What digital tools can make supporting airworthiness easier?
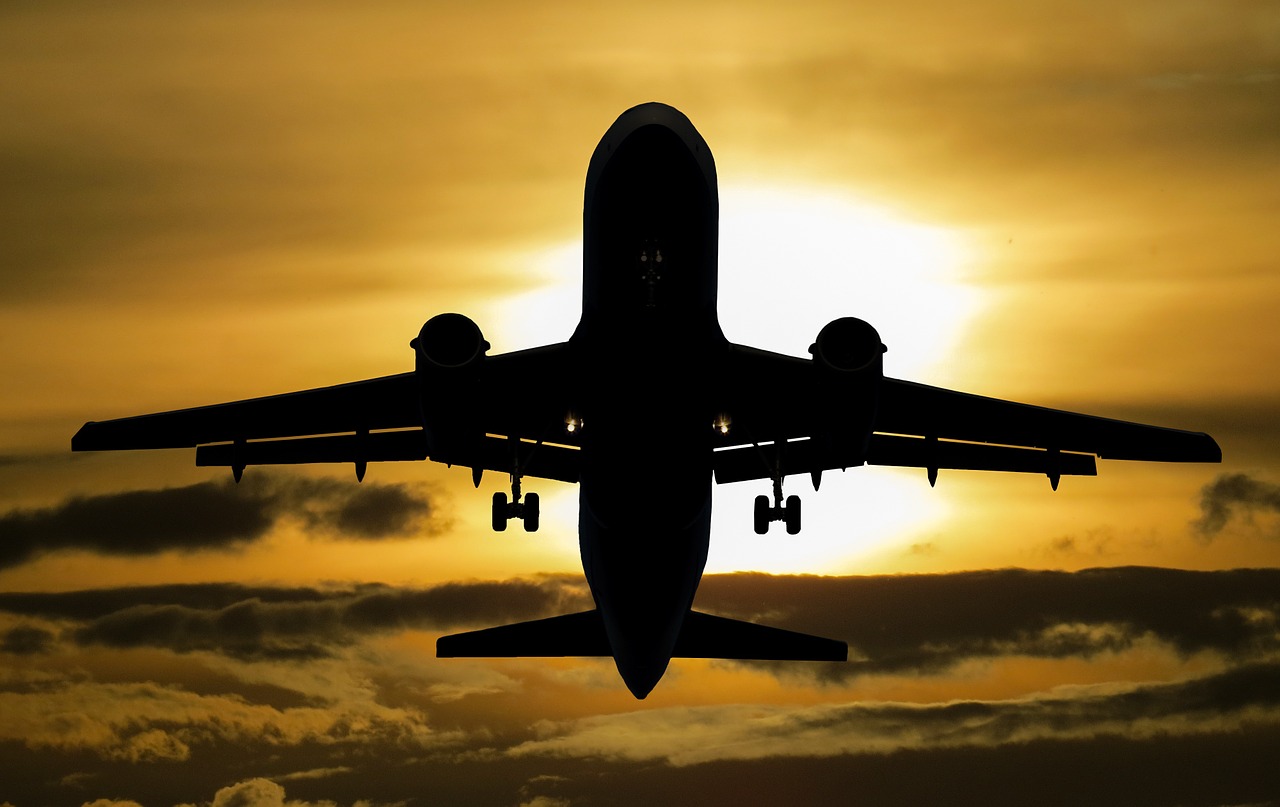
By: David Chan and John Cunneen
As airworthiness certification increases in complexity and more laws and regulations create a greater need to adopt a digital program management strategy, companies must find the right tools to make the process easier, cheaper and more reliable.
In our previous blog regarding airworthiness certification, we discussed the difficulty in proving airworthiness, the methods available to make the job easier and the benefits of using digital certification management.
Listen to the Podcast Episode Now
Here, we will touch on what going to an integrated digital program management system means, how it can support airworthiness and what implementing these strategies mean for the future of certification, including electric and autonomous aircraft.
What does integrated digital program management mean?
An integrated digital program management strategy allows a company to proactively approach every phase, from development through delivery, with the artifacts of compliance to prove airworthiness. Instead of the daunting task of collecting countless documents and signed-off designs at the end of the production process, an integrated digital program management system should include airworthiness certification within the entire process, not a separate part of the process.
For the aerospace industry, the costs associated with certification continue increasing to the point where they equal or exceed development costs. If almost half of the cost of development and production program is validating the product’s safety and reliability, companies will need a comprehensive integrated digital program management system to reduce costs and remain competitive – pieces of paper in a file in someone’s desk simply doesn’t cut it anymore, especially as it will be multiple desks across multiple company and supplier sites.
While it is difficult enough even if all goes according to plan, problems in engineering production, and all through the process, will occur. When and if they impact safety, the effects can be minimized. Amid the safety concerns and headaches associated with having to ground a fleet, companies and investigators can leverage the digital thread of the certification process to look back to see how it met requirements. The digital thread makes it easier to determine who made the effected parts and if they were analyzed and signed off correctly; the certification data is readily available.
