The model based enterprise as JT innovation’s next step
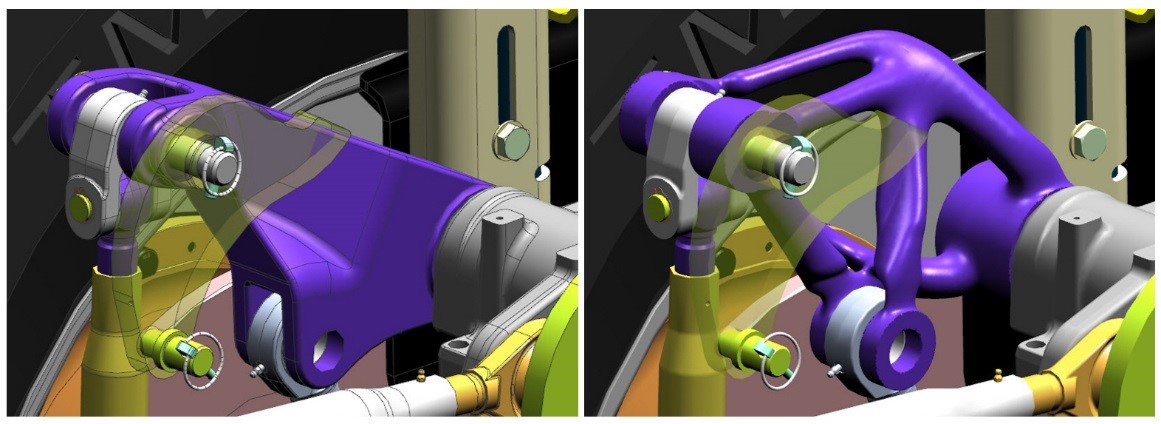
Industry needs to be able to ask and answer “What’s next?” to discover and identify the ideas that will transform the market. Leading companies today are thinking about how to solve what might be called “the next big problem”. In this three part series, we’re exploring how a model based enterprise utilizing 3D JT data can help companies answer questions about what’s next in industry and what’s next for JT.
Part one provided a look at the impact visualizing 3D JT data has had on model based engineering. Part two focused on model based definitions and digitalization. For the final part of this series, I discuss the role Siemens PLM plays in a model based enterprise and four things happening today that will be catalysts for future innovation.
A model based enterprise using model based definitions is truly the way of the future. There are four trends happening today in innovative model based enterprises that will be the catalyst for how companies deliver their next great idea to the market. As different as these situations may seem, they each share the need of digital 3D shapes to be successful. Let’s look at each situation and its potential.
1 – Convergent modeling and Generative Design. In general, products look the way they do because of the design process used to create them. Typically, engineers come up with an idea for a product and then, using numerous tools and a computer, they create a digital product definition. This has been an effective method for product design for decades.
The problem with this method is there are implicit limitations on how engineers are allowed to think. Restrictions are built into the processes and materials used to produce products designed this way. Industry is beginning to embrace a relatively new concept for product design called generative design.
The generative design methodology can unlock thousands of potential product designs very quickly. Siemens convergent modeling capabilities allow data from many sources, including captured representations of existing physical designs, to flow into the generative design process. The convergent models become part of the generative design process. Engineers can put rules in place that define the products functionality, how it should be manufactured and the materials it can be made from. The application of these parameters will tell the engineer what his product design should actually look like.
Generative design and convergent modeling can unlock new design possibilities by processing thousands of ideas, and applying them with shapes and geometry from the real world. These capabilities can help companies create the model based definitions that bring their next big innovation to the market.
2 – Industry 4.0. For the past decade, Industry 4.0 has been a part of the Siemens AG narrative. It is being realized today at the Siemens plant in Amberg, Germany, where Simatic programmable logic controllers are made. In this facility, each bin in the factory comes with a barcode, the machines in the plant read the bin’s barcode to learn what’s inside the bin and what must be done with the parts. With a plant automation level of 75 percent and employee training, workers are able to collaborate in both analog and digital worlds to solve problems.
While this is an effective process, Siemens has been looking to answer its own “What’s next?” question. Engineers are experimenting with technology that will give robots in the plant the ability to interpret what’s happening around them. The ultimate goal is to have robots in the plant be able to “see” what’s coming and to recognize what the part is meant to be and the person who needs it. The robots will recognize what part is using that shape. The shapes will be provided to the robot through technology made possible by 3D JT data.
3 – Collaborative robots. Robots in today’s plants are typically big and powerful. To protect workers these machines operate in secured areas. If a human moves within a certain distance of a robot, it automatically shuts down. While this is a necessary safety precaution, it creates slowdowns in production.
Innovative companies are working to make collaborative robots smart enough to actually work next to a person on a production line. These robots will be aware of their surroundings and know where things are based on the shapes they recognize. Once again, shape recognition can be enabled using 3D JT technology. Safe robots will become collaborative partners that help companies transform the way they get products to market.
Soon, collaborative robots will be able to know their surroundings and where things are using 3D JT technology.
4 – Augmented reality. For many people, Pokémon Go is their first experience with Augmented Reality. Users overlay virtual objects into real life using a phone as the visual display device. Though Pokémon Go is a primitive example of augmented reality, there are many mature instances used today.
Surgeons can overlay holographic images of anatomy using an augmented reality headset. Plant floor productivity improves with employees who use augmented reality lenses for building maintenance and to design and service heavy machinery. These use cases require accurate, often complex, 3D data to be successful.
What supplies the shapes for augmented reality workflows? You guessed it: 3D JT data files.
Augmented reality requires accurate, complex 3D data to be successful.
Use JT for model based definitions to find tomorrow’s innovations
Using a familiar 3D format such as JT, in conjunction with the four situations we see today, allows innovative ideas to move past traditional visualization workflows. By doing so, you can let 3D JT provide the shapes in the model based designs necessary for the digitalization of a model based enterprise.
This concludes our introduction to model based enterprises and the future of JT.
About the author
Mike Zink is a Senior Product Manager and Openness Evangelist working in the Corporate Technology Office of Siemens PLM Software. He has more than 36 years of experience with software product development, project management and manufacturing support. Mike currently has product management responsibility for the Siemens PLM JT Toolkit, PLM XML Software Development Kit and JT2Go, the 3D data viewing tool for JT. He is also the Siemens PLM Software openness evangelist and encourages openness in industry through programs such as the Code of PLM Openness and ISO standardization of JT. Mike has a Master’s degree in software development and management and a Bachelor of Science degree in computer science from the Rochester Institute of Technology.
Comments