How the digital thread transforms verification management
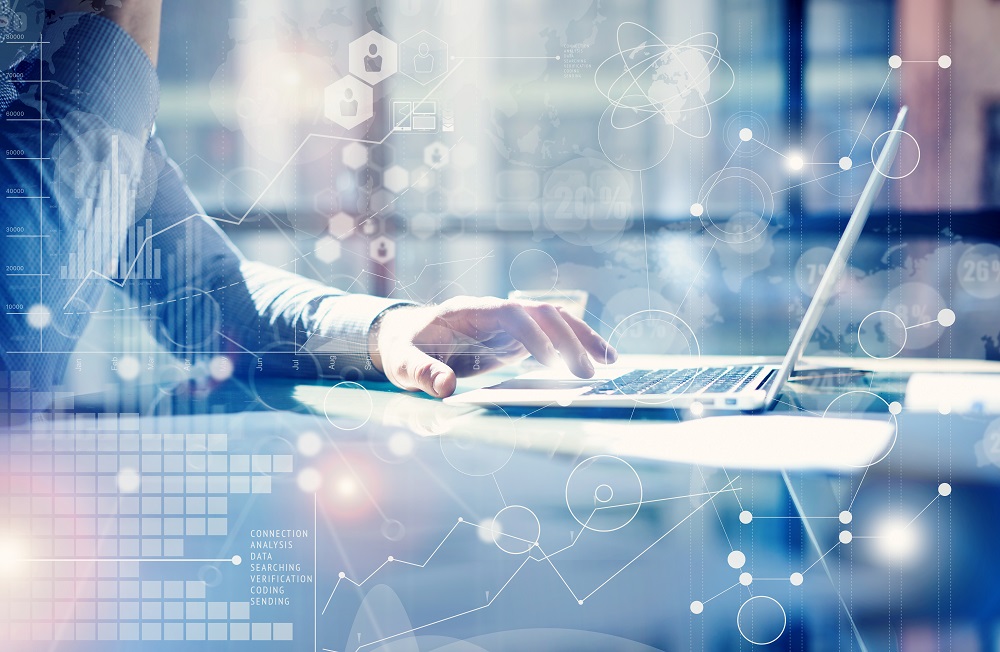
More Americans are living to 100 years or older than ever before. The Centers for Disease Control and Prevention said the number of centenarians in the U.S. rose 44 percent between 2000 and 2014.
Advances in data-driven diagnostics and disease management are a major contributor to increasing longevity. The same can be said for B-52s, the Boeing defense bombers built between 1952 and 1962.
Seventy-six of them remain in active service; and with modern maintenance practices, those planes could still be active at 100 years old.
But there is one big challenge for aerospace and defense (A&D) manufacturers: With tens of thousands of regulatory requirements—each of which must be re-certified every time a change is made—streamlining the verification process is critical.
The good news is that advances in product-data management—just as in healthcare—can streamline the verification process and return other important benefits.
Imagine having all product lifecycle data (test requests, test procedures, test results, simulation results, artifacts, test articles and simulation models) in one place and linked to the design models. This would enable a product manager or engineer to determine the impact of a proposed change before executing it.
An added bonus for A&D manufacturers: The 20- to 40-year lifetime of their products means the benefits of an integrated product data system will accrue for decades. Downstream operators won’t need to waste time, effort and opportunity because of missing data for design, production, certification, commissioning, maintenance and other prior processes and decisions.
To build this integrated product-data model, A&D manufacturers need to have an always-on, always up-to-date and widely accessible digital thread of product data.
The digital thread and promise of Industry 4.0
The value of the digital thread is essentially the foundation of Industry 4.0, which, by definition, is tailor-made to address the biggest challenges in today’s processes. That is, the need for and obvious benefits of:
• Horizontal integration of the value-added network
• Seamless integration of the engineering of that network
• Vertical integration and networked production systems
Industry 4.0 is all about integration and hence the digital thread. Industry 4.0 promises to integrate the “cyber-physical” systems. Design takes place solely in the digital realm and generates only digital records while testing and other downstream processes take place in the physical world—with data that might or might not be digitalized, but traditionally always resides separately from design data.
While these once-modern point solutions still might yield some benefits, they are outdated. They can’t provide an always-updated and integrated digital thread of data across a product’s lifecycle.
By contrast, leading A&D manufacturers are using product lifecycle management (PLM) as a process- and product-management platform that uses the value of the digital thread to enable data integration beyond product development and production, and into maintenance and service requirements.
Only in the last four to five years have software and hardware become powerful enough to enable such integration. Earlier PLM systems were limited in terms of the types of objects for which they could create relationships. For example, they could create a trace link between certain types of data, say a requirement and a document. But they couldn’t create a trace link between a requirement and a product structure or a part, nor could they create a trace link between test data and a product and the best procedure.
In new applications, trace linking between and among any object is possible. This feature alone removes mountains of complexity, time drain and error potential from commonly practiced verification processes. The power of this digital thread capability, especially to A&D manufacturers, is self-evident.
They can pursue verification management’s holy grail: a complete end-to-end, closed-loop integration of the entire product-service cycle that’s easily accessible to all stakeholders during the product’s life.
The integrated data flows across all enterprise value streams—development, design, sourcing, compliance, production and support—and enables end-to-end collaboration, continuous improvement, improved decision-making, quality and traceability. The value of the digital thread is the foundation of Industry 4.0, which is enabled to address big challenges in today’s processes.
The compounding value of integrated verification management
To make effective decisions, stakeholders must have on-demand access to all the linked program data. Most important, such a system maintains the digital thread and enables answering the “why” question. Knowing the answer to the “why” question is critical throughout the thousands of decisions made during the product’s design, manufacture and service.
Having all the artifacts and information that informed the initial certification process ensures that when a question arises, the answer is easily found and traced through each part of the process. Anyone can review how the original requirement was met and certification completed. What was the analysis? What thinking drove that analysis? What tests were run? Why this set of requirements?
Without such traceability, locating the analysis behind a decision, or the tests that were run and their results, costs time and money. In many cases, the knowledge is either lost or so difficult to find that tests must be rerun and reanalyzed.
With total integration of the product lifecycle, knowledge is retained and easily available ensuring that full system program verification is cost-effectively completed on schedule, and that any problems at any time can be solved quickly.
This concludes our introduction to the value of the digital thread in verification management.
About the author
Dave Riemer is the Vice President of Aerospace and Defense Strategy for Siemens PLM Software. He is responsible for using Siemens PLM’s resources to provide value-added solutions for the Aerospace and Defense Industry. He has more than 35 years of experience in the industry. Riemer was previously the Vice President of Science and Engineering at ATK Aerospace Systems, where he was responsible for all technology in the company’s systems group, including development of the Ares I first stage booster and all engineering activities on the Space Shuttle Reusable Solid Rocket Motor, missile defense systems, strategic missile and commercial satellite solid rocket boosters. Riemer spent nearly three decades at Raytheon Aircraft, where he was responsible for product development and airworthiness of all aircraft, including military trainer aircraft and aircraft, and he held leadership positions for the missile business and cryogenic business divisions. He began his career at General Dynamics in the Convair Division as a Thermodynamics Engineer. Riemer holds a Bachelor of Science degree in computer science, with minors in mechanical engineering and finance, as well as a Master of Science degree in mechanical engineering, from the University of Utah.