Cars, mobility, chip-to-city design and the iPhone 4
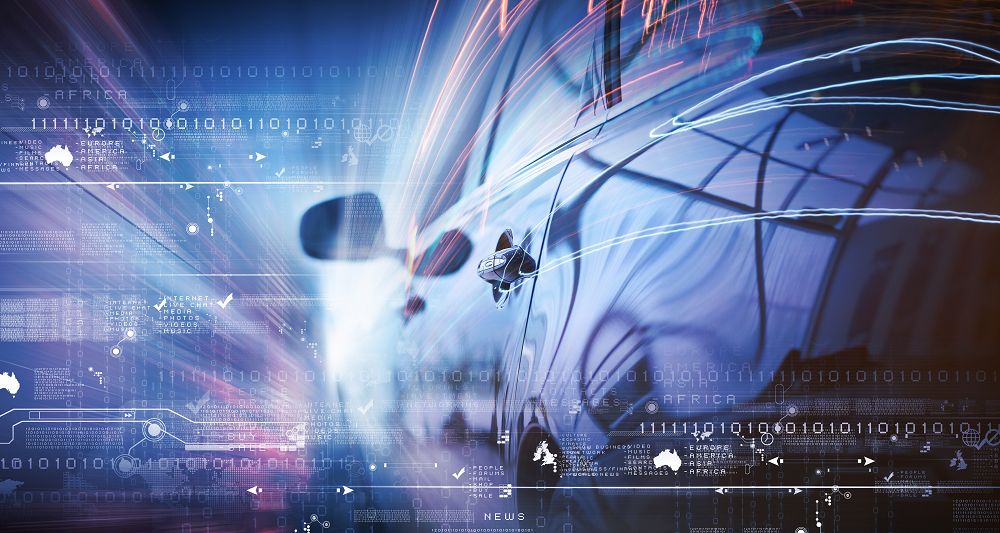
What’s the big deal with cars and computer chips? There are regular rumblings about carmakers wanting to be more involved in the development of semiconductor chips for some of the high performance compute domains in vehicles today.
Of course, exhibit A is Tesla. Electrek‘s Fred Lambert reported in late 2018 that Tesla was testing its new Autopilot Hardware 3 with employees. Fred included a snippet from an email Elon Musk sent to employees with his take on the capabilities of the new hardware:
“Tesla needs a few hundred more internal participants in the full self-driving program, which is about to accelerate significantly with the introduction of the Tesla designed neural net computer (known internally as Hardware 3). This has over 1000% more capability than HW2!”
These chips are commonly referred to as SoCs (system-on-chip) due to their highly integrated nature; the combination of components on a single substrate is exactly why carmakers and their tier 1 suppliers are taking such interest given the trend toward electronics and compute consolidation.
Traditional PC architectures had (and indeed many still do) a central processor, and a number of discrete components that perform different functions, all laid out on a single printed circuit board, or motherboard. Then along came the SoC that integrated many of these functions on a single chip: things like Ethernet connectivity, USB interfaces, RAM, plus probably some analog functionality to allow it to talk to the external world.
The advantage of the SoC approach includes less space (single chip vs. printed circuit board) and lower power consumption. This is important if your car runs off a battery, like a small but rapidly increasing number of vehicles on the road today. Add in the high compute requirements for applications like ADAS and automated driving, along with connectivity and all of the comfort features we enjoy in our cars today, and the problem of power consumption becomes very real.
But wait. Sure, the benefits of SoC design are apparent, but there are plenty of automotive-grade chips available off the shelf today. Why would automakers want to get any way involved in the highly complex world of chip design, when they have more than enough on their plates already? And why did NVIDIA make the leap from being king of gaming graphics processing units (GPUs) to an industry with traditionally high barriers to entry such as automotive? And why is Tesla publicly talking about its own in-house SoC development when chip design is notoriously expensive, needs massive scale, and gets exceedingly complicated when “automotive grade” is added into the mix of requirements?
Smartphones’ influence on automotive electronics systems
Before answering, let’s wander away from automotive and look at the iPhone 4 (the best looking phone Apple ever designed, in my opinion), the first device that used an Apple-designed SoC, which Apple called the A4. This was based on ARM Cortex-A8 architecture, tweaked for higher clock rate and lower power, which translated into better performance running apps, and longer battery life — the fundamental demands of smartphone users), with some extra cache thrown in.
Jump to today: iPhone XS has A12 Bionic SoC with four cores for performance, four further efficiency cores to help with power consumption, integrated graphics, some kind of on-chip security, and a neural engine for running AI and machine learning apps.
Basically everything that Apple touts as key selling points are direct benefits from having control over the SoC used on their devices. Battery life, performance, security, image processing speeds and quality for the camera, faster Face ID — these features are all driven by A12 Bionic capabilities.
Ask Apple to design an iPhone XS-like device using off-the-shelf components. It would likely be possible, but I’d wager that battery life would be an hour, it would probably need some water-cooled system due to power and heat, and it would likely cost twice the price of phones in your local Apple store, which is problematic since there’s an upper limit to the willingness of even the most ardent fans when it comes to paying the Apple. The form factor idea would be thrown out the window to cram in all the extra discrete components. Basically, Apple’s entire value proposition for iPhone can be traced back to having their own SoC design capability.
Cracks may be appearing in the iPhone edifice, but it’s without a doubt the most remarkable of profit-and wealth-generating device from the Silicon Valley in the last decade. Apple quite famously captures a modicum of overall smartphone unit sales (less than 20 percent) while capturing 80 percent or more of smartphone profits.
SoC design in the auto industry
Back to automotive. Apply the same level of product differentiation from the mobile industry to cars, and it starts to make sense why carmakers and their tier 1s are looking for ways to get more control over SoC specification and design. Their whole value could be, and in fact very likely will be, determined by the chips powering key domains inside the vehicle.
With vehicle architecture design moving toward a more centralized, domain-processing model, it makes perfect sense at the vehicle level to take hold of the chip-design reins. Domains such as automated driving, connected car and mobility solutions lend themselves to in-house SoC development: partner with a fabless chip design house, and also a manufacturing partner, to keep costs manageable. Co-designing hardware and software in an optimized way is the best chance for carmakers to offer the level of power management (e-mobility), performance (in-vehicle experience for media and entertainment), and elegant user interfaces (taking iOS as the benchmark) customers are coming to expect.
The chip is designed around functional requirements, and software is written to extract every last bit of capability from that hardware design, creating an optimum consumer experience. Indeed, this meta trend is why the auto supply chain has long been moving toward a supplier network and trying to find collaboration in SoC design.
But that raises the question: how does a carmaker that is traditionally invested in mechanical design, system integration and marketing get into this murky world of chip design? Automotive SoCs are hugely complex to design. They need to operate at up to 150 degrees Celsius and higher (if located close to the engine, for example), and they come with reliability requirements way beyond that of the chips in a smartphone; today, SoCs likely control your vehicle’s braking system and steering, not something that can be messed around with. Automated driving sets the bar even higher.
The future of SoC design in automotive electronics systems
The answer is collaboration throughout the industry. The leading auto chip design houses have been working with carmakers for years on specification and design of key components, such as engine control and braking systems. The carmakers already have a degree of expertise in chip hardware and today write much of the software that runs on them. Tier 1s may own their own manufacturing facilities for semiconductors, or fabs. They may create software models for part of the chip and work with the semiconductor houses to implement on custom chips.
The baseline is in place. What is needed is a methodology that allows this co-development of SoC design where carmakers can decide where they want to control the IP for key domains. They can work with their partners to create early silicon models that can be used to write software, test it, and then test it at the vehicle level; the only way correct behavior can be defined is in the context of the entire vehicle. Then, they can add in layers of simulated testing for, say, autonomous vehicles.
There are many questions such testing seeks to answer.
• How can we test autonomous or automated functionality using silicon models of an SoC that have not even been manufactured yet?
• How can we ‘drive’ millions of simulated miles under many road conditions before the SoC is physically ready?
• How can we test this software in the context of vehicle-to-infrastructure environment?
• How do we develop and validate correct SoC and system behavior in months instead of decades, reduce development time, improve quality and comply to standards such as ISO 26262 for ensuring functional safety?
So what’s the point? Is this is just a big wish list of things we need to put in place?
Actually, it’s all in already and happening now. As with other tech waves like smartphones and apps, there is an emergent development environment for transportation. And for all breadth of smartphones and mobility, this new development environment is larger still: spanning chip-to-city domains, enabling multiteam, multidiscipline collaboration, and applying new methodologies — all upending the way travel is created and ultimately consumed.
About the author
Andrew Macleod is director of automotive marketing at Siemens, focusing on the Mentor product suite. He has more than 15 years of experience in the automotive software and semiconductor industry, with expertise in new product development and introduction, automotive integrated circuit product management and global strategy, including a focus on the Chinese auto industry. He earned a 1st class honors engineering degree from the University of Paisley in the UK, and lives in Austin, Texas. Follow him on Twitter @AndyMacleod_MG.