How the future of flight changes product lifecycle management
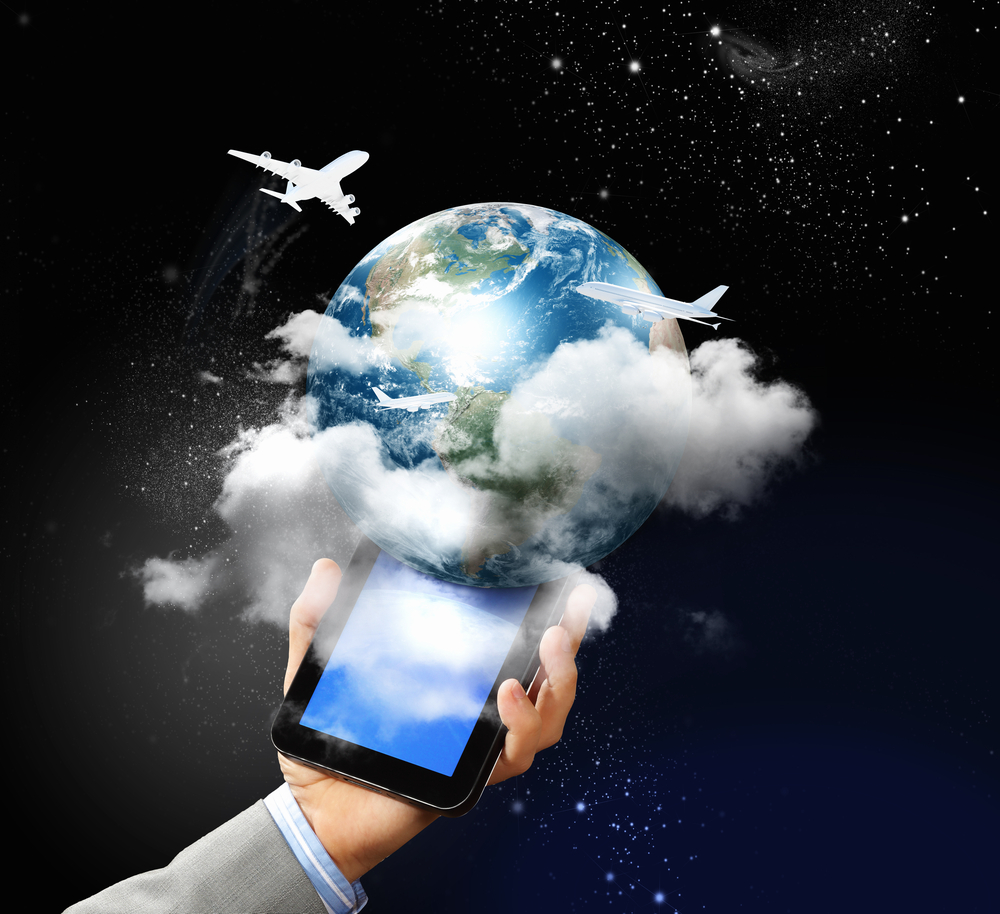
On July 20, 1969, Neil Armstrong’s televised moonwalk transfixed the world. People couldn’t believe what they were seeing. A spacecraft had safely transported two astronauts 360,000 kilometers (223,694 miles) away to an unchartered orb, and now a human was bouncing along the primitive, rocky landscape.
Today, we’re on the brink of another giant leap for humankind driven by aerospace innovation. New advances in propulsion, materials, human machine interfaces and artificial intelligence will challenge aerospace manufacturers as products and services grow more complex and interdependent. At the same time, aerospace supply chain models will change as manufacturers weigh efficiency gains against intellectual property protection.
To successfully manage this changing landscape, manufacturers will need sophisticated product development and management technology.
The industry is already making huge strides in efficiency and cost reduction in production programs, and modern aerospace software enables lower-cost development and concurrent design across multiple disciplines and partners.
The following trends have helped make it possible to profitably commercialize new crafts and concepts when essential software tools are in place.
Product Lifecycle Management
Perhaps most often used and best known is Product Lifecycle Management (PLM), which enables companies to create an end-to-end, integrated real-time digital thread of information covering a product’s entire life. All product records, from testing to redesigns, are in this thread, and the records are always up-to-date and always available to decision-makers.
PLM technology enables concurrent development among multi-disciplinary teams and prepares companies to engage with the extended supply chain.
The experience at NPO Saturn provides one such example. Yuri Zelenkov, IT director at the Russian aerospace engine producer, understood that his existing design technology wasn’t effective. The company had a Communist-era practice of producing one type of engine at a time and needed to be able to simultaneously develop more than 10 new innovative designs. The company chose Siemens PLM Software to transform their processes.
“The company’s management realized that the development and engineering data management system had to be drastically changed,” Zelenkov said. “Not just to evolve with the fashion and spirit of the times, but rather to address the company’s real needs.”
With the new software, he added that all the engine development stages—engineering analysis, production planning, NC programming, manufacturing and tests—are performed in a concurrent or synchronized manner, not one after one.
The new process cut the company’s engine development time in half and eliminated prototype testing, which saved significant program costs. The company is also now better positioned to participate in extended supply chains.
“We have established business processes that match modern international best practices,” Zelenkov said. “As a result, the company is an equal partner to large international projects.”
Application Lifecycle Management
A more recent trend, one that’s perhaps less well known, is Application Lifecycle Management (ALM). What PLM has done to streamline product development overall, ALM has done specifically for software development.
As flight vehicles are augmented with powerful software to control, monitor and maintain them, their development will require ALM. One estimate finds that the number of lines of source code needed to control the avionics in an aircraft increases by 400 percent every two years.
One global defense industries giant dramatically increased the application control and visibility within its project-managed process. It was able to achieve a CMMI Level III certification in three months for one project—rather than the 10 months it had anticipated before implementing ALM.
The solution (Polarion) also accelerated the project’s documentation process. Reports were able to automatically generate, cutting down the time it took the company to produce reports from weeks to two days.
Choosing the right ALM technology is critical. The systems must be specialized to unique challenges of avionics software. They must also be compliant with the regulations of certifying agencies to ensure that the application data is controlled, managed and updated in accordance with aircraft industry-specific requirements.
Integrated PLM-ALM solutions
Increasingly, the new innovations driving the future of flight involve combinations of mechanical, electrical and digital systems.
As pressure grows to adopt more digitally driven product capabilities that rely on software code, aerospace manufacturers will require a technology that integrates PLM and ALM. This will enable aerospace manufacturers throughout the supply chain to embed software into the electronics hardware and mechanical parts, just as they incorporate other features. With ALM-PLM integration, developers can manage, link and trace software requirements and design objects (functions, test cases, models, etc.) to data from all the interdependent domains.
As well, they’ll be better able to understand cross-domain relationships and dependencies in all product lifecycle phases. From requirements to delivery and maintenance, they can manage the software lifecycle in the context of the entire product to accelerate product introduction, lower costs and improve quality. Such capabilities are available in Siemens PLM Software’s Teamcenter program.
Taming complexity
It’s critical in a highly complex industry to increase the capability of the development organization by employing specific development tools. Enabling more concurrency in the development process among multidisciplinary teams becomes increasingly important as products incorporate new advances.
A critical point occurs when complexity outpaces capability within the organization. This translates into obvious business failures, such as delayed schedules and budget overruns. The challenges recently seen in many aircraft development programs speak directly to this problem.
To succeed, the development organization must continually bend the capability curve. That is, it must increase capabilities in the organization faster than the complexity the product requires. But with the latest product and software development and management tools, aerospace manufacturers can stay ahead of the complexity curve, ensuring their competitiveness in the next generation of flight.
This concludes part two of our series on the future of flight. In part three, we discuss how the future of flight will change relationships with suppliers.
About the author
John O’Connor is the director of product & market strategy in the Specialized Engineering Software (SES) organization of Siemens PLM Software. SES develops and markets CAD-integrated, specialized engineering software for product design and manufacture in the aerospace, automotive and other design-driven industries. O’Connor has served in numerous roles at Siemens, ranging from application support and technical sales management to business development. Prior to Siemens, he was a senior design engineer at Lockheed Martin, where he led a number of product design teams. He holds a Master of Science in materials engineering and a Bachelor of Science in mechanical engineering.