The benefits of becoming a digital machine shop
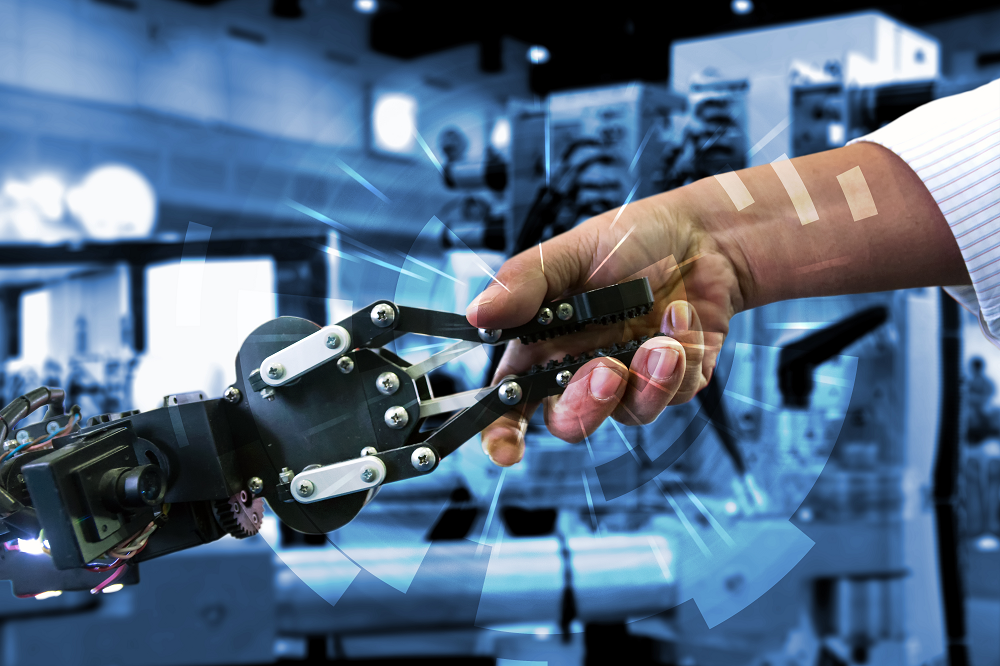
Information already drives the machine tool industry to a certain extent, but in today’s digitalized world, managing and sharing knowledge is fast becoming a critical competitive advantage.
Unfortunately, at traditionally run machine shops, that knowledge resides in spreadsheets and multiple software systems, and is shared among process owners on thumb drives, paper and other uncontrolled file systems. Worse, some of the most vital knowledge is “stored” in the minds of manufacturing experts who carry it home with them each evening.
These disconnected systems disrupt the flow of information and knowledge sharing—as well as the flow of the manufactured part—as it moves from department to department from development to delivery. Such systems result in process variability and errors that slow time-to-market, add cost and inhibit continuous improvement, accuracy, efficiency, effective resource utilization and quality. These problems, in turn, destroy competitiveness and constrain profitability.
Leading edge machine shops, however, are adopting Industry 4.0 technology to integrate disconnected processes, an approach that not only eliminates problems caused by the lack of data integration, but also creates new capabilities.
These technologies start with the digital twin—digital representations of product, production system and their performance—and integrates them into a digital thread that weaves together every step of the manufacturing process, closing the loop between the virtual and real worlds of production. Capitalizing on this process of digitalization requires a fundamental change in how machine shops work.
Callaway Golf, one such example, is known as the first company in its industry to seriously invest in engineering to improve their clubs.
Starting with Siemens NX CAD to design new products, Callaway accelerated the introduction of new clubs to every 10 to 16 months, which had previously taken from two to three years. Later, the company added NX CAE for engineering, and NX CAM software so machinists could make push-button prototypes. All the teams use Teamcenter software to manage the entire process.
With this digital thread, Callaway is able to stay ahead of—and even shape—customer expectations, allowing it to control its destiny while keeping the competition back on its heels.
Be a digital business strategist
What sets apart machine shops today is the ability to quickly turn around perfect products when and where the customer demands. This requires more than manufacturing expertise; it requires more effective knowledge sharing between and among people, systems and machines.
The traditional inward focus on manufacturing expertise and manipulating materials has been turned inside out. Machine shop owners must shift their focus from material handling and machining toward satisfying their customers’ ever-more demanding needs.
Solutions that integrate functions and make data sharable across them create digital machine shops that achieve the following:
• Deliver more complex products faster: Perhaps nothing challenges machine shop owners more than customers’ increasingly demanding turnaround times of complex and customized products. The traditional response, speeding up workflows, is stretched beyond its limits. Simply upgrading the old, disconnected software and systems and working harder won’t work and adds other risks, such as increased errors and lower quality.
• Work efficiently and effectively: With integrated systems, even more complex projects become easier to complete on-time and on-budget. Product engineers and operators can work concurrently, because they can access the information they need when and where they need it, and it’s all accurate and up to date. They can also draw upon and reuse designs, analysis and best practices of previous projects, all stored in the digital thread.
• Strengthen existing customer relationships: Shops that reduce time-to-delivery and consistently hit promise dates keep customers coming back. Digitalization increases efficiency by reducing time-wasting variability and errors caused by knowledge transfers between processes.
• Expand capabilities: Digital machine shops are ready to quickly adopt the latest manufacturing technologies, like additive manufacturing, advanced robotics and automation as well as emerging technologies such as artificial intelligence. With these technologies, machine shops offer customers new products and services, as well as reap the efficiencies within the business.
• Diversify and expand: Digital machine shops are better equipped to grow the business. With knowledge collected, stored and always available in the digital thread, less experienced employees can do more. This frees up manufacturing experts to focus on higher-value-added work, such as attracting new customers, entering new markets and innovating new products and processes.
• Boost margins: As time-to-market shrinks and costly mistakes are avoided, digital machine shops capture the savings, converting them to bigger profit margins.
• Drive continuous improvement: With a unified, digital end-to-end technology system, machine shops more easily collect, adapt, re-use and build on their expertise. Everyone from designers, engineers and machine operators can access, act on and contribute to best practices.
Haidlmair, a European mold-maker, is already capitalizing on these benefits. The company credits the switch to an integrated Siemens NX system for the following:
• Being able to move part information from one department to another without losing accuracy
• Digitalizing knowledge and eliminating paper, thus enabling parallel processing
• Speeding development of the company’s custom molds by making information from prior parts orders accessible for reuse
• Reducing costs by 15 to 20 percent
• Speeding customer delivery
The company’s next steps are standardization and automation.
For today’s machine shop, being data-driven is necessary, but not sufficient, to ensuring competitiveness. Only by becoming a digital machine shop, with connected and integrated data systems, will they effectively eliminate problems that occur with manual data hand-offs and enable the flexibility and responsiveness that customers demand.
This concludes part two of our digital machine shop series. In part three, we discuss how to open your shop’s doors to new markets with adaptive systems.
About the author
Sashko Kurciski is a senior marketing manager at Siemens PLM Software. Sashko leads the marketing of the part manufacturing software solutions to help companies transform their production processes through digitalization. He has been in the CAD/CAM/PLM software industry for almost 20 years, working in a range of roles, including product management and software development. Sashko holds a master’s degree in Mechanical Engineering from the University of Arizona and lives in southern California, USA.