Why the digital machine shop is crucial for future business
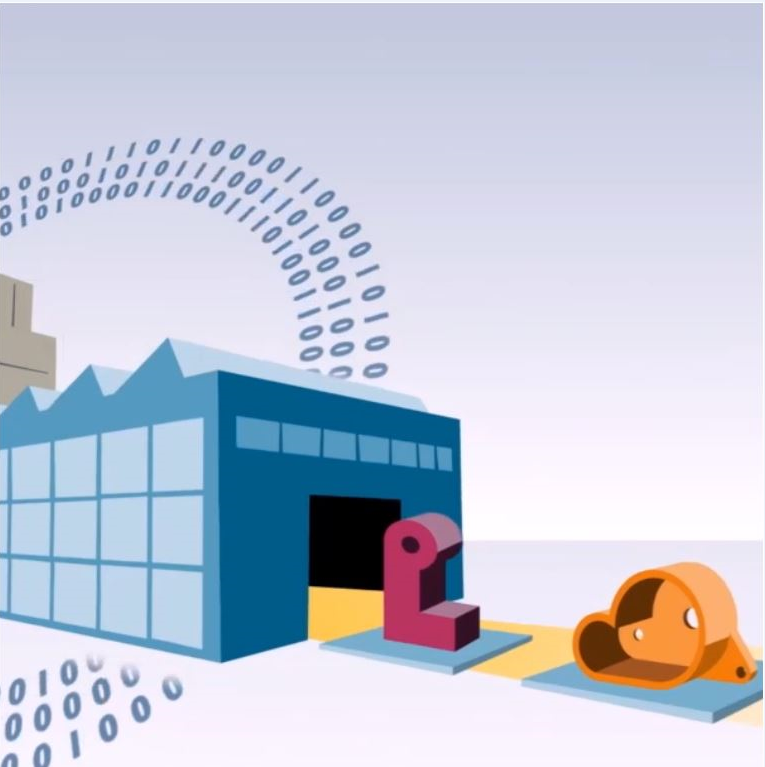
As manufacturers move toward the next Industrial Revolution, they face new challenges that could make or break their business. Competition continues to be tough, particularly from businesses newer to the market, and shifts in the market are more volatile than ever: one false step could knock long-standing market leaders from the top, and they may never recover.
With so much at stake in Industry 4.0, manufacturers are looking for what will give them the competitive edge and what will help prolong their success. Their advantage and success, lies with the ability to digitalize processes and transform how their business performs.
One big way manufacturers can retain their competitive edge is by creating a digital machine shop. A digital machine shop, which uses data to drive a manufacturing environment, can seamlessly connect all of your processes, machines, robots and equipment. Because it’s adaptive, it can sense, learn and share knowledge with every resource in its ecosystem – including people.
The digital machine shop is the focus of a recent series by Armin Gruenewald, the Vice President of Business Development MBG, Manufacturing Engineering Software for the Siemens Digital Factory. Throughout his series, Gruenewald explores how the digital machine shop works and how it ties into the future he and Siemens envisions for manufacturers. He also discusses how the digital machine shop will leverage other concepts we’ve discussed throughout our Thought Leadership series, including the digital twin, additive manufacturing and the smart factory.
How should the digital machine shop fit into your future?
What’s possible with the digital machine shop? A big driver behind the digital machine shop is that tasks once thought impossible become possible. Complex projects become easier to complete. With technologies in their digital machine shop that allow real-time access to information, manufacturers can transform their business and gain an edge against their competition because they can build products customers want and still increase the quality, efficiency and flexibility of their systems.
How do new technologies fit into the digital machine shop? Industry 4.0 technologies aren’t just for larger machine shop businesses: small- and medium-sized businesses also benefit. With the right software, you can virtually fly over your shop floor, no matter its size, and see all of the equipment and machines in it. Using this technology, you can also click on any particular machine to see what’s running, analyze machine statistics or view machine manual.
How do new technologies help me design tools? Having the best possible tools in your digital machine shop is crucial, so you need the right technology to help you design them. Using the best mold design tool can optimize the process and deliver productivity levels that outperform traditional CAD software. This mold design tool provides step-by-step guidance to help you create the most efficient workflow and to integrate complex design elements into automated sequences.
How does the digital twin fit into process planning? CAM is an important component of the digital machine shop, but it isn’t the biggest thing. If you want your set-up to be done correctly the first time, you need to incorporate the digital twin. The digital twin allows you to predict virtually what will happen physically by taking information from the virtual, simulated world and the physical, machined world into one place. Once you refine your setup with the digital twin, you can shift the setup down to the shop floor and be confident it will work with the highest possible accuracy and efficiency.
What’s the best way to set up and manage my tools? Tools are an important component of any machine shop, and they’re especially important in the digital machine shop. And, because the digital machine shop is just that – digital – you’re dealing with more than just a physical catalog of tools. Having physical and digital catalogs can drive up production costs, but having the right processes in place will allow you to precisely manage every tool you use throughout the manufacturing process, all the way from set-up to executing the jobs at hand.
How can I access the digital twin from the shop floor? When a machine goes on the shop floor, it should work the way you think it should from the moment you first power it on. You also need the machine’s digital model to be an exact match of the physical machine and which tools are used in its setup. The digital twin eases this process. You don’t need traditional tools like papers, drawings or spreadsheets to access that data; instead, the digital twin makes it possible to access data using newer technology, like tablets.
How do robots fit into the part-making process? Finding a way to take advantage of robots could be the critical difference between you and your competition getting products to the market faster. The cost of robots continues to go down, and although they aren’t as accurate as traditional machine tools, they have nearly unlimited space for machining – a big advantage in the next Industrial Revolution. With the right software, you can actually program a machine and use that machine’s programming for a robot to help you complete demanding tasks quickly and more efficiently.
How can I use 3D printing in the digital machine shop? 3D printing isn’t new; it’s been around for manyyears. What is new is how much the costs for 3D printers have gone down and how many people are able to 3D print as a hobby. But the power of 3D printing is something manufacturers really need to consider in their digital machine shop. Manufacturers can use additive manufacturing and hybrid machining technologies to build more complex products and still ensure they’re of high quality.
How do we include coordinate-measuring machine and programming? Having information available to you through the digital twin is good, but being able to connect that information to every point in the manufacturing process is what gives you the valuable insight. The digital thread helps close the loop and get you the data you need to the coordinate-measuring machine (CMM), to planning and then into your software so you see how the real, physical part compares to the planning data. Data can then come back into the digital world for real-time comparisons and adjustments.
For more information on the digital machine shop, visit our NX manufacturing blog.
About the author
Toni Boger is the editor-in-chief of Digital Transformations, the Thought Leadership blog for Siemens PLM Software. As the marketing coordinator and content strategist for the Siemens PLM Thought Leadership initiative, she oversees the content creation, management, publication and promotion for all content in the initiative. She graduated from Saginaw Valley State University with a Bachelor of Arts degree in communication and English. Prior to joining Siemens, Toni worked as an associate site editor for TechTarget, a technology media company.