Implementing smart manufacturing for parts manufacturing
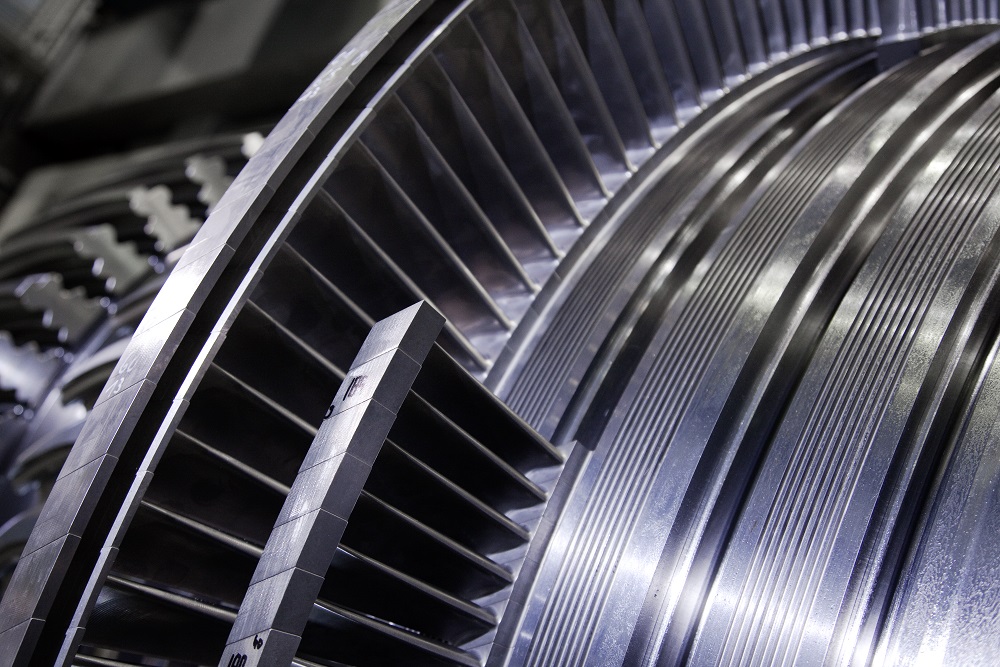
Industrial machinery in manufacturing is witnessing dynamic technological advancements. It is a significant task to manage a new wave of advanced manufacturing and assembly operations for achieving stellar quality while optimizing cost.
In a transcription of our third podcast of a smart manufacturing series, we are learning how machine manufacturers are implementing smart manufacturing to improve the product of parts manufacturing. We will highlight the advantages that smart manufacturing brings to industrial machinery manufacturers.
Also, we’ll take a close inspection of the improvements smart manufacturing brings to manufacturing execution management, including the Manufacturing Bill of Process and Manufacturing Bill of Materials.
We welcome again our expert in this series, Bill Davis, who has over 30 years’ experience in the industry, and 20 years as an engineer, and is currently the Director of Industrial Machinery and Heavy Equipment Solutions at Siemens.
Below, is the transcription from our third audio podcast on smart manufacturing, sponsored by Siemens Thought Leadership team. For the full audio podcasts or blog series, refer to the links at the bottom of the page.
Blake: Siemens obviously has a very comprehensive approach to smart manufacturing. So, when you look at the greater global Siemens and their approach to smart manufacturing, could you give some of the things we have learned in our approach, and how that’s changed as it has been a dynamic process of learning and improving. What is our general philosophy in approaching smart manufacturing?
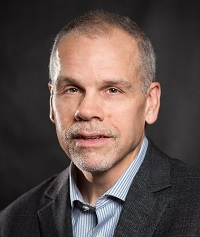
Bill: At Siemens AG, and the PL side of our business, we have a combined approach. We learn from each other and execute our software solution to tell us exactly how it works and how it doesn’t work for them. So, by having that feedback loop, we can do things that are forward-looking. Our own Siemens PL tends to be a little bit conservative, but our manufacturers are always looking for ways to take advantage of the next big thing. So, it kind of pulls us in that direction for how we can provide and be forward-thinking when it comes to the manufacturing execution. Companies are trying to squeeze every ounce of profit out of the manufacturing process. There are not many the size of Siemens with both the manufacturing capability and an industry breadth of knowledge.
We’re able to show our capabilities in various industries, in different ways, and they are supported by what is executing in the factory at Siemens. Therefore, we sell to ourselves well.
There are different scales from a volume perspective when you’re building PLCs, HMIs or motor controllers, so you’ve got enormous volume. Therefore, every ounce of weight and every second that is spent in dwell time is an opportunity for saving money. So, by being able to have an operations control management execution or manufacturing execution management tool that lets me get down to that fine-grained analysis level helps me drive value into the manufacturing process.
It is essential when we begin talking about the low volume of highly complex operations, to realize we have unique manufactured order machinery and the correlation between each one of the variants of the machinery. The common thread is being able to look at how the assembly is orchestrated in a fine-grain manner to feed that information back into the engineering space and provide a closed-loop continuous improvement. That’s a lesson learned from our relationship with our Siemens AG partners.
Another piece of the competitive advantage of manufacturing execution management is that we know the Bill of Process. It’s basically the recipe for building a machine. It’s not necessarily the components that we’re building, but the methodology used to construct each part and roll that into parts manufacturing assembly where it’s optimized. As a result, we get a picture of what can be imported into the schedule because we have all the assembly setups necessary to create it.
Also, it’s crucial to have the ability within our data management products to pull apart the bill of material and reconfigure it to fit the manufacturing operation more effectively. The grouping of parts in assembly necessary for manufacturing the parts, common part requirements or assembly of the machine in a different order than the engineering bill are essential.
Historically, there’s a delicate balance between engineering and manufacturing and a throw-it-over-the-wall mentality. We leverage the capability with manufacturing execution and still retain the connection back to the engineering bill of materials, eliminating the conflict and allowing the manufacturing side to customize how they want to view the bill of materials. The result is a more efficient operation management process.
The bill of process can also build in quality steps to drive the operation of the process and product. One of the challenges in a machinery build operation is how to ensure that the bolts needed for assembly are correctly torqued. The quality control measure was to have the assembler accountable to indicate what bolt to tighten by a paint marker, though not scientific, it held the person accountable. Therefore, now with many advanced tools, we can take the torque measurement off the torque wrench and bring it back into the manufacturing quality process. This is another example of value delivered from smart manufacturing which reinforces the quality delivery of the machine.
When you start putting these various pieces together, Siemens is the only solution provider that has the end-to-end solution, from manufacturing, design, service and back into the business system.
Blake: When you spoke of quality, and building the highest quality parts for the lowest amount of labor content in the fastest time, what are the differentiators that Siemens provides in parts manufacturing? Also, what kind of technology are we inputting to make sure that happens?
Bill: From a parts manufacturing perspective, most parts require several different machining operations to perform. You know what the finished piece looks like and build quality. So, you need to ensure that you have a process that’s capable of meeting the quality requirements. Seldom considered is the software for any given part that’s machined, or fabricated in any manner, which must accommodate the conditions of the machine shop or manager.
There are four to five different types of machining centers that are involved and possible to create the part. We need to guarantee that each one of these processes – the CNC code and the CMM data traceability – can take that information that we’ve qualified for each one of those methods. Once we begin to lay across that part in the shop, the best way to make it is putting it on machining center one and have it do everything. This is a more complex machine, which is required to have the flexibility in the process to place it on various machining centers to meet the timing and sequence schedule.
Therefore, it’s vital for the part manufacturing operations to trace and track the optimal manner to create the part and other options, so there is no reinventing the wheel every time there’s a scheduling conflict. Also, in the process of making the part and extending it out, there’s the capability of being able to extend our factory into the supply chain partners. So, we know that a part goes out for heat treating and plating, and we need to extend that manufacturing process and manage it through the shop to include them as part of the operations management. Therefore, there needs to be a toolset that takes the manufacturing of the part and entire operations for part execution.
Another crucial factor in making the part is the critical components in scheduling and the tools that fit into the machine. You need to be able to trace these machining components and tooling so that it becomes part of the schedule. This adds another level of complexity to the entire process if the tool is being allocated to a different machine to make a different part. When I need it to be doing something else for the part that I’m introducing, I must have another way of making it with another tool. Therefore, it’s important that the processes and software solutions allow us to manage the machining center, visualize the workflow and trace it to the specific CNC code and tools required to manufacture it. All of these are connected to the part manufacturing bill of process.
There are trends discussed with respect to part manufacturing and how to take advantage of it. Additive manufacturing is an investment that part manufacturers, as well as machine builders, can take advantage of in the design space; however, this an investment in new hardware, new machining centers that have additive and machining capabilities or additive and subtractive capabilities. So, the CAM programs and files you send to the machining centers are important to the software that you’re building – CAM software, design software – to have the ability to handle those different technologies. Siemens is active on the CAM side and leverages the capabilities of additive in terms of how we can support machine shops and machinery manufacturers with technologies like additive.
Another piece that’s trending in the differentiating capabilities is that Siemens CAM solutions have many experiences in aerospace and automotive, moving away from a single-purpose machining center toward higher capacity multi-functioning machining centers. So, the more complicated the center, the CNC code will require more complexities to simulate multiple machining centers. For example, in a mill-turn operation where you’re cutting with multiple spindles simultaneously, you need an advanced set of in taking advantage of the capabilities from CAM software to simulate that and drive individual code through the machining. Otherwise, you’re merely creating a more complex simple machining center.
So, to take advantage of that, you need to have software like our CAM software, where we cut our teeth on high-capacity multi-function, very complex, five, six and seven-axis machining centers, and now roll that knowledge down into the conventional machine shops in an unmatched way.
Also, in addressing the skilled labor shortage, the baby boom generation is moving out of the workforce and being replaced by more technology-savvy individuals who have less experience in conventional machine shop and machining center operation. So, the reliance on the digital twin and digitalization strategy that a manufacturing company or machine builder has is becoming crucial to younger workers who understand how the technology fits. However, what they’re trying to learn is how to turn this cool technology into real parts. So, fortunately, we have the suite of products from the digitalization process that helps to fill that gap that’s being provided by the exiting skilled labor workforce.
Blake: When you’re talking about these complex machine centers and being smarter with the challenges of manufacturing operations to maximize quality in assembly and in commissioning, what are the right solutions that we use to implement it?
Bill: Good question, but let’s first discuss quality solutions that are important to manufacturers. Whether it’s an assembly processor running a machining center, the quality we care about pertains to people, process and product. Those are the three overarching principles in the quality scheme. Also, to ensure the process can handle the requirements specified by our part and know the product can meet its requirements from a performance and durability perspective.
However, regardless of the manufacturing process, we need quality on the people side and process side. These are ingrained in your processes so that it isn’t just an output, quality is about maximizing throughput and quality in the assembly and commissioning phase.
So, with the digital twin we leverage operations as an essential part of finding solutions and driving out waste and cost. A portion of it is the bill of process and the manufacturing bill of material. Also, there’s a need to build quality into the bill of process as it’s the recipe for manufacturing or assembling the components in preparation for commissioning.
We need an assembly process and material list from the manufacturing bill of material linked to the engineering bill of material, allowing us to look backward to drive back into the machine shop and supply chain for delivery requirements. This prevents us from starting over with every configuration and variant. It’s crucial to link the bill of process and the manufacturing bill of material back to the engineering bill that created it, to prevent this process for every new machine on the floor.
Blake: Great insight. Again, we thank Bill Davis for informing us about the smart manufacturing industry and its effect on parts manufacturing. We look forward to the next and final podcast in this series when we discuss how to make your factory smarter.
To learn more about the competitive advantages of smart manufacturing for industrial machinery, listen to all of our smart manufacturing podcasts or begin reading the first blog in this series.
This concludes the seventh blog in a series on smart manufacturing and the trends affecting the industry. Our final blog will continue to spotlight the last excerpt from the transcribed conversation of the original podcast, providing solutions for where today meets tomorrow.
About our expert:
Bill Davis is the acting Industrial Machinery and Heavy Equipment Industry leader for Siemens Digital Industries Software. His experience and insights have been acquired from a career spanning 30 years in engineering and operations management with machinery and heavy equipment companies. Bill holds a master’s degree in Business Administration from Marquette University, with a concentration in Operations Management and Strategic Marketing, as well as a Bachelor of Science degree in Mechanical Engineering from Milwaukee School of Engineering.