capture and monitor real-world sensor data, analyze and diagnose critical scenarios, perform physics-based sensor modeling, complete massive simulations and physical vehicle validation, and connect all of these processes with a robust data backbone that is open, secure and provides traceability.
To learn more about Siemens’ chip-to-city solutions, watch Matthieu Worm’s full presentation from IESF Auto 2020. Or, check out these blogposts from Matthieu: