Why do you need integrated assembly planning?
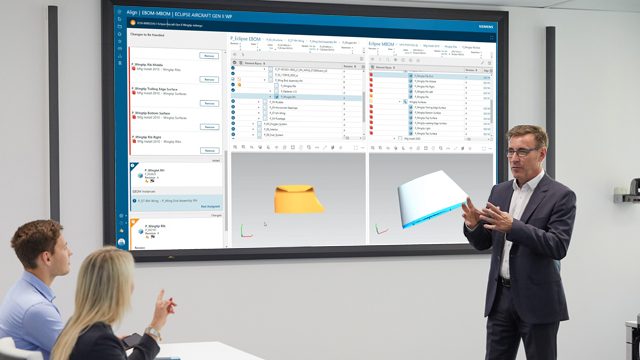
This is the first blog of an eight-part series where we will discuss our integrated assembly planning solution capabilities and the potential benefits that can be realized.
Currently many manufacturers attempt to resolve the needs of assembly planning within their enterprise resource planning (ERP) systems or with other point solutions, such as spreadsheet based planning or CAD based process plans and documentation. These types of solutions are generally disconnected from the control and flow of engineering changes and require significant overhead to manually synchronize data to ensure data quality and accuracy.
Additionally, timing and cost pressures in conjunction with increasing product complexities are causing many manufacturers to re-evaluate their production strategies. Globalization also continues to impact manufacturers and drives the need for faster response to changes in demand and the ability to alter production rates or shift production between facilities as required. Achieving the same quality within all this complexity is critical and requires robust knowledge sharing and reuse to implement best practices and a common understanding across production facilities. Quickly identifying and developing new improvements will require robust digital twins of production processes to run experiments, to validate those improvements, and to understand their potential impact prior to real production.
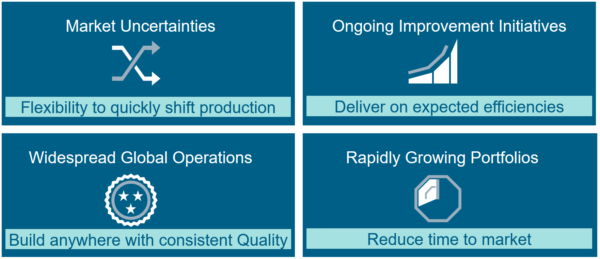
The reality for many manufacturers today is that they continue to work in silos with sub-optimized processes within each function and very little true collaboration across the organization. This operating model can create sequential, manual hand-offs and significant data redundancies. This lack of collaboration and data inconsistencies creates the potential for miscommunication, quality escapes, and late identification of manufacturability issues, all of which can drive significant time, effort, and cost in rework.
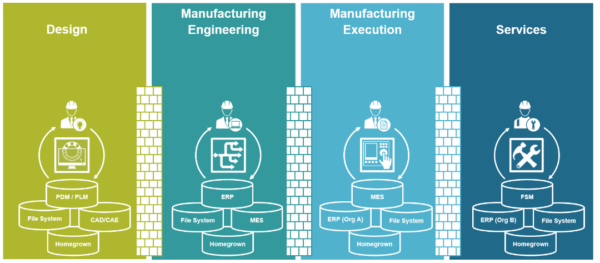
Extending your digitalization strategy to manufacturing will allow you to shift your assembly planning activities earlier in the product lifecycle. This will enable early collaboration across your organization providing the required visibility to resolve potential issues and optimize your production process plans while the cost of change is still reasonable.
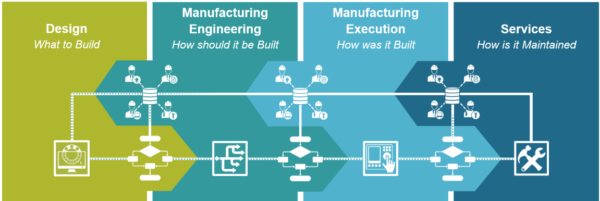
Our Assembly Planning solutions allow you to:
- Create a Manufacturing Bill of Material (mBOM) for a specific view and extension of the Engineering Bill of Material (eBOM) fully linked to ensure alignment and compliance to the required design requirements.
- Define and verify the intended production Bill of Process (BOP) very early in the product lifecycle and in collaboration with all stakeholders.
- Author detailed electronic work instructions with direct linkages to the required Parts and Tooling that are available based on association to the BOP.
- Leverage approved timing standards to develop detailed time analyses balanced to achieve optimal utilization while meeting the required production throughput.
- Capture, share, and reuse manufacturing knowledge across your organization to propagate best practices, improve data quality, and minimize data redundancies.
These solutions also allow the same data foundation to be enriched through our various digital manufacturing solutions and provide for a controlled and consistent data feed to your downstream systems.
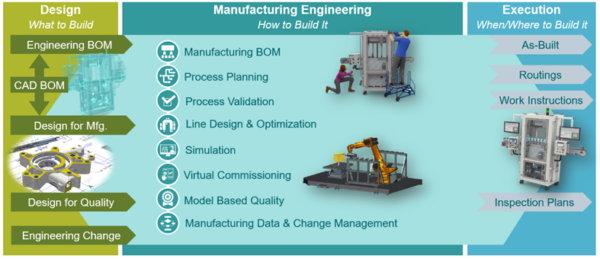
As we continue through this series, we will discuss the various capabilities in more detail and how our assembly planning solutions can be leveraged to manage all the data and processes required to extend the digital thread to manufacturing and continue building toward a truly comprehensive digital twin.
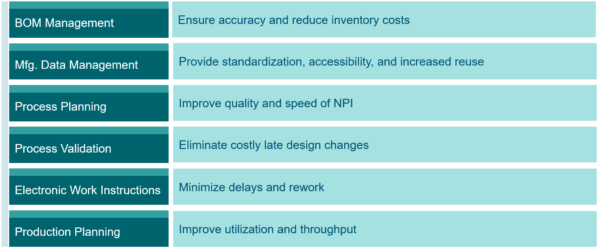
Look for part two in the series where we will discuss the upstream and downstream advantages of managing an integrated Manufacturing Bill of Material (mBOM).
—–
Learn more about our Assembly Planning solutions > here.
You can also try our Easy Plan software free for 30 days > get started today.