Virtual commissioning’s role in manufacturing quality
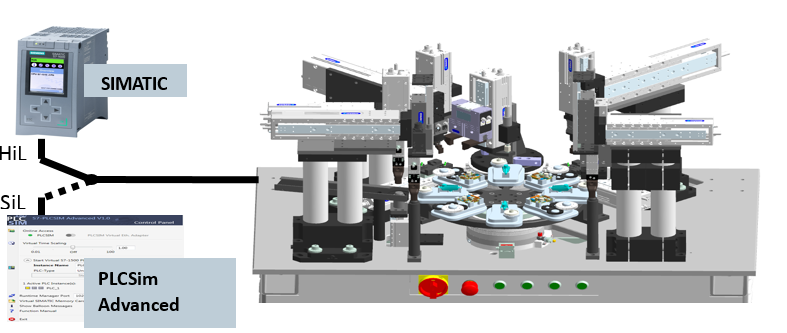
The market is quickly approaching the point where innovation in products alone will no longer be enough to keep you ahead of your competition. Increased product personalization and Industry 4.0 are creating a volatile market that will require manufacturers to be able to adapt and respond quickly to keep a competitive edge.
Innovation must also be in your manufacturing processes. Your processes must be able to guarantee consistently high manufacturing quality that can account for numerous variables. To accomplish this, your company must include virtual commissioning as part of its preparations for this change.
In part one of our series, we began by looking at how the challenge to improve overall manufacturing quality is leading companies toward virtual commissioning. Here, we discuss virtual commissioning’s benefits during the design phase.
In the past, commissioning involved putting the physical machine in its target operational environment and then adjusting its parameters and tweaking the controller code until the machine acceptably performed and fulfilled its process requirements. Commissioning during the design phase wasn’t an option.
The big difference between traditional commissioning and virtual commissioning is that virtual commissioning can be performed during the design phase before the physical machine is produced. The machine design is still changeable at this phase, so it can be corrected and optimized for future use. You can change the design if something doesn’t satisfy a requirement originating from the machine’s future use case, either by adding in or taking out aspects of the design, because nothing has been committed for build until you’re absolutely confident in your design.
Machine virtual commissioning and manufacturing quality
When you incorporate machine commissioning into your processes, you use a combination of the machine design and information about its future use – a combination that allows you to create a machine that could ultimately pull you ahead of your competition.
You’re able to validate the machine’s function in the context of its future usage and make changes for optimization purposes during the design phase. Why the design phase? This part of the process allows you to put all of your engineering intentions into a virtual model of the machine. You create the conditions in which the machine will operate to see if the design does what it’s supposed to do, and you get the chance to make necessary adjustments to the design to:
1. debug the controller code;
2. optimize the machine behavior in context of its future usage;
3. ensure the required functional flexibility for expected variations of the target process, and
4. confirm the design with the machine’s future users.
This can be done before you begin building the machine, which helps you ensure a high manufacturing quality in your processes. Completing your machine’s functional validation in the design phase helps guarantee you’ve engineered the machine to your process’s quality requirements.
You virtually modify the machine until it fulfills the requirements you want it to, in terms of quality and productivity expectations for future use. Once it’s built, you know your engineering processes will do what they should do because of these validations. Much of this confidence comes from the closed-loop feedback, an important part of the process.
The other key to testing your designs to the fullest is being able to borrow behavior-defining components from the real controls that are part of your design. For this purpose, programmable logic controller (PLC) hardware can be interfaced with the validation software to drive the virtual machine. This hardware-in-the-loop (HiL) setup allows you to run the virtual model with high accuracy, giving you a direct reference to reality while you perform complex functional tests with your virtual machine.
New generations of controller hardware can offer software that represents the control’s behavior without needing to use the physical control. This way, a virtual commissioning setup can contain this digital clone of the control in a software-in-the-loop architecture (SiL). However, the ability to build virtual commissioning with these components requires a close cooperation between virtual commissioning software vendors and control manufacturers.
Virtual machine commissioning example case
Typical use cases for virtual machine commissioning are for new designs or overhauling a current design, which should result in a new design-optimized machine, or optimizing a current machine with new components. Let’s look at one sample case.
To study the benefits of virtual commissioning in the design phase, a team designed and modeled an experimental machine to assemble a small mechanical product for use in all commissioning tasks.
The five almost identical placing machines collaboratively place parts into a product, and the rotary table transfers the product from one station to the other. The table holds eight units of this product.
Areas of interest when using virtual machine commissioning: optimized collaboration of nodules, validation of machine behavior and seamless integration of machine design and machine commissioning.The machine needs a synchronous setup. Each placing device should be able to do its job and not collide with neighbors when reaching in. The motion sequence should allow them to execute the appropriate placing motion at the right time, and the table must move when each device retreats to load the next part.
Virtual commissioning of this machine requires you to execute numerous tasks, but there are four main functions to focus on:
Validate the machine design for functional integrity. This task validates the machine’s design and testing its components’ interaction when performing intended functionality.
Assure sequence of operations, synchronized collaboration of handling units. This task aims to tell how the devices should work and collaborate with each other and in which order. This is done by running PLC code while the controller in the loop drives the machine’s simulation model. This controller in the loop can be present as a physical device (HiL) in the virtual commissioning setup, or by emulating software of the real controller (SiL).
Teach in actuators. With devices like robots or placing machines, the ‘teach in’ functionality allows us to virtually hold the hand and guide the robot to perform the desired motion rather than programming these motions. The actuators perform pick-and-place motions, and in some cases perform tasks such as welding, drilling motion; they can be taught-in, respectively.
Validate PLC code. PLC code is responsible for the logic and execution of motions. During virtual commissioning, we run it on the virtual machine to validate the machine’s correct behavior. During this task, you ensure the machine’s safe and performant operation.
Siemens PLM’s role in virtual commissioning
Siemens has seen the benefits of being able to accomplish this virtual machine commissioning, so we do all of it. With how complex of a process it can be, Siemens also has all of the components to make it possible. Being able to combine the virtual and physical worlds for virtual commissioning is a difficult thing to do.
Siemens PLM Software can provide customers the means to incorporate both worlds into their virtual commissioning processes by collaborating with other Siemens business units, which lead the global market in producing PLCs and computer numerical controllers (CNCs).
How is Siemens PLM Software able to offer customers this kind of solution? We don’t have the same borders or confidentiality limits that prevent others from offering these capabilities. We’re able to integrate the real and physical parts of the future machine, plus the planning software that will define it in the future – which allows us to give our customers the competitive advantage.
This concludes part two of our virtual commissioning series. In part three, we discuss virtual commissioning’s role during operations.
About the author
Dr. Nezih Yaramanoglu is the Program Manager of two major cross organizational research and development programs in Siemens Product Lifecycle Management, with the scope on Digital Enterprise and end-to-end machinery production solutions. His focus is on industry processes and their influences on IT solution architectures. Nezih has more than 36 years of experience in IT Solution research and development for production processes. Prior to his current role, he provided development support in initiating and leading strategic Digital Manufacturing projects. He co-founded the e-Factory organization of UGS in 2001 and led the dCADE PBU of UGS Products organization, which merged with Unigraphics Solutions GmbH in 1999. Before the merger, he was the President and CEO of dCADE GmbH, which he co-founded in 1991. Nezih’s academic background is in mechanical engineering. He received a Ph.D. in production engineering from Technical University of Berlin, Germany, where he also received his Master’s degree in biomedical engineering.