Establish your manufacturing process and collaboration plan
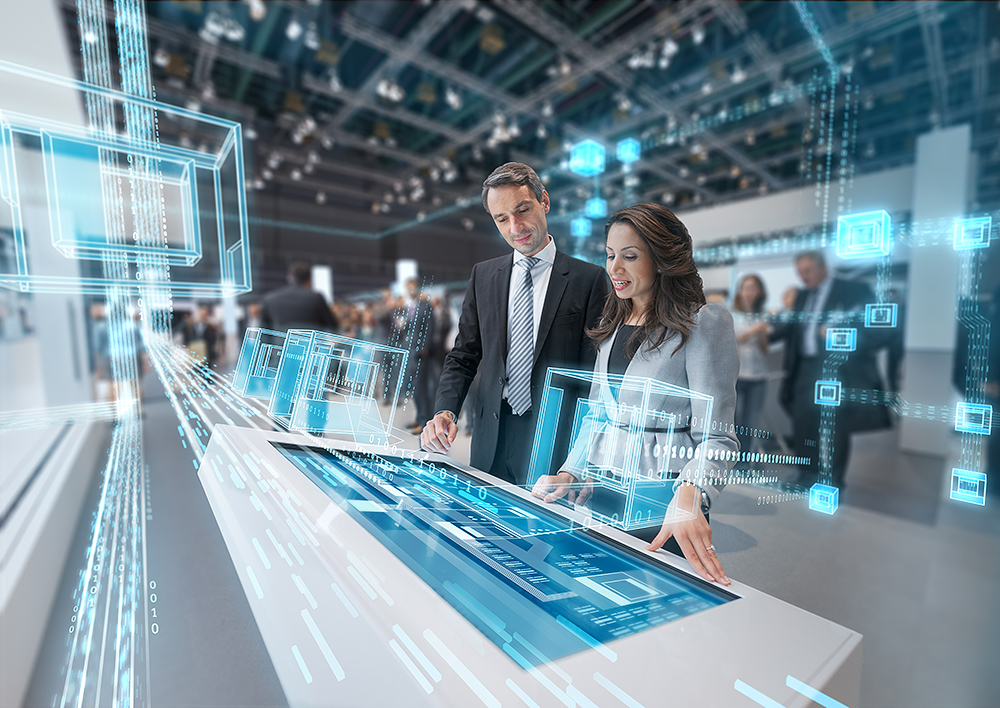
By: Wolfgang Schloegl and Christian Heck
The ability to analyze and plan the process for manufacturing your product is crucial.
Product manufacturing is entirely different from the past, and changes in the industry are driving the competition to change the process as well. Collaboratively planning and adjusting in multiple cycles leads to the best result and more iterations to determine the resources, space, materials and production needed to manufacture your product ― making for intelligent, smart design.
A manufacturing planning engineer, for example, who is responsible for the production plan of a new product line, discovers that collaboration is crucial as they find various areas for improvements in the product, optimizing the manufacturing production process.
The plan also results in upfront costs directly influencing the profitability of your product. According to a 2016 CIMDATA report, splitting the costs for ideation and manufacturing results in the planning process consuming approximately 20 percent, while the remaining 80 percent going toward manufacturing the product.
This value allows for a smart design process and a smart design for manufacturing. When the ideation phase is performed correctly, you can reach tremendous benefits during the manufacturing process. Moreover, the digital thread in production planning supports you to ideally shape and guide your product design to cost-efficiency via a tailored production.
The process, digital thread and manufacturing plan
The digital thread connects the product design with the manufacturing planning and is also the structure of elements in the planning and manufacturing process which enable a connected flow of data across and throughout the lifecycle. If you manage this correctly, it results in a significant positive impact on the profitability of the production process. When you plan the manufacturing process based on the digital thread, you link the product-build with processes and resources.
Most importantly, the digital thread assists in making necessary modifications to enhance manufacturability. For example, in building an automobile, placing the water pump on the right side versus the left side of the engine could make a significant difference in production, its build sequence, assembly line features and process documentation.
Structure and resources
Planning the product manufacturing and resources within a specific plant context becomes a major factor to make relevant decisions. for your manufacturing process Global production capabilities typically offer multiple possibilities where manufacturing can be performed to optimize profitability.
Collaboration is crucial to begin the manufacturing process based on the digital thread. The resultative data could dictate changing the order of the process, the physical space or the actual product; which all have an impact on the costs, quality and manufacture-ability to your process. When you manage this part correctly, it results in a positive effect on the profitability of the production process.
Value
The value of planning your manufacturing process with a digital thread is to have consistency in that plan. Likewise, the importance of collaboration between product and design, manufacturing and execution and production on the shop floor becomes apparent in faster/better results. The collaboration based on the digital thread provides an increase to manufacturability that‘s economical, quicker and more efficient – impacting your profit.
The digital thread improves the overall value and profit for your company, which enables collaboration.
This concludes part two in a series on defining digital thread for production systems engineering. In part three, we’ll continue by discussing factory and line design.
About the authors
Dr. Wolfgang Schloegl leads the Digital Engineering department in the Siemens Digital Factory division and is amongst others responsible for the software Automation Designer. He also works on providing integrated solutions of Siemens PLM Software with Siemens automation systems. He has been with Siemens since 2003 and previously worked in planning and digital manufacturing for automotive production. Wolfgang was formerly with Daimler in Sindelfingen, Germany, where he worked on knowledge management for production planning, and later, in project management for assembly planning. He studied production engineering at the University of Erlangen-Nuremberg in Germany, where he earned his doctorate in the area of simulation for discrete production.
Christian Heck is a Production Systems Engineering Solution Manager for Siemens PLM Software, a business unit of Siemens Digital Factory Division. He has more than 14 years of experience in automation engineering and commissioning, as well as developing cloud-based industry applications. Heck gained much of his experience working for Siemens Oil and Gas Offshore in Norway, where he worked as System Responsible for several major oil and gas projects. His previous experience with Siemens includes leading a Service Line for optimizing production plant performance based on data analytics applications. Heck holds a Bachelor of Science degree in automation engineering from the University of Cooperative Education in Karlsruhe, Germany.