Why you need a digital strategy for future manufacturing
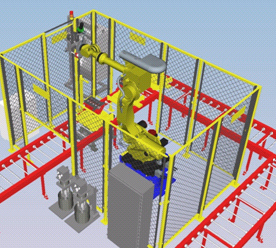
The world of manufacturing continues to evolve as it becomes increasingly global and digital. Many manufacturing companies are struggling to make the transition to digital manufacturing. But the companies choosing to move forward with a digital strategy stand a better chance of not just surviving these changes, but thriving in them.
One company hedging its bets on its digital strategy is Nexteer, a Michigan-based Tier 1 steering and driveline supplier with global locations. Nexteer is embracing the changes digital manufacturing is bringing to the market, and it’s implementing processes throughout its digital strategy that will allow its business to bring its “digital map” to life and continue to bring value to customers and shareholders in the future.
Nexteer’s process, as well as the digital manufacturing issues it currently faces, were highlighted in a presentation from Dennis Hoeg, vice president of manufacturing, manufacturing engineering and enterprise systems, at this year’s Digital Twin Summit. Some of Hoeg’s observations included how:
• The company’s digital strategy begins with the company’s culture. Hoeg said that Nexteer believes the people throughout the company will determine how successful its digital strategy actually is, so it created a digital map that will make sure the right processes are in place moving forward. This digital map includes virtual manufacturing and virtual design processes, global plants, current technologies place, as well as space to accommodate for future changes.
• Traceability is a key part of Nexteer’s business, so the company is ensuring its digital strategy efforts account for this important safety component. Traceability is a core part of the company’s manufacturing intelligence model, as well as the quality and product performance side of the business, to ensure that its products and processes stay safe.
• Nexteer works with a lot of data. The company has data coming from sources such as manufacturing execution systems (MES), traceability, lock control, enterprise resource planning (ERP) and PLM. One of Nexteer’s major goals is to connect all of its important operations so it can predict performance before it begins testing. The company wants to accomplish this with fast, complete problem-solving processes that allow for mining databases, understanding important data in them and then being able to analyze, predict and control key parameters. Hoeg said this can be a difficult dream, but one that’s very possible to achieve.
We hope you enjoy this video.
Keep an eye on this blog as we continue to provide links to other summit talks.
About the author
Indrakanti “Chaks” Chakravarthy is the Marketing Programs Director working in the Americas zone at Siemens PLM Software, where he is responsible for marketing programs covering the aerospace, defense, federal and marine industries. Chaks has spent the last 30 years working for a number of companies in presales technical, sales and marketing areas of the PLM portfolio in India, Japan and the United States. He has a mechanical engineering degree from Jawaharlal Nehru Technological University in India.
VIDEO TRANSCRIPT
TOM MAURER: Ok. Our first speaker this afternoon is Dennis Hoeg from Nexteer. He’s vice president of manufacturing, manufacturing engineering and enterprise systems. Dennis, the stage is yours all.
DENNIS HOEG: Alright, thanks. Good afternoon, everyone. I am very thankful to represent Nexteer here at this great event, and it’s been a great event so far today. Now we’re going to talk a little bit about manufacturing, which is deep in my blood.
A little bit about Nexteer. We’re a tier 1 steering and driveline supplier to many, many OEMs. We’re headquartered in Michigan, but globally we have 13,000 employees, and we’re a $4 billion company.
Our product overview: we have steering columns and I-shafts. We have driveline products, electric power steering, hydraulic. And then in the center, you’ll see, and many of you talked about this – this morning ADAS [advanced driver-assistance systems] and automated driving technologies – a big move towards that. You’re going to need steering in these cars. Whether you need a steering wheel or not, you still need steering – an important part of what’s coming in the future.
Then, this is our manufacturing footprint, and an important part about this is going to come up later when I talk about integration and manufacturing. Just kind of keep an idea that we are a global company in a lot of different locations.
You think about digital manufacturing, and we talked about already this morning, the landscape is changing, and so are we. We’re really working hard at changing how we do manufacturing and really integrating the business.
Also mentioned this morning, the term “shift left.” We use that term as well. This is our business process: from product design, through process design, through industrialization, into production. Our whole goal is to shift to the left, reduce the lead time, shrink what it takes to do our business.
It’s really important going forward, because these digital solutions and this architecture, we believe, is a key part of future customer and shareholder value. It really does bring value to the company, and brings value to those we serve.
But it starts with people. On the left is our culture. Culture is a big part of our company, and a big part of who we are. The people inside the company are really the pillar, that are implementing this digital strategy across the company.
So we created an organization. Their job is to implement these technologies within manufacturing and across the enterprise, a really important part of this strategy beyond just the technology itself.
You’ll never be able to read this map, but this is our strategy map for the digital trace across the company. We started out trying to figure out, how do we get this on one page? So this is our first attempt to trying to get our strategy on one page. As technology changes and time changes, there’ll be a 2.0 and a 3.0. But we’re going to keep this updated, because it starts on the right with the virtual manufacturing and the virtual design, and works our way through the plants globally, and with each of the technologies that we’re applying and the future ones that we’re working on as well.
So this is our digital map for the future. It’s also a dream. You know, you’ve got to dream big. This is our dream. But I don’t think it’s that big; I think it’s very doable.
I’ll talk about a couple of segments, what we’re doing inside of this digital trace inside that map. One thing is, we’ve been using Teamcenter, NX and the drawing and design tools for a long time. We integrated a new PLM system here a few years ago, and now we’re moving on to integrate the teams that are manufacturing part of this to add to that database all of the manufacturing details that go along with the product details.
You know, a lot of us have what you see on the left, are document centers full of paper and that out on the floor. Not the ultimate goal, but an ultimate outcome of doing this, is going to get to a paperless factory. We know that’s going to be the outcome, and we also know that that way, we’ll have the latest information in front of those people who need it.
All of this is around digital standards. We start with a standard machine design; we call it SMD. But what is it, is it’s the base design that we’re going for to meet the requirements of the product. And then you see, there’s folders, so to speak, of categories inside of this machine design that has all the parameters around the machine: machine design itself, operator interface. It could be standard work, operator control plans, quality documents – everything that’s required tied to that job, tied to that database.
The other part is our manufacturing structure, and this is a picture of what we’re implementing across the company. We’re calling it our manufacturing intelligence model. If you look to the right, it’s traceability. We’re a safety product supplier; traceability is a key part of what we are and what we do, so that’s a major part of what we’ve implemented already.
Then, we’re working to the left. We’re implementing maintenance operations. This quality system; warehouse inventory operations, which is internal to us; we already have an ERP system for external; and then MES, how to tie all this together inside our production operations.
The key part of this is integrating all of this. You see on the left, the business system, all the production and the quality systems. We have models inside of each of those that we’ve implemented. The key about this is integrating them together, getting them in the right database, making sure that database is clean and then being able to integrate that all together.
How does this all fit together? Why are we trying to do all of this? I’ll go back to our map. Here’s a case where we have a product A that’s manufactured in five different locations globally. It’s important to understand that these things are very similar: similar machines, similar operations, similar tools, similar requirements.
How do we make sure that we’re optimizing all of those and that they’re at the best value and at the right requirement level? We’re sharing lessons learned. We probably all struggle with how do we get lessons learned integrated back into what that main design is and the standards going forward.
When I think about data connections, this is where the database part comes in. You have machine and operations analysis. That comes out of the MES, the ERP databases, and the standards are coming from PLM. It’s important all three of those databases are accessible and integrated.
Then on the quality and the product performance side, there’s traceability, which is very critical to us. There are on some of our products, for example, we carry at least 1,500 lines of information on a completed product when it goes out the door. You talk about having all this data. Do we look at all of it, no? But it’s important to have that, because we’ve found cases where the data itself wasn’t important, but the relationship between some of the data was important. Just having that data and being able to analyze it is really critical to us.
Then there’s warehousing. How do I connect what’s coming in the door? How do I connect what comes through the supply chain to us, and then integrate it in the quality side and into the performance side of our products? Then always it gets down to cost – what’s our cost? What’s our opportunity? That’s a connection between MES and ERP.
You can see there’s a lot of need to connect all these databases together and to use that for what we have to do to improve our business and operations.
If you think about performance improvement, I think about it as a math equation. You’ve got this function of X, and I’ll pick on a test parameter – I’ll pick friction, for example. At the very end of the line, or very close to you in a line we test for friction. There’s a lot of things that go into that friction level before it even gets to the end of the line.
We need to connect, and we are starting to connect, with all of those operations that are important, trying to figure out which ones are important, connect the data from those. This is where I strongly believe we can get to the point of predicting performance before we even get to the point of testing for it. If you can predict for it, now you don’t have to do the test for it anymore. You can do something different. You don’t have large system costs tied up at that final end where you’re testing – you can take care of it in a component level or in a subsystem level.
But you think about where all the data comes from, it’s the same thing. It comes from MES, it comes from traceability, it comes from lock control, PLM. There’s even operator interfaces that are tied to some of this.
I really believe that we can get to faster and more complete problem-solving by digging into these databases, understanding what’s important and then start to do the analysis, the prediction, and then controlling some of those key parameters that are well before the point where we test today, and then spend that time later doing something else that adds value to the product. I know that may be a difficult dream, but I know it’s very possible. We’re seeing gains already in some areas that prove that; I know that’s very possible.
I like to say we’ve been hearing this recently from many other companies, so I stole it. But I think it’s important to think big. I go back to our picture of what we believe is our vision of what digital trace should be.
But think big, and then start small. You know you’re not going to conquer the world, but pick what you want to pick that’s going to make a difference for you.
And then fail fast. You guys talked about this morning about doing iterate changes that were going on inside software development. Same thing with us: fail fast. Check, fix, check, fix, do the PDCA [plan-do-check-act] cycles as quickly as you can.
Then scale quickly. Sometimes that’s hard. It’s easy to just start small. It’s easy to fail this. But we have to learn and have to really push to scale quickly, because the opportunity is there as long. As we can define and get our systems to where we want them to be, we need to just scale it up as fast as possible. If I think back about our map and that product that’s in five different locations, it’s critical that those five locations get integrated together.
Some key takeaways I’ll give you from where we are so far.
I know that reduced lead times really are going to impact our customers’ shareholder value. It’s a big deal to us, and it is not that difficult to do. It’s a great opportunity for us.
Complete analysis of our production process, of our designs, can be done now following a global standard. Using these databases, integrated databases, to help ourselves. That’s a key to me going forward of our manufacturing and process design and analysis.
Lessons learned and continuous improvement. How do you integrate that back together? We’re going to do it inside of the PLM system, but get it back to a standard. That’s really important. How do you get those lessons learned from all these different locations of all these different points back to a common place?
Proactive solutions. Be more predictive.
Also, this global collaboration. It’s difficult sometimes to do the collaboration globally. But when you get the data, when you get these digital systems together, I believe it’s a lot easier to do the collaboration that needs to go on.
And, again, passing those lessons learned.
For us, technology really is allowing us to change how we manufacture. It’s really a difference in the world today. To me, the future is really exciting about being in manufacturing.
Not a lot of people stand up and say it’s really exciting to be in manufacturing – but it really is.
Thank you for your attention.
[Applause]