Is design space exploration part of your innovation strategy?
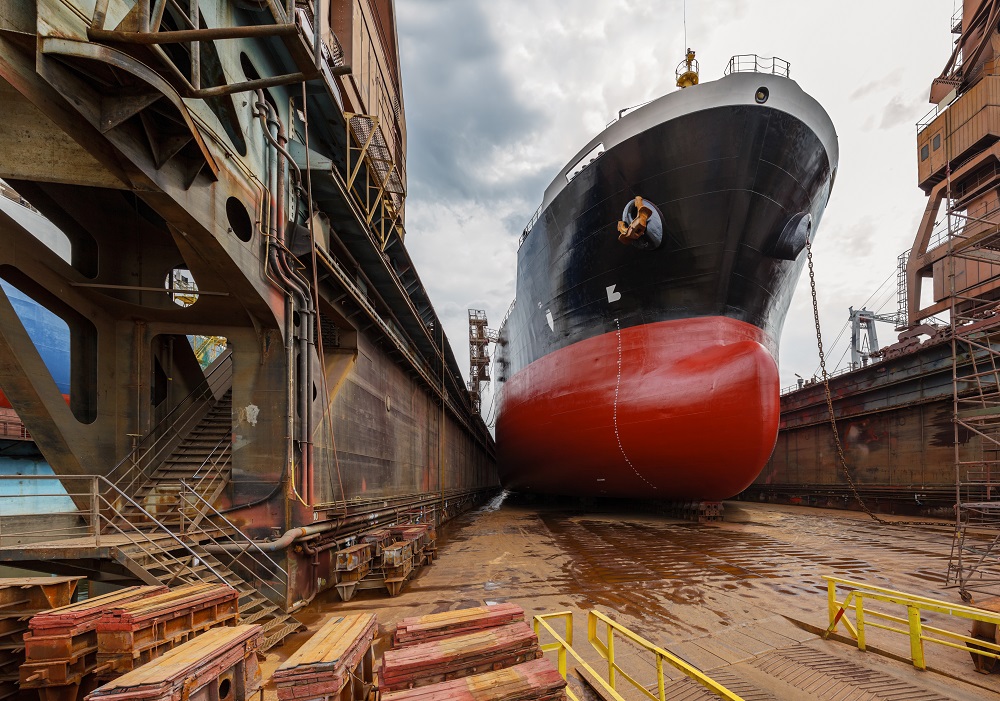
The International Maritime Organization mandate to shipbuilders is to drastically reduce emissions from their current level of 938 million tons of CO2 over the next few decades. Marine industry companies are now scrambling to meet the standards, which demand 30 percent greater efficiency by 2025 and a 50 percent reduction in emissions by 2050. Shipbuilding companies are faced with having to innovate quickly to meet these targets.
The key to successful innovation may lie in a design space exploration: creating digital twins to examine design alternatives prior to physical prototypes to quickly uncover more efficient solutions.
The traditional process for design space exploration and optimization is limited and time consuming. Often, it produces only minor improvements, not the true innovations needed to succeed and remain competitive.
That’s where modeling and simulation software comes in by enabling a virtual digital twin of the proposed product. These tools provide an ideal and cost-effective way for designers and engineers to evaluate how their products will perform, close the loop, and ensure the best results.
Figure 1 shows a tiny sample of how the simulation tool processes the space and limitations to optimize a design for potential for use in transportation. The purpose of the simulation is to determine the optimal cooling configuration for the electronics housed in this metal container. Completing this simulation involves defining objectives for the design, identifying certain parameters, and connecting multiple tools and processes, such as a CAD model, a CFD simulation, a cost sheet for the materials and a few other things.
Fig.1: Simulation offered dozens of iterations based on objectives, parameters and multiple connected tools and processes.
Before the simulation, it is imperative to define a few key things. In this particular case, only the location of the vents, size and shape of the rods and the fan can change. The thickness of the casing, the size of the vents and the shape and location of a few other aspects are defined as static. Without these limitations, the simulation test would exponentially increase in the time spent exploring that design space. It’s always a challenge to understand what kind of time computationally and clock time you have to commit to an exploration. It all depends on the objectives.
Connecting these tools through software enables automated communication. The CAD model edits the geometry, passes it along to the CFD model, which remeshes to the new geometry, and then conducts a simulation. The results then influence the next design iteration. Creating the model in a unified environment ensures the varying simulations complement each other and work together in a semi-automated way. (Fig. 2)
Fig. 2 Comparing the initial design with the improved design proving the benefits simulation is capable of delivering.
Simulation can examine many design variations in a fraction of the time and investment using a digital twin. The algorithm explores as many opportunities as possible, without being constrained by human logic. As a result, it can produce a wealth of data that include both less intuitive as well as more conservative results.
In the end, this new paradigm for design space exploration saves an incredible amount of time. The algorithm, by design, tunes itself, configures its results, and can display those results easily within the given tools.
With design space exploration simulation, it’s possible to complete an entire study in just hours, get a result and, if necessary, relaunch a new iteration. The algorithm will already have tuned itself based on the previous iteration and, from continuous learning, efficiently influence the current run.
Managing the challenges
The challenge is to put realistic limits on the size and shape of certain aspects of the design. It’s critical to understand the limits to prevent the simulation from having free rein and literally trying any and every possible solution. Without limits, simulations could run indefinitely, and the most optimized results may never be apparent.
Realistically, it’s essential to define where exploration will yield the best results and to ensure the design can be manufactured. An optimized design is of little use if it can’t physically be produced in the real world, at a reasonable cost.
Discover better designs, faster
A successful simulation requires four steps:
- Process automation. Providing parameters and limitations automates the process and ensures a variety of results.
- Distributed execution. Within the different tools, it’s possible to sequentialize the simulations, and easily run simulations in parallel. Any changes can then automatically transfer and be applied to the new simulation conditions based on the updated CAD model.
- Efficient search. Automating leads to search methods based on previous results. Simulation will always look at the previous iterations and influence where it will try next.
- Insight discovery. It’s crucial to be able to track the design through each iteration and easily track results to ensure it’s on the right track and meeting the required standards for the product. The simulation should also be rerun to make sure it performs to expectation.
Most companies operate in a reactive model that uses simulation to validate and troubleshoot, and perhaps predict possible avenues for innovation. While there are benefits to predicting, it’s not until the automation and exploration process is utilized that innovation, providing timely, cost-effective and more efficient outcomes, can truly be used.
For the marine industry, time is of the essence. Conducting design space exploration with a digital twin of the proposed product will mean successfully meeting standards, reducing emissions and minimizing the cost of innovation while achieving better results.
How can design space exploration and simulation tools work for your company?
Anthony Laurella, MBSE specialist, MayaHTT contributed to this blog
Mr. Laurella has been part of the Technical Pre-Sales team at Maya Heat Transfer Technologies for the past three years specializing in system simulation. He graduated from McGill University in 2015 with a degree in Mechanical Engineering and has experience in applications from medical equipment to electric vehicles and working with physics ranging from electrical to thermal hydraulic to mechanical.
Maya HTT was founded in 1982 as a company specializing in 3D thermal and fluid dynamics analysis. Maya HTT has more than 35 years of experience developing and implementing specialized software solutions in a wide range of fields and has been at the forefront of specialized software development.
Click here to learn more about Maya HTT.