Finally, an integrated digital program management system allows a manufacturer to think of its long-term viability and tracking how to keep an airplane in the air. Whether it’s the manufacturer maintaining the aircraft or the owner/operator, they must know how to realistically maintain it for decades as their supply chain will certainly change.
Digitalization and documentation
Compiling technical documents by searching files and tracking down engineers and designers can eat up tens of thousands of work hours, driving up costs and delaying product release or maintenance of revised parts. Integrated digital management ensures that the searching and traceability in reporting is tailored to the airworthiness community so technical publications, parts lists, assembly and maintenance instructions and all products that go out to the field for regular service or major repairs remain up-to-date.
Many times, aircraft manufacturers and maintainers have the ability to substitute original hardware items or “standard parts” when availability fluctuates. Manufacturers familiar with these types of substitutions typically will develop lists of acceptable alternative parts. However, if not published correctly in the service publications or parts catalog, it may cause confusion in the field; a mechanic may try to locate an exact replacement part while an alternate may be more readily available. This substitute part may even be of equal or higher quality because standards change or availability fluctuates. Having this information is important to reduce downtime, ensure safety and lower the total cost of ownership.
In certification, it’s not just one kind of data type: it’s multiple data types. It’s crucial to keep track of the original manufacturing plans, specs, drawings, materials and standard hardware as repairs and maintenance parts may not be in the original design. The number of variants can become daunting as the use of a non-original part alters what can be used going forward. Integrated digital management keeps the latest iterations and changes available and allows rotating crews over decades of managing the care of an aircraft to ensure the right parts align with the parts currently in use.
The aftermarket aspect can be expensive. Owners and operators have a whole supply chain that supports maintenance, but what happens when a supplier is out of business and not making the parts that need to be replaced? How do you get the specs or reuse what you have?
It’s not uncommon for companies and military depots to spend thousands, sometimes millions of dollars, delivering repair parts only to find it doesn’t work, and then spend more money trying to reverse engineer it while the aircraft remains out of service. Also, some structural parts on planes being flown above their expected life limits weren’t designed to be interchangeable and are never meant to be replaced at all.
Bottom line: you’ve got to keep all of this straight. Over time, the OEMs and those operating the aircraft change so it’s important to have all this information at your fingertips because access to that knowledge is what keeps the asset in the air.

Supporting airworthiness
One step of streamlining the airworthiness certification is implementing integrated program planning (IPP), which allows manufacturers to fulfill requirements and define, plan and schedule numerous work breakdown structures.
IPP is about organizing the work breakdown structure. For instance, if you design a wing, what are the processes of designing and building it? What are the requirements? What kind of tests will need to be conducted or have been conducted? IPP can help link back to the specifications of the end customer and the governing airworthiness authority. It ensures those in the entire product lifecycle are checking off the steps and satisfying the requirements, which may include tests and simulations, manufacturing, inspection, usability, documentation and maintenance.
This integrated digitalized level of planning brings all jobs together, breaking down silos and reducing the need to search for information, all of which leads to a fully comprehensive environment that can be used to prove airworthiness.
Conclusion
Integrated digital program management is both a tool and a process. You may have the best tool in the world, but if applied with bad disciplines or processes, it doesn’t work. Manufacturers are using digital tools when designing and building aircraft; they’re just not using the software for airworthiness.
Integrated digital program management will also aid the potential resurgence of small-to-midsized aircraft. Electric powered aircraft are currently emerging. Right now, designers continue pushing the limits into electric aircraft by reducing emissions, extending range and power density of batteries, and significantly reducing the cost of operation.
Siemens is leading the way in our development of the eAircraft family of engines. These types of new aircraft have the potential to revolutionize the aircraft market and perhaps the aerospace industry. However, manufacturers will need the benefits of integrated program management more than ever to manage their certification programs, because the rules for these new airplanes are currently being developed and will need to be done in tight collaboration with the regulatory agencies.
Manufacturers will need the best and most comprehensive tools to demonstrate that they have covered all the requirements for these new types of aircraft. Integrated digitalization program management is the key to the future success of the aviation community.
Learn more about this topic by reading two Siemens white papers: “Analysis and simulation in aircraft structure certification.” and “Digital certification management.”
Watch the webinar: “Accelerated aircraft certification through verification management.”
To continue reading our series on airworthiness, click here to read why the aerospace industry must adopt condition-based maintenance.
About the authors
Dave Chan is a technical account manager supporting the aerospace, defense and federal business for Siemens PLM Software. His career with Siemens PLM Software started in 1996, and he has driven customer success with the adoption of digitalization and digital engineering solutions for numerous commercial and federal customers. Dave has been in the engineering software business for more than 22 years. He has a bachelor’s degree in industrial engineering degree from Lehigh University.
John Cunneen is a business development consultant for Siemens PLM Software’s Aerospace, Defense, Federal, and Marine division. He leads efforts to uncover, develop, and respond to industry and government requirements pertaining to all aspects of product and system lifecycle management and provides thought leadership to customers. John has been an avid general aviation pilot since 1987, earned a Bachelor of Science in aerospace engineering from Arizona State University in 1989, and has been a key part of Siemens PLM Software since 1999.