Manufacturing for additive and subtractive processes
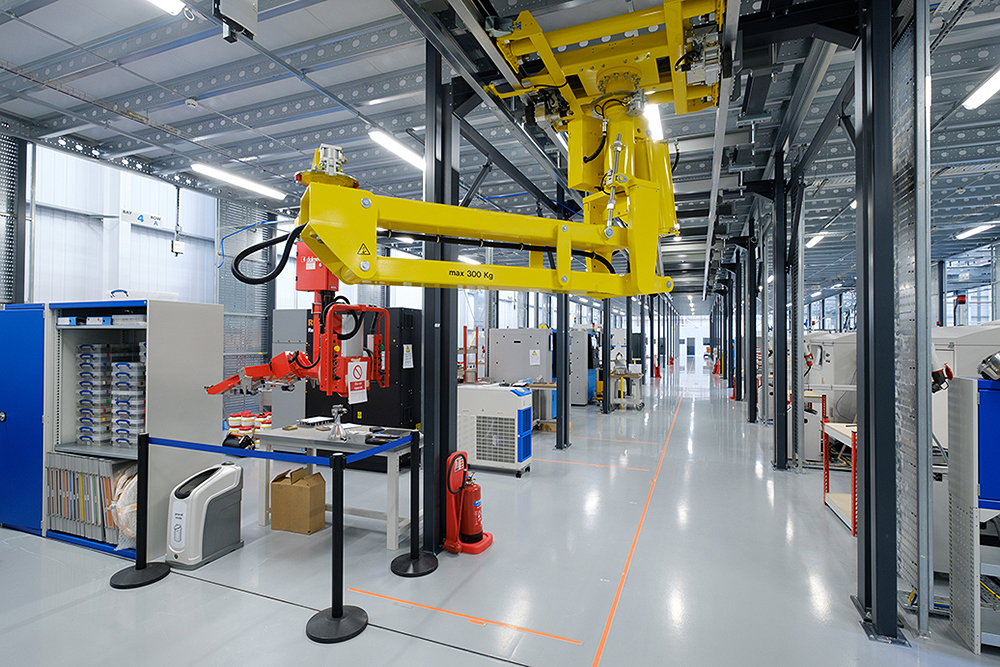
Modern manufacturing is seeing tremendous gains in technological innovation, combining the old and the new, allowing manufacturers to benefit from both worlds – one machine, two processes – additive and subtractive.
A recent article in advancedmanufacturing.org, by Karen Haywood Queen, Contributing Editor, states, “Additive machines can print more intricate, complicated and exotic shapes. But compared with subtractive processes, additive offers less final precision. To achieve required specifications, many manufacturers already use a combined additive and subtractive approach: an additive machine creates a complicated part and then the part is moved to another machine for final milling or turning.”
A hybrid approach provides the benefits of both technologies from one machine. “Most additive processes print near-net shape. You can get in the ballpark, but they will not get you that perfect shape every time. With a hybrid approach, you can stop at any point and clean up,” says Mark Norfolk, Fabrisonic CEO.
One machine for both additive and subtractive manufacturing translates into one operator that mills the inside and outside of the part. This hybrid process is not an option with a separate finishing machine that completes only milling of the part’s exterior, according to Norfolk. When printing a part via 3D, you can always go back and mill the part exterior on another machine, but this is not possible for the internal features. However, with hybrid manufacturing, one machine provides both, offering cleanup to interior features as well.
When a machine has these multiple features, it is more complex, thus more challenging to maintain. However, the advantages supersede any infrequent difficulties. These machines are ideal for jobs with significant volumes that have an increase in applications.
These advantages translate in the milling process. A hybrid machine allows for stopping at any point, refining the dimensions for precise measurements. Moreover, it provides for a smooth glass-like surface finish after 3D printing, which can often result in a rough surface. “The better the surface finish, the easier it to pump liquid through the cooling channel,” said Norfolk regarding the additive manufacturing of pipes with complex channels for cooling.
Siemens additive manufacturing and DMG Mori are collaborating in the development of an additive/hybrid bundle, allowing manufacturers to program machines for hybrid manufacturing. “Earlier software was not designed for optimizing the topology of parts produced with additive or hybrid manufacturing,” said Dale Tutt, Head of Aerospace and Defense Industry at Siemens. “If you’re machining a part, you are limited to the capabilities of the machine. Design tools are built around the subtractive method.”
Legitimate hybrids don’t lose any content of the part. “With our software setup, you can use the design files all the way through and maintain the linkage from form to finished part,” says Tutt.
These designs are outside the box of conventional methods, and in the final analysis, meet the desired goals of the manufacturer.
Learn more from the article in advancedmanufacturing.org, The Best of Both Worlds in the Same Machine, by Karen Haywood Queen, Contributing Editor.