Virtual commissioning and the production process
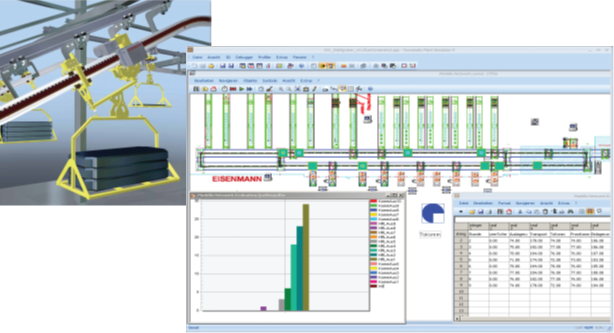
Product personalization and Industry 4.0 are creating an increasingly volatile market, and manufacturers need to be able to quickly respond to change so they can maintain a competitive edge.
This market also means there’s a major transformation in how you stay ahead of the competition. Product innovation is no longer enough: your manufacturing processes must also be innovative, and these processes should help to guarantee consistent manufacturing quality.
To accomplish this, manufacturers must include virtual commissioning in their processes to account for this change. Until now, we’ve discussed how the necessity to improve overall manufacturing quality is driving the need for virtual commissioning. We’ve also observed virtual commissioning in the design cycle of a production system.
Now, we will focus on the virtual commissioning application with the highest impact on production quality and efficiency: virtual commissioning of the production process.
Unlike virtual machine commissioning, virtual process commissioning is about using machines on the shop floor where devices such as robots, conveyers and production machines collaborate with each other during production.
Whenever the production process is the main concern, a new virtual commissioning task is required anytime there’s a variation in the product, or if there are changes to the scope of produced goods, to ensure production works efficiently with same the quality expectations in the new setup.
Virtual process commissioning can be used in two levels of the production systems structure: the sub-system (cell) level, and the system (plant) level. We’ll take a closer look at the different scopes virtual commissioning plays in these two levels.
Assignment of tools and performed tasks to the different scopes of virtual commissioning.Virtual Commissioning of Processes at the Sub-System (Cell) Level
At the sub-system level, virtual commissioning’s focus is on the production cell, where the actual product processing takes place. Depending on the kind of production task you must accomplish, this can be a part being machined, assembled or welded, and where one or more devices can collaboratively perform an operation or a sequence of operations.
At this stage, virtual commissioning must validate three things.
1) PLC codes and robot programs define the tasks the devices must collaboratively perform, and they secure an errorless, high performing, safe execution of tasks.
2) The system layout and configuration are task-optimized.
3) The setup and parameters secure the targeted build quality.Focus of Virtual Commissioning on the Sub-System Level.
Software tools that can support virtual commissioning tasks at this level should provide certain capabilities, including: mechanical sequence validation; PLC code, robot programs and HMI verification; safety interlock tests and system diagnostic testing.
Tools with these capabilities offer significant help to develop complete robot programs, to perform “what-if” scenarios for failure modes and to validate cell design prior to its configuration. These efforts prepare the production cell to satisfy requirements set for its production use concerning:
• Regulatory factors and being able to comply with geographic facility requirements
• Safety factors and achieving interlock and operator safety requirements, and
• Meeting volume production and quality targets.
KUKA Brazil: Virtual Commissioning at the Sub-System Level
KUKA Brazil is one of South America’s top production-line integrators. After successful virtual commissioning applications with a customer, KUKA engineers decided to deliver the next project in its entirety using Process Simulate, a Siemens validation tool particularly useful for virtual commissioning involving industrial robots. KUKA framing station in a body shop.
KUKA engineers practice multidisciplinary engineering review sessions in distributed virtual commissioning rooms. In these sessions, electrical, mechanical and control engineers work together on the same scenario, and everything is visualized and validated with virtual commissioning tools.
Practicing such tasks virtually instead of testing in the physical environment results in damage avoidance on the shop floor, a significant benefit of this new technology.
When KUKA uses virtual commissioning, its engineers can remotely prepare production. These engineers can get the robotic work cells 98 percent ready before they ever go onto the shop floor.
Typically, after the initial production-line installation, KUKA outsources the line start-up to suppliers. The company estimates that approximately 70 percent of the start-up work is robotics and control-programs tuning; with virtual commissioning, that number goes down 20 to 30 percent.
This brings two significant benefits to KUKA Brazil. The company experiences significant financial savings because it outsources a smaller amount of work. And, the company is much more knowledgeable regarding these types of scenarios. By having greater startup know-how, its engineers can improve operations and experience fewer issues on the shop floor as they move between projects.
Virtual Commissioning of Processes at the System (Plant) Level
When it’s done at the system level, virtual commissioning is for the entire plant. The logistics of the part/product transfer and the interdependencies on material flow between the plant’s sub-systems play a major role. At this stage, virtual commissioning’s main objectives are to streamline overall plant performance. This could include:
1) Detecting and optimizing interdependencies between sub-systems
2) Optimizing material flow through the plant
3) Using reliable simulation technology to determine optimized dimensioning of production systems, as well as transfer systems, logistic parameters and buffers, and
4) Higher flexibility to adapt to customer demands and process changes.Objectives of Virtual Commissioning on the System (Plant) Level.
Eisenmann: Commissioning Benefits in All Phases of Production
Traditional commissioning on the plant level is done through numerous tests to verify that the facility or plant functions according to specifications.
Eisenmann Conveyor Systems uses Siemens PLM’s Plant Simulation tool to simulate this testing so the commissioning process occurs in a virtual environment. Plant level virtual commissioning can offer major benefits to overall production. It front-loads the optimization and verification operations to the real production process, which is what Eisenmann production engineers practice today.
Eisenmann also uses Plant Simulation in its automotive business to simulate different production lines, such as paint shops, the overhead monorail systems that deliver parts to assembly lines and automated guided vehicle systems. Typical input parameters for these simulations include the plant’s layout, such as geometry and topology; technical parameters, such as speeds and acceleration; and, logistical parameters, such as requested throughput, shift pattern, mean time to repair and availability.
When Eisenmann wants to work on conveyor dimensioning, for example, the scope of analysis will typically be the cycle time of the discrete conveyors and flow strategies.A CAD model of an electrified monorail system by EISENMANN designed using NX. The simulation model created using Plant Simulation shows the monorail layout, a bar chart showing the order queues, a circular chart showing the level of empty trolleys and a table showing the hourly throughput values.
Sometimes, after several years of operation, a production line needs to be rebuilt. The simulation model that was created when the line was delivered to the plant can help engineers document and visualize the impact of the changes. When Eisenmann built the model with Plant Simulation, it became a part of their deliverable to customers. Many of those customers also use Plant Simulation, so the engineers know how to run the simulation and change the necessary parameters. This task becomes even more efficient if they get a virtual model of the physical line from their supplier, who may have practiced virtual machine commissioning during the design of the same line.
The simulation targets in the automotive business unit typically include throughput confirmation, such as jobs per day, conveyor and paint shop cycle time and a sequence check of the batches. Other targets could also include decoupling conveying areas to analyze the failure impact, checking conveying strategies, sorting color blocks in a paint shop, sorting to rearrange a sequence, determining or estimating the number of skids and hangers, visualizing complex material flow and discussing or developing conveying strategies in a layout.
Eisenmann’s virtual commissioning process is a good model of how a company can benefit from the information virtual commissioning creates during the design of a production system. The simulation models used during machine commissioning provide accurate information of this system to be used in later stages of its lifecycle, when further changes occur and optimization tasks become necessary later in the production. This information also becomes available to operators of the same system.
Final thoughts on virtual commissioning
By being able to reuse the information that defines these devices and their behavior now – not to optimize the design, but to optimize the process – businesses can improve their profits, their product quality and the adaptability of their production processes. Industry 4.0 will revolutionize the technology of production.
Innovative products will no longer be enough to main success in future markets, which is why adaptive production is a major target companies are aggressively pursuing to maintain a competitive edge in a volatile market. Virtual commissioning is one of the complementing measures to revolutionize the process of production to achieve the level of innovation that became the key for success in today’s market place.
This concludes our introduction to virtual commissioning and its role in maintaining high manufacturing quality.
About the author
Dr. Nezih Yaramanoglu is the Program Manager of two major cross organizational research and development programs in Siemens Product Lifecycle Management, with the scope on Digital Enterprise and end-to-end machinery production solutions. His focus is on industry processes and their influences on IT solution architectures. Nezih has more than 36 years of experience in IT Solution research and development for production processes. Prior to his current role, he provided development support in initiating and leading strategic Digital Manufacturing projects. He co-founded the e-Factory organization of UGS in 2001 and led the dCADE PBU of UGS Products organization, which merged with Unigraphics Solutions GmbH in 1999. Before the merger, he was the President and CEO of dCADE GmbH, which he co-founded in 1991. Nezih’s academic background is in mechanical engineering. He received a Ph.D. in production engineering from Technical University of Berlin, Germany, where he also received his Master’s degree in biomedical engineering